ALL >> Business >> View Article
A Buyers’ Guide To Industrial Scales
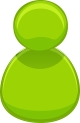
Evaluating your needs
Any investment in your production processes, manufacturing capability, testing, quality and weighing facilities, is something that requires careful planning and execution.
It is, of course, true that no two businesses are the same, hence any equipment that you buy or hire, needs to be a good fit for your specific needs and environment.
In a day and age when finances are tight, it’s important to explore all of the practical, physical and cost considerations before you decide on a specific pathway.
This article discusses some of the purchasing considerations with regard to the acquisition of industrial scales, stainless scales and/or other weighing equipment.
Where to start?
There are many hundreds, even thousands of branded industrial scales out there. These are used across many different industries and designed for a wide range of applications.
The best place to start perhaps is to consult ...
... your production team. This will determine what they need and why they need it, so that you can start to focus on the type/s of weighing equipment best suited to your environment.
You need to understand, things like where the scales will be located, how many you’ll need, what size the weighing platform needs to be, the minimum/maximum weighing capacities, how accurate the readings need to be etc.
When you have a checklist of key criteria you can then move on.
The physical parameters
The efficiency of your production processes and staff depends on the type of weighing equipment that you select. When choosing a scale solution, therefore, you need to ensure that equipment is fit for purpose, ie: the appropriate size/capacity. In other words, is the platform going to be able to precision weigh output consistently and without fail? There is one train of thought that suggests buying a larger platform from the outset, is a better, safer option than having to upgrade within a few weeks. This is a particular consideration if you manufacture large parts, rather than small pieces.
Assessing your environment
Understanding where and how the scales will be used is hugely important.
For example, does it need to be floor standing, or will it be located on a bench or worktop? Will it be wall mounted? Some industrial scale solutions also need to be mobile and travel around your business. These often come with a weighing indicator (or display) that can be detached and used as a handheld device. Others come with mounting kits that make it easier to take and record readings and operate the device.
If you work in a harsh, potentially explosive environment, or with flammable liquids/processes, you will also have to ensure that equipment complies with the ATEX Regulations and has been certified accordingly.
Some models are better suited to certain environments than others. It’s important that you go through this thought process asking yourself questions like: how often will I need to clean it? Is the environment conducive to cleaning, ie: is it dust free? Will the unit need to be moved? It, therefore, needs to be robust and suitable for heaving handling.
Here’s a condensed checklist of some of the key points raised:
Will the equipment meet current and proposed legislation requirements, and be suitably legal and compliant for the job it is intended to do?
Will I need to collect data and have this transmitted to a PC?
Will I need to meet strict hygiene requirements, or are there any hazardous area issues? ie: ATEX
Will the equipment will suitable for automation?
Will it be legally verified for trade use, using the minimum ao average weight system, or is my application purely internal?
Will the equipment, as far as possible, be future proof?
Will my supplier offer me a comprehensive maintenance and/or servicing plan?
Will I need UKAS standard calibration? If so, can my supplier provide this service?
There are, of course, many other factors that come into the equation such as price, availability, financing, customer care, reputation, installation support and so on.
Abacus weighing offers different types of weighing products like Industrial scales, ATEX Scales, Laboratory Scales etc. Situated in Littleborough, Greater Manchester, they specialise in sale, repair, maintenance and calibration of industrial weighing systems. They supply and service end users directly as well as through approved distributors.
Add Comment
Business Articles
1. Lucintel Forecasts The Global Polyvinylidene Difluoride (pvdf) Market To Reach $2 Bllion By 2030Author: Lucintel LLC
2. Electronics Thermal Management Solutions Market Size & Share, Analysis 2031
Author: Andy
3. Choosing The Right Custom Injection Mould Manufacturer For Your Needs
Author: MOULDING-INJECTION
4. Discover The Timeless Beauty Of Handmade Ceramic Products
Author: Matthew Edwards
5. The Power Of Advanced C Frame Mechanical Power Presses
Author: Mankoo Presses
6. Lucintel Forecasts The Global Short Fiber Thermoplastic Market To Reach $24 Billion By 2030
Author: Lucintel LLC
7. Lucintel Forecasts The Polyurethane Resin In The Global Composites Market To Reach $188 Million By 2030
Author: Lucintel LLC
8. Custom Sticker Printing In Dubai: The Answer To Individual Branding
Author: Digital glob
9. Lucintel Forecasts The Global Greaseproof Paper Sheet Market To Reach $3 Billion By 2030
Author: Lucintel LLC
10. Speech Development Experts For Kids In Hyderabad
Author: pavitra
11. Lucintel Forecasts The Global Polypropylene (pp) Compound Market To Reach $15 Billion By 2030
Author: Lucintel LLC
12. Forecasting The Expansion Of The Ginger Powder Market
Author: mmr
13. Why Work With A Leadership Consulting Firm: A Complete Guide
Author: cluboneair
14. Unlocking The Billionaires Mindset: 10 Transformative Habits To Achieve Limitless Success
Author: Ourbusinessladder
15. Embrace Solar Energy With Elite Electrical Kent: Your Trusted Partner In Bromley And Beyond
Author: nicola