ALL >> Education >> View Article
A Quality Management Plan
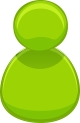
A Quality Management Plan
Introduction
Quality management is a crucial factor in the success of an organization in both manufacturing and service industries. Quality is examined on the basis of various factors, including being durable, safe, aesthetic, and reliable besides its performance levels (Armstrong 2006). Total quality management encompasses concepts such as control, assurance, and total quality management as well as the ISO system. Moreover, it can be assessed from the view of manufacturer, product, or the user. Therefore, quality management refers to the plans, choices, tests, and designs involved in the production of a quality product that has the capacity to meet customer requirements. It also entails operations to be undertaken to sustain the target level of excellence. The objective of this research paper is to examine quality management frameworks and their application in organizations as well as the impact of applying the Six Sigma in the long term with a case study of the Motorola Company.
History of Quality
Quality dates back to the medieval times in Europe during the craftsmanship ...
... era when workers formed unions referred to as guilds. This was copied through to the 19th century with products undergoing inspection up to the industrial revolution. In the beginning of the 20th century, the practice of quality emerged with the Second World War. This was as a result of inspection of bullets per product and simplification of the manufacture process without lowering quality (American Society for Quality, n.d). To enhance compatibility of the bullets with different rifles, standards were developed and published coupled with the introduction of statistical methods of ensuring quality as well as sampling. Total quality as a concept was thus developed in the US and embraced in Japan with researchers such as Deming emphasizing on enhancement of organizations on the basis of processes and procedures. Total quality management was later embraced in the automobile sector of the US and lately into sectors such as healthcare and education.
Quality Management Frameworks
ISO 9000
Quality management is also guided by eight other principles as expounded by the International Standards Organization (ISO). These are focus on the customer, systems, and process approach besides the factual approach and engagement of people. The ISO standard is a framework for internationally accepted standards of quality. It outlines the requirements of a quality management system that applies to all organizations despite differences in size or ownership. In addition, it creates guidelines and standards for performance as well as aspects of training and financial elements. This framework is important to the organization as it plays a major role in customer satisfaction. This is facilitated by the systematic framework it lays down for organizational procedures (ISO 2011). Moreover, the framework is flexible and can be implemented in various sectors and businesses with diverse cultures as it puts forward requirements for quality rather than rules for the organization to meet. ISO is also open to self-audit by the organization but can be checked by clients or independent certification agencies. The principles advanced by the quality framework are suitable to Motorola and enable it to develop and deliver products that correspond to international standards.
Canadian Awards for Business Excellence
The Canada Awards for Excellence is a framework for quality management that was adopted by the Ministry of Industry in 1984 and implemented by the National Quality Institute. It was created on the basis of the Baldbridge Model to award organizations in terms of functions. The National Quality Institute (NQI) had an objective of instilling excellence for organizations in Canada. This was achieved through strategic frameworks and principles of quality as well as practice and certification as per the NQI standards. The framework consists of guidelines for excellence, customer focus and planning in addition to leadership and management of processes. Moreover, it contains principles on people focus and performance of business as well as partnerships. The award recognizes achievements with the quality award being presented to the organizations satisfying or exceeding the criteria. This includes award of certificates of Merit for companies working towards excellence and are likely to win the awards.
The tenets of the award are linked to the success of the organization. For instance, leadership is defined on the basis of ability to change the actions and thinking frameworks of management. Performance in the organization is thus ensured through top level management that facilitates and directs change. The framework also emphasizes that excellence in quality is attained through teamwork and concentration on the customer. In addition, excellence is associated with management that is founded on prevention processes as the organization is regarded as a network that results in value addition. Excellence thus ensures enhancement of performance by altering the entire system (Porter, Tanner, & Centre for Business Excellence, 2004:164).
European Business Excellence Model
The European Business Excellence Model was created in 1988 by the European foundation for quality management for evaluating business processes. The framework ensures quality by satisfying the needs of the customer and staff besides ensuring performance and acceptance by the society. The framework focuses on the business with points being assigned to principles referred to as enablers while others are categorized as results. In this framework, the results comprise its attainments and outcome while the enablers class constitutes strategies used in operating the business.
The enablers in this case include aspects such as the policy framework and strategy in use in addition to the resources applied in the process and individuals involved. The results category in the other hand contributes to organizational success on the basis of the outcomes of various stakeholders (Baškarada, 2009:38). These include society, the customer and the people in the organizations. The award therefore recognizes the contribution of the organization to society from perceptions created by people. This is in addition to the living standards and impact on the environment as well as other resources. The framework would be suitable to the Motorola company as it enhances business processes. This means that the use of the framework at the Motorola Company is likely to result in appropriate policies and positive outcomes.
Quality Award in China
The Quality Award in China was developed from the Malcolm Bridge National Quality Award to create suitable business environment for Chinese businesses. The framework used by this award emphasizes on quality through credibility and formulation of strategies for developing brands. It also focuses on development with due regard to its sustainability. Moreover, it focuses on the element of culture such that it is flexible and easily adaptable to the specific conditions of a country. It is also based on the theory of knowledge by Deming that advocates for cautious application of best practices. The framework is thus applicable to Motorola for use in its global network that comprises of different organizational cultures with a common need for quality management (Evans 2007). An application of the framework to the Motorola company would enable it develop quality standards that correspond to the specific situation of the firm in its global network.
Australian Business Excellence Award
The Australian Business Excellence Award is a framework for leadership and development. It is designed to clarify the direction for the organization so as to attain its goals while striving to enhance its results and procedures. It also sets principles on consumer value at present and the future with strategies for improvement and innovation. Moreover, it requires the organization to utilize data and information so as to improve the decision-making process. The success of the organization is also achieved through the framework that asserts that sustainability is associated with capacity to develop and deliver value for all stakeholders. It also advocates for continual improvement on the part of leadership so at to create conditions for application of other quality management principles (ABEF n.d.).
This framework can be applied to the Motorola Company to improve outcomes and sustainability as well as ensure participation of all in the work system. The award is divided into four categories with the business improvement level being in recognition of companies working towards excellence. The award level targets companies with the required practices that are named as the finalist. The categories also encompass the gold and prize levels. The ward therefore ensures success in the organization by focusing on the company as a whole and recognizing the fact that management is an interconnected process.
Malcom bridge framework at Motorola
The Malcom Balbridge framework consists of a model for warding business excellence used for self assessment. The award utilizes a criterion that aims at enhancing success of the firm and increasing its competitive advantage. This is achieved through emphasis on the value of customer as well as enhancing the performance of the organization. It is based on concepts such as leadership, strategic planning and customer value as well as organizational learning. The framework emphasizes on the concept of leadership whereby is expected to direct the organization and develop values and balance. In addition, senior leadership is mandated with governance and takes care of other aspects such as modeling appropriate behavior, communication and training. It is also expected to develop strategies that aid decision making processes in order to attain organizational objectives. The concept of leadership at the Motorola Company is ensured by the intervention of senior management in quality through a show of commitment that steers the organization to success.
Customer Focus and Strategic Planning
The framework also emphasizes on the implementation of strategies that result in excellence fro the view of the customer. This implies that the organization that qualifies for the award has to be able to consider the attributes of its products and services to ensure that they add consumer value. This is achieved through capacity to satisfy and retain the customer besides being loyal to them. It also requires organizations to minimize the occurrence of errors, mistakes or defects in its products and services. Customer focus at the Motorola Company is taken into account by the consideration of the position of the customer in all strategic plans made by the company. This implies that the company considers the definition of quality form the view of the customer. Strategic planning on the other hand is advanced by the framework in terms of deployment of strategies. It is judged on the basis of the capacity of workforce planning to cater for the requirements and capacities of the employees. It is regarded as the use of various techniques and tools to predict about the future of the organization. The information obtained is later used in planning resource utilization and decision-making (Hertz, 2007). The Motorola Company applies the strategic planning concepts in its business strategies.
Human resource focus and Learning
The organizations are also analyzed on the basis of learning approaches and strategies that are modified to ensure that particular goals are achieved. The process is thus expected to constitute daily routines and applied in efforts to resolve problems in the organization. In addition, personal learning is considered a mechanism for enhancing the performance of employees through new skills. The Malcom Balbridge Framework also includes the concept of employee value whereby performance of the organization is determined by the competencies, skills and motivation of the staff. The firm is therefore expected to meet the needs of the workforce and take care of their welfare. The Motorola Company emphasizes on the importance of the workforce by working to attract and retain appropriate employees. These are later encouraged to commit to quality through supportive work environment. This is in addition to developing their capabilities coupled with mechanisms for recognizing, rewarding and supporting the workforce.
Measurement, Analysis, and Knowledge Management
This refers to the selection, collection and analysis of data and information for use by the organization. Organizational success is measured on the basis of the effectiveness of techniques used as well as their correspondence with current business needs and changes. The information is then used in decision making with the results of performance evaluation being integrated into the processes of the organization. Analysis in this case involves examination of trends, technological progress and relationships so as to identify the root causes and aid in resource allocation.
Process Management
This involves identifying the major capabilities of the organization, management design and key processes as well as work systems. The process is crucial in attaining the set goals for the firm with customer satisfaction being achieved as well. The core competencies in this case refer to its sectors of expertise that can be utilized to gain competitive advantage. Work systems on the other hand entail the activities of stakeholders such as suppliers and contractors that are organized in such a way that results are obtained. The elements of key processes include operations that call for the participation of a great proportion of the human resource.
Results
The component of results in this case encompasses outcomes in the areas of market, customer relationships, processes, leadership and human resource. For instance customer results are based on market segmentation and grouping of customers with comparison being made on satisfaction. Fro the financial market, various measurements are taken into account including profit margins, cash flow and liquidity as well as uses of assets (Herz, 2007:32). Workforce focus on the other hand involves an examination of trends including aspects such as job satisfaction, skill development and organizational commitment.
Quality management also encompasses error proofing to ensure that all activities and records are undertaken as per specific instructions by use of data gathered and mobile technology. In addition, the proofing entails scanning that is done before and after the process. This brings out any processes or steps that have been omitted so that deviations are rectified before they affect output. Moreover, inspection is part of the quality management process in Motorola. Inspection involves the examination of paperwork and processes to ensure that errors and points that are not productive are identified. The inspection is carried out by engineers and inspectors using technology to lower the chances for errors. This ensures efficiency in inspection and validation of work as information is transferred faster to guide all operations (Motorola Solutions Inc 2011).
Motorola also uses quarantine in quality management to separate materials and end products that are out of date or obsolete. Technology in manufacturing is utilized to bring out and get rid of quarantined material so that the process is completed using up-to-date equipment and facilities. This also serves to avoid cases of costs incurred in recalls as well as the likely negative effects on the brand image of the company. The company also ensures quality by tracing batches throughout the production process. Technology and technical systems are used to trace batches by use of serial identification numbers so that deviations from the target level of quality are easily recognized and rectified. More recently, a technique that utilizes serial numbers to trace all parts to be assembled tracks the components throughout the process to facilitate fast recalls in case they are necessary.
Application
A quality management framework is crucial to the organization as it aids in the creation and attainment of organizational goals and objectives with suitable parameters. Moreover, it is used to comprehend the business systems and their impact on relationships in the organization. It also brings out the likely risks coupled with the fact that it facilitates proper allocation of resources. Quality management is viewed as a strategy for success of an organization through the competitive advantage gained. It is a strategy as it constitutes objectives to be attained, underlying principles, and activities aimed at attaining the set goals. The convectional approach that based business strategies on financial and marketing departments of the organization was weakened by the fact that it neglected the aspect of competitive advantage. Quality is a suitable approach as it considers elements of competitive advantage in terms of differentiation and costs. The concept of quality facilitates effective management as its principles constitute the process of planning. It accentuates organizational performance by adding on sales, increasing capacity, and enhancing production resulting in success.
Competitive advantage implies that the firm’s products or services are regarded as superior to those of competitors indicated by motivation to meet customer needs that adds onto organizational success. This also means that the organization resources correspond to the chances in the setting of the company. Competitive advantage is further attained through the durability in terms of the quality as well as the opportunity created for improvement with direction for the organization. The advantage is gained through various elements of quality, including differentiation and cost leadership. The latter involves the creation of a view that the particular organization leads in low costs that are facilitated by enhanced productivity brought about by quality (Free-Books-Online 2010).
Quality management, for example, in manufacturing is focused on reducing defects from the initial stages of production to the shipment and distribution stages. Success is achieved through command over costs and price that is made possible by quality products so that competitors are compelled to lower their prices. An example of quality management framework is depicted in construction companies that implement quality management in the form of eight strategies. These are management of customers, people, suppliers, information, process, and leadership. Moreover, the companies’ quality management entails continuous enhancement with organizational learning as a vital element (Low & Koh 2010).
Six Sigma at Motorola
The Motorola Company utilizes the Six Sigma as a quality management framework. The Six Sigma developed by Motorola involves a process for problem solution with various stages. It was later adopted by General Electric (GE) under Jack Welsh. The process involved the DMAIC, referring to definition, measurement, analyses, improvement, and control. The definition stage entails recognizing customers and their requirements. The stage also sets boundaries for the project with a clear outline of the processes targeted for improvement. The measurement stage calls for the examination of performance, collection of data, and identification of defects as shown by the customer survey. During analysis, the technique compares standard and current performance and investigates the causes of the variation and ways of improving the situation. Subsequently, the improvement stage involves the utilization of obtained data to eliminate the root causes of the problem. The final stage that focuses on control is then undertaken. This encompasses monitoring the improvements achieved so that the end products are free from defects.
The company utilizes the Six Sigma quality in its objective of quality improvement and customer satisfaction. The technique involves a measure of variation from the expected outcome that is statistical in nature. This implies that the company aims at achieving no more than 3.4 defects for every million products, including customer care services. It also means that the company emphasizes on manufacturing designs that can handle variation and result in uniform end products. The Six Sigma is also based on the concept of critical to quality that focuses on qualities of the product that are valuable to the customer. In addition, capability to deliver quality in the process coupled with the aspect of defect ensures that customer needs are precisely met. Six Sigma also entails the concept of consistent operations so that the processes are constant and predictable to enhance customer view and response to the product. The design for Six Sigma as a component of six sigma implies that it is tailored to have processing capability and meet requirements as voiced by customers.
The Six Sigma implemented in Motorola resulted in the company saving more than $17 billion. This is in addition to a 20-percent rise in profits, with share prices increasing at a 21.3-percent rate annually between 1987 and 1997. This was attributed to the fact that the company was able to recognize the needs of customers, identify all areas likely to have defects, and evaluate the company performance against standards set by the Six Sigma methodology. This technique also outlined the steps required for the attainment of such standards to be followed by the company. The success of the company was also due to the fact that it facilitates the achievement of strategic objectives and optimizes variations in products and services to meet customer needs (Leong, Tan, & Wisner 2008).
Quality Management at Motorola
The quality improvement initiative involves the entire workforce whereby variations and defects in all functions are recorded with due regard to statistical technologies. Moreover, the initiative works to reduce the duration between order placement and delivery to customers. For instance, new products are handled with the least cycle time so that time is counted on conception of the idea to develop the new product. Thus, the cycle time aspects for quality improvement takes into account the entire system, including manufacture, design, and the process of marketing.
The company leads in quality management as indicated by managerial support aimed at evaluation of quality strategies, with feedback being distributed to the employees in the organization. Employees also participate through the Participative Management Program (PMP) that combines the efforts of staff given a particular task in a particular section of the organization. The PMP facilitates the consistent evaluation of progress made in pursuance of quality objectives, resolution of issues, and coming up with new projects for quality improvement. The company also uses a scheme generated from the PMP initiative to recognize quality work so savings that result from recommendations are distributed among team members. For instance, bonuses gained from the PMP initiative in the last four years are equal to 3 percent of the company’s payroll. Furthermore, quality management is facilitated by training and development of staff on principles and framework of quality. It is estimated that the years between 1983 and 1987 saw the company invest $170 million for training, with 40 percent of training being on quality improvement (NIST 2001). Quality management also entails benchmarking of quality of Motorola with that of other companies in terms of cost, performance, and design.
The conceptualization of the Six Sigma as a framework for quality management therefore includes various aspects. To start with, the need to meet customer needs is crucial as highlighted by the approach that the needs are recognized and assessed. Moreover, management in terms data gathered and its use in the process of decision making. The approach is also based on an analysis of the process that is monitored to ensure quality. The theory of Six Sigma also calls for the use of a management style that is proactive in nature that examines root causes of problems before they get out of control. The approach is also driven by cooperation and integration of efforts employees to establish teamwork. Lastly, the approach is based on motivation towards perfection to minimize the opportunity for defects in the process of production as well as the final product (Verma & Boyer 2009).
Six Sigma Quality Management
Benefits
An organization that implements the Six Sigma approach benefits from the advantages it brings about even if it also deals with various challenges that come with the approach. The benefits are observed in the financial, operational, and organizational sectors of the company. Financially, the approach facilitates risk management and results in increased profits and output. It also leads to increased revenue and high returns on investment. At the organizational level, benefits include greater customer satisfaction, better image, and improved competitiveness. The approach also enhances the process of business in the organization by aiding in the use of statistical tools in management. Moreover, the company gains from the results of applying the approach to particular projects such as improved communication and strategy and bottom-line results. On the basis of operation, benefits arise from reduced tasks and termination of procedures that add little value to the production process.
The benefits of the approach are also seen as functional, convenience, and psychological benefits. The psychological gains are attributed to perceptions regarding the product such as prestige. The convenience benefits of the approach are associated with the ease of correcting defects in the product and avails it to the customer. The functional benefits come about as a result of the capacity of the product to meet customer specifications in terms of being reliable and durable besides being scarce in supply in its market. Furthermore, the approach has the impact of reducing design changes and the cost of the production cycle. It also outlines a framework for use in project management and the time taken to deliver products to the market. It also saves the organization costs incurred after sale service or support necessitated by low quality products (Launsby & Brue 2003).
The continual improvement element of the Six Sigma approach ensures that the organization constantly seeks to attain perfection in its operations. Another benefit of the perspective is seen in the fact that it necessitates training so that it is mandatory to all staff. This is done through the Six Sigma Quality Control Program that affects the entire production process. Six Sigma also facilitates organizational change as members are familiar with the constant motivation towards improvement. Change is thus inevitable as problems are identified and solutions put forward on subsequent action. It therefore serves to prevent resistance to change in cases wherein the organization seeks to make fundamental changes. Other intangible benefits of the Six Sigma come in the form of increased accountability among the workforce as well as effectiveness that maximizes performance. Generally, the benefits of implementing the approach in an organization are associated with quality, customer satisfaction, savings, and time.
Problems
Organizations that implement the Six Sigma approach are also likely to encounter various challenges in its use. The implementation of Six Sigma requires commitment to the process by the organization because lack of dedication can affect the implementation process. It also calls for adjustment of various organizational norms and functions such as the use of time that has to be adjusted. Moreover, the implementation necessitates the assignment of metrics to all business processes in the organization. The company needs to undertake an analysis of all functions to allocate them quantitative values for the approach to be implemented which brings about problems to the team responsible.
The approach has also been viewed by critics as a methodology that counters innovation and creativity due to inflexibility. The rigidity is as a result of the tools used in the implementation process that focus on reduction of variants from the expected. The lack of support for innovation is attributed to the fact that it fails to create new business models that allow for growth. Moreover, its implementation entails skill that makes it difficult to achieve staff commitment and control during the process of implementation. Another weakness of the approach is that it requires an environment for scientific techniques to be applied as six sigma black belts are required in implementation. The approach also creates new positions in the organization that is why changes are experienced in terms of leadership and commitment. Six Sigma has also been associated with models that counteract with organizational objectives and oversimplify the situation in the real world. The model is also viewed as incomprehensive, with a need for clear understanding prior to its application in the organization (Neely & Jarrar n.d.).
Conclusion
From the research, it is apparent that quality management is a fundamental aspect of the organization. Quality has been defined in terms of durability, safety, and reliability among other attributes. It has also been noted that quality management takes into account various decisions, plans, and designs in a bid to meet customer requirements. Moreover, it has been found that quality management impacts on performance of an organization by influencing profits, market share, and customer satisfaction. It has further been established that quality is linked with the success of the organization as it determines creation of competitive advantage and suitable products that are free from defects. It is also evident that the Motorola Company as the pioneer in the Six Sigma approach to quality management has benefited greatly from its use. This is attributed to quality that has earned the company increased sales and greater market share. It applies the various concepts in the frame work to achieve organizational success. It has also been observed that the application of the six sigma approach in quality management results in various benefits and challenges as well.
List of References
ABEF (n.d.) Australian Business Excellence Framework (ABEF) [online] available from
[30 March 2011]
American Society for Quality. (n.d). The History of Quality - Overview. Retrieved March 31, 2011, from http://asq.org/learn-about-quality/history-of-quality/overview/overview.html
Armstrong, M. (2006) A handbook of management techniques: a comprehensive guide to
achieving. London: Kogan Page Publishers
Baškarada, S. (2009). IQM-CMM: Information Quality Management Capability Maturity Model. Wiesbaden: Vieweg +Teubner.
Evans, J. R. (2007) Quality And Performance Excellence: Management, Organization, And
Strategy. London: Cengage Learning
Free-Books-Online (2010) Total Quality Management And Global Competitive
Advantage [online] available from [28 February 2011]
Hertz, H. S. (2007). Criteria for Performance Excellence. Retrieved April 6, 2011, from http://www.nist.gov/baldrige/publications/archive/upload/2007_Business_Nonprofit_Criteria.pdf
ISO. (2011). ISO 9000 essentials [online] available from
[29 March 2011]
Launsby, R. G. and Brue, G. (2003) Design for Six Sigma. London: McGraw-Hill Professional
Leong, G. K., Tan, K.-C., and Wisner, J. D. (2008) Principles of Supply Chain Management.
London: Cengage Learning
Low, S. P. and Koh, T. Y. (2010) ‘Empiricist Framework for TQM Implementation in
Construction Companies.’ Journal of Managemt in Engineering 26, (3) 133-143
Motorola Solutions Inc. (2011) Quality Management Solutions for Manufacturing [online]
available from [1 March 2011]
Neely, A. and Jarrar, Y. (n.d.) Six Sigma – Friend or Foe? [online] available from
[1 March 2011]
Porter, L. J., Tanner, S. J., & Centre-for-Business-Excellence, E. (2004). Assessing business excellence: a guide to business excellence and self ... London: Butterworth-Heinemann.
Verma, R. and Boyer, K. K. (2009) Operations and Supply Chain Management for the 21st
Century. London: Cengage Learnin
Author's bio:
The author is associated with the www.urgentdissertations.com and he can help you with research papers,term papers,dissertations,thesis,course work
Add Comment
Education Articles
1. Tested Tutor Reading Comprehension In Wellington: Enhancing Literacy Skills For Lifelong LearningAuthor: khizar haider
2. Studyauracle
Author: Studyauracle
3. 10 Digital Marketing Tools You Must Use In 2025
Author: neetu
4. School Tutor Website In Palm Beach
Author: khizar haider
5. Studying Mbbs Abroad Is A Way To Successful Mbbs Career
Author: Mbbs Blog
6. Join Microsoft Dynamics 365 Courses – Online Training
Author: Pravin
7. Gcp Cloud Data Engineer Training | India
Author: naveen
8. Generative Ai For Devops Training Classes | Visualpath
Author: Visualpath
9. Best Az-305 | Azure Solutions Architect Expert Training
Author: gollakalyan
10. Tomorrow Starts With A Healthy Today
Author: Akshaya Patra
11. Gen Ai Training In Hyderabad | Best Generative Ai Training
Author: Susheel
12. Top Sap Ariba Training Institutes | Sap Ariba Training In Bangalore
Author: krishna
13. Safety & Health At Work - Qqi Level 5 Qualification
Author: johnnytorrt
14. School Tutor Website In Boynton Beach
Author: khizar haider
15. How To Become A Special Needs Tutor In Jacksonville
Author: khizar haider