ALL >> General >> View Article
Office Cubicles And Crafting The Rfp
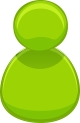
The following paragraphs describe considerations that should go into crafting an RFP (Request for Proposals) to office furniture dealers and distributors supplying technology-compatible modular office systems. Managers may place more weight on certain considerations over others, but should insist that their vendors strive to meet all of these desirable features.
1. Office Cubicles Panel Considerations
Start with the basics. Modular systems get a lot of hard use. Structural systems (the skeleton or framework) that support panels, accessories and work surfaces should be constructed of 16-gauge cold-rolled steel. This provides strength and rigidity when in use and enables the systems to remain distortion-free during MACs. Panel tiles should be at minimum 24-gauge 1 BOSTI - The Buffalo Organization for Social and Technologic Innovation steel while shelves and filing cabinet drawers should be of 18 and 20-gauge steel.
Most manufacturers offer solutions that restrict flexibility in managing space and placing components. A new approach called off-modular design allows much greater freedom in locating bins, shelves ...
... and divider panels. Similarly, factory-assembled structural systems were traditionally limited to what fits into an elevator and confined designs to linear or right angle configurations. Newer technologies such as knockdown and ready-to assemble structural elements overcome traditional restrictions and, as a bonus, add flexibility while reducing production and erection costs. These new features give designers and installers virtually unlimited options in tasktailoring today's office and workspace layouts.
Another benefit of this new construction technology is the stackable panel frame - an innovation taking office furniture systems literally to the next level. Load-bearing walls 30 inches to ceiling high can be constructed, moved and reconfigured quickly and efficiently to create spaces in harmony with the work being performed or support a wholesale job change. Size, height and functionality limitations disappear when specifying load-bearing stackable panel systems that are shipped with knockdown, ready to assemble structural components. Bins and shelving can be attached where needed; glass, solid and airflow panels are easily and intuitively inserted, moved or removed.
2. Office Cubicles Cable Management
Cable management for power and voice/data/video is a major challenge to be addressed in technology-intensive workplaces. Vendors should confirm that their cabling installers are trained and certified for power and data installations, and that all wiring and cabling conform to local codes. Power systems should not share channel space with voice and data systems, and should be available for positioning either above or below the work surfaces. The power distribution system should provide a minimum of one dedicated circuit plus a maximum of 3 common circuits sharing a 10-gauge neutral wire for each workstation. Duplex receptacles should be easily installed and removed. The design should support plug and play moves, adds and changes (MACs) by trained office technology personnel.
The horizontal voice, data and video cabling system serving the office must conform to applicable industry standards such as TIA/EIA 568-A and 569-A2. More recently, the TIA has introduced new guidelines in response to the growth of open offices. Called TSB (Technical Services Bulletin) TSB-753, it specifically addresses cable management for office layouts characterized by frequent MACs.
Most office cubicle manufacturers are only now beginning to address cable management. The pioneer was MAiSPACE, Inc of Fairfield, NJ in collaboration with The Siemon Company, Watertown, CT, introduced MAiSPACE as the first office cubicle modular system in compliance with TSB-75. It uses a simple plug and play design that permits employees equipped with a minimum of training to handle in a few hours the MACs that formerly would require trained outside technicians working several days to accomplish. The cost of change can drop to $50 per cable vs. $500 in conventional systems.
Add Comment
General Articles
1. Categorization Of Plant Life CycleAuthor: Anthea Johnson
2. Commercial Spaces Need Style Too! Transforming Cafés & Resorts With Custom Pergolas
Author: Noor Mariam
3. Level Up Your Hana Adventure: Why An Audio Tour Is Your Best Road Trip Companion
Author: Katie Law
4. Best Erp Software Solution Company In Noida For Schools And Colleges
Author: CONTENT EDITOR FOR SAMPHIRE IT SOLUTIONS PVT LTD
5. Hinduism: Environmental Friendliness And Protecting Nature
Author: Chaitanya Kumari
6. From Ai To App Store: How Generative Tech Is Reshaping Ios Experiences
Author: Sara Wilson
7. Faston Service In Noida — Reliable, Affordable & Quick Home Ac Repair Services
Author: faston services
8. What Are The Uses And Benefits Of A Vegetable And Fruit Dryer?
Author: DYNAMIC DRYERS INTERNATIONAL
9. Primary Care Without Insurance In Raleigh
Author: satyamprimarycare
10. All Four Paws Offers Champion English Cream Golden Retriever Puppies In Indiana
Author: Geroge
11. Box Truck Wraps: The Ultimate Moving Billboard For Your Brand
Author: Saifee Signs
12. Generative Ai And Data Science Course In Hyderabad
Author: Hari
13. Mca Guidelines For Company Name
Author: Startupporta Business Services
14. Seo Services In Chennai: Boost Your Online Visibility With Proven Strategies
Author: istudio technologies
15. Best Internet Marketing Service In India
Author: Matrix Web Studio