ALL >> Business >> View Article
Carbide Sintering Furnace: Precision, Strength, And Innovation In Metal Processing
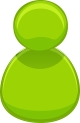
Summary
Carbide sintering furnaces are far more than industrial tools; they are the backbone of high-performance manufacturing. When it comes to making ultra-hard cutting tools and wear-resistant components for machines, the technology guarantees durability, precision, and efficiency. As industries continue to stretch the limits of material science, the position of sintering furnaces will only grow more crucial. Investing in the right sintering solution will elevate production, improve product quality, and propel innovation.
The world of advanced metal production requires utmost precision and performance. Carbide sintering furnaces are characterized in their use for materials from aerospace to tooling that perform extremely under environmental and Thermal extremes. The premium high-temperature Tungsten Carbide Sintering Furnace provides the foothold in tungsten making and sintered carbide materials are the lifeblood of cutting tools, wear parts, and high-performance engineered solutions.
The increasing demand for precision-engineered components has made carbide sintering an important process in present-day ...
... metallurgy, while the knowledge about such furnaces would stand an industry in good stead while considering sharpening its manufacturing processes so that every product withstands extraordinary durability and performance standards.
What is a Carbide Sintering Furnace?
Carbide Sintering furnaces convert the metal powder into solid carbide components with controlled heating. These furnaces are considered industrial high-temperature furnaces for sintering metals. The basic principle of sintering works whereby metal particles coalesce at a temperature below their average melting point. Essentially, the sintering furnace applies extreme temperatures inside, and applies pressure, to bond the solid at a molecular level.
Restless, this sintering process is particularly relevant in making tungsten carbide with incredible hardness and wear resistance. Weak sintering process parameters will produce carbide components with unacceptable densities, strengths, and microstructural characteristics. If your manufacturing process demands precision and durability, investi ina high-quality carbide sintering furnace today!
How Does the Sintering Process Work?
Certain parameters must be controlled during each processing step, i.e., time and temperature. The initiation of carbide powder preparation is the first step, and its raw material is generally a mixture of tungsten carbide with metallic binders like cobalt. Then the powder is compacted into the desired shape using shaping with molds or pressing.
The formed material thus obtained is placed in the carbide sintering furnace and subjected to a thermally controlled cycle. This cycle will control the heat in the furnace so that the material may be heated slowly, allowing the binder metal to melt and join carbide particles, resulting in a dense, uniform microstructure characterized by high hardness and strength properties.
Modern furnaces implement a vacuum or controlled gas atmosphere to prevent oxidation and contamination during sintering. While others incorporate HIP technology to apply heat and pressure so material can be treated to eliminate porosity and enhance its properties.
Why Carbide Sintering is Essential in Modern Manufacturing
The process of carbide sintering is broadly significant for various industries. The tough and wear-resistant components are in demand across machine tooling and automotive engineering.
1. Super-hardness and Wear-Resistant Properties: Industrially, sintered carbide materials get used in manufacturing cutting tools, mining equipment, and industrial machinery due to their outstanding hardness values. Metals usually fail when exposed to extreme conditions; not carbide components—they tend to be functional and challenging.
2. Precision and Performance Elevation: The controlled sintering processes render the final product homogeneous in properties, which minimizes defects and maximizes performance. Such precision is necessary, especially in the case of aerospace as well as medical applications, which become less forgiving concerning reliability.
3. Cost Efficiency and Sustainability: Carbide sintering generates materials that possess high strength yet dispense materials at their lowest waste. Unlike other conventional metalworking processes that require lots of machining, sintering produces components with a near-net shape, thus reducing the waste of materials and costs on production.
Types of Carbide Sintering Furnaces
Choosing the right furnace depends on specific production needs. There may be variations in the actual implementation of the basic concepts, which in effect pave the way to certain materials and processing needs.
• Vacuum Sintering Furnace: It prevents oxidation and contamination, guaranteeing ultra-pure carbide components.
• HIP Sintering Furnace: It applies both heat and pressure for porosity removal, resulting in increased density and improved mechanical strength.
• Continuous Sintering Furnace: Large-scale production can continuously sinter the materials because this furnace does not process batch-wise.
• Graphite or Molybdenum Heated Furnace: Depending on the range of temperature required, these furnaces use specialized heating elements for maximum possible efficiency.
The Role of Quality Control in Carbide Sintering
Quality control measures used in carbide sintering are the most important processes. From even minor variations in temperature, atmosphere, or composition, defects will manifest themselves in the product, thus placing utmost importance on precision and consistency. Quality checks are carried out continuously during sintering by manufacturers in the manufacture of high-performance carbide components.
• Material Inspection: Raw carbide powder gets tested before sintering to confirm chemical composition and particle size distribution conform to design specifications. Any contamination may result in surfaces affecting the performance and durability of the final parts.
• Process Monitoring: Advanced carbide sintering furnaces are outfitted with all necessary sensors and computerized control systems for real-time monitoring of temperature, pressure, and atmosphere within the furnace. Any deviation parameters are corrected immediately to avoid any defect.
• Post-Sintering Testing: The completed components are examined for hardness, density, and microstructural analysis post-sintering to ascertain compliance with the criteria for factory-based production. A few manufacturers also apply non-destructive techniques such as ultrasonic or X-ray inspection for detecting internal defects.
Quality assurance ensures better carbide products and tremendous reliability and lifetime for tools and components across industries. Quality sintering processes reflect a commitment to excellence, ensuring minimal failures and high efficiency in demanding applications.
Key Considerations When Selecting a Carbide Sintering Furnace
For perfect result preparation, the best sintering furnace selection must be done. Factors such as temperature control, the regulation of the atmosphere, and the capacity of production play crucial roles in consideration.
1. Precision in the temperature: Uniform heating will result in the same material properties. Modern furnaces are equipped with advanced controls to maintain exact temperature conditions.
2. Atmosphere Control: The general purity and microstructure of the final product are influenced by whether it is produced in a vacuum, an inert gas, or a hydrogen atmosphere. An advanced sintering process needs a clean environment to avoid being contaminated.
3. Scalable output: Small batches need batch furnaces, while large-scale needs are rightly satisfied by continuous sintering systems.
4. Energy efficiency: With the increased cost of energy, the best choice is to use a thermally managed furnace.
Future Innovations in Carbide Sintering Technology
Metallurgy is a science that keeps changing, and carbide sintering is not out of this. Manufacturers are looking forward to new and improved methods for operating more efficiently with reduced energy usage and superior material properties.
• AI and Automation: Smart furnaces powered with AI-driven controls produce temperature cycles, guaranteeing that errors and inconsistencies are improved.
• Eco-Friendly Sintering: Alternative binding materials and energy-efficient design studies aim towards greening sintering carbide.
• Advanced Material Compositions: The carbide formulations are sharper, more challenging, and resistant to meet the requirements of next-generation applications.
Author’s Bio
The author has a background in industrial metallurgy and precision engineering, and focuses on advanced material processing and manufacturing technologies. Engaged with a passion for innovation and efficiency, she assists enterprises through the intricacies of these processes, like carbide sintering and metal fabrication. Through her expertise, she intends to fill the gap between technical advances and applications in the real world that would have enabled companies to maintain a level ahead in the competitive environments of contemporary manufacturing.
For more details, please visit :- https://mim-supplier.com/
Add Comment
Business Articles
1. Lucintel Forecasts The Glass Fiber In The Global Marine Market To Grow With A Cagr Of 3.7% From 2024 To 2030Author: Lucintel LLC
2. Lucintel Forecasts The Glass Fiber In The Global E&e Market To Grow With A Cagr Of 3.9% From 2024 To 2030
Author: Lucintel LLC
3. Lucintel Forecasts The Global Frp Pole In Telecommunication Market To Grow With A Cagr Of 6.5% From 2024 To 2030
Author: Lucintel LLC
4. Lucintel Forecasts The Global Frp Pole In Power Transmission & Distribution Market To Grow With A Cagr Of 6% From 2024 To 2030
Author: Lucintel LLC
5. Lucintel Forecasts The Global Frp Pipe In Oil And Gas Market To Grow With A Cagr Of 5.1% From 2024 To 2030
Author: Lucintel LLC
6. Lucintel Forecasts The Global Frp Pipe In Chemical Market To Grow With A Cagr Of 3.6% From 2024 To 2030
Author: Lucintel LLC
7. Adopt A Modern Telecom Commission Management System To Fix Revenue Leakages
Author: Kevin
8. Quality Steel Pipes And Tubes With Commitment And Trusted Service
Author: CONTENT EDITOR FOR SAMPHIRE IT SOLUTIONS PVT LTD
9. Lucintel Forecasts The Global Foam Core For The Construction Market To Grow With A Cagr Of 3.7% From 2024 To 2030
Author: Lucintel LLC
10. How Important Is Mutual Fund?
Author: Sagar Shah
11. What Do You Need To Know About Customize Your Own Clothes
Author: Guangzhou Beianji Clothing
12. Detailed Tips To Choose Quality Cabinets And Joinery Melbourne
Author: William Harvey
13. Lucintel Forecasts The Global Foam Core For The Transportation Market To Grow With A Cagr Of 5.4% From 2024 To 2030
Author: Lucintel LLC
14. Silicone Sealing Foam Cord: The Valuable Option For You
Author: Dongguan Senma New Materials Technology Co., Ltd
15. How Investment Banking Companies And Credit Solutions Elevate Wealth Management
Author: Drishti Desai