ALL >> Shopping-Product-Reviews >> View Article
Oil Analysis Program | Does It Save Money?
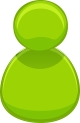
Rudy McCormick, Trico Corporation
Its 2015, in some way most companies either have tried to, tested, or have implemented oil analysis programs to better manage their equipment and lubricant assets. While some have received only marginal benefits, many have reported substantial savings, cost reductions and increased productivity. Success in an oil analysis program requires a dedicated commitment to understand the equipment design, the lubricant, the operating environment and the costs involved in maintaining the equipment vs. fixing/replacing critical internal parts.
Oil Analysis Today
Over the last decade North American companies have spent literally millions of dollars in oil analysis programs and many of them don’t understand the return on that spend. The analysis performed by Original Equipment Manufacturers (OEM) lubricant manufacturers is often termed as “free”. In many of those cases, the results from the testing have little to no affect on the maintenance, planning and/or evaluating equipment condition. In many cases, value is lost because of lack of knowledge: a failure to understand the value ...
... lost when a sample is not representative of the system. Most companies lack the ability to turn equipment and lubricant data into useful information which can then be used to maintain equipment. Failure to understand the true requirements and operating characteristics of the equipment can also be a factor. In many cases, oil analysis programs which do not utilize human experts simply provide data which is meaningless to all but a few engineers who’ve been exposed to proper oil analysis. Conflicting information from equipment suppliers, laboratories and lubricant manufacturers have clouded the true requirements of equipment to the maintenance personnel or individuals responsible for the program.
The following steps provide a guideline for implementing an effective oil analysis program: a program considered one of the critical technologies to increasing equipment reliability in a way that allows for return on investment and increases in productivity simultaneously.
Commitment is not an option when working to collect and record all information necessary to understanding equipment, the needs of the equipment, the operating environment and ultimately your oil analysis program. You either do it or you don’t…in…or out.
Equipment Audit
An equipment audit is critical in maintaining useful knowledge of the equipment, its internal design, the system design, and the present operating and environmental conditions. Simply put if you don’t understand the needs and conditions of your equipment undermines the technology. This information is used as a reference to set equipment targets and limits while supplying direction for future maintenance activities. The following should be documented in your equipment audit process:
Equipment Mission Criticality
Equipment Component and System Identification
Operating Parameters
Operating Equipment Evaluation
Operating Environment
Maintenance History
Oil Sampling Location
New Oil Baseline
Cooling Water Baseline
Targets and Alarms
Database Development
Lubricant Audit Process Equipment reliability requires a lubricant that meets and maintains specific physical, chemical and cleanliness requirements. A detailed trail of a lubricant is required beginning with the OEM (oil supplier) and ending after disposal. Sampling and testing of the lubricants are important to validate the condition of the lubricant through its life cycle. In the process reliability professionals should audit:
Lubricant Requirements
Lubricant Supplier
Oil Storage
Handling and Dispensing
Waste Oil
Oil Analysis Program Evaluation
Predictive Maintenance tasks are based on condition measurements and performance on the basis of defects - before outright failure impacts safety and production. Well-managed PdM or condition monitoring programs are capable of identifying and tracking anomalies. Success is often measured by factors such as the number of machines monitored, problem recognized, number of saves and other technical criteria. Few have successfully translated technical and operating results gained by predictive maintenance into a value and benefits in the financial terms necessary to assure continued support. Without credible financial links to the facility’s and organization’s business objectives, technical criteria is essentially weightless. As a result, many successful predictive maintenance programs are being curtailed, even terminated, as a cost reduction measure. This at times is counter-intuitive because oil analysis programs allow for the extending of time between lubricant change-outs which can save companies big dollars on their bottom line. Dedication to an oil analysis program requires the documenting of all the obtained cost benefits associated with a properly implemented program, which relates the program to outcomes in the bottom line.
Summary
Training, software, user-friendly labs, modernized testing equipment for used oil analysis, and the introduction of portable test equipment have allowed maintenance personnel to obtain meaningful data from a sample of oil. Data that can tell the tale of what is really going on inside the machine, however, many times this information remains as data and is not used properly as information to benefit or direct maintenance activities within the plant. This can lead to failed early detection of deteriorating lubricants and equipment conditions and neglects the profitable pinpointing of the root causes. Nonrepresentative samples, lack of equipment knowledge, uncontrolled testing, generic targets and limits are all among the inconstencies that affect the legitimacy of actions requested by maintenance professionals to perform maintenance activities initiated with this data.
An oil analysis program can be one of the most powerful technologies used to increase equipment reliability period. One failure averted or one extended oil change interval is often all that is needed to not only cover the cost of the program, but pay in terms of increased productivity less downtime, and documentation can prove this beyond any shadow of doubt.
Add Comment
Shopping/Product Reviews Articles
1. 7 Gifting Ideas For Women’s Day Under $100Author: fine color jewels
2. Wood Glue: The Ultimate Adhesive For Durable Bonding
Author: yakubali7842
3. The Steady Rise In Law Firms In The Modern Society
Author: Henry Jones
4. How To Find The Best Deals On Watches This Christmas And New Year In Australia
Author: Watch
5. Bulk Winter Rubber Animal Toys For Kids: A Fun And Affordable Seasonal Delight
Author: La Luna Bella
6. Built-in Bra Tops: Your New Wardrobe Essential For Style And Comfort
Author: Henry Vongxay
7. Enjoy Warmth And Health: The Surprising Benefits Of Hydronic Heating
Author: Jackson Smith
8. The Best Employee Gift Ideas Singapore - Know Before You Buy!
Author: DTC World Corporation Pte Ltd.
9. Christmas 2024: Jewelry Gift Ideas For Women
Author: fine color jewels
10. Discover The Timeless Appeal Of Ceramic Wedding Rings
Author: thejewelrysource
11. Creative Ways To Use Rice Paper Wraps For Healthy And Delicious Dishes
Author: King Soba Noodle Culture
12. Experience The Perfect Blend Of Flavour And Sustainability With Te-a-me
Author: Te-A-Me
13. Indoor Led Display Module: Enhancing Visual Experiences
Author: ledcontrollercard
14. Thoughtful Best Man Gifts: A Guide To Men’s Accessories
Author: Andrew Wilson
15. Why The Parsley Chopper Is The Solution To Herb Prep Problems
Author: aaron