ALL >> Business >> View Article
Arlyn Scales Introduces Internet Connected Inventory Control System
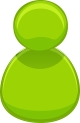
East Rockaway, NY August 15, 2008 -- Arlyn Scales Introduces Inventory Control System with Internet Connectivity
Inventory control has always been critically important for production and manufacturing. Clearly, it is important to make certain that there are enough parts to produce the correct number of assemblies. These may include fastener components, such as screws, rivets, washers, bolts, nuts and others. A wide variety of other mechanical components may be necessary, such as valves, fittings, gaskets and enclosures. Often there are also electronic and electrical devices, such as capacitors, resistors, transistors, filters, connectors, microprocessors, memory devices and converter devices. A simple assembly may only consist of a handful of parts. But more complicated devices may require hundreds or even thousands of individual components.
While a manufacturing line can be brought to a standstill if even one item is missing, financial considerations discourage overstock. Too many parts may represent hundreds of thousands of dollars of excess inventory. An efficient organization must be careful to avoid this type ...
... of financial waste. Also, components that may be in excess of those currently required need additional space for storage, and more labor to keep track of it. Additionally, there is further risk of these components becoming obsolete if there are design changes or complete model changes. Furthermore, any inventory is always subject to losses from facility failure or even theft.
Keeping track of a large number of components can be a complex assignment. Purchasing these components and assuring delivery on a timely basis can be even more demanding. The personnel resources can include purchasing agents, shipping and receiving clerks, internal stocking personnel to get the components to the right storage areas, and information technology staff to keep track of all of this. These tasks can distract an organization from their primary goal of actually building the devices in question.
Many manufacturing organizations choose to outsource some or all of these responsibilities to distributors. These distributors may contract with a number of manufacturers to handle all of their stocking requirements. The distributors have extensive purchasing staffs and may be able to make very attractive arrangements with components manufacturers, as their volumes may be very high. They will generally also have an infrastructure that is suitable for purchasing from a large number of different vendors.
One of the most significant challenges facing the distributor is monitoring the number of parts in their clients' locations. One way, of course, is to visit each location periodically and perform a manual count of each part. This can be a very time consuming process. Parts counting scales can significantly reduce this amount of time. Using this type of industrial scale, a small sample of parts is counted manually and placed on the scale platform. The operator enters the number of parts in the sample, and the digital scale will automatically calculate the weight of an individual part. Now the entire bin of parts may be placed on the scale. Knowing the weight of the bin, the scale will automatically subtract out that weight, leaving only the weight of the parts in the bin. Recalling from memory the weight of the individual part, the scale can divide this value to calculate the total number of parts in the bin. The operator may now record this, and determine if additional parts need to be ordered.
Some higher quality parts counting scales, such as the Arlyn brand, allow the operator to store many parts weights in the internal memory of the scale. Each part is stored with the part name. A menu can be accessed to see each item and part weight. Recalling this part weight allows the scale operator to skip the sampling process, making the counting process more efficient.
It would be far preferable, though, to be able to keep track of inventory remotely. Distributors clients may have a number of different locations, and some of them may be quite distant. The time and effort to perform a manual inventory, and the number of people required to do this can become quite significant.
To address these issues, a Bin Inventory Control System has been introduced by Arlyn Scales. The system consists of three major systems. Parts bins are placed on Drawers which rest on the storage shelves. These drawers can have a profile as low as 1 ½, so they will not interfere with the shelving system. Each drawer may include up to four built in scales, for four parts bins. The drawers include a digital display, which will show the weight of each bin of parts. They also act as independent parts counting scales. The piece weight of the components in each bin can be entered into the display. Also, the minimum acceptable inventory amount, and the maximum acceptable amount may be programmed into the drawer. The drawer includes red and green indicator lights for each bin. Using this system, the actual number of parts in each bin may be read from the display. A green light will be present if the inventory is within the acceptable range. A red indicator will light if it is outside that range, so that action may be taken.
While it is useful to be able to see this information locally, it is preferable for the distributor to be able to monitor this from their own central offices. Therefore the Arlyn design allows a large number of drawers to be wired together in an industrial network. Using an industry standard RS-485 network, dozens of drawers may be connected together, and may then be attached to the second major system called a network Master. This device collects the data from all of the bins in all of the drawers. It also has an Ethernet port to connect to the clients' local area network.
The final major system is the software that connects the distributor to any of the Master devices from their own location and collects and analyzes the data. Typically, whenever a system tries to access any devices from within another local area network, there are a number of security and communication challenges. Devices on an internal local area are protected from exactly this type of intrusion, as it may be a pathway for improper access. Firewall hardware and software and other types of filters will block this access. The Arlyn system securely and appropriately allows only authorized users to only connect to the parts bins on the client's network.
The distributor may access the information, in database format, from the client's drawers using any browser enabled device that is Internet connected. Of course, proper password and access information is required to connect to the system. A large number of Master devices may be programmed to communicate with the distributor's database. Each Master may be in a different location. The database is arranged so that each client will be shown as a different entity within the system.
The distributor may also program minimum and maximum inventory levels for each of the bins. Alarms will be noted in the database software for each component that falls outside of the acceptable levels.
Bin information is sent to the database at regularly scheduled intervals. These intervals may be programmed by the client. Depending on the volume of usage, and the frequency of refilling the bins, the interval may be once a day or even less often, or as often as once every few minutes. As the data is entered into the distributor's database, the date and time will also be noted. This provides further information to the distributor as to the rate of usage of those components.
Because the software and database are browser based, more than one office person within the distributor organization can access this information. For example, an account representative can view the component consumption for his client, while a purchasing agent can collect all of the items that need to be placed on order. Another example could be a situation where the client had facilities in two different locations, each of which was serviced by a different office of the distributor. Again, the account executives and purchasing agents from both locations would have the ability to access the data from both sites of the client. As an added benefit, the account executive who may have an appointment with his client could review the client's data on his web enable cell phone immediately prior to the visit. If any shortages were noted, he could already have made arrangements for restocking, as he arrives at the client's facility.
Arlyn Scales's goal is to provide clients with superiority in equipment and service unrivaled in the scale industry. For almost 30 years Arlyn has manufactured top of the line industrial weighing equipment with an accent on quality, accuracy, advanced technology and durability. From Industrial Scales to Platform Scales and everything in between, Arlyn Scales has it all.
Add Comment
Business Articles
1. Repair And Maintenance Guide For Garden FencingAuthor: Vikram kumar
2. Lucintel Forecasts The Global Palatant Market To Grow With A Cagr Of 5% From 2024 To 2030
Author: Lucintel LLC
3. Choosing The Right Gas Regulator In Florida: A Complete Guide
Author: Technico
4. Why Deer Park Learners Trust Local Driving Instructors
Author: Aintree Driving School
5. How To Properly Install And Uninstall Your Air Conditioner System With A Low Budget
Author: Neha Jain
6. What Is The Role Of Pdca In Iso 50001?
Author: William Charles
7. Step-by-step Instructions On How To Generate Inventory Reports Quickbooks?
Author: Jack Edwards
8. How To Track Employee Work Hours Efficiently With Trackhr
Author: TrackHr App
9. From Grounded To Global: 4 Ceos Rewiring India’s Aviation Sky
Author: Skyone
10. The Role Of Automation In Modern Cloud Migration Methodology
Author: Netscribes
11. Master Photo Retouching | Steps To Become A Photo Editing Expert
Author: ukclippingpath
12. Great Dependability And Performance Are The Reasons For Extensive Use Of Hydro Pneumatic Press
Author: David Camp
13. Best Lasik Eye Surgery For A Spectacle-free Life
Author: Anil Eye Hospital
14. Industrial Oven Manufacturers In Coimbatore
Author: Heatcon Sensors
15. Plumbing In North Salt Lake: Your Guide To Reliable Services
Author: Brown Jones