ALL >> Business >> View Article
Copper Forgings Seamless Rolled Rings
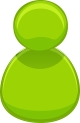
Custom forgings generated revenue of over $8 billion dollars in the United States, Canada and Mexico in 2006. The areas covered by the custom forging category include impression die forging (or closed die forging), open die forging and seamless rolled ring forgings. Seamless rolled rings accounted for over $1.2 billion of the total in 2006 and represented an astounding 42% increase over the previous year.
Like open die forging, there is a lot of flexibility in the size and shape of the products that you can make. Ring diameters can range from a few inches up to 30 feet in diameter and the weight of the material can be less than an 1 pound to up over hundreds of thousands of pounds. There are literally thousands of different shapes that can be produced with contours on the outside, inside or both diameters of the part.
In the process, the raw material, which is typically round in shape, is pierced or punched in the center. It is then placed on a mandrel and the piece is then rolled, squeezed or even pounded circumferentially to create a ring (or donut shape). The continuously applied pressure reduces the wall ...
... thickness and increases the inner and outer diameters and creates the ring shape.
There are many advantages to rolled ring processes and they include the following:
1. There is the economic advantage of significant material savings when compared to plate products for example. You can use up to 66% less material when using this process
2. Another economic advantage when compared to the closed die process is that no tooling charges are required here
3. The time required to machine the final product is minimized because of the near net shape. This not only yield economic advantage but could also decrease the lead time in getting the product to you.
4. Finally, in this process, the grain flow of the material can be easily controlled and thereby producing product that has superior impact and structural strength.
In fact, from a performance standpoint, the forging process provides unmatched capabilities particularly in the power generation industry, whether for specialty bearing or end rings in motor rebuilds. Other industries with safety or critical applications include mining, aerospace and heavy equipment. OEM's and machine shops that process parts in these industries rely on forged products for their needs.
Not only are carbon and alloy steels popular materials for this process, but many nonferrous alloys, including aluminum, copper and titanium as well as nickel-base alloys. Some of the common nonferrous materials include C10100 (OFE or Oxygen Free Electronic), C46400 (Naval Brass), C18200 (Chromium Copper), C70600 (Copper Nickel) and C18150 (Chromium Zirconium Copper).
Add Comment
Business Articles
1. Stem-xpert At Web Summit Qatar 2025, Pursuing Innovative Solutions In Stem-as-a-serviceAuthor: stem-xpert
2. Deepseek’s Rapid Rise: Disrupting The Ai Market Amid Controversy
Author: Iconic success
3. Reimagining Customer Services With Microsoft Dynamics 365 Implementation
Author: Maria
4. Upcoming Developments In Ss Flanges: Possible Effects On Different Industries
Author: Neelam Forge India
5. Mg Hector 5 Seater Price In Chennai: A Detailed Review
Author: balaji
6. Mg Hector Ev Price In Chennai: A Comprehensive Overview
Author: balaji
7. Spring Marketing Trends: How Print And Video Can Refresh Your Brand
Author: Devin Herz
8. Auto Transport Services In South Carolina
Author: Secure Car Shipping
9. Authentication Of Australian Certificates In Canada: A Complete Guide
Author: anzilanx
10. Low Maintenance Plants For Home Landscaping
Author: Apunga Landscapes
11. The Ultimate Guide To Rocking Chairs – Comfort, Style, And Elegance
Author: tushar
12. Bioethanol Market Size Insights Forecast 2024-2030
Author: Nilam Jadhav
13. Touffy Fabric Upholstered Rocking Chair – The Perfect Blend Of Comfort And Elegance
Author: tushar
14. Maximizing Efficiency: Why Small Businesses Should Outsource Bookkeeping And Financial Services
Author: KMK Ventures Pvt Ltd
15. Big Patient Data And The Future Of Real World Evidence: Learnings From Biotechx 2024
Author: Industry Chronicle