ALL >> Education >> View Article
An Effective Laboratory
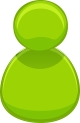
An Effective Laboratory
Laboratory Non-Conformances
Introduction
A non-conformance refers to a deviation from the expected quality characteristic that result in a product or service insufficiency in terms of meeting certain requirements. In the laboratory, the non-conformances can occur in technical operations as well as management processes. These are recorded in the laboratory corrective action form to facilitate the initiation of corrective measures. In this case, the corrective action entails cause analysis and remedial action. The remedial action is the immediate response to the problem while the cause analysis looks into the underlying issue as it is an indication of a greater problem in the system. Preventive action on the other hand involves two major activities [NHS 8, pp. 1]. These are assessment of risk that is usually undertaken during the adoption of a new process or on the occurrence of a change. Continuous enhancement also contributes to the preventive action through a process that recognizes ...
... and targets improvements in the system. It also aids in alleviating the situation by identifying the origin of the non-conformances. The objective of this research is to examine laboratory procedures for non-conformances in areas of management processes and technical operations and undertake a root cause analysis of the problems suing the Fishbone diagram and 5Whys approach.
Technical Operations
Non-conformances in technical operations can be attributed to various aspects in the context of a laboratory. One of the major problems in the technical operations is instrument and equipment problems in the area of calibration. This entails the comparison between the instrument results and the expected standards [National Instruments Summit 6, pp. 1]. This is a fundamental issue in the laboratory as it determines the results of laboratory tests and subsequent processes as well as the quality of results that impact on the health of a patient. The instrument problem needs to be investigated and corrected as it is likely to compromise the quality of treatment offered to patients due to instruments that deliver wrong results.
Problem Identification
The problem in this area is evidently the calibration of instruments in the laboratory. A root cause analysis is hereby important to aid in identifying the major cause of the problem as an essential tool for bringing out relevant corrective and preventive measures to avoid it recurrence and correct it [Bromilow & Daniels 5, pp. 34]. Using the 5whys approach, the root cause analysis indicates that instrument problems in the laboratory are caused by various factors as it enquires on the causes of the problem. The root cause analysis using the method indicates that instrument problems are caused by the major underlying issue of power quality in the laboratory. Moreover, the analysis shows that the equipment utilized in the laboratory heavily relies on electricity for operation [Mulm 3, pp. 1]. This is further compounded by the fact that the instruments are easily destroyed by power interruptions as well as other malfunctions in the power line systems. The 5whys approach also attributes the power problems to a deeper significant issue of voltage imbalances in electricity supply. Finally, the problem is attributed to procedures involved in the installation of equipment that fails to take measures to test and calibrate instruments.
Corrective Action
The immediate response to the problem is the remedial action that in this case will involve the calibration of instruments with immediate effect. The corrective action will thus involve an overhaul of the procedures coupled with training to ensure that calibration is done appropriately. This should also include steps aimed at complete power protection of the laboratory. This can be facilitated by the installation of equipment such as voltage regulators and power line filters. The poor power quality issue that results in instruments problems will be eliminated by the voltage regulators as power supply will be maintained to the levels required by the equipment. In addition, the power line filter will work to shield laboratory technical operations from the effects of protection from noise and interruption. The implementation two devices is thus an important corrective action in dealing with the technical operation problem.
Management Process
Management processes in this case refer to activities undertaken by personnel to allow for the smooth running of laboratory procedures. Non-conformances in management processes are associated with various areas include in the running of the laboratory. These are indicated by results from management reviews and audits as well as monitory of routine activities in the laboratory. In this context, staff training is a crucial requirement and entails education on the use and care of equipment used in the laboratory [Bromilow & Daniels 5, pp. 34]. A root cause analysis is therefore essential to identify the underlying problems.
Problem Identification
The laboratory needs trained personnel to run its activities and avoid errors in procedure. However in this case, the level of qualification for laboratory staff has been found to be below the required standards. Management is thus expected to investigate the underlying causes of the problem and give the appropriate corrective action for alleviating the situation. A root cause analysis undertaken using the fishbone diagram reveals various causes of the problem that are crucial for its resolution. The fishbone diagram breaks down the causes of poor training in laboratory personnel into various categories based on the condition of the organization, work and resources [Bromilow & Daniels 5, pp. 34].
Fishbone Diagram Template
The analysis reveals that the personnel in the laboratory lack the essential skills due to irregular training sessions for staff. It also indicates that organizational factors contribute to the problem in terms of management role of tracking and maintaining training information for staff. In addition, the laboratory lacks sufficient equipment to train all personnel in the various procedures that are performed in the area. This is further compounded by the fact that the department lacks financial resources to fund training of staff on a regular basis or on the introduction of new procedures or equipment. Low levels of qualification for laboratory have also been brought about by the poor systems of human resource management and performance management in the organization. Finally, the fishbone diagram identifies poor communication as a cause of training deficits in the laboratory. This has eventually translated into the underlying causes such as poor leadership and administration in terms of training records and monitory [PIBS 9, pp. 6].
Fishbone Diagram Template
Corrective Action
To avoid recurrence in the future, various measures need to be put in place as corrective actions. For instance, to address the training problem on the basis of staff training records, the laboratory should develop a new and more elaborate system for monitory individual training progress and regular update. Furthermore, the administration is expected to allocate resources for staff training on the use of the different equipment and tools by prioritizing it accordingly [Bromilow & Daniels 5, pp. 34]. The situation can be further alleviated through an enhancement of recruitment and training procedures overseen by the human resource department. The communication issue as a cause of poor training can also be reversed through implementation of more elaborate methods of interaction among subordinates and leaders. Moreover, training can be aided through improved methods of leadership that ensure administrative practices in the organization focus on the needs of its personnel. Finally, proper training for staff is a long-term corrective measure in this situation [Bromilow & Daniels 5, pp. 34].
Importance of Non-Conformance Investigation and ISO 15189 Standards
Non-conformance investigations are a crucial part of laboratory operations due to the fact that they reflect the underlying sources of problems in addition to the appropriate measures to correct them. Moreover, a look into the non-conformances aids in improvement and quality through the recommended corrective actions that seeks to alleviate the issue. The exercise is also important in that it comes up with the best methods of dealing with a situation and preventing its recurrence. The corrective action identified is also keen to meet the requirements of the problem using an approach that is proactive or reactive [Russell 2, pp. 8]. This is in addition to developing methods of evaluating the solutions implemented on the basis of their effectiveness in solving the problem. The investigations are also fundamental to the organization as a whole as they focus on sustainability of established solutions as well as their effects on the persons applying them such as laboratory staff.
The ISO 15189 comprises of standards expected internationally for medical laboratories in terms of competence and quality. The standards are based on the ISO 9000:2000 and ISO/IEC 17025:1999 as it is an accreditation standard that allows individuals or groups to undertake particular tasks. The accreditation standard recognizes that laboratories need to provide results accurately and at the required time. In addition, the medical laboratories are expected to conduct their operations discretely and ensure patient safety as well as interpret results properly [Cooper 4, pp. 2].
In dealing with non-conformances, the standards clearly state requirements for management systems and processes. To begin with, problem solving practices are expected to take a participatory approach. This means that employee’s engagement is required through roles assigned to staff. To add to that, reports and impact of non-conformances should be explained and forwarded to the clinician responsible. The standards further require that once the non-conformances are identified, corrective action should be initiated. Continuation of investigation on the non-conformances is only carried out after the approval of responsible authority. The laboratory is also expected to record and report non-conformances to facilitate regular assessment by management. This is important in aiding the organization of hospital to detect and correct the situation to avoid further deterioration [Noble 7, pp. 1].
Non-conformances are also regulated by the ISO 15189 standards under the clause referred to as continual improvement [Noble 7, pp. 1]. The clause focuses on proper delivery and provision of services coupled with user or patient satisfaction. Competence of the laboratory is assessed in terms of ability to carry out tests on human samples with adherence to the various classes and sub-classes defined in the scope of accreditation. Moreover, the standards focus on hospital management systems whereby the laboratory is evaluated for effectiveness [A2LA 1, pp. 2]. These are examined in areas of pre-analysis, analysis and post-analysis. The standards also seek to alleviate non-conformances by examining laboratory procedures utilized in the detection, prevention and control of the non0conformances. The standards also outlines requirements for quality testing and service s as well as the management system in its entirety to asses its effectiveness [Noble 7, pp. 1].
Conclusion
From the study, it is apparent that management processes encounter issues such as lack of training while technical operations face instrument problems. The root cause analysis has established that the instrument problems are as a result of calibration as well as poor power quality that have been caused by other underlying issues. In addition, the study has found that poor training as a management problem is as a result of organizational and administrative factors. The study has also indicated that non-conformance standards are important in the maintenance of quality and delivery of services. It has also found that the ISO 15189 standards seek to address the non-conformances through assessment done on a regular basis.
Reference List
1. A2LA. R3R305 – General Requirements: Accreditation of ISO 15189 Medical Testing Laboratories. Available from: www.a2la.org/requirements/15189_General_Requirements.pdf, 2008.
2. D Russell. Five Why’s Root Cause Analysis with Fishbone Diagram. 2008. Available from: http://www.daivrussell.com/Fishboning.pdf, 2008.
3. D Mulm. Poor Power Quality in the Laboratory : A major source of instrument operating problmes. American Clinical Laboratory (1995): 1-4.
4. G Cooper. Seeking Laboratory Accreditation Under ISO 15189. Available from: http://qcnet.com/Portals/0/PDFs/ISO15189Booklet.pdf, 2009.
5. I Bromilow and D Geoff. Essential Guide to Blood Groups. London: John Wiley and Sons, 2010.
6. National Instruments Summit. Calibration Basics. Available from: , 2011.
7. M Noble. Michael Noble MD FRCPC UBC Program Office for Laboratory Quality Management. Available from: http://www.polqm.ca/powerpoint/rt_lqm_2_quality_partnerships_and_standards_development.ppt, 2010.
8. NHS. Q 36 - Corrective and preventive action.. Available from: www.hpa-standardmethods.org.uk/documents/qsop/pdf/qsop36, 2007.
9. PIBS. Operating Authority Accreditation: How to Respond to Audit Findings. Available from: http://www.ontario.ca/drinkingwater/dw_el_prd_044946.pdf, 2011.
Author's bio:
The author is associated with the www.urgentdissertations.com and he can help you with research papers,term papers,dissertations,thesis,course work
Add Comment
Education Articles
1. Devops: The Modern Skillset Every Tech Professional Should MasterAuthor: safarisprz01
2. Salesforce Marketing Cloud Training In India | Cloud
Author: Visualpath
3. How An English Medium School Shapes A Child’s Future In Today’s Global World
Author: Mount Litera Zee School
4. Mern Stack Online Training In Ameerpet | Mern Stack Ai Training
Author: Hari
5. Why Online Courses In Sap Sd Are The Best Solution For Today's Professionals
Author: ezylern
6. Sailpoint Online Course In Bangalore For Professionals
Author: Pravin
7. Sap Ai Course | Sap Ai Online Training In Hyderabad
Author: gollakalyan
8. Why Aima Is The Best Choice For A Global Advanced Management Programme
Author: Aima Courses
9. The Best Oracle Integration Cloud Online Training
Author: naveen
10. Mlops Training Course In Chennai | Mlops Training
Author: visualpath
11. International Cbse School In Nallagandla,
Author: Johnwick
12. Best Mba Dual Specialization Combinations For 2025 And Beyond
Author: IIBMS Institute
13. Top Docker Kubernetes Training In Hyderabad | Docker And Kubernetestop Docker Kubernetes Training In Hyderabad | Docker And Kubernetes
Author: krishna
14. Full Stack Web Development Course In Noida
Author: Training Basket
15. Master Advanced Pega Skills With Pega Cssa Infinity'24.2 Online Training By Pegagang
Author: PegaGang