ALL >> Others >> View Article
High Pressure Side Channel Blowers
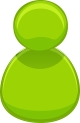
Regenerative blowers are ideal for moving large volumes of air at low pressures or vacuums. Unlike positive displacement compressors and vacuum pumps, they pressurize air through a nonpositive displacement method. Typical regenerative blower applications include sewage aeration, vacuum lifting, vacuum packaging, pneumatic conveying, concrete aeration, pond aeration, vacuum tables, drying, dust/smoke removal, air sparging, and chip removal.
Of all air handling equipment, regenerative blowers are probably the least understood. However, when system parameters fall within their range, they can be among the most cost-effective methods for moving air and producing pressure or vacuum.
Regenerative blowers are sometimes called side channel blowers or ring compressors, terms that refer to their physical construction. They can be direct or belt driven. In direct drives, the impeller is mounted on an electric motor shaft. The number, size, and angle of the blades on the impeller determine pneumatic performance as well as the relationship between the impeller and housing. Some blowers have rather flat performance curves while ...
... others have steep ones.
The impeller spins within a housing with an inboard and outboard channel. It is from this configuration that the name side channel blower is drawn. As the impeller blades pass the inlet port, they draw air in. The impeller rotation pushes air outward and forward into the channels. The air then returns to the base of the blade. As the impeller spins, the process repeats. This regeneration gives the blower its pressure/vacuum capabilities.
A regenerative blower operates as a multistaged compressor. Each blade-to-blade regeneration stage results in a slight pressure increase. Total pressure rise from air entry to discharge yields a continuous operating pressure up to 300-in. w.g. (11 PSIg) or a vacuum to 14-in. Hg with continuous flows to more than 1400 scfm (Fig. 3).
Most blowers are single stage: Air travels around the blower housing once and is discharged. Two-stage regenerative blowers can provide almost twice the pressure or vacuum of single-stage units. In a single-impeller, two-stage unit, air makes one revolution around the front side of the impeller. Then, instead of being discharged, the air is channeled to the backside of the impeller through internal porting. Air then makes another revolution around the backside of the impeller before it is discharged. Other two-stage configurations are also available, including designs that use two separate impellers in one housing or two impellers and housings.
Among the major benefits of a regenerative blower is its lack of maintenance and monitoring requirements. The impeller is the only moving part and is wear free and does not come in contact with the housing channels. Self-lubricated bearings are the only parts that wear.
Regenerative blowers are oilless and have no complicated intake/exhaust valving. Most can be mounted in any plane and, with dynamically balanced impellers, generate little vibration. Because they are nonpositive displacement compressor/vacuum pumps, they discharge air that is clean and pulsation free, which are important considerations for today's plant instruments and controls.
The majority of blower failures are caused by improper installation or operation. Regenerative blowers have close internal clearances between the impeller and housing. It is important to prevent foreign material from entering that space. Ingested debris wedging between the impeller and housing can cause the blower to lock up and lead to a catastrophic failure. A blower should always be equipped with an intake filter. A 10-micron size is usually adequate. Filters must be kept clean. A blocked filter will starve flow.
Overpressurization can also cause deadheading (zero airflow through the blower) and catastrophic failure. Some blowers tolerate deadheading, but other models (typically those above 1 hp) must have air passing through them for cooling. If air does not pass through the blower, heat builds up in the impeller causing it to expand at a faster rate than the housing. Eventually the impeller locks up with the housing and the blower fails. A relief valve prevents overpressurization and deadheading conditions and allows air to pass through the blower.
For additional information please refer to Canada Blower Co. web site http://www.canadablower.com/index.html.
Susan Terlitski
Canadian Industrial Process Designer
Canada Blower Co.
http://canadablower.com
http://canadablower.com/blowers/index.html
Add Comment
Others Articles
1. شات فلسطين: تعرف على أصدقاء جدد بدون تسجيل!Author: شات فلسطين هو شات عربي مجاني تم انشائة أواخر عام 2
2. Transform Your Space With Professional Concrete Floor Solutions
Author: Concrete Floor
3. Why Global Key Info Solutions Is The Best Web Development Company In Noida For Your Business Success
Author: Prince GKIS
4. Add Elegance And Function With Stainless Steel Bathroom Basins In Auckland
Author: Kiwi Stainless
5. Upgrade Your Kitchen With Auckland’s Trusted Benchtop Experts
Author: Kiwi Stainless
6. Top Reasons To Choose Hp Servers For Business Growth
Author: Behera seo
7. Venus Detective Agency, Noida's Top Female Detective Agency, Can Help You Find The Truth
Author: venus detective
8. Reliable And Hygienic Stainless Steel Wash Troughs In Auckland
Author: Kiwi Stainless
9. Top Considerations For Finding The Best Outsourced Accounting Services
Author: CRSP Connect
10. Bvi Business Companies Act: Key Reporting Changes For 2025 - Acquarius
Author: Acquarius
11. Stainless Steel Fabricators Auckland: Bringing Durability And Style To Your Projects
Author: Kiwi Stainless
12. Second Fashion Act Event Set For Paris In May, With Focus On Circularity - Skywire London
Author: Skywire London
13. Steel Snap Hook
Author: secure first
14. How To Store Carboxyl-functionalized Nanoparticles. Don't Make These Mistakes!
Author: Alpha Nanotech Inc.
15. Switching To Solar Energy In Canberra Is A Smart Choice For Homeowners Looking To Save On Electricity Bills While Contributing To A Sustainable Future
Author: sunboost