ALL >> Business >> View Article
Industrial Reverse Osmosis Systems
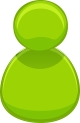
A- INTRODUCTION
Any industrial RO product water usually requires post treatment, regardless of the types of RO device, the chemical nature of the RO membrane, and the intended application of the water. Post treatment requirements depend primarily on the application and must be determined on a case-by case basis. For many industrial applications, post treatment consists of demineralization by means of ion exchange and disinfection with ultraviolet radiation. Post treatment for municipal applications includes pH adjustment with bases or a degasifier ,or both, and disinfection with chlorine. Details of post treatment are given for RO product waters from brackish as well as sea water sources.
Post treatment of any industrial reverse osmosis product water is usually required. The degree and type off post treatment needed depends primarily on the application. For example, water for potable use requires disinfection for health reasons and treatment to prevent corrosion of water mains and household plumbing. If hydrogen sulfide (H2S) is present, degasification is also required.
Water used in high pressure boilers ...
... must be completely demineralized to prevent scaling and deoxygenated to minimize corrosion. Because water used to decontaminate microchips in the electronics industry must be ultra-pure, RO post treatment includes complete demineralization.
The most often used post-treatments are demineralization, pH adjustment, disinfection, and degasification.
B-1 COMPLETE DEMINERALIZATION:
The total dissolved solids (TDS) in the RO product depends on the TDS of the feed water, the ionic composition of the feed water, the feed pressure, the RO device, and the recovery rate of the RO system. Brackish water RO systems usually reduce the TDS by 95-98 percent.
The RO product of a sea water system typically has a TDS of 350-500 mg/l. Some applications, such as makeup water for high pressure boilers, rinse water for the electronics industry, and water for various chemical and pharmaceutical processes, require complete demineralization.
This is accomplished by ion exchange post treatment of RO permeate. Although ion exchange materials were discovered early in this century, the technology was not economically attractive until stable synthetic ion exchange resins were developed during World War II. Almost all of the inorganic salts are removed when the RO product water is passed through ion exchange resins.
Two types of ion exchangers are needed: a strong acid cation exchanger and a strong base anion exchanger.
The strong acid cation exchanger resin is a copolymer of styrene and divinylbenzene that contains sulfonate groups (SO3-). The resin in the acid form exchangers hydrogen ions for cations (Eqs 1 and 2).
Ca(HCO3)2 Ca
Mg(HCO3)2 + 2HZ 2Z Mg + 2H2O + CO2 (1)
2NaHCO3 2Na
CaSO4 Ca
MgCl2 + 2HZ 2Z Mg + 2H2SO4 + 2HCL (2)
2NaCl 2Na
A degasifier placed between the two ion exchangers removes carbon dioxide (CO2) and reduces the load on the anion exchanger, resulting in less frequent regeneration. If the reverse osmosis product has low concentrations (< 10 mg/l) of CO2 and bicarbonate (HCO3-), the degasifier would not be used because it would not be cost effective. The concentrations of CO2 and HCO3- in the RO product are directly proportional to their concentrations in the RO feed. Since CO2 is not rejected by RO membranes, RO systems using acid pre-treatment will contain a higher concentration of CO2 in the product. IF the RO pretreatment involves ion exchange softening, a higher operating pH can be used to yield a lower level of CO2 in the product. At a higher feed pH, aramid membranes have a higher HCO3- rejection and consequently result in a lower level of HCO3- in the RO product.
Some ion exchange demineralizing systems have a mixed bed exchanger after the strong base exchanger. The mixed bed contains both strong acid cation and strong base anion resins in one vessel and removes any residual salts. To regenerate a mixed bed, it is necessary to separate the resins hydraulically, treat each resin with its regenerate, and then remix the resins before use. For some applications, a mixed bed alone can give the required demineralization.
Although packaged ion exchange units are available, most large systems are deigned for individual feed water and operating needs. The design of the pressure vessel that contains the ion exchange resins, as well as the operating procedures for backwashing, regeneration, and rinsing, is readily available form the suppliers of such equipment. Suppliers can size ion exchange systems to the desired final water quality.
Cation exchange resins are susceptible to iron, copper, and aluminum fouling, whereas anion exchange resins are fouled by organic material. Both resins are susceptible to colloidal fouling.
Because strong oxidizing agents, such as chlorine, degrade ion exchange resins, any chlorine in the RO product must be removed upstream of the ion exchange system by an activated carbon filter or the addition of sodium bisulfite. Since chlorine also degrades polyamide RO membranes, systems using this type of membranes should dechlorinate the feed water upstream of the industrial RO system.
Systems using cellulose acetate membranes may have controlled amounts of chlorine in the RO feed to prevent biological attack of the membrane. In these cases, the chlorine in the system’s product water must be removed before the water is passed through the ion exchange system. Some RO systems with aramid membranes use iodine in the feed as a disinfectant. Because some of the iodine will pass though the membrane, an activated carbon filter or sodium bisulfate addition is used ahead of the ion exchange system to remove iodine from the RO product water.
The aggressive effluent from an ion exchange system will attack some piping and tank materials. This means careful consideration must be given to the materials of construction for storage and distribution. Because the ion exchange effluent will rapidly adsorb CO2 from the air and become acidic, it must be protected from exposure to air.
B-2 PH ADJUSTMENT
With either a brackish water or a sea water RO system, the product water is almost always acidic, typically pH 5.5-6.9. If an industrial application requires a more acidic product water, acid (hydrochloric acid [HCl] or H2SO4) can be added. However , for most applications, a higher pH is required.
Adding base (NaOH, sodium carbonate [Na2CO3], or lime) will increase the pH as well as the TDS. To increase the pH of the RO product water to 8.2 by adding NaOH, the ratio ® of alkalinity to CO2 must be 100:1. To calculate the amount of 98 percent NaOH needed to raise the pH to 8.2 for case 1, Eq 4 is used:
R = 100 = (ALK + 1.23X)/CO2-1.08X) (4)
In which X = the amount (milligrams per liter of NaOH needed to raise the pH to 8.2, ALK = alkalinity (milligrams as CaCO3/l) before base addition = 30 mg/l, and CO2 = CO2 (milligrams as CO2/l) before base addition = 102 mg/l. (Product value before adjustment)
It can determined from Eq 4 that 93.1 mg/l of 98 percent NaOH is required to raise the pH to 8.2. At this new pH, the alkalinity is 30 (product alkalinity before adjustment) + 1.23 (93.1) = 144.5 mg/l and the CO2 content is 102 - 1.08 (93.1) = 1.5 mg/l. Adding 93.1 mg NaOH/L increase the sodium level by 93.1 x 23/40 = 53 mg/l as ion (23/40 is the molecular weight of sodium divided by the molecular weight of NaOH).
B-3 REDUCING CORROSIVENESS
Although adjusting the pH neutralizes the acid, the RO product water may still be corrosive. For potable applications, the corrosiveness of the water must be controlled to protect water mains and household plumbing. The Langelier saturation index (LSI) is one parameter used to determine the corrosiveness of water.
LSI = pH - pHs
in which pH = the actual of the water, and pHs = the pH at which the water is saturated with CaCO3.
If the LSI is negative, the water has a tendency to dissolve CaCO3, and if the LSI is positive, the water has a tendency to precipitate CaCO3. If CaCO3 tends to precipitate on metal surface (positive LSI), some protection against corrosion is achieved.
The pHs is calculated using Eq. 7:
pHs = pCa + pAlk + C (7)
in which pCa = -log [Ca2+], pAlk = -log [HCO3], and C = constant which varies with TDS and temperature.
For case 1 before neutralization, the concentrations of Ca2+, HCO3-, and TDS are 25 mg as CaCO3/L, 30 mg as CaCO3/L and 142 mg as ion/L respectively.
Another parameter used to asses the corrosive nature of water in the Ryznar stability index (RSI), which is defined as follows:
RSI = 2pHs - pH
Several techniques are used to stabilize RO product water. The technique selected will depend on the final water quality needed and the application. The more frequently used techniques for stabilization are:
Blending the RO product water with the raw or other water source.
Using lime to adjust the pH and thus increase the Ca2+ concentration
Adding CO2 and adjusting the pH with lime to increase both the Ca2+ and the alkalinity concentrations
Adding corrosion inhibitors.
Blending is best illustrated using case 1 product water and the raw water from which it was obtained.
B-4 DISINFECTION
The same disinfection techniques used for other water can be used to disinfect RO product water. The application determines what disinfecting technique, if any, is used. The two procedures used most often are ultraviolet radiation (UV) for industrial applications and chlorination for municipal applications.
ULTRAVIOLET RADIATION. The disinfecting affect of UV light is believed to be associated with its absorption by various organic compounds in living organisms, with the resultant breaking of chemical bonds appearing to cause deadly biochemical changes.
The most common UV light source is a low pressure mercury vapor lamp, which emits a wave length of 253.7 nm. The degree of disinfection is a direct function of both exposure time and intensity. If the product of the time and the intensity is the same, the effectiveness of the disinfection will be the same, regardless of whether a short exposure time and high intensity or a long exposure time and low intensity are used.
The UV dosage (which is expressed in micro-watt-seconds per square centimeter) required for effective disinfection varies, depending on the organism (bacteria, yeast, mold spores, viruses, protozoa, or fungi). A typical UV system is designed to deliver a dose in excess of 30000 W-s/cm2.
Commercial UV systems vary in their design. Some systems seal the lamps inside quartz sleeves and require the lamp to be immersed in the flowing water. Quartz is one of only a few materials that are essentially transparent to UV light at 253.7 nm. Another UV system design requires that the water be passed through tubes made of PTFE fluorocarbon, with the UV lamps located outside of the tubes.
The PTFE not only permits the UV light to pass through it into the water, but its non wetting surface also prevents buildup of slime and debris, thus minimizing tube fouling. Commercial UV systems are available for flows ranging from 5 to 3000 gpm (0.3 to 189 l/s). Suppliers of UV systems can provide details of system design, operating costs.
The main advantage of the UV disinfecting technique is that no chemicals are added to the water. For this reason, UV treatment of RO product water has been used extensively in industrial applications, particularly the electronics industry. The UV system is typically installed down stream of the ion exchange deminiralizers. Because RO product water has an extremely low turbidity, UV light is particularly effective for disinfecting it.
The main disadvantage of UV disinfection is the lack of a residual disinfecting capacity. Biological recontamination downstream of the UV system therefore cannot be tolerated.
CHLORINATION: For drinking water applications, the RO product is typically disinfected by adding chlorine. In large systems, chlorine (Cl2) gas is added to the water, whereas operators of small systems generally inject an aqueous solution of sodium hypochlorite (NaOCl). Although the mechanism by which chlorine disinfects water is not completely understood, the disinfecting species is hypochlorous acid (HOCl), regardless of whether Cl2 gas or NaOCl is used.
( Eq13 and 14)
Cl2 + H2O HOCl + H+ + Cl- (13)
HOCl H+ + OCl- (14)
The final concentration of HOCl is determined by pH. The efficiency of chlorine disinfection is a function of the concentration of chlorine, contact time, pH, and water temperature. Increasing the concentration, contact time or water temperature increases the effectiveness of disinfection.
With proper chlorination, diseases associated with drinking water, such as typhoid fever, cholera, amoebic dysentery, gastroenteritis, and schistosomiasis, will be prevented. For effective disinfection, the chlorine and water must be thoroughly mixed, and after a contact time of about 30 min, a residual chlorine concentration must be present. The disinfection of RO product water is generally achieved with a residual chlorine level of 0.5 - 1.0 mg/L. Although only proper bacteriological tests can determine the effectiveness of chlorine disinfection, frequent measurements of residual chlorine should be made.
Product water from RO system contains very low levels of compounds that react with chlorine, such as Fe2+, Mn2+ and organics. Thus, the amount of chlorine required for disinfection can be quite low compared with that required for disinfection of raw surface or well waters. Also, the low concentration of organics minimizes or eliminates the formation of trihalomethanes and other chlorinated organic compounds, which have been of recent concern.
If the storage of Cl2 or NaCl solution is not desirable, it is possible to make NaCl on site by the electrolysis of a sodium chloride (NaCl) solution. (Eq. 15)
The electrolytic generation of NaOCl is particularly attractive if the NaOCL solution is available in the form of seawater.
At the
cathode 2Na++2e- 2Na
2Na+2H2O 2NaOH+H2
At the
anode 2Cl- -2e- Cl2 (Eq. 15)
Cl2 + H2O HCl + HOCl
Overall
reaction 2NaCl + 3H2O NaOCl + NaCl + 2H2O + H2
Electrolyzes usually use titanium electrodes and have an anode that is plated with platinum. If electrolyzers are arranged in series, with recycling of the solution, a Cl2 concentration of up to 3g/L can be obtained from seawater. If only 1 mg Cl2/L is required to disinfect the RO product water, addition of the chlorine-seawater solution will increase the TDS of the RO product water by about 10-15 mg/L.
Regardless of whether an electrolyzer, Cl2 gas, or a NaOCl solution is used to disinfect the RO product water, the supplier of the equipment must be consulted about the system design and operating and safety procedures.
B-5 SUMMARY
Post treatment requirements for RO product water will depend primarily on the application and must be determined on a case-by case basis. The post treatments described in this essay are those used most often, but they do not encompass all possible. Post treatment processes must be properly operated, maintained, and monitored.
Industrial RO
Industrial Reverse Osmosis
Contact Us:-
Pure Aqua, Inc.
2230 South Huron Drive
Santa Ana,
CA 92704 USA
Tel: (714) 432-9996
Fax: (714) 432-9898
Add Comment
Business Articles
1. Lucintel Forecasts The Global Satellite Operations As A Service Market To Grow With A Cagr Of 13.3% From 2025 To 2031Author: Lucintel LLC
2. Lucintel Forecasts The Global Satellite Operation As A Service Sale Market To Grow With A Cagr Of 13.5% From 2025 To 2031
Author: Lucintel LLC
3. Ticket Booking Api
Author: RishiHassan
4. Jewelry Photo Magic: Unveiling The Tricks Of Professional Editing
Author: ukclippingpath
5. How Outsourced Accounting Services Improve Cash Flow Visibility
Author: Harsh Vardhan
6. 5 Ways To Make Homes Safer For Seniors
Author: Jack Jones
7. اكتشفي أناقتك مع متجر عبايات: دليلك للتسوق المثالي
Author: Max
8. When Is Assisted Living Needed? 5 Signs To Watch Out For
Author: Jack Jones
9. How To Document Nonconformities In Iso 22000 Audits
Author: Jane
10. Elevate Your Career Opportunities With A Supply Chain Management Certification
Author: jayesh
11. Kpi Vs. Okr: Understanding The Difference For Smarter Goal Setting
Author: TrackHr App
12. Explore The Fascinating Businesses And Landmarks Found Along Luz Church Road
Author: jayesh
13. High Temperature Superconductors Market Size & Share, Analysis 2031
Author: Andy
14. Maximize Medical Practice Profits With Expert Revenue Cycle Management In Houston
Author: patriotmedbill
15. Enhancing Quality Of Life: The Role Of Senior Living Property Management Companies
Author: Trinity Diaz