ALL >> Education >> View Article
Finite Element Analysis Project
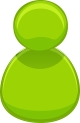
Finite Element Analysis Project
Finite Element Analysis (FEA) is a method used in engineering in order to find solutions to complex problems by replacing them with simpler ones. In solving the simpler problem, an approximation of the solution of the original complicated problem is obtained. In order to get an analysis of the response of a complex structure when subjected to an external force, the structure is divided into several different parts called finite elements and an approximate solution to each finite element is worked out. The behavior of the overall structure is then derived. Finite element method is mostly used in structural mechanics in analyzing the stress, elasticity and displacement of different geometrical shapes when subjected to a load. However, the method has also been applicable in heat flow, viscosity, and magnetic and electric fields. Companies carry out simulations of the behavior of new designs of products when subjected to stress in before launching them into the market in order to ensure that specifications of the consumers and market requirements are met. In this way, the firms are able to ...
... manufacture only the products that will perform as required and therefore avoid unnecessary costs and time wastage. This is made possible by using FEM (Rao, 2005).
FEA models involve mapping the design with a system of points called nodes which make a mesh. The material properties assigned to the different parts of the mesh in order to determine the behavior of the model as a whole when subjected to different loads. These properties or variables include temperature, mass, acceleration, elasticity, load and displacement. Of consideration is the fact that loading can be done under different conditions, such as pressure, gravity, etc. different elements of solids may be analyzed using FEM. Examples include two dimensional elements such as
- Rod, beam and plate
- Shear panel
Three dimensional elements such as
- Solid elements
- Rigid elements
Other elements include spring elements, mass elements and damping elements.
Basically, there are two main types of finite element analysis, i.e. Structural analysis and vibrational analysis. Structural analysis involves models fall in to categories
i) The linear model
In this model it is assumed that the material is loaded within its elastic limit. This implies that the material regains its original length and shape after it is unloaded and hence no permanent deformation occurs.
ii) The non-linear model
In this model, the material is assumed to be compressed beyond its elastic limit and the deformation is therefore permanent, even after the load is removed.
In vibrational analysis, the response of the material is analyzed on impact or irregular vibration and collision. This is especially important in structures which may fail due to resonance arising from vibrations which correspond to the natural frequency of the material.
Other FEM applications include analysis of heat flow models and fatigue analysis models which are used to estimate the expected life of a component in automotives and aeronautics (Zienkiewicz and Taylor, 2000).
Background
Finite element methods have been in use since ancient times, though the Finite Element Method (FEM) terminology gained universal usage only recently. Mathematicians used this method in finding the circumference of a circle by taking the circle to be a polygon with many sides and approximating the circumference by calculating the perimeter of the polygon. Modern FEA was first formulated by Courant in the mid-twentieth century when he used calculus to find estimates of solutions to wave systems. Later, FEM was exclusively applied using computers. Currently, the advancement in information technology and computation power of the current generation computers has made it possible for FEM to be utilized to yield very accurate solutions to complex engineering problems. Most FEA problems involving linear elasticity and stress/strain relationships are relatively easier to solve. However, for practical applications, material behaviors are rarely linear. They involve elements of non-linearity, both in geometrical and material aspects. In materials that are perfectly elastic, the behavior of the material when loading is the same as in unloading. On loading, the material stretches linearly; i.e. F = kx, where F is the load, x is the displacement and k is the constant of proportionality. On unloading, the relationship remains true and the original length and shape of the material is restored. An illustration of this situation is the loading and unloading of a perfectly elastic spring. In such a case, the FEA is linear and the displacement and stress/strain analysis is linear. This is however not always the case. Some materials exhibit plastic elasticity in which the original length and shape of the material are not restored after unloading the material. In such a case, non-linear finite element analysis is required, a method that takes into consideration the non-linear qualities of the material.
Discretization is the process of subdividing a body into several discrete parts (finite elements) in order to make it possible to analyze of each finite element and draw an overall behavior of the system or body. Discretization may involve partitioning the body into 1-dimensional, 2-dimensional or 3-dimensional elements. Generally, the body is first divided into a number of finite elements in the processes known as meshing. This makes it possible to consider each part (finite element) as a distinct component. The shape of the finite element depends on the shape of the body and the orientation and aspects of the load among other factors (Zienkiewicz and Taylor, 2000).
Technical Approach
When a material is acted on by a force, which is often referred as load, it may respond in several different ways. The material may have a fracture, the material may stretch, it may change its shape depending on its elasticity, or it may fracture. This is especially so in brittle materials because they do not deform under stress but instead fracture or crack. The behavior of a material when subjected to a load is dependent on the properties of the material, the geometrical shape, the load and the forces that exist between its atoms. Theoretically, the strength of a material is about a tenth of its elastic modulus. In practice, however, the strength of a material is found to be much lower than a tenth of its elastic modulus. This has been explained by the presence of cracks and flaws on the surface and in the core of the material. Ductile materials are however able dto deform plastically, thereby avoiding to crack or fracture. It is very important that the strength of a material design be calculated during the design of machinery parts and other components because when a material is loaded beyond its strength then the material fractures. One important factor which cannot be ignored when considering fracturing in ductile and brittle materials is temperature. As the temperature of the material goes up, the fracture becomes more ductile. Conversely, as the temperature of a material is lowered, the fractures become more brittle. Ductility is dependent on temperature. This phenomenon can be explained by the fact that aat higher temperatures, the atoms in a material vibrate with a greater amplitude and are therefore able to get greater displacements when the material is under stress. At low temperatures, the atoms vibrate with shorter amplitude. This limits their displacement when the material is under stress and consequently leads to fracture when the material is subjected to a load that exceeds its yielding point. It follows that no material can be said to be perfectly ductile of brittle at ordinary temperatures as this all depends on the temperature range. At ordinary temperatures, any material possesses both ductile characteristics as well as brittle ones (Zienkiewicz and Taylor, 2000).
The Model
The mesh of the FEA model to be analyzed is the beam shown in the figure below.
The variables that are believed to affect the response of the design within each element in the mesh are traced. In analyzing the stress resulting from the load in the design, the beam will be treated as a geometrically symmetrical 3-dimensional structure and will be treated as consisting of several layers of the material. This will make the analysis easier as it can be a simplified to a 2-dimensional design. It will also be assumed that the atoms in the material which make up the finite elements are not under any stress or strain and that are at zero displacement before the application of the load. The beam design will be analyzed using a totally elastic material model. The properties of the material are tabulated below:
Young’s modulus = 150,000 psi
Poisson’s ratio = 0.30
The beam has a length of 0.30 inches and is 0.03 inches wide. The geometry of the beam is as shown in the figure below. Since the beam has a uniform cross section, it is considered to consist of six layers of 0.010 inches thickness. The mesh contains 1,044 elements and 1,560 nodes. For simplification of the task of expressing the displacements, the beam is oriented with the X-Y- Z coordinate such that the length of the beam is along the X axis; the width of the beam is along the Y axis and the thickness of the layers of the model lie along the Z axis.
The dimensions of the design are shown in the figure below.
The figure above shows the finite element mesh consisting of six layers used to model the beam. The right hand coordinate system is used to align the elements such that the thickness of the layers is along the Z axis.
The diagram below shows the displacement of the nodes along the length of the beam.
The dimensions of the designs are as shown in the figure above. When the tensile forces are applied as shown in the diagram, it is assumed that the crack or fracture will occur at the region between the two notches. This means that the crack will be perpendicular to the axis of the load or tensile force. The maximum stress is approximated by using the following equation:
Where the magnitude of the tensile load σ0, the radius of the curvature is ρ and α is the length of the curvature. To determine the stress concentration factor, the following formula is used:
Stress is usually concentrated in a material at regions where there are fissures, cracks and notches at the either on the surface of the material or internally at the core of the material. At the macroscopic level, stress is concentrated at regions of sharp bends, around bends and notches and around hollow parts.
Results
The stress analysis of the models using FEM in this project shows the points of maximum stress. These are the points at which fractures are most likely to take place. It is evident that the distribution of stress depends on the shape of the structure. On subjecting a structure to a load- either a compression or tension, the force is distributed throughout the body. Stress, however, is not distributed uniformly. Regions with sharp bends or around holes have a higher concentration of stress. At the particle level, cracks and notches on the surface of the material increase stress at these regions and if the load exceeds the yielding point of the material, then two things may happen:
i) The material may fracture at this point,
ii) The material may stretch elastically and regain its original shape on unloading, or
iii) The material may become permanently deformed if the elastic limit is exceeded and the material is ductile enough at this temperature.
Discussion
Stress is analyzed using finite element analysis model by determining the distribution of the displacements and stresses of the elements under the given conditions. In order to obtain a feasible solution to the problem, the following relationships pertaining to solid mechanics must be ensured to hold true.
The number of equations must be equal to the number of unknown quantities in order for the system of equations to be soluble.
The solutions to these sets of equations are always in the form:
Ku = f
Where K is a coefficient matrix, u is the load and f is the resulting stress in the material. In solving the problem using FEA, the initial problem is always of in the form:
Yn+1 = Y(un+1) = fn+1 – P(un+1)
Where un+1 is the set of parameters that determine the discretization, fn+1 and P are vectors. P is dependent on the parameters while fn+1 is independent. To arrive at a solution, an initial approximation of the solution is always the first step. This should always start at;
U = un, Y = 0, f = fn
Under the compression or load,
fn+1 = fn + Δfn+1
Δfn+1 is kept small and the number of iterations is kept relatively small. This is in order to make the increments easily traceable and to simplify the procedure.
Iterative techniques
The figure above shows the possibility of several sets of solutions to a problem using the finite element analysis method (Rao, 2005).
In a static body, the forces in a body must balance for the system to be in equilibrium. It therefore follows that if a load is applied to a body, the reactive forces in the body must balance with the load in order for the system to be in equilibrium. It follows that the following equations must be satisfied:
For isometric materials, the following stress and strain equations must hold true:
Where |C| is a matrix of coefficients of elasticity and is given by;
ε represents the strains before the deformation, E is the Young’s modulus and v is Poisson’s ratio (Rao, 2005).
The figure below shows a beam with a hole in the center and the corresponding mesh for the FEM model. The dimensions of the structure are shown and the coordinate system is used to orient the elements such that the length of the beam is along the X axis.
W is the width of the beam, h is the thickness, d is the diameter of the hole, h is the thickness of the beam and P is the load. After application of the force, FEA results show that the nodes are displaced that that they are concentrated more around the hole. This implies that the stresses are concentrated more around the hole too.
Conclusion
Finite element analysis is a method used in engineering to analyze and determine the behavior of materials when subjected to compression or tension. The method has also been applicable in heat flow, viscosity, and magnetic and electric fields. Companies carry out simulations of the behavior of new designs of products when subjected to stress in before launching them into the market in order to ensure that specifications of the consumers and market requirements are met. In this way, the firms are able to manufacture only the products that will perform as required and therefore avoid unnecessary costs and time wastage. This is made possible by using FEM.
Bibliography
Rao, Singiresu S., (2005). The finite Element Method in Engineering. USA: Elsevier Butterworth-Heinemenn.
Zienkiewicz, O. C. and Taylor, R. L., (2000). The Finite Element Method. USA: Burlington.
Author's bio:
The author is associated with the www.urgentdissertations.com and he can help you with research papers,term papers,dissertations,thesis,course work
Add Comment
Education Articles
1. Gavin Mccormack Journey As An Education ChangemakerAuthor: selinclub
2. What Makes Dubai An Ideal Destination For Global Business Conferences?
Author: All Conference Alert
3. D365 Functional Course In Ameerpet | Dynamics 365 Course
Author: Hari
4. Best Sre Certification Course | Sre Training Online In Bangalore
Author: krishna
5. Best Google Cloud Ai Training In Ameerpet | Visualpath
Author: visualpath
6. Azure Ai Engineer Course In Bangalore | Azure Ai Engineer
Author: gollakalyan
7. What To Expect At The Vermont Dmv Driving Test
Author: Ravinder Malik
8. Key Highlights Of Punyam Academy’s Iso 9001 Lead Auditor Training Course
Author: Emma
9. Ai With Aws Training | Ai With Aws Online Training Bangalore
Author: naveen
10. Salesforce Devops Training | Salesforce Devops With Copado
Author: himaram
11. How Does Cpr Affect High-risk Professions Like Healthcare, Sports, And More?
Author: Christopher Bayer
12. Best Bba Colleges In Hyderabad For Students Seeking A Corporate Career
Author: SSDC
13. Why We Charge A Training Fee At Pydun Technology
Author: Pydun Technology Private Limited
14. Informatica Idmc | Informatica Online Training In Hyderabad
Author: gollakalyan
15. Best Snowflake Course | Snowflake Training In India
Author: Pravin