ALL >> Business >> View Article
Dust Collectors For Material Conveying
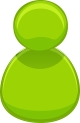
Dust collection, fume removal, and material conveying systems each have unique characteristics, but all three are similar in their dependence upon proper air velocities. Dust collection and fume removal are generally thought of as “housekeeping” systems that usually incorporate a hood at the system entry point. There are many types and styles of hoods in common use, and hood design is a subject in itself. Some state and local codes offer hood design criteria, and there are several reference texts, such as Industrial Ventilation - A Manual Of Recommended Practices, that can assist in the selection and design of hoods. In all cases the hood design should minimize turbulence and offer the lowest possible entrance losses.
Determining the minimum velocity for dust collection or fume removal is often a matter of practical trial-and-error judgment. State and local codes may dictate minimum velocities for certain materials. Reducing the velocity to near the settling point will generate the lowest overall operating cost but raises the risk of system plugging, increased maintenance costs, and lost production.
Although ...
... the differences between dilute-phase material conveying systems and dust collection or fume removal systems might appear to be minimal, there are certain distinctions that are critical to the successful operation of material conveying systems. These differences include the method of introducing the material to the hood, the velocity requirements, the duct configuration, and the fan type.
The introduction of material into a material conveying system can be difficult. The most important criterion is to feed the material into the airstream evenly. This can be accomplished by means of gravity or by a mechanical device. A hood or hopper can be used as a gravity feeder. Use of these components is limited to dry, free-flowing materials. It is important to remember that it is the velocity moving around and past the material that induces it to flow. If the entry becomes plugged with material, the required velocity cannot be maintained, significantly impeding air and material flow.
Just as designing around a velocity that is too low will impede the material conveying capability of the system, unnecessarily high velocities can also be detrimental. System resistance increases as the square of the increase in velocity. Therefore, additional energy is required to overcome that resistance. Also, the abrasive or erosive characteristics of the material being conveyed will increase with an increase in velocity, shortening the service life of all system components. Only the air volume is considered in determining the velocity. The material volume is ignored to compensate for the periods of inconsistent material loading that occur during start-up and shut-down. However, the material content of the overall airstream mixture cannot be ignored when calculating system resistance or when sizing the fan.
Fans are constant volume machines that discharge a fixed volume of air at a fixed speed. If a fan is required to handle a given volume of air and a given volume of material, it should be sized to handle the combined volume. However, in situations where greater material volumes are being handled or when the bulk material density is much lighter, the volume cannot be ignored.
The effects of the material on system resistance must be considered. Since most materials usually exhibit a lower coefficient of friction than air, a simple density correction based on the combined weight and volume of the air / material mixture would result in an unnecessarily high correction. No dependable methods of determining the flow resistance of air/material mixtures have been proven, so only reasonable estimates are available. Some researchers have theorized that the bulk material content merely acts to reduce the effective area of the pipe or duct and so ignore the density effect by calculating air resistance through the resulting smaller pipe diameter. The best method for determining the resistance of the air/material mixture is through pilot-plant testing or experimentation.
For additional information please refer to http://olegsystems.com/index.html.
Oleg Tchetchel
Systems Designer
Oleg Systems Co.
http://olegsystems.com
http://www.olegsystems.com/industrialventilation/Index.html
Add Comment
Business Articles
1. Lucintel Forecasts The Glass Fiber In The Global Marine Market To Grow With A Cagr Of 3.7% From 2024 To 2030Author: Lucintel LLC
2. Lucintel Forecasts The Glass Fiber In The Global E&e Market To Grow With A Cagr Of 3.9% From 2024 To 2030
Author: Lucintel LLC
3. Lucintel Forecasts The Global Frp Pole In Telecommunication Market To Grow With A Cagr Of 6.5% From 2024 To 2030
Author: Lucintel LLC
4. Lucintel Forecasts The Global Frp Pole In Power Transmission & Distribution Market To Grow With A Cagr Of 6% From 2024 To 2030
Author: Lucintel LLC
5. Lucintel Forecasts The Global Frp Pipe In Oil And Gas Market To Grow With A Cagr Of 5.1% From 2024 To 2030
Author: Lucintel LLC
6. Lucintel Forecasts The Global Frp Pipe In Chemical Market To Grow With A Cagr Of 3.6% From 2024 To 2030
Author: Lucintel LLC
7. Adopt A Modern Telecom Commission Management System To Fix Revenue Leakages
Author: Kevin
8. Quality Steel Pipes And Tubes With Commitment And Trusted Service
Author: CONTENT EDITOR FOR SAMPHIRE IT SOLUTIONS PVT LTD
9. Lucintel Forecasts The Global Foam Core For The Construction Market To Grow With A Cagr Of 3.7% From 2024 To 2030
Author: Lucintel LLC
10. How Important Is Mutual Fund?
Author: Sagar Shah
11. What Do You Need To Know About Customize Your Own Clothes
Author: Guangzhou Beianji Clothing
12. Detailed Tips To Choose Quality Cabinets And Joinery Melbourne
Author: William Harvey
13. Lucintel Forecasts The Global Foam Core For The Transportation Market To Grow With A Cagr Of 5.4% From 2024 To 2030
Author: Lucintel LLC
14. Silicone Sealing Foam Cord: The Valuable Option For You
Author: Dongguan Senma New Materials Technology Co., Ltd
15. How Investment Banking Companies And Credit Solutions Elevate Wealth Management
Author: Drishti Desai