ALL >> Technology,-Gadget-and-Science >> View Article
The Importance Of Torque Wrench Calibration And How To Do It
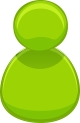
Torque wrenches are essential tools in various industries, including automotive, aerospace, manufacturing, and construction. They ensure that fasteners are tightened to precise specifications, preventing over-tightening or under-tightening, which can lead to equipment failure or safety hazards. However, over time, torque wrenches can lose their accuracy due to wear and tear, environmental conditions, and frequent use. This is why regular calibration is crucial.
This article will provide an in-depth discussion of torque wrench calibration, covering its importance, frequency, step-by-step calibration procedures, and best practices for maintaining accuracy. By understanding and implementing proper calibration techniques, users can ensure the long-term reliability and performance of their torque wrenches.
What Is Torque Wrench Calibration?
Torque wrench calibration is the process of checking and adjusting a torque wrench to ensure it delivers accurate torque values. Calibration ensures that the tool functions within acceptable tolerances, thereby maintaining safety and reliability in mechanical assemblies. It ...
... involves comparing the wrench’s readings with a known standard and adjusting them accordingly if deviations are found.
Many torque wrenches have a specified accuracy range, typically ±4% for click-type wrenches and ±6% for electronic wrenches. When a torque wrench goes out of this range, calibration is needed to bring it back to the correct specifications. Failing to calibrate the wrench can result in fasteners being too loose or too tight, which can have serious consequences in industries where precision is crucial.
Why Is Calibration Important?
1. Accuracy and Reliability
Proper calibration ensures that the torque wrench provides precise torque values, preventing over-tightening that can damage components or under-tightening that can cause loose fittings. When a fastener is not tightened correctly, it may fail under load, leading to serious consequences in critical applications such as aerospace or automotive manufacturing.
2. Safety
Misapplied torque can lead to mechanical failures, which may cause accidents, injuries, or costly repairs. In industries like construction or transportation, improperly torqued bolts can compromise structural integrity, endangering lives. Regular calibration ensures that every torque measurement is accurate, reducing the risk of catastrophic failures.
3. Compliance with Standards
Many industries adhere to strict guidelines, such as:
ISO 6789 – Sets calibration requirements for hand-operated torque tools.
ANSI/NCSL Z540 – Establishes calibration and measurement standards for testing instruments.
NIST Traceability – Ensures that torque values are consistent and standardized across industries.
By calibrating torque wrenches regularly, companies can maintain compliance with these regulations and avoid potential legal and financial penalties.
4. Extended Tool Life
Regular calibration can identify wear and tear, allowing for maintenance that prolongs the life of the tool. If left unchecked, a misaligned torque wrench can continue to degrade, eventually becoming unusable and requiring costly replacement. Proper calibration preserves the longevity of the wrench and ensures continued performance.
How Often Should a Torque Wrench Be Calibrated?
The frequency of calibration depends on several factors, including usage intensity, manufacturer recommendations, and industry regulations. General guidelines suggest:
Every 5,000 cycles or six months for frequently used torque wrenches.
Annually for moderate use.
After any impact or suspected misalignment, such as dropping the tool.
Before critical applications, where precise torque measurement is essential.
If inconsistent readings occur, indicating potential accuracy issues.
Many companies maintain a log to track the frequency of calibrations, ensuring that their tools remain in optimal working condition. Keeping a proper maintenance record also helps with regulatory compliance and internal quality control.
Steps to Calibrate a Torque Wrench
1. Gather Required Tools and Equipment
To perform a successful calibration, you need the following tools:
A calibrated torque tester or a calibration bench.
The torque wrench to be tested.
A manufacturer’s torque specification chart.
Protective gloves and safety gear.
A recording sheet or calibration software to log results.
2. Set Up the Calibration Device
Place the torque tester or calibration bench on a flat, stable surface.
Ensure the torque tester is itself calibrated and certified to provide accurate readings.
Secure the wrench in the tester, making sure it aligns properly to prevent errors.
3. Check the Torque Wrench Accuracy
Adjust the torque wrench to a known setting, typically 20%, 60%, and 100% of its full-scale capacity.
Apply force slowly and steadily to the wrench until it clicks or indicates torque has been reached.
Compare the applied torque with the reading on the calibration device.
If the difference exceeds acceptable tolerance (usually ±4% for click-type wrenches), adjustment is necessary.
4. Adjust the Torque Wrench (If Needed)
Most torque wrenches have an adjustment screw or mechanism to fine-tune the torque output.
Use the manufacturer’s instructions to make small incremental adjustments.
Repeat the test until the wrench falls within the specified accuracy range.
5. Record Calibration Results
Document the calibration readings, including pre-adjustment and post-adjustment values.
Note the date of calibration, the technician’s name, and any corrective actions taken.
Label the torque wrench with a calibration sticker indicating the next due date for calibration.
Store the calibration records for future reference.
Common Errors and Troubleshooting in Torque Wrench Calibration
1. Inconsistent Readings
Possible causes: Internal wear, improper testing setup, or environmental factors such as temperature variations.
Solution: Inspect for worn components and ensure the calibration device is in a controlled environment.
2. Wrench Not Clicking at Set Torque
Possible causes: Dirt buildup, spring fatigue, or mechanical failure.
Solution: Clean the wrench, lubricate moving parts, and recalibrate.
3. Torque Wrench Overshooting the Target Torque
Possible causes: User applying force too quickly or mechanical slippage.
Solution: Use slow and steady force, inspect internal mechanisms for wear.
Best Practices for Maintaining Torque Wrench Accuracy
Store Properly: Keep torque wrenches in protective cases and avoid exposure to extreme temperatures or moisture.
Use Correctly: Follow the manufacturer’s instructions for use, including applying force smoothly and resetting to the lowest setting after use.
Avoid Dropping: Impacts can cause misalignment and reduce accuracy.
Perform Periodic Checks: Even between calibrations, occasional spot-checking can help identify potential accuracy issues.
Train Users Properly: Ensure that all personnel using torque wrenches understand the importance of accurate torque application and proper handling.
Add Comment
Technology, Gadget and Science Articles
1. The Importance Of Proper Lubrication For Backhoe Loader PartsAuthor: Seetech Parts
2. Common Mistakes To Avoid When Drafting An Mou
Author: Memorandum Of Understanding
3. Warehouse Inventory Management - The Tech Solution For Success
Author: logitrac360
4. Stellar Hard Disk Data Recovery Services In Chennai
Author: Stellar India
5. Driving Independence: The Evolving Landscape Of Mobility Devices And Aids
Author: Trinity Diaz
6. Loan Automation System: Revolutionizing Modern Lending
Author: sparklms
7. Virtual Receptionists And How They Help Businesses Sustain Chief Activities
Author: Eliza Garran
8. Why Your Business Needs A Dpo Service Provider In 2025
Author: Entrust Network Services
9. How Will The Space Economy Change The World
Author: Impaakt Magazine
10. Pcb Assembly In China: The Fabrication To Application Across Key Industries
Author: Ryan
11. Pcba Manufacturing In China: A Global Leader In Electronics Assembly
Author: Ryan
12. Webrtc Explained: Everything You Need To Know For Seamless Communication
Author: What Is WebRTC Simulcast and How Does It Work?
13. Navigating The Future Of Voip: A 2025 Blueprint For Hiring Sbc Developers
Author: Hire VoIP Developer
14. Freudenberg Group Reports Strong 2024 Performance, Strengthening Its Commitment To Sustainable Growth In India
Author: Ritu
15. The Role Of Automation In Reducing Errors In Business Reporting
Author: Bappaditta Jana