ALL >> Technology,-Gadget-and-Science >> View Article
Alternative Energy Series Fast Burn Conversion
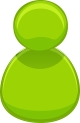
The best candidates for fast burn conversion are spark ignited piston engines with adjustable spark timing. Those with carburetors as original equipment do not have computers that control additional automotive functions besides fuel metering and spark timing. The fast burn engine can't use computer management as a low cost conversion option. If an idle circuit similar to that of a carburetor is added to a fuel injection throttle body as a spacer plate, a throttle body might be able to serve as a basic carburetor for cold vapor fuel. Many modern fuel injected engines can be owner retrofitted with carburetors and aftermarket or used factory intake manifolds for use with carburetors.
The traditional multi circuit carburetor is not required for vapor fuel, but is less expensive than producing new twin circuit carburetors designed specifically for vapor fuel. All carburetor air vents should be plugged so engine vacuum signals draw only from the unvented carburetor fuel bowl, which is connected to the fuel bubbler in the tank or racing fuel cell. The fuel float and needle valve assembly is removed. Any accelerator pump ...
... is removed and the enrichment hole is plugged. In carburetors that use vacuum power valves, such can be used to fine tune vapor flow according to vacuum signals. The idle circuit must retain adjustment from barely open to wide open.
Rod and jet enrichment systems such as used on Carter and Rochester carburetors can also be used to fine tune vapor mixtures. Go as lean as you can without the engine stumbling under load on the power circuit and richen slightly for best throttle response. If the max power metering is sufficient with selected main jets, which flow much more vapor than liquid, we can regulate the maximum fuel supply by means of an adjustable valve in the supply line. Start the fast burn engine with the idle mixture screw open wide and quickly close it after the engine starts. Back the adjustment screw off one turn after you stall the engine for lack of idle fuel. Too much idle fuel could melt engine parts as easily as too much fuel in the power circuit. If we never meter more fuel than can burn in half a power stroke, we avoid meltdown while maximizing power and fuel economy, minimizing exhaust emissions.
With fast burn, we want to retard initial spark timing to between sixty and eighty degrees after top dead center. On a V-8 we can move each wire in the distributor cap forward one position on the cap in the direction of rotor rotation. This will retard timing 90 degrees from the standard initial timing. A timing light on the number 8 cylinder will allow you to set initial timing with the stock timing marks. Setting number 8 cylinder for ten degrees advance would have number one cylinder firing at 80 degrees after top dead center. 20 degrees advance would have number one firing at 70 degrees ATDC, etc. An aftermarket timing tape, when available, is another way to accurately set spark timing. Otherwise, one can remove the crankshaft dampener or pulley with timing marks, measure the circumference, divide by 4 and mark at 90 degrees ATDC, 85, 80, 75, 70, 65, and 60 degrees. Marking all the way back to 30 degrees ATDC is a good idea. This is the most advance likely practical for max fast burn power and allows one to check for total mechanical or electronic spark advance. Optimum timing for best performance and economy, like fuel mixture, must be worked out by road testing the converted vehicle.
Fully vaporized fuel is likely to be combustible over a wide range of air/fuel ratios. As a safety precaution it makes sense to install a PCV valve or something similar. Should a timing chain let go or an intake valve bend, we don't want fire in the intake manifold to find its way back to our bubbler and explode it. Better that a fuel supply line disconnect or rupture under the hood from combustion back pressure.
The bubbler where our vapor is made by engine vacuum, is a modified fuel tank or racing fuel cell. Our tank/cell must be vented to atmosphere. We want our air pick up filtered with something like a lawnmower air filter and mounted higher in or outside the vehicle, than the outside of the fuel filler tube, which is the most convenient place to tap our tank/cell for a very rich vapor.
On the typical fuel tank, our air vent can be easily installed where the original fuel supply line attached. We want another PCV valve near our air supply filter to seal the tank from atmosphere when the vehicle is not running and the tank/cell is pressurized by atmospheric heat. Gas expansion in our tank now moves fuel through the carburetor into the intake system, where it allows instant starts, as with fuel injection.
Bubbler design is guesswork. Whatever supplies the most consistent air/vapor mixtures from a tank 3/4, 1/2, 1/4 and 1/8 full, is what we want. Variations in vapor from the tank will make engine tuning difficult and variable. Consistent mixture from the bubbler is important. If the air supply is opposite the vapor supply line, we would expect a richer vapor than if the air supply line was near the vapor supply line. We want the air supply line to lie on the bottom of the tank, below whatever fuel we have. We never want the fuel tank full, so a drain in the air supply line will be handy for accurately checking fuel economy. You add ten gallons to an empty tank and drive until a working fuel gauge goes below 1/4 tank and you then drain the remaining fuel from the tank into gallon jugs. Subtract the remaining fuel from the ten gallons you started with. Divide the gallons used, into the miles driven and we will know our MPG.
We never want to fill our fuel tank to filler nozzle shut off, as that would give us a minimal surface area from which to vaporize our fuel and our mixture could then be too lean to run our engine. However, if one wanted to build a vapor chamber and install it above the top of the fuel tank and filler tube, there might not be much difference when the tank is overfilled. One thing we definitely want to avoid is liquid fuel in our vapor supply line. Though it is unlikely the liquid fuel would reach the carburetor, the more it wet the vapor supply line, the richer the mixture would be at the carburetor.
I envisioned a tri Y air bubbler on the fuel tank floor, to evenly distribute air in the tank. The line connecting to the old fuel supply line, inside the tank would split into two equal length lines of the same diameter from a Y or T connector. The two lines are then split into two more equal length tubes (fuel proof, of course) and porous air bubblers to make small bubbles moving through the fuel. This would give us a richer mixture at the fuel supply line, than a single tube with no air diffusers. I would terminate my air supply lines with those bronze fuel filters many carburetors used just ahead of the needle and seat assembly at the end of the supply line. Short term tests I did several years ago showed that the ceramic bubbler filter for fish aquariums gave very fine air bubbles and did not seriously deteriorate in gasoline. They were not very expensive.
I can only guess at supply line sizes. My guess is that the filtered air supply line need be no more than a quarter inch ID. The vapor supply line probably needs to be no greater than three eighths inch ID.
These are the basics of a cold vapor, fast burn fuel system. I would expect improvements to come rapidly following road testing. When we know the typical optimum spark timing and air/fuel mixtures, we can apply this knowledge to small engines with fixed spark timing, like lawn mowers, snow blowers and electrical power generators.
My expectations of fast burn performance is between two and three horsepower per cubic inch displacement, which would make fast burn conversion the best power bang for the dollar. No other modification can come close in dollar costs. Under most racing rules, fast burn would be legal for the allowed fuel and add more power than supercharging or nitrous oxide injection. Yet, these power boosters will add a lot more power to a fast burn engine than to a slow burn engine. Hence, the fast burn conversion will out perform slow burn by a wide margin, regardless of class allowed modifications. The fast burn conversion can also be camouflaged to look stock by plumbing the supply line through a non functional fuel pump.
As to economy, Charles Pogue exceeded 200 MPG with his hot vapor, ‘37 V-8 Ford, which would rarely yield 20 MPG in slow burn configuration. Uniform cold vapor might have allowed him to achieve the 300 MPG economy he was shooting for, while more than doubling stock power output. When fast burn conversions become common, performance and economy contests will lead to rapid improvements in the very simple technology.
As to emissions, if we are consuming less than 10% of the fuel per mile driven, emissions will be less than 10% of the slow burn equivalent. Burning 100% of the fuel on a shortened power stroke, will further dramatically reduce emissions, probably to less than 5% of slow burn engines. In addition, the much higher power outputs of fast burn engines allows engine downsizing. A 300 cu. in. slow burn engine can be replaced with a 140 cu. in. fast burn engine and still provide a power increase. Economy is improved, along with emissions. Big cars and trucks Americans favor, in fast burn configuration will easily exceed hybrid electric cars in economy and reduced emissions, as well as power. On the other hand, a fast burn hybrid could top 400 MPG if we want to go that far.
I would love to hear from any individuals or groups already doing fast burn conversions and learn what they have learned. While the piston engine has had a bad rap for efficiency due to the liquid fuel systems, the Tesla Turbine, seldom used as a combustion engine, can be built as a very lightweight, compact, multi stage, supercharged, exhaust scavenged 30 horsepower per pound, fast burn engine. The Tesla Turbine with only one moving part is cheap and easy to manufacture in a small machine shop. The turbine requires no drive train except the connection to the drive wheels. No gear reductions, instant tire spinning torque and instant rotational reversal for engine braking. Stay tuned for more on the potential of this remarkable engine, developed early in the 20th Century and virtually ignored by industry ever since, except for vastly superior pumps.
About the Author
Freelance writer published on many websites and newspapers.
justanotherview.com
edhowes@hotmail.com
Add Comment
Technology, Gadget and Science Articles
1. Cloud Storage Providers In India | Cloud Computing Services In IndiaAuthor: Sathya Technosoft
2. The Future Of Multilingual Web Development: Smarter, Faster, Global
Author: Addxp Technologies
3. Bubbling Life Back Into Lakes: The Power Of Micro Nano Bubble Generators
Author: NICO Nanobubbles
4. Ai Call Centers: Boosting Efficiency, Reducing Costs, And Improving Customer Experience (cx)
Author: precallai
5. What Is The Future Of Blockchain Technology In India?
Author: DC Kumawat
6. Ice Line Freezer: Revolutionizing Cold Chain Storage In Laboratories And Healthcare
Author: kabir Digital
7. How To Scrape Product Info, Images & Brand Details From E-commerce Sites - A Complete Guide
Author: Real Data API
8. The Pros And Cons Of Outsourcing Mobile App Development
Author: Chloe Decker
9. It Helpdesk Provider Business – Reliable It Support In Singapore
Author: Entrust Network Services
10. Unveiling Florida's Premier Banner Printing Services: Quality And Affordability Combined
Author: printitusa
11. Transforming Hr Efficiency: Walkme For Human Capital Management
Author: Stephen Pech
12. 5 Best Ai Tools For Ai Marketing In 2025
Author: jatin
13. How Social Media Can Help You Grow Your Business
Author: jatin
14. Why Rooftop Solar Is The Smartest Investment For Your Home
Author: Seo Globo
15. Best Light Therapy Glasses For Better Sleep And Energy
Author: Joe Stewart