ALL >> Education >> View Article
Basics Of Green Belt Six Sigma Training
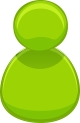
Are you ready to improve your processes with a proven method?
Your customers are complaining too much, production costs are too high, your problems are repeated again and again, your processes are not stable, improvements expected to bring benefits do not work, if you recognize yourself in either of these situations, then Six Sigma can help you. To minimize your problems in a radical and permanent manner, you should consider a method that has proven itself in several types of company. This approach, which uses tools from different levels of complexity is within the reach of businesses of all sizes, whether in the manufacturing sector or in services. You will finally be able to think in terms of continuous improvement in every phase of your work. Given by the "worker-trainers" with practical experience of this methodology, this course provides the teachings of the "real life"! The application tool how-to and interpretation of statistical analysis will be honored. At the end of this course, estimate the capacity of a process will no more be the secrets for you.
Goal
The
... href="http://www.apolloiec.com" title="Green Belt Six Sigma Training">green belt six sigma participants will be able to clearly define a good project for continuous improvement to build a successful team and to determine the factors and parameters causing the problems and eliminate them. It will be able to develop an appropriate plan for the implementation of solutions and to check the results. The realization of the benefits can then be calculated easily.
Earnings
Identification of good projects that will contribute to the success of the company
Learning various basic tools (brainstorming, histogram, etc.) and advanced (quality function deployment, FMEA, etc.).
Learning effective ways to choose solutions and implement them permanently.
Who Should Attend?
Managers and professionals, who identify, manage or carry out a continuous improvement project in their organization. Six Sigma Training participants must have at least two years of relevant experience in the workplace and knowledge of basic Microsoft Excel.
Specific objectives
Overview of Six Sigma
Background of continuous improvement
Applications for the improvement of products and services
The five phases and their indicators
Review of some statistical concepts and graphs
Mean, median, standard deviation
Histograms
Normal curve
Define a continuous improvement project - Phase 1
Selection of relevant projects
Team training
Project Definition and "SIPOC"
Definition of the objective
Measuring parameters and the current performance - Phase 2
Definition of indicators related to objectives and data collection
Basic tools: brainstorming, cause-effect diagram, etc.
More advanced tools: quality function deployment, FMEA, etc.
Mapping process and performance indicators
Process capability
Analyze the most important factors and causes of the problem - Phase 3
Graphics and their interpretation
Understanding natural variation and assignable
Identification of factors to improve
Improvement (innovation) by choosing the best solution and reducing variation - Phase 4
Selecting the solution
Tools creative
Evaluation of scenarios
Pilot plan and implementation plan
Monitor changes and maintain the gains - Phase 5
Establishment of a monitoring plan
Lessons Learned and audits
Evaluation of gains
Control charts
Teaching strategies
A case study is used as a backdrop for learning. Participants progress through the case study, identification of the problem to the control plan and the implementation of solutions. At each stage, several exercises are presented to participants and invited to share their experience. Participants must pass two exams: the end of the first block of 2 days (30% weighting) and at the end of the second block (weighting 65%). The final exam includes a practical exercise related to a problem chosen by the participant. The pass mark is 80%. In addition, participants will demonstrate an attendance four days of training (5% weighting).
Add Comment
Education Articles
1. Can Ielts Academic Be Used For Immigration?Author: lily bloom
2. A Course On The Importance Of Upskilling At The College Level
Author: stem-xpert
3. Global Clinical Trials: Unveiling India’s Booming Market Outlook For 2025!
Author: Aakash jha
4. The Power Of Micro-influencers: Why They Matter More Than Ever
Author: dev
5. Digital Marketing Course In Dadar
Author: Sanchi
6. The Best Sre Course Online In India | Sre Training
Author: krishna
7. Top Google Cloud Ai Training In Chennai - Visualpath
Author: visualpath
8. Best Dynamics 365 Business Central Online Training - Hyderabad
Author: Susheel
9. The Best Data Engineering Course In Hyderabad - 2025
Author: naveen
10. Microsoft Dynamics 365 Course In Hyderabad | D365 Training
Author: Hari
11. Top Salesforce Marketing Cloud Training In Ameerpet
Author: Visualpath
12. Top Snowflake Course In Ameerpet | Snowflake Online Training
Author: Pravin
13. List Of Top Online Ma Colleges In India
Author: Study Jagat
14. Scrum Master Training In Bangalore | Scrum Master Classes
Author: visualpath
15. Mendix Online Training | Mendix Online Certification Course
Author: himaram