ALL >> Business >> View Article
The Importance Of Press Brake Tooling
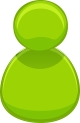
Keyword: press brake tooling
Link: https://www.lmrmtool.com/exploring-the-leading-brands-of-press-brake-tooling/
Press brake tooling plays a critical role in sheet metal fabrication, directly affecting bending accuracy, efficiency, and overall production quality. Whether in small-scale workshops or large industrial manufacturing plants, selecting the right press brake tooling can significantly enhance operational performance and reduce material waste.
High-quality tooling ensures precise bends, minimizes errors, and extends machine lifespan. On the other hand, improper tooling selection can lead to inconsistencies, rework, and increased production costs. Therefore, understanding press brake tooling and choosing the most suitable options for specific applications is essential for any metal fabrication business aiming to improve efficiency and maintain competitive advantages.
Types of Press Brake Tooling
Press brake tooling consists of upper and lower dies that work together to bend sheet metal into desired shapes. Choosing the right type of tooling is essential for achieving accurate and consistent ...
... bends. Below are the main types of press brake tooling:
1. Upper Tools (Punches) and Lower Tools (Dies)
Punches:The upper tools that press the sheet metal into the lower die to create the bend. Punches come in various shapes, such as straight punches, gooseneck punches, and radius punches, to accommodate different bending requirements.
Dies:The lower tools that determine the final bend angle and shape. Common die types include V-dies, U-dies, and hemming dies.
2. Standard vs. Custom Tooling
Standard Tooling:These are pre-designed punches and dies that fit general bending applications. They are cost-effective and widely available.
Custom Tooling:Designed for specific bending needs, custom tooling ensures precision for complex or unique shapes but often comes at a higher cost.
3. Common Tooling Materials
The material of the tooling affects its durability, precision, and resistance to wear. The most common materials include:
Carbon Steel:Low-cost but wears out quickly, suitable for light-duty applications.
Alloy Steel:Offers better hardness and durability than carbon steel.
Hardened Tool Steel:Highly durable and resistant to wear, ideal for high-volume production.
Carbide-Coated Tooling:Provides excellent wear resistance and long service life, suitable for demanding applications.
Selecting the appropriate press brake tooling depends on the material type, thickness, and desired bending angle. Proper tooling ensures accurate results, minimizes material waste, and enhances overall productivity in metal fabrication processes.
How to Choose the Right Press Brake Tooling
Choosing the right press brake tooling is crucial for ensuring high-quality bends, reducing material waste, and optimizing production efficiency. Several factors need to be considered when selecting tooling for your press brake. Here’s a guide to help you make the best choice:
1. Material Thickness and Type
Thickness:The material thickness is one of the most important factors in tooling selection. Thicker materials require larger, stronger dies and punches to create the desired bend. For example, a V-die with a larger opening may be needed for thicker materials to prevent excessive force or tool wear.
Material Type:Different materials, such as stainless steel, aluminum, or mild steel, have varying levels of hardness and bending characteristics. For harder materials, you may need specialized tooling, such as high-strength punches and dies, to handle the additional stress.
2. Bend Angle and Geometry
Bend Angle:The angle of the bend influences the type of tooling required. For sharp bends, specialized tooling such as gooseneck punches may be necessary. The angle of the V-die also plays a role, as a smaller V-opening is used for sharper angles.
Bend Geometry:If your project requires specific shapes, such as a complex contour or radius, custom tooling might be required. Custom dies and punches are designed to match the specific geometry of the part you need to produce.
3. Precision and Tolerance
Tolerance:Precision is vital when selecting tooling. For applications that demand high tolerance, like aerospace or medical components, tooling with tighter tolerances should be used to ensure that the bend remains within the specified range.
Surface Finish:The tooling material and its finish can also affect the final product. High-quality tooling with smooth finishes will minimize surface imperfections, which is particularly important for decorative or visible parts.
4. Production Volume and Cycle Time
Low vs. High Volume:If your production is low-volume or for prototypes, you may opt for standard tooling, which is more affordable and readily available. For high-volume production, investing in custom tooling or tooling made from durable materials such as carbide-coated steel might be necessary to maintain efficiency and extend tool life.
Cycle Time:Faster cycle times depend on the efficiency of the tooling. Tooling that is easy to change and can handle materials with minimal adjustments can reduce downtime and improve overall productivity.
5. Cost vs. Performance
Balancing the cost of tooling with its performance is crucial. While custom or specialized tooling can be more expensive, it may provide a longer lifespan and greater precision, which can reduce the overall cost per part in high-volume operations.
Conversely, standard tooling may be sufficient for less demanding applications and can be a more cost-effective choice for businesses that need to prioritize budget over customization.
By carefully evaluating these factors—material properties, bend angles, precision requirements, production volume, and cost—you can select the right press brake tooling that ensures optimal results while maximizing productivity and minimizing costs.
About us
LMRMis a professional manufacturer specializing in high-quality press brake tooling. With years of expertise in the industry, LMRM is dedicated to providing innovative, durable, and precision-engineered tooling solutions for sheet metal fabrication. Their commitment to quality and customer satisfaction has made them a trusted partner for businesses seeking reliable and efficient manufacturing solutions.
Whether you're looking for standard or custom tooling, LMRM offers a range of products designed to meet the needs of various industries, ensuring optimal performance and long-lasting results.
Add Comment
Business Articles
1. Why Bookkeeping For Cpa Firms Is Essential For Growth And ComplianceAuthor: Niharika Jain
2. Kitchen Remodels Ideas: Farmhouse Kitchen Design Ideas To Warm Your Heart
Author: Vikram kumar
3. Top 8 Bi Tools With Intelligent Data Analytics Capabilities
Author: Maria
4. Top 5 Mistakes To Avoid When Getting An International Shipping Quote
Author: Tom
5. The Ultimate Guide To Cheap Rdp: Affordable And Secure Remote Desktop Solutions
Author: DigiRDP
6. The Role Of Financial Advisory Companies In India
Author: Drishti Desai
7. How Jaspire Makes Student Visa Approvals Faster And Easier
Author: pavitra
8. Finding The Best Pediatric Eye Doctor In Thane For Your Child’s Vision Care
Author: Anil Eye Hospital
9. Retirement Planning In 2025
Author: jkanishk
10. Cynosure Apogee For Rent: Expand Your Laser Hair Removal Services Without The Upfront Cost
Author: Ryan
11. Selectech, Inc. Receives Environmental Product Declaration For Ecolock
Author: Steven Dubin
12. Master Photo Editing With Google Photos: Top Tips And Professional Services To Elevate Your Images
Author: Sam
13. Mg Astor Automatic Price In Chennai: A Smart Suv Worth Exploring
Author: balaji
14. Find The Best Morris Garage Showroom
Author: balaji
15. How To Save Hours On Editing With Smart Clipping Path Techniques
Author: ukclippingpath