ALL >> Education >> View Article
Quality Engineering Management
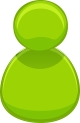
Quality Engineering Management
Introduction
In the world business history, quality management could be seen as the initial efforts toward attaining the success in industries, organizations, government bodies and private investments. Various gurus, in the western countries, especially Japan, had been observed contributing immensely on the issue of quality management in the present industries and organizations. These philosophers and business gurus believed that any success starts with management thus any quality needed in products, services and customers’ satisfaction starts with how best quality management is viewed. This had been achieved through various philosophies, plans and theories which to date proves to be the backbone of quality management in our present business activities.
Therefore this essay will trace the history of quality management, identifying some of the pronounced business gurus, their theories and plans and highlight how they have influenced the current quality management approach.
Body
Quality management in the past was perceived to influence every quality process in a ...
... business environment starting from inspection to the finished products. Based on the history of business gurus’ theories, challenges and experience, innovations have been made in the present management. In this respect, various processes and ideas have been developed in organizations as a reflection of quality management. Moreover, central business tools and theories have also been developed to help the development, management and production improvement geared towards both private and public sectors. The old perception of multi-stage quality management can also be seen in the present business settings aiming at quality products and customer satisfaction (The Original Quality Gurus).
In the past, there was famous and influential Japanese whose ideas could still be seen adopted in the current thinking on quality management (Chapman 2009). As argued being the first quality expert, he emphasized that no quality management can be feasible if employees are not empowered and shows much commitment towards attaining quality. In this idea, our present management focuses most on empowering their employees both financially and technically so that commitment level improves. In doing so, organizations meet their customer requirements. His further idea of quality management, to be made part of a person, has made the present managers adopt the positive ethical management approaches which always yield the best.
Chapman (2009) in early 1950, there were some Americans, like W Edwards Deming, who visited Japan with the issue of quality. In late fifties, Japanese responded to the American’s message of quality. However between1970 and 1980 western business gurus also adopted the Japanese achievements ideas. This chain of success can be seen even with the present quality management where organizations tend to imitate and borrow quality management ideas from successful colleagues in a consultative manner. Countries, continents also borrow quality management ideas from other developed worlds in order to achieve the best quality of management. Edwards really valued management and considered it responsible for over 90% of arising problems related to quality. Compared with present quality deviations, most organizations normally hold responsible the managers for any substandard quality. They are seen as the most responsible employees in seeing that the quality set by the organization or needed by customers is attained through their quality management approach (Adam 1975, p. 667).
Moreover, Edwards’s points can still be seen as source of quality management in the present business management. This business guru believed that this is the only way to enable management maintain her business standards (Chapman 2009). He suggested that for quality management to be realized, management should eliminate fears in her employees, institute on job training and supervision, eliminate interdepartmental barriers, stop acknowledging business based on price factors, independently get the problems in the organization system, and carry out intensive and extensive education and retraining programs. In conclusion, Edwards had a philosophy which up to date is embraced by the present quality managers who want to show quality in their responsibility; the philosophy of “we can no longer live with commonly accepted levels, delay mistakes and defective workmanship” (Chapman 2009). In this context, managers tend to think that the best way to perform is to make quick changes in case of incompetent workforce, slow processes and tend to be innovative in management rather than applying the accepted standards. Since his recommendations covered a variety of issues, the present management is split into levels depending on the skills and organizational needs (Atuahene-Gima, 2003, p. 360). This approach is linked with the Edwards idea that quality management is team work rather an individual tasks. In addition the old Japanese guru Shewhart developed the systematic criteria to problem solving arising in management. He recommended that quality managers need to plan on the need, do it, check that the plan works and finally act to rectify the unfavorable situations so that the net effect is quality management. This approach, PDCA , to date seems useful to managers and other business individuals whose problem solutions are featured with planning, simulation, evaluation and action which has made them meet much of the customers’ needs (Albright and Roth 1994).
Chapman (2009) Dr. Joseph M Juran invented the quality trilogy which represents quality management to consider quality in planning, control and improvement. He argues that good quality managers need to plan, improve and control their actions (Chapman 2009). So if this is connected with Shewhart’s systematic approach and Edwards’ team work ethics in quality management, it becomes obvious that in present management, various managers are being employed to deal with various tasks in planning, control, and improvement in order to achieve the best in management by avoiding conflict of issues. In addition, Juran valued customers as the most beneficiaries of quality in management. This idea is still the focus of present organizations which aims at satisfying the customers through quality management of customer needs. Juran’s ideas of goal setting and training among others, as in Edwards’s ideas, make even the present management set goals for the organizations and arrange training for her employees with the net aim of displaying quality in their management services. However, Dr. Kaoru Ishakawa’s ideas in quality have formed the base for human factor considerations in achieving quality management in an industry. His quality tools have influenced the present management to apply and avail some of his analytical tools in order to achieve the best in their management responsibility (The Original Quality Gurus).
Nevertheless, Philip B Crosby really valued the concept of “Quality is free” and “Zero Defect” He further considered conformity and prevention which, to date, influence managers to strive conform to the organizational requirements and customer requirements. In addition, his idea has influenced the present management to be innovative enough in preventing liabilities to the organizations. On the other hand, Tom Peter considered leadership in management as the backbone in quality achievements. Here, he suggested leaders in management team need to listen and teach values through facilitation processes. This can only be achieved by “MBWA ”Nowadays it can be seen that managers occasionally take a walk in the organization to comprehensively fulfill their quality management responsibility (The Original Quality Gurus).
Conclusion
The idea of quality management started way back in early nineties when business challenges were realized by old business gurus like W Edwards Deming, Shewhart, Dr. Joseph M Juran, Dr. Kaoru Ishakawa’s, Tom Peter and Philip B Crosby.
To solve the issues, which needed quality management, American gurus presented the matter to the Japanese business gurus who in turn developed theories, philosophies and approaches. Consequently, such kind approach has really influenced even the way current quality management is achieved; through consultations and borrowing of ideas, use of past theories, philosophies and approaches. Finally the basic idea behind quality management is all about customer satisfaction which can be achieved in team work rather as individual responsibility (The Original Quality Gurus).
QUESTION 2
Introduction
In the fields of manufacturing, service industries and other forms of business faculties, the main vision is to remain competitive in the market for future expansions. However, employees, right from management levels to the subordinate staffs, retire, resign, some mean and die but the organization still remains to deliver to their customers. In this context, customers would also like to get the expected quality of services or products and this in turn push the producers or manufacturers to ensure continuous production levels with consistent quality. These issues therefore push organizations to adopt the concept of knowledge Management and Six Sigma which have been in use since their inventions to provide tools and approaches to counteract the short comings facing organizations so that they live up to their vision. This essay will therefore discuss how Knowledge Management and Six Sigma can be used to improve quality and reduce waste in an organization by identifying some of the tools and processes involved.
Body
Six Sigma can be perceived as the structured and disciplined process and methodology aimed at improving the business systems and procedures by eliminating the possible defects by the use of statistical analytical tools (Stamatis 2004, p. 42). It can therefore be said that individuals can catch knowledge in business through Six Sigma by involvement in the various processes, methodology and tools provided by this approach. In the Six Sigma methodology, DMAIC , there is definition of opportunity, measurement of performance, analysis of the opportunity, Improvement of performance and finally control of performance (Stamatis 2004, p. 46). So if one is an employee of an organization with good business ethics, he would be in a position to catch the required business information. For instance, if he is involved in this system, he would be able to know how business opportunities are discovered and weigh them on the basis of their performance. In addition, he would know how to analyze and improve business activities in a controllable manner (Harry 1988, p. 74). On the other hand, one can easily catch business knowledge when the Six Sigma methodology is used with the business principle, DFSS , in designing a completely new business process (Harry 1988, p. 75). This would enable an individual to know in greater details about processes of new business. However since Six Sigma emphasize on ceaseless reviews and fine-tuning of business processes, individuals involved would be in better position to catch the relevant business knowledge through continuous and repeated learning.
Knowledge Management on the other hand is perceived as processes and objects which try to deal with human faculty, in the perspective of sharing of the personal knowledge to the rest of the colleagues or using the personal knowledge in achieving the best quality products or services for an organization (Sveiby 1990, p 43). It therefore follows that individuals would catch the business knowledge through KM by undergoing the organizational cultures of training workshops, ethical handing over on retirement, postures and use of available systems such as computers (Sveiby 1990, p. 41). When employees are trained on the organizational business processes, systems and procedures, they would also know the required knowledge in achieving business goals. Similarly, if the retired staffs can ethically hand over duties to the fresh staffs, the new staffs would be in a position to know the existing business knowledge in the organization. On the same note, interaction among employees themselves can enable others to catch the business knowledge from their more experienced counterparts (Debra 1988, p. 90). However at times, one can just observe what is going on organizational postures and processes to personally judge and know the necessary business knowledge. In this respect, individuals can catch some of business knowledge while already on the job by continuous repetition of the same instructions and processes every day (Sveiby 1990, p. 50). Consequently a point will be reached where he would be well equipped with the relevant business knowledge. However, some challenges which may face the organization can also serve as away of catching the business knowledge since employees would be there seeing and experiencing how the organization overcomes them (Sveiby, KE 1986, p. 43).
Since quality products or services is what make organizations remain competitive in the market, the concept of Knowledge management and Six Sigma have been adopted side by side to constructively improve quality and reduce waste in production process. The methodology, DMAIC, used by the Six Sigma provides a very strategic way of achieving quality with reduced resource wastage. This is achieved by its logical processes considered in the manufacturing or business process by the use of powerful statistical tools. To achieve this effectively, Knowledge Management is required to build a good social and communication ground so that whichever process involved in the opportunity definition, measurement of performance, analysis of the opportunity, improvement of performance and control of performance can be done with total faithfulness and commitment thus reducing waste which could be caused deliberately (Debra 1988, p. 64). Consequently the end result would be quality products (Birkett, 1995, p. 33).
On the other hand, Six Sigma provides means of minimizing the defects in the final product by reducing variations. It therefore means that an organization can adjust her factors of production, prior to allowable defect level of 3.4, in order to produce virtually Zero defect products. However, to achieve this, organizations need to focus on the highly competent and experienced employees who have the know-how in Six Sigma. The management should also create a friendly work environment which would motivate workers to deliberate with honest thus achieving best quality needed with limited deliberate wastage. Moreover the Six Sigma has managerial tools which help the organization to involve their managers to have hands on experience of quality management which can yield quality production. These powerful tools avail vibrant means of upgrading production processes, finished products and human factors in business processes. But since managers are also human beings found within the docket of Knowledge management, they need to be intellectually managed in order to achieve the best quality within a free atmosphere as required by Knowledge Management (Arthur, 1996, p. 21).
In addition, Six Sigma provides engineering capability. If this functionality is combined with innovations (creation of new ideas) provisions as encouraged with Knowledge Management, the end result would be quality products. The Six Sigma would greatly analyze, control and test the intellectual property exhibited by the employees of an organization so that when the idea is implemented, the result would quality with minimal waste. Similarly, creation of incentives to such innovations as the best way of managing the intellectual property (Knowledge) would eliminate meanness on information among such employees and from employee to the organization (Nonaka & Takauchi 1995, p. 53).
Various processes of the Six Sigma’s methodology and principles are associated with huge volumes of data and information in the production process or service delivery. Moreover these information and data may need to be shared among the departments of the organization (Bill 2000, p. 88). Therefore, the concept of Information Technology as seen in Knowledge Management must come in to ease collection, storage, processing and sharing of data and information. This would save production time and increase reliability, integrity and accuracy of the Six Sigma outputs thus yielding quality products. Similarly any wastage which could be associated with delays, inaccuracies and unreliability would also be eliminated (Hiroyuki 1987, p. 42). However, since every process in achieving quality products with minimal wastage involves human beings, the concept of Knowledge Management must again come into play to avoid liabilities which may occur due to either internal or external forces (Bill 2000, p. 81). Consequently in the future, organizations which have adopted these two business approaches would completely change even the way they train their work force and conduct their business process (Sveiby 1989, p. 79). In addition, these approaches would ensure that organizations maintain the required competent workforce and information on quality products thus meet their customer needs with more revenues and minimal resource wastage (Weiig 1990, p. 36)
Conclusion
Six Sigma and Knowledge management complements one another in a successful business process. This is because while Six Sigma provides technical and logical statistical methodologies and principles, Knowledge Management provides how to deal with human faculty and IT , involved in implementing them, to ensure that the expected results are obtained in a less wastage manner.
QUESTION 3
Introduction
In most engineering industries, parts for production are commonly outsourced from other industries specializing in their manufacture and the final products need to meet the customer requirements in terms of their operating environment, maintenance cost, usability, safety, effectiveness and lifespan. In order for an industry to achieve this, it is logical to involve the engineering approach in the procurement of parts needed. Consequently industries adopt the use of Reliability and Maintainability case in the process of parts procurement.
This essay would therefore discuss and analyze the advantages and disadvantages of introducing the idea of R&M to the supplier of car parts in accordance with the case study about the process.
Body
Reliability and maintainability, as the name suggests, is one of systems engineering approaches that ensures that the final product meets the requirements of the users. This is achieved through the use of specially designed and predictive software like Isograph software, Hazop+, ReliaSoft BlockSim, RAM Commander, RMAT and ITEM ToolKit When this approach was introduced to the supplier of car parts, many benefits could be noticed on both sides of the car company and the supplier. To start with, this idea would contribute on the quality of cars manufactured and reduce liabilities resulting from customer rejections. This is due to progressive assessments and rigorous improvements of the processes involved during the supply right from the R&M requirement stage to actual supply (Ministry of Defense 1999, p. 6). It simply means that no substandard part would be supplied. In this respect, the car industry would develop a strong business trust in the supplier since the process of R&M absolutely involves full time collaboration between the supplier and the industry.
In R&M car part description, the supplier would be able to deeply understand the physical features of the parts to be supplied and its physical boundaries rather than making assumptions from their previous makes or designs. As a result, it becomes important since the car industry could have made some changes in their design which in turn dictates the supplier to change design (Ministry of Defense 1999, p. 8). Since R&M case provides the supplier with much information about the related issues on the parts needed such as parts’ usage, operating environment, scalability, built standards, operator skills and maintenance considerations, the part supplier would be able to deliver according to the requirements and this would save the industry on costs related to personnel and future expansions.
In the R& M case, the supplier would provide ways on how to meet the requirements provided by the car industry. This would allow for prior adjustments in their design so that any variation can be rectified before the delivery. However, the supplier may experience some risks associated with his efforts in meeting the R&M case requirements. These risks, to the car industry, build more assurance that they have a potential and reliable supplier judged from the supplier’s new strategies and robust philosophies in meeting the parts requirements.
According to Ministry of Defense (1999, p. 9) if the supplier has worn the bid, the R&M case would require that all evidence and claims are availed. Moreover the idea would allow for reasoned claims and assumptions on the supplier which, in summary, restore confidence in the car industry. This is because anything or decision made would be in a live traceable record and it would also shows that the supplier’s R&M program meets the R&M requirements of the car industry. R&M case would also require the supplier to provide comprehensive evidence that their design would meet the parts’ standard needed and understand the risks involved. However should there be any change associated with the parts’ usage, requirements or difference between actual performance and design benchmarks, the R&M records would as well be updated. This would therefore mean that R&M case improves the reliability of the parts supplied.
In addition, the provision by the R&M case of personal dialog between the parts supplier and the car industry would yield much confidence to both of them and this would prevent future losses to either the supplier or the car industry. On the other hand, on understanding the requirements of the R&M, the supplier would be able to determine his target as this forms the benchmark for qualification of a supplier. During the process of part supply, the R&M provides for modifications in order to meet the R&M requirements of the car industry. This is initiated if the supply results do not conform to the R&M case requirements or the set success criteria thus eliminating the uncertainty concept on the parts supplied (Ministry of Defense 1999, p. 10).
Given that the R&M document would oscillate between the part supplier and the car industry, the supplier would feel part of the car industry and this would instill much commitment in him (Ministry of Defense 1999, p. 10). However once the supply contract is over, the supplier would retain one copy of R&M documentation. This document would help the parts company with references on challenges, risks and other processes which can then be used once again as the base for future improvements. On the other hand, the copy held by the car industry would help the industry improve in future parts procurement contracts. In addition it would be used to provide easy reference in case of arising problems with the supplied parts (Ministry of Defense 1999, p. 11).
In contrast, the R&M presents some disadvantages in its applications in the supply of car parts. First, it is an expensive approach. This could be justified by the expensive Reliability and Maintainability software needed for data analysis, data storage (database) and simulation purposes. This normally raise the cost of production which in turn makes the parts be expensive. Similarly, the produced cars would be costly that customers may not afford their prices. Secondly this idea of R&M is quite involving and time consuming. This is common in situation where the part supplier has not met the R&M requirements which then initiate several redesign processes. Unfortunately if the part supplier might not meet the R&M requirements it would be dropped having consumed much time and resources in design and redesigns activities.
Conclusion
R&M idea has proved to be the best engineering approach in the car industry since ensures that the manufactured cars are reliable and maintainable. It achieves this through the use of various assessment tools used in the R&M software. Consequently, it makes the produced cars be dependable since they would have high standards of safety, availability, effectiveness and low maintenance costs.
QUESTION 4
Introduction
The iPad is a tablet computer that is made and developed by Apple. The devise is commonly marketed as a platform for audiovisual communication. Its weight is about 1.5 pounds. The devise was released in April 2010 and the company sold about 3 million pieces in duration of 3 months. In this research, the reliability of iPad is of concern. Reliability can be described as an ability of a system or a devise to perform the anticipated functions under the given conditions through a specific period of time. This is often regarded as probability.
Body
The 5 Years iPad reliability plan
The main purpose of the iPad reliability plan is to distinguish and diagnose the problem that may arise in a period of coming five years. The plan is aimed at improving devise usability and also making it the best in the market. The plan will be implemented in five years which is anticipated that at the end of the period, there would be commendable improvements in the devise. There are few steps that will be followed in order to achieve the anticipated goal.
The steps would be:
• Trouble shooting the devise
• Tracking the problem
• Analyzing the problem and problem causes
• Diagnosing the problem
• Testing the devise.
Year 1
Trouble shooting the devise
The problem that is being planed for is not problems that are already in hands, they are problems that may arise when operating the devise and may hinder the functionability of the devise. Any problem that could be noted under the normal operating conditions would be referred to as a problem and would be tracked till the solution is found (Leemis, 1995, p. 72). Example, the delay in response can be a problem that may need a proper care and concern to avoid complications on the user side. There could be a number of reasons why the device can be slow, but there need each to be addressed individually.
The areas that will be looked upon to distinguish the reason why the devise is slow would include the memory and processing capability, the amount of input and output the devise can handle at a given time and also the duration the devise has been in use. This will need a number of devises to perform this task and would be operated at different conditions to enable a clear tracking of the problem.
Year 2
Tracking the problem
The problem would be tracked in order to know the exact cause and the origin of the problem. Designing the devise at a high standard is much easier than fixing the problem when the devise is already in the market. This will include calling for the users to report on any problem that will be noted in order to allow the engineers relate the problem with already found (Leemis, 1995, p. 89). The problem tracking will also help in distinguishing what parts of the devise may need a repair or change to alleviate the problem forever. This will be done on new and on the devises that are already sold to know whether is a developing problem in all devises or on few devises that are put to test.
Year 3
Analyzing the problem and problem causes
This is the phase that will give the engineers the actual cause of the problem and probable methods that can be used to diagnose the problem. In this phase too, the engineers will know how deep the problem is and also how it can affect the entire working system. This phase is helpful because it will be easy to know how the problem is affecting the devise and how its affects the market of the iPad in general.
The analyzing of the problem will entirely depend on different modes of approach including statistics, reliability and probability theories. Most of the techniques that are used in determination of the effectiveness of the devise are based in the reliability prediction. Among the things that can give a precise answer on the reliability of the product include the Weibull analysis thermal management, reliability testing as well as the accelerated life testing.
Most of the reliability testing is performed of specific projects and for their expenses and the varying degrees for their reliability techniques. Each technique fits a unique situation and that’s the reason why the reliability plan is effective and required for such specific system. In iPad, the reliability plan testing would take five years to ensure the best results are achieved and can be depended upon (Leemis, 1995, p. 79).
The probability that the devise will work will perform for a given period of time and the specified condition can be done as;
Where is the failure probability and t is is the duration of time or period of the implementation and is assumed to begin at time zero.
There are four key elements the reliability test definitions as derived from above equation (Nelson, 2004).
• The reliability is also regarded as a probability. This is a random phenomenon. This is not given an individual attention like the causes of failure, diagnosing the failure or the relationship between failures except the probability of failure to occur varies with time and the probability of failure to occur in future. The reliability function is concerned with meeting some specific needs.
• The second part of the reliability plan is the intended function. In general, this is intended to test without failure. Even when the system is working fully, there is a need to test whether the system is performing as it was intended. The system is charged against the system reliability as this is the criterion that will be used to test the reliability.
• The reliability will also apply to a specified period of time. In this regard, it means that the system will operate for some time without any failure detected and this should be (t).
The reliability will be restricted to perform under certain conditions. This is necessary because the system must be tested for certain conditions. Each device, whether having the same functions is individually tested under specified conditions (Nelson, 2004, p. 53).
Year 4
Diagnosing the problem
The diagnosis of the problem will entirely depend on several factors. This will require some tools to enable the engineers diagnose the problem fully. The tools are;
Design for reliability (DFR)
The failure modes and effects analysis (FMEA) is a procedure that is used in the product development and procedures. The process will be used in detecting the probable failures that may occur in the product. FMEA would be used as part detecting errors that may arise in the third phase of the product development. This is one of the tests that will be performed on the product and is purposely for detecting errors on the product and diagnosing the problem (Neubeck, 2004, p. 73).
The reliability design will first develop the model. It will use block diagrams and fault tree in order to provide graphical means of analyzing the data and evaluating the relationship between the different parts of the system that is being tested and needs to be diagnosed. The most important part of the iPad development and the reason why it’s a step ahead its competitors is the use of redundancy test. Diagnosing the problem will help in retaining the customer base the iPad already have (Neubeck, 2004, p. 55).
Year 5
Testing the devise
Testing the devise is the last thing that will be done in the fifth year to make sure that the devise is ready for the consumer usage (Leemis, 1995, p. 99). Testing the devise will help in knowing whether the problem has been fully solved. The devise will be tested under different conditions to allow any error that may not have been discovered to come out and help the engineers rework on the problem.
Conclusion
iPad reliability test will enable the device work more perfectly than its competitors in the market. The reliability test will help in understanding where the failure could come from and on the other hand how it can be diagnosed without affecting the functionability of the devise. For the duration of 5 years, starting from time zero, it would be easy to understand the failures and how to improve and develop the devise.
The error analysis and diagnosing is an important part of the procedure because it will help in avoiding any such problem to arise in future. The procedures that will be used to analyze the problem will determine whether the devise will need further troubleshooting or can work better without further diagnose.
List of References
Adam, E. Jr. (1975) Behavior modification in quality control. The Academy of Management Journal 18(4): 662-679.
Albright, T. and Roth. P. (1994) Managing quality through the quality loss function. Journal of Cost Management (Winter): 20-37
Arthur, B. "Increasing Returns and the New World of Business." Harvard Business Review, July-August 1996, 74(4), pp. 100-109.
Atuahene-Gima, K. (2003) The effects of centrifugal and centripetal forces on product development speed and quality: How does problem solving matter? The Academy of Management Journal 46(3): 359-373.
Bill, H. (2000) Beyond Knowledge Management: New Ways to Work and Learn. The Conference board, Oxford University press, New York
Birkett, B. "Knowledge Management," Chartered Accountants Journal of New Zealand, Feb 1995, 74(1), pp. 14-18.
Chapman, A. (2009) Quality Management History [Online]’available from’ . [December15, 2010]
Debra, A. (1988) Managing the Knowledge Asset in to the 21st Century: Focus on Research Consortia. Purdue University: Technology and Strategy Group, Indiana
Harry, M. J. (1988). The Nature of six sigma quality: Motorola University Press, Illinois
Hiroyuki, I. (1987) Mobilizing Invisible Assets. Harvard Business Press, London.
Leemis, L. (1995) Reliability: Probabilistic Models and Statistical Methods, 1995, Prentice-Hall, New Jersey
Ministry of Defense (1999) Directorate of Standardization. Kentigern House 65Brown Street
Nelson, B. (2004), Accelerated Testing - Statistical Models, Test Plans, and Data Analysis, John Wiley & Sons, New York,
Neubeck, K. (2004) "Practical Reliability Analysis", Prentice Hall, New Jersey
Nonaka, I. & Takauchi, H. (1995) The Knowledge Creating Company. Oxford University Press, New York
Stamatis, D. (2004) Six Sigma Fundamentals: A Complete Guide to the System, Methods, and Tools. New York: New York Productivity Press
Sveiby, KE (1986) The Knowhow Company. University of Stockholm PhD dissertation, Stockholm
Sveiby, KE (1990) Knowledge Management. University of Stockholm PhD dissertation, Stockholm
Sveiby, KE. (1989) The Invisible balance Sheet. University of Stockholm PhD dissertation, Stockholm
The Original Quality Gurus [Online] ‘available from’ . [December15,2010]
Weiig, K. (1990) Knowledge Management: An Introduction in Proceedings of IAKE Second Annual International Conference. Washington DC: International Association of Knowledge Engineers
Author's bio:
The author is associated with the www.urgentdissertations.com and he can help you with research papers,term papers,dissertations,thesis,course work
Add Comment
Education Articles
1. Anantrao Pawar College Of Engineering & Research (apcoer): A Premier Institution For Engineering Admissions And Postgraduate Degree Courses In PuneAuthor: EngineeringcollegesinPune
2. The Role Of Threat Intelligence In Proactive Cyber Defense
Author: dev
3. The Role Of Music, Art, And Drama In Early Childhood Education
Author: Kookaburra
4. Best Servicenow | Servicenow Course In Hyderabad
Author: krishna
5. Best Iics Online Training | Informatica In Hyderabad
Author: gollakalyan
6. Msu 34th Convocation
Author: viraj anand
7. User Experience Design: Merging Functionality With Visual Appeal
Author: Rajat Sancheti
8. Enroll Now Microsoft Dynamics Ax Training | Microsoft Ax Training
Author: Pravin
9. Small Business, Big Impact: Affordable Graphic Design For Marketing Growth
Author: Rajat Sancheti
10. Master React.js: The Ultimate Course For Front-end Developers
Author: Infocampus
11. Full Stack Developer Course: Your Gateway To A High-demand Career
Author: Infocampus
12. Empowering Underprivileged Children In India Through Quality Education By Vibha
Author: Vibha
13. लाखों कमाओ! Social Media Expert बनकर!
Author: Sandeep Bhansali
14. Can You Recommend Nail Art Designs For Short Nails?
Author: john
15. How Can A Person Get Funds Or Sponsorship To Study Abroad?
Author: john