ALL >> Business >> View Article
Role Of Cmp Tester In Industries
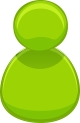
The AFM (atomic force microscope) functions as a cmp tester to assess the rate of removal by one particle in the cmp slurry. With regards to its description, the procedure uses a corrosive chemical and abrasive together with a retaining ring and polishing pad, usually greater in diameter compared to the wafer.
Chemical Mechanical Polishing refers to a procedure for the planarization of semiconductor wafers, materials etc. This procedure can be regarded as a fusion of free abrasive (polishing) and chemical etching. This process takes advantage of the synergetic impact of both chemical and physical forces for wafer polishing. Its objective is to acquire regular planarization across the wafer in a global fashion. The wafers comprise numerous small patterns which take the shape of interconnected silica and copper lines. Planarization refers to a process that eliminates the surface topologies, flattens and smoothens the surface; planarization level signifies the smoothness and flatness of a surface. The process takes place when the polishing of interconnects occurs at a similar level. During the polishing process, four various ...
... forms of polishing take place; smoothing, no planarization, global and local polishing.
The AFM (atomic force microscope) functions as a cmp tester to assess the rate of removal by one particle in the cmp slurry. With regards to its description, the procedure uses a corrosive chemical and abrasive together with a retaining ring and polishing pad, usually greater in diameter compared to the wafer. The wafer and pad undergo joint pressing using a polishing head which is dynamic in nature. Head rotation then occurs using various rotation axes to remove material and even out any unequal topography. This process has several advantages. To begin with, planarized surface permits enhanced resolution of photolithography procedure. Secondly, planarized surfaces eradicate sidewall thinning due to poor PVD step coverage. Lastly, the process also eliminates the prerequisite of extreme development and exposure.
Prior to 1990, technicians considered the CMP as too dirty to be incorporated in fabrication processes that deal with high precision. Additionally, abrasion has a tendency to form particles and the abrasives contain impurities. Since that period, the industry that deals with integrated circuit has shifted from using aluminum to copper conductors. This necessitated the invention of a procedure which has distinctive capabilities that eliminate material in a uniform and planar manner. As a result, the adoption of this process has made it more prevalent. Other than copper and aluminum, the creations of these procedures have occurred for polishing silicon dioxide and tungsten. In terms of application, STI, a procedure used in fabricating semiconductor apparatus, is a method used in enhancing the separation of active areas and devices. Furthermore, this process has an elevated planarity degree making it vital in applications related to photolithography.
The process of CMP tester has several limitations that occur throughout the polishing procedure, demanding new technology optimization. Specifically, wafer metrology needs improvement. Additionally, procedures related to CMP have numerous possible defects including weak surface delaminating, stress cracking and corrosive attacks from chemicals (slurry). The oxide polishing procedure also has a serious problem; the absence of end points needs blind polishing, which makes it difficult to establish when the required quantity of material has undergone elimination, or the required planarization level has undergone acquisition. If the oxide cover has faced insufficient thinning or the required planarity level has not met its achievement throughout this procedure, then wafer re-polish can occur. Other problems that emerge during polishing include corrosion, dishing and erosion. Although, this technique is costly and time-consuming because technicians have to pay more attention while conducting this procedure, it remains significant.
Author of this article is associated with Rtec Instruments that deals in equipment such as CMP tester and ball on disk tester.
Add Comment
Business Articles
1. 5 Common Mistakes In B2b Lead GenerationAuthor: Akash
2. Indulge In Opulence: The World Of Luxury Jewellery
Author: Dhee Jewels
3. Empowering Aviation Safety Enhanced: Expert Fatigue Management
Author: skyone
4. Best Digital Marketing Agency In Bangalore | Best Digital Marketing Services
Author: Sanbrains Seo
5. Achieve Iso Certification In Greece: Boost Credibility & Growth
Author: Sistema Certifications
6. The Affordable And Beautiful Spray Bottles
Author: Forever Gleam Chemicals
7. Top 7 Cryptocurrencies Under 1 Cent With Real-world Utility In 2025
Author: Jasmyhit
8. The Raw Wisdom Of Kevin Gates: Unpacking Inspirational Quotes From A Street Philosopher
Author: Gaurav b
9. Enhancing Community-level Cybersecurity With Barracuda Networks' New Initiatives
Author: Industry Chronicle
10. Women Empowerment Ngos In Chennai: Prajha Trust’s Vision For Inclusive Growth
Author: Anbu Thalapathy
11. Iso Certification In India: Benefits And Process
Author: Sistema Certifications
12. G20 Summit 2023: 5 Key Takeways That Look Good For Business!
Author: Impaakt Magazine
13. Unitron Hearing Aids In Delhi: Find The Best Solutions At Hearing Clinique
Author: Hearing Clinique
14. How Performance Analysis Software Can Improve Decision-making
Author: TrackHr App
15. Top Domestic Courier Services In Gurugram- Fast, Dependable And Reasonable
Author: Karishna Trading Co