ALL >> Business >> View Article
Hot Dip Galvanization Process – An Overview
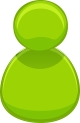
Three basic steps in hot dip galvanization process are surface preparation, galvanizing and inspection. Surface preparation determines the durability of coating typically involving caustic cleaning, pickling and fluxing. In caustic cleaning, organic contaminants are removed, while fluxing eliminates oxides. Read on to know more.
Galvanization is an effective, low-cost method to improve the durability of steel, which is coated in a thin layer of zinc to promote the corrosion resistance of the product. The process involves cleaning incoming substrate with an alkaline detergent, annealing, coating with molten zinc and leveling tension on both lines. The product is heat-treated after coating to prepare it for painting. Procurers can also get done ink printing and chem-treatment done on steel.
Hot dip galvanizing process, which is preferred by the industries, consists of three basic steps – surface preparation, galvanizing and inspection.
Surface preparation is the critical first step that determines the durability of coating. Zinc simply won’t stay on a steel surface that is not clean. Surface preparation ...
... typically involves caustic cleaning, pickling and fluxing.
In caustic cleaning, the steel is dipped in a hot alkali solution for removal of organic contaminants such as grease, oil, paint markings and dirt. Vinyl, epoxies, welding slag and asphalt is removed by mechanical means like grit blasting and sand blasting. It is then put in a rinsing tank. Next step is pickling when the product is dipped in a dilute solution of hydrochloric acid, which cleans scale and rust from the surface. Now, it is dipped in a second rinsing tank.
The final step for preparation is fluxing, which eliminates oxides and prevents further oxides from forming on the metal surface prior to galvanization. It promotes bonding of zinc to the steel surface. The product is then pre-fluxed in an aqueous solution of zinc ammonium chloride and then air dried.
Now begins the process of galvanization. The steel is completely immersed in a solution that contains a minimum of 98% pure molten zinc. The immersion is done at about 850°F (454°C), and then withdrawn slowly whereby the excess zinc is removed by draining. The steel is then cooled in ambient air or quench tank.
The last step is inspection. The two features closely scrutinized are coating thickness and coating appearance. Several physical and laboratory tests may be performed to determine thickness, appearance, uniformity and adherence.
Advantage of hot dip galvanizing is that it produces no significant changes in the mechanical properties of the structural steels or welds. Underlying steel of the galvanized product is chemically and metallurgical equivalent to the uncoated steel.
One of the processes is galvannealing wherein the surface of the just-coated steel is immediately reheated by open-air burners. Zinc alloys or metallurgical blends with steel and the surface of the strip. A galvannealed item corrodes more readily than galvanized steel. It is intended for applications where it would be painted, such as appliance panels and computer brackets.
Most ferrous materials are suitable for galvanizing including malleable iron, cast iron, cast steels, and hot and cold rolled steels.
Companies like BlueSteel Services LLC can be trusted for the quality of galvanized pipes, steel coils and electrical conduits. This site represents domestic and offshore producers in the US of finished and semi-finished steel goods.
Visit home page for gathering more information about the company’s product line. They can stand up to the challenging standards in a rapidly changing marketplace.
Author of this article is associated with BlueSteel Services LLC, which is engaged in OCTG sales, steel coils, electrical conduits, water well casing and pipes.
Add Comment
Business Articles
1. Lucintel Forecasts The Global Polyvinylidene Difluoride (pvdf) Market To Reach $2 Bllion By 2030Author: Lucintel LLC
2. Electronics Thermal Management Solutions Market Size & Share, Analysis 2031
Author: Andy
3. Choosing The Right Custom Injection Mould Manufacturer For Your Needs
Author: MOULDING-INJECTION
4. Discover The Timeless Beauty Of Handmade Ceramic Products
Author: Matthew Edwards
5. The Power Of Advanced C Frame Mechanical Power Presses
Author: Mankoo Presses
6. Lucintel Forecasts The Global Short Fiber Thermoplastic Market To Reach $24 Billion By 2030
Author: Lucintel LLC
7. Lucintel Forecasts The Polyurethane Resin In The Global Composites Market To Reach $188 Million By 2030
Author: Lucintel LLC
8. Custom Sticker Printing In Dubai: The Answer To Individual Branding
Author: Digital glob
9. Lucintel Forecasts The Global Greaseproof Paper Sheet Market To Reach $3 Billion By 2030
Author: Lucintel LLC
10. Speech Development Experts For Kids In Hyderabad
Author: pavitra
11. Lucintel Forecasts The Global Polypropylene (pp) Compound Market To Reach $15 Billion By 2030
Author: Lucintel LLC
12. Forecasting The Expansion Of The Ginger Powder Market
Author: mmr
13. Why Work With A Leadership Consulting Firm: A Complete Guide
Author: cluboneair
14. Unlocking The Billionaires Mindset: 10 Transformative Habits To Achieve Limitless Success
Author: Ourbusinessladder
15. Embrace Solar Energy With Elite Electrical Kent: Your Trusted Partner In Bromley And Beyond
Author: nicola