ALL >> Business >> View Article
Compression Molding
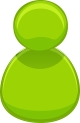
Every passing day is contributing in the development of new processes and ideas in manufacturing industry. Manufacturers always search for more and more sophisticated methods and techniques for making products. In modern times, Molding is recognized as a widely used method for manufacturing. In the process of molding, liquid raw material is given shapes of different products by using a Mold.
There are various types of molding techniques which are being employed in today’s manufacturing industry. Compression molding is one of these types. Compression molding can be defined as a method of molding in which raw material, usually preheated, is directly placed into an open and heated metal mold. When the hot material takes position in the mold cavity, mold halves will be closed by hydraulic ram. At next stage, pressure is applied to force the material to congest in the mold cavity. The mold cavity will remain closed for a certain time, thus the material will flow in the cavity and fill up all the empty spaces. There may be some overload material which can be channeled away by the overflow grooves.
The applying pressure ...
... forces the material to adopt the shape of mold cavity. During this process, heat and pressure are maintained until plastic is compressed into the shape of the mold. After some time, applied pressure will be released, and molded part is removed from the mold. A very high pressure is used in compression molding depending upon the type of material and part thickness. A hydraulic ram is often used to produce sufficient force during molding procedure.
There are two different kinds of compounds which are most commonly used in compression molding: Bulk Molding Compound (BMC) and Sheet Molding Compound (SMC).
Compression molding was basically developed to manufacture composite and complex parts for metal replacement applications. It is used to produce larger flat or fairly curved parts. Nowadays, many automotive parts such as hoods, fenders, scoops, spoilers, as well as smaller complicated parts are manufacture by compression molding. In addition, Compression molding is frequently used for manufacturing electrical parts, buttons, buckles, knobs, handles, electronic device cases, flatware, gears, appliance housing, and large container.
Two general types of resins are used in compression molding: thermoset, like epoxies and cyanate esters; and thermoplastics, like Polyetheretherketone (PEEK), Polyamide-imide (PAI), Polyphenylene Sulfide (PPS) and Fiber reinforced plastics.
The thermosetting resins are used in compression molding process, either in the form of granules, putty-like masses, or preforms.
Compression molding offers lots of advantages. Through Compression molding technique, ultra large size parts can be manufactured, that are not possible to produce by extrusion methods. This technique is utilized to manufacture very intricate and complex parts with high quality.
It is considered as the lowest cost molding method as compared to other methods. Moreover, compression molding wastes relatively little material, making it an ideal option for working with expensive compounds. Generally, parts manufactured by compression molding have good surface finish with less joint lines and less fiber-length degradation than injection molding.
However, compression molding is not suitable for some types of parts. It often provides poor product constancy and cause difficulty in controlling flashing. Besides that, its manufacturing speed is not equal to injection molding standards. Another disadvantage of compression molding is its limited capacity to produce parts with undercuts.
In order to achieve the highest results from compression molding, the amount of raw material, heating time and technique, applied pressure and cooling time/technique must be cautiously developed and supervised.
plastic packaging
pet bottles
containers
plastic
pet bottle
mineral water
Add Comment
Business Articles
1. Lucintel Forecasts The Glass Fiber In The Global Marine Market To Grow With A Cagr Of 3.7% From 2024 To 2030Author: Lucintel LLC
2. Lucintel Forecasts The Glass Fiber In The Global E&e Market To Grow With A Cagr Of 3.9% From 2024 To 2030
Author: Lucintel LLC
3. Lucintel Forecasts The Global Frp Pole In Telecommunication Market To Grow With A Cagr Of 6.5% From 2024 To 2030
Author: Lucintel LLC
4. Lucintel Forecasts The Global Frp Pole In Power Transmission & Distribution Market To Grow With A Cagr Of 6% From 2024 To 2030
Author: Lucintel LLC
5. Lucintel Forecasts The Global Frp Pipe In Oil And Gas Market To Grow With A Cagr Of 5.1% From 2024 To 2030
Author: Lucintel LLC
6. Lucintel Forecasts The Global Frp Pipe In Chemical Market To Grow With A Cagr Of 3.6% From 2024 To 2030
Author: Lucintel LLC
7. Adopt A Modern Telecom Commission Management System To Fix Revenue Leakages
Author: Kevin
8. Quality Steel Pipes And Tubes With Commitment And Trusted Service
Author: CONTENT EDITOR FOR SAMPHIRE IT SOLUTIONS PVT LTD
9. Lucintel Forecasts The Global Foam Core For The Construction Market To Grow With A Cagr Of 3.7% From 2024 To 2030
Author: Lucintel LLC
10. How Important Is Mutual Fund?
Author: Sagar Shah
11. What Do You Need To Know About Customize Your Own Clothes
Author: Guangzhou Beianji Clothing
12. Detailed Tips To Choose Quality Cabinets And Joinery Melbourne
Author: William Harvey
13. Lucintel Forecasts The Global Foam Core For The Transportation Market To Grow With A Cagr Of 5.4% From 2024 To 2030
Author: Lucintel LLC
14. Silicone Sealing Foam Cord: The Valuable Option For You
Author: Dongguan Senma New Materials Technology Co., Ltd
15. How Investment Banking Companies And Credit Solutions Elevate Wealth Management
Author: Drishti Desai