ALL >> Education >> View Article
Importance Of Safety And Health Training In Petroleum Sector
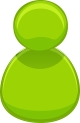
Occupational safety and health training is an essential aspect in workplace hazard management programs. As training objectives, learning safe work practices, recognition of job hazards and appreciating other precautionary measures can significantly contribute to the goal of minimizing occupational risk of injury as well as disease. This paper reviews the importance of safety and health training to prevent work place incidents in the petroleum sector.
The Petroleum industry faces abundant challenges including global climate changes, sustainable development and of course, environmental and workplace health and safety. Whereas the sector’s implementation of health and safety management systems has yielded considerable advancements in industry-wide safety performance measures over the last few years, persistent vigilance is necessary, particularly in the area of employee safety and health. Many petroleum companies provide wide-ranging safety and health training for their staff to make sure they know and observe the latest safety and health procedures and are able to operate and maintain equipment safely in the workplace. ...
... A number of firms develop internal safety training programs or contract safety experts to execute these programs.
Petroleum firms work diligently to put in place emergency response plans, in addition to preparing workers with training exercises in case of emergencies. Most of these firms hold safety meetings with their team regularly to ensure potential risks are addressed and fortification of safety practices are followed. Work-related safety covers the daily hazards, most of which are within the control of a competent, well-supervised working group. Every employee has to behave responsibly and be conscious of immediate hazards. Failure of workplace safety results in the bulk of lost-time injuries, which are caused by slips or falls, poor materials handling and misuse of tools/equipment. All employees in the petroleum sector as well as in other sectors must be trained in appropriate work procedures and educated to work safely. It is the responsibility of management to provide sufficient safety training and education to employees. Safety training may include on-the-job training, formal classes, reading assignments, written tests, one-on-one discussions and online training. Employees have to be convinced that it is their responsibility to work safely, and that they benefit their organization as well as themselves in doing so. The goal of preventing accidents and illnesses can only be realized through well-developed and synchronized training efforts, which incorporate training for employees, safety officials, supervisors as well as management personnel.
Training programs should be designed in such a way to instruct employees in their work performance in a healthful and safe manner. The training should be in line with the responsibility level of each individual. It is important to train staff in safety because untrained staff can: injure themselves and others, cause needless expenses, and come up with their own methods of performing tasks. Well trained employees are not only a benefit to themselves, but also to their coworkers, their employers and their clients. Educating employees on the safety regulations of the work environment also gives them a sense of safety and security as they perform daily tasks, which leads to increased productivity. Additionally, safety training is important since it provides a way for organizations to document proof that such training has taken place, protecting them from possible lawsuits involving injuries.
Literature review
In the United States, over 11.3 million workers are seriously injured, and approximately 11,000 employees are killed on the job annually. An estimated $155 billion is paid by U.S. employers in direct costs (e.g. insurance premiums and workers' compensation) related to workplace injuries, adding up to over $1,400 for each work-related injury (Williams & Geller, 2000). Employees face several instances through the course of a typical workday where they put themselves at risk for injury. In the year 2000, about 2,810,000 falls, 724,000 burns and 425,000 violence cases were reported in Iran, a major producer of crude oil (Rafieifar, 2005). The number of deaths as a result of workplace injuries is estimated to be 25,365. According to a study by Nasab and Ghofranipour (2008) the damage caused by workplace accidents rose from 4.5 million dollars in 1991 to 42.5 million dollars in 2001. Research on workplace accidents in Iran indicates that chemical, metallic and electrical industries had the highest accident rates and over 90% of the casualties were male employees with low level of education (Rafieifar, 2005).
Over the past century, petroleum has emerged as one of the most sought after energy source in the world. Even though alternative sources of fuel continue to be developed, petroleum is still in high demand in both developed and developing countries. Today’s petroleum industry must operate in a universal community that seems to be getting smaller by the day. On the other hand, petroleum-related tasks and technology in this competitive climate have become more complex (Markussen, 2006). Operations within this industry have become more complicated and challenging. In order to reap the benefits from petroleum production, some risk have to be taken. Apart from monetary risks required for actual production, refining and marketing of products, some of the risks are on a more personal level i.e. safety and health risks to employees and contractors, the communities around the workplace as well as the environment in which we live. Employees and contractors in the petroleum industry face a risk from continued exposure to harmful chemicals and physical hazard agents for long hours and at great concentrations. In order to lessen and avoid the risk to employee from such harmful exposure, management programs/systems that include effectual standard operating procedures, appropriate communication of such procedures and proper safety and health training must be developed and implemented.
According to a study by Health Watch conducted in Australia, it was found that petroleum industry workers have better health than the general community. However, the study revealed that the risk of leukemia in petroleum workers was greater than in the general population. Leukemia has been an ailment of special concern in the industry due to its association with benzene exposure (Health Watch, 2007). The industry has taken major steps to minimize exposure to petroleum products particularly benzene. The known connection between benzene and leukemia has seen governments around the world set workplace exposure standards for benzene and oil companies have taken measures to ensure that they adhere to them. Health Watch results further showed that a higher rate of melanomas was diagnosed in workers in the petroleum sector. Workers in the petroleum industry were reported to be more likely to have the disease detected sooner than in the general population. An increased melanoma prevalence rate can result from this increased rate of reporting (Health Watch, 2007). Noise and vibration from drill floors, generators, shakers and other equipment can also pose significant health risks to workers. Where noise cannot be avoided, the typical approach has been to set up noise control zones necessitating the use of hearing protection. Further, the use of hand-held vibrating tools is common on offshore installations (e.g. needle guns, grinders, impact wrenches, chipping hammers and air drills). This creates the likelihood for hand–arm vibration disorder in workers who use such tools regularly. Diverse forms of radiation as well as thermal extremes are also fairly common on offshore sites. Exposure to direct sunlight and intense heat in tropical areas and to intense cold in high latitude areas can become major sources of health risk depending on the geographical region.
The author is associated with
The author is senior writer at https://www.allacademicanswers.com
Add Comment
Education Articles
1. Guaranteed Grades: Pay Someone To Take My ExamAuthor: Doug Macejkovic
2. Blocks Before Books
Author: Michale
3. Azure Devops Training Online | Azure Devops Online Training
Author: visualpath
4. Learn Python Programming - from Basics To advanced
Author: vishal more
5. Data Engineering Course In Hyderabad | Aws Data Analytics Training
Author: naveen
6. Oci Online Training | Oracle Cloud Infrastructure In Hyderabad
Author: visualpath
7. Best Salesforce Data Cloud Certification Training
Author: visualpath
8. The Benefits Of Online Dry Needling Certification
Author: Daulat
9. Top Google Cloud Data Engineer Training In Bangalore
Author: Visualpath
10. Aima’s Management Diploma: The Smart Choice For Future Leaders
Author: Aima Courses
11. How Regular Mock Test For Bank Help You Crack Bank Exams
Author: Ayush Sharma
12. Debunking The Myth: Is Preschool Just Playtime?
Author: Kookaburra
13. Cps Global School: A World-class Learning Destination In Chennai
Author: CPS Global School
14. Chennai Public School: Shaping Future Leaders Through Excellence In Education
Author: Chennai Public School
15. "transform Your Data Analysis With Lcc Computer Education's Excel Training"
Author: Khushi Gill