ALL >> General >> View Article
Multi-rifled Seamless Cold-drawn Boiler Tubes: A Revolution In Power Generation
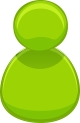
Introduction:
In the relentless pursuit of enhanced efficiency and reliability within the power generation sector, innovation in boiler technology plays a pivotal role. Among the groundbreaking advancements, multi-rifled seamless cold-drawn boiler tubes stand out as a revolutionary solution, promising significant improvements in heat transfer, operational efficiency, and overall power plant performance. These specialized tubes, meticulously engineered through a combination of seamless manufacturing and cold-drawing processes, coupled with an internal rifled design, are redefining the standards for heat exchange in modern boilers. This article delves deep into the intricacies of multi-rifled seamless cold-drawn boiler tubes, exploring their manufacturing process, unique advantages, impact on power generation, and the crucial role played by Seamless Heat Exchanger Tube manufacturers and Coil Formed Tubes Manufacturers and Suppliers in their widespread adoption.
Understanding the Fundamentals:
To appreciate the significance of multi-rifled seamless cold-drawn boiler tubes, it's essential to understand the individual ...
... components of their name and manufacturing process:
Seamless: Unlike welded tubes, seamless tubes are manufactured from a single piece of metal, typically through processes like hot extrusion or piercing. This eliminates the weld seam, a potential point of weakness, resulting in superior strength, enhanced corrosion resistance, and higher pressure-bearing capabilities. This inherent robustness makes them ideal for the demanding conditions within a boiler.
Cold-Drawn: Following the initial shaping, the tubes undergo a cold-drawing process. This involves pulling the tube through a series of dies with progressively smaller diameters. Cold drawing refines the tube's dimensions with exceptional precision, improves surface finish, increases tensile strength and hardness, and ensures a uniform microstructure.
Multi-Rifled: The most distinctive feature is the internal rifling. This involves creating a series of helical grooves or ribs on the inner surface of the tube. These riflings induce a swirling flow of the fluid (water or steam) passing through the tube. This turbulent flow disrupts the laminar boundary layer that typically forms along the tube wall, significantly enhancing heat transfer efficiency.
Boiler Tubes: These tubes are specifically designed for use within boilers, the heart of thermal power plants. They are responsible for transferring heat from the combustion gases to the water, generating steam to drive turbines and produce electricity.
The Manufacturing Process: A Symphony of Precision
The creation of multi-rifled seamless cold-drawn boiler tubes is a complex and tightly controlled process, demanding expertise from Seamless Heat Exchanger Tube manufacturers and specialized Coil Formed Tubes Manufacturers and Suppliers. The general steps involved include:
Raw Material Selection: High-quality steel alloys with specific chemical compositions and mechanical properties, capable of withstanding high temperatures and pressures, are carefully selected.
Seamless Tube Formation: The chosen material is processed to create a seamless tube, typically through hot extrusion or rotary piercing. This ensures the absence of any weld lines.
Cold Drawing: The seamless tube is then subjected to multiple passes through a series of cold drawing dies. This reduces the tube's diameter and wall thickness to the desired dimensions, while simultaneously improving its mechanical properties and surface finish.
Internal Rifling: This crucial step involves creating the helical grooves on the inner surface of the tube. Various techniques can be employed, including:
Mandrel Drawing: A shaped mandrel with the desired rifling pattern is inserted into the tube as it is drawn through a die.
Rotary Swaging: Specialized tools with the rifling profile are used to impart the pattern onto the inner surface as the tube rotates.
Internal Machining: Precision cutting tools are used to create the grooves on the inner bore.
Heat Treatment: After cold drawing and rifling, the tubes may undergo heat treatment processes like annealing or normalizing to relieve internal stresses and optimize their microstructure for the intended application.
Finishing and Inspection: The tubes are subjected to rigorous quality control checks, including dimensional accuracy, surface finish, mechanical property testing, and non-destructive testing (NDT) to ensure they meet stringent industry standards.
Coiling (Optional): In many boiler designs, these tubes need to be formed into coils. Specialized Coil Formed Tubes Manufacturers and Suppliers utilize precision bending techniques to create the required coil shapes without compromising the tube's integrity or the rifling pattern.
Advantages that Drive the Revolution:
Multi-rifled seamless cold-drawn boiler tubes offer a compelling array of advantages that contribute to their increasing adoption in modern power generation:
Enhanced Heat Transfer Efficiency: The primary advantage of the internal rifling is the significant improvement in heat transfer. The swirling flow induced by the ribs disrupts the stagnant boundary layer, leading to increased turbulence and better contact between the fluid and the tube wall. This results in:
Higher Steam Generation Rates: More efficient heat absorption translates to faster and greater steam production.
Reduced Fuel Consumption: For the same steam output, less fuel is required due to the improved heat transfer, leading to lower operational costs and reduced emissions.
Smaller and More Compact Boiler Designs: The enhanced heat transfer allows for the use of fewer or smaller tubes to achieve the same heat exchange capacity, leading to more compact and potentially less expensive boiler designs.
Improved Operational Reliability: The seamless construction and cold-drawing process contribute to enhanced reliability:
Elimination of Weld Weaknesses: The absence of weld seams removes potential failure points, increasing the tube's resistance to stress and fatigue, especially under high pressure and temperature conditions.
Superior Corrosion Resistance: The uniform microstructure achieved through cold drawing and the absence of weld heat-affected zones often lead to better resistance to various forms of corrosion.
Reduced Fouling: The turbulent flow induced by the rifling can help to minimize the deposition of scale and other fouling materials on the inner tube surface, maintaining heat transfer efficiency over longer periods and reducing the need for frequent cleaning.
Enhanced Flexibility in Design: The availability of these tubes from specialized Coil Formed Tubes Manufacturers and Suppliers allows for greater flexibility in boiler design:
Complex Coil Geometries: The ability to form intricate coil shapes enables optimized heat exchanger configurations within the boiler.
Adaptability to Different Boiler Types: Multi-rifled seamless cold-drawn tubes can be implemented in various boiler designs, including subcritical, supercritical, and ultra-supercritical power plants.
Suitability for High-Pressure and High-Temperature Applications: The inherent strength of seamless tubes, further enhanced by cold drawing, makes them ideal for the demanding operating conditions of modern high-efficiency power plants.
Lower Maintenance Costs: The improved reliability and reduced fouling contribute to lower maintenance requirements and longer operational lifespans for the boiler.
Impact on Power Generation:
The adoption of multi-rifled seamless cold-drawn boiler tubes is having a profound impact on the power generation landscape:
Increased Plant Efficiency: The enhanced heat transfer directly translates to higher overall plant efficiency, reducing the amount of fuel needed to generate a specific amount of electricity. This leads to significant cost savings and a lower carbon footprint.
Reduced Emissions: Lower fuel consumption inherently results in reduced emissions of greenhouse gases and other pollutants, contributing to more environmentally friendly power generation.
Improved Plant Availability: The increased reliability of these tubes minimizes downtime due to tube failures, leading to higher plant availability and more consistent power supply.
Support for Advanced Power Plant Technologies: The capabilities of these tubes are crucial for the efficient operation of advanced power plant technologies like supercritical and ultra-supercritical boilers, which operate at higher temperatures and pressures to achieve greater efficiency.
Contribution to Sustainable Power Generation: By enabling more efficient and cleaner power generation, multi-rifled seamless cold-drawn boiler tubes play a vital role in the transition towards a more sustainable energy future.
The Role of Manufacturers and Suppliers:
The widespread adoption and continued innovation in multi-rifled seamless cold-drawn boiler tubes rely heavily on the expertise of specialized manufacturers and suppliers:
Seamless Heat Exchanger Tube Manufacturers: These manufacturers possess the core expertise in producing high-quality seamless tubes with the precise metallurgical properties required for boiler applications. Their understanding of material science, seamless manufacturing processes, and quality control is fundamental.
Coil Formed Tubes Manufacturers and Suppliers: These specialized entities play a crucial role in transforming the straight seamless tubes into the complex coil geometries often required in boiler designs. They employ advanced bending techniques and quality assurance measures to ensure the integrity of the tubes and the rifling pattern throughout the coiling process. Their ability to provide customized coil solutions is essential for boiler OEMs and power plant operators.
The collaboration between these manufacturers and the power generation industry is vital for driving further advancements in boiler technology and ensuring the reliable supply of these critical components.
Challenges and Future Directions:
Despite the numerous advantages, there are ongoing challenges and areas for future development:
Manufacturing Complexity and Cost: The production of multi-rifled seamless cold-drawn tubes is a complex process that can be more expensive than conventional tubes. Continuous efforts are needed to optimize manufacturing techniques and reduce costs.
Material Selection for Extreme Conditions: As power plants strive for even higher efficiencies with supercritical and ultra-supercritical technologies, the demand for materials that can withstand increasingly extreme temperatures and pressures continues to grow. Ongoing research into advanced alloys is crucial.
Further Optimization of Rifling Designs: Research and development efforts are focused on optimizing the geometry and pattern of the internal rifling to achieve even greater heat transfer enhancement and reduced fouling under various operating conditions.
Integration with Advanced Boiler Designs: Continued collaboration between tube manufacturers and boiler designers is essential to seamlessly integrate these advanced tubes into innovative boiler configurations.
Conclusion:
Multi-rifled seamless cold-drawn boiler tubes represent a significant leap forward in heat transfer technology for power generation. Their unique combination of seamless construction, precise cold drawing, and innovative internal rifling offers a compelling solution for enhancing boiler efficiency, improving operational reliability, and reducing environmental impact. The expertise of Seamless Heat Exchanger Tube manufacturers and Coil Formed Tubes Manufacturers and Suppliers is indispensable in producing and delivering these critical components to the power industry. As the demand for cleaner and more efficient power generation continues to grow, multi-rifled seamless cold-drawn boiler tubes are poised to play an increasingly vital role in shaping the future of power plant technology, driving a revolution towards a more sustainable and reliable energy landscape. The continuous innovation in materials, manufacturing processes, and design optimization promises even greater advancements in the years to come, further solidifying the importance of these specialized tubes in the quest for efficient power generation.
Add Comment
General Articles
1. Categorization Of Plant Life CycleAuthor: Anthea Johnson
2. Commercial Spaces Need Style Too! Transforming Cafés & Resorts With Custom Pergolas
Author: Noor Mariam
3. Level Up Your Hana Adventure: Why An Audio Tour Is Your Best Road Trip Companion
Author: Katie Law
4. Best Erp Software Solution Company In Noida For Schools And Colleges
Author: CONTENT EDITOR FOR SAMPHIRE IT SOLUTIONS PVT LTD
5. Hinduism: Environmental Friendliness And Protecting Nature
Author: Chaitanya Kumari
6. From Ai To App Store: How Generative Tech Is Reshaping Ios Experiences
Author: Sara Wilson
7. Faston Service In Noida — Reliable, Affordable & Quick Home Ac Repair Services
Author: faston services
8. What Are The Uses And Benefits Of A Vegetable And Fruit Dryer?
Author: DYNAMIC DRYERS INTERNATIONAL
9. Primary Care Without Insurance In Raleigh
Author: satyamprimarycare
10. All Four Paws Offers Champion English Cream Golden Retriever Puppies In Indiana
Author: Geroge
11. Box Truck Wraps: The Ultimate Moving Billboard For Your Brand
Author: Saifee Signs
12. Generative Ai And Data Science Course In Hyderabad
Author: Hari
13. Mca Guidelines For Company Name
Author: Startupporta Business Services
14. Seo Services In Chennai: Boost Your Online Visibility With Proven Strategies
Author: istudio technologies
15. Best Internet Marketing Service In India
Author: Matrix Web Studio