ALL >> Hardware-Software >> View Article
Is Optimizing Inventory A Big Challenge For Manufacturers And Service Managers
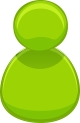
Inventory Management is a rather broad and complex topic with manufacturers and service managers. A lot has already been discussed about it, but the classic question remains the same: Is optimizing inventory a big challenge for manufacturers? Quite often than not, the answer that we receive is Yes. With multiple processes for managing the inventory, and no standard structure, Inventory Management often sounds like an oxymoron. Here are few of the reasons listing why optimizing inventory is a big challenge for manufacturers and service managers:
Challenge No. 1: Tracking and Analysis of Demand and Inventory Planning: The information of sale, purchase and movement of products is collected in the style and manner of each individual. Typically, first this information is written on papers, and is later entered into a computer system. Since the information is entered in multiple formats, tracking and analysis of inventory take a backseat. Hence the only analysis of Demand Vs. Inventory Planning comes with the physical audits that happen periodically. This is one of the biggest challenges faced by manufacturers, ...
... wherein people, system and databases don't talk with each other.
This leads to the collection of inaccurate real-time data throughout the product supply chain. Many OEMs have multiple trading partners who may all use different ERP systems to keep track of the data. As a result, majority of the OEMs still rely on complex spreadsheets and databases to track inventory, making it difficult to estimate the inventory required to deliver product to end customers timely.
Challenge No. 2: Mismanagement of Inventory: Another very taxing challenge in inventory management exists in poor demand forecasting due to the non-availability of correct and valid data. The inventory eventually grows to the point where the numbers are just too big to ignore. It is at this point that the excess inventory gets the attention of management. These scenarios often lead to increased operational cost and decreased efficiencies.
Challenge No. 3: Managing Forward and Reverse Logistics: Factors like consumer buying behavior, seasonal changes, consumer promotions and new product launches drive product returns, resulting in a complex inventory return management. While there are streamlined processes that define the forward logistics, manufacturers and service managers neglect the reverse logistics process. Some manufacturers claim to have enabled multi-channel returns; however, the majority of them have disparate systems for each channel.
Planning the service supply chain is very critical in achieving customer service at a low cost. So with challenges like these, how do manufacturers and service managers remain competitive? Strategic, Tactical or Operational in nature, to overcome the challenges related to inventory management, you must make several important decisions, which may include:
Capturing the variability in demand and supply
Determining a procurement budget
Defining the quantity of inventory you should hold
Implementing specialized service management software
Reviewing sales and service reports periodically
Reviewing buying plans and adjustments as required
Inventory Control and Management helps you improve delivery performance, reduce inventory costs, decrease TAT and measure performance against objectives. The challenges are part of the process, but aren't too big to tackle. All you need is a streamlined approach that is quick and efficient. An effective after-sales Service Management Software capable of automating end-to-end service management processes including complete inventory tracking & management is must have for the manufacturers and service partners to run their business processes smoothly and without burning their pockets.
Rakesh Kumar is a business consultant of Zed Serviceâ„¢. Zed Serviceâ„¢ is a leading service management software in India. Zed Serviceâ„¢ has lots of innovative features including service management software, warranty tracking software etc.To know more visit our web site www.service-management-software.net now!
Add Comment
Hardware/Software Articles
1. Top Tips To Improve Ecommerce Customer Support ServicesAuthor: Kuldeep Singh Tomar
2. White Label Polymarket Clone Scripts: Key Features And Advantages For Entrepreneurs
Author: judemaxwell
3. How Alumni Engagement Programs Boost University Reputation And Enrollment
Author: Brenda Joyce
4. Reducing Errors In Law Enforcement: The Precision Of Electronic Warrants
Author: Edwin
5. Inventory Management For Startups: A Beginner's Guide To Success
Author: Hourglass IT
6. Lean It Uses Contemporary It Solutions To Enhance Business Operational Efficiency
Author: Lean IT
7. Streamline Your Business With The Best Pos Billing Software
Author: Eazybills
8. A Deep Dive Into Ask On Data
Author: Vhelical
9. Financial Consolidation Software: A Necessity In Today’s Complex Financial World
Author: BiCXO
10. Mobile Application Development Company: Innovating For The Future
Author: Quickway Infosystems
11. 2025's Top Choice For Casino Entrepreneurs: 7bitcasino Clone Script
Author: aanaethan
12. Online Admission Management Software
Author: Aditya Sharma
13. The Role Of Technology In Enhancing Student Retention
Author: Brenda Joyce
14. Capcut Template New Trends: A Glimpse Into The Future Of Video Editing
Author: Oliver Nash
15. Understanding Canva Mod: Is It Worth The Hype?
Author: Mason Brooks