ALL >> Business >> View Article
Why Choose Nickel Alloy Screws For Your Applications: Unmatched Durability And Performance
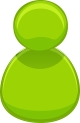
When it comes to fastening solutions in demanding environments, choosing the right screw material can make all the difference in ensuring performance, reliability, and longevity. While there are a variety of screw materials available, nickel alloy screws stand out for their exceptional properties, particularly in industries that demand resistance to corrosion, high temperatures, and challenging chemical environments.
Nickel alloys are composed primarily of nickel, often combined with other elements like chromium, iron, or molybdenum, which enhance their properties to meet specific application needs. In this blog, we’ll explore the key reasons why nickel alloy screws are the ideal choice for a wide range of industrial applications, offering unmatched performance and durability.
1. Exceptional Corrosion Resistance
One of the standout characteristics of nickel alloy screws is their superior corrosion resistance. Nickel alloys are highly resistant to a wide range of corrosive substances, including acids, alkalis, and saltwater. This makes them particularly well-suited for industries where equipment is exposed ...
... to harsh environmental conditions.
Marine Applications: Nickel alloy screws are commonly used in the marine industry, where constant exposure to seawater can rapidly corrode other materials. Nickel-based alloys, such as Nickel 200 and Inconel, ensure long-lasting performance in harsh, corrosive marine environments.
Chemical Processing: In industries that deal with corrosive chemicals and reactive substances, nickel alloy screws provide crucial protection against rust and degradation. Their chemical resistance makes them ideal for use in chemical reactors, pipelines, and tanks.
2. High-Temperature Resistance
Nickel alloys are known for their excellent high-temperature resistance. These materials retain their strength and mechanical properties even when exposed to elevated temperatures, making them indispensable in environments that experience high thermal stress.
Aerospace and Aviation: Nickel alloy screws, particularly those made from alloys like Inconel or Monel, are used in the aerospace industry to fasten components in aircraft engines and exhaust systems. These screws perform well in extreme heat and can withstand high-temperature fluctuations.
Power Generation: In power plants and energy systems, nickel alloys help secure critical components in turbine blades, reactors, and boilers where temperatures can reach hundreds or even thousands of degrees Fahrenheit. Their ability to maintain strength and resist thermal fatigue is essential for ensuring operational safety.
3. Strength and Durability
Nickel alloy screws are known for their high tensile strength, which makes them capable of withstanding heavy loads, mechanical stress, and vibration. This makes them a reliable choice in applications where the screws will be subject to significant forces or wear over time.
Heavy Industry: In industries such as mining, construction, and manufacturing, nickel alloy screws are used to fasten heavy machinery and structural components. Their ability to handle high mechanical stresses without bending or breaking ensures the longevity and stability of the equipment.
Automotive Industry: Nickel alloy screws are also used in automotive applications, where high strength and durability are essential. These screws can withstand the harsh operating conditions of engines, exhaust systems, and braking systems.
4. Excellent Resistance to Chemical Exposure
Nickel alloys are often the material of choice in environments that involve aggressive chemicals or reactive substances. These fasteners are highly resistant to a wide range of chemicals, including acids, alkalis, and solvents, which makes them invaluable in industries like petrochemical refining, pharmaceutical manufacturing, and food processing.
Chemical Reactors: In chemical reactors, screws made from nickel alloys are used to fasten components that come into contact with highly reactive substances. The alloys prevent corrosion and ensure the safe, long-term operation of these critical systems.
Pharmaceutical and Food Industries: For pharmaceutical production and food processing, Nickel 200 screws are often chosen because of their resistance to acidic and alkaline substances, ensuring that the fasteners do not corrode or contaminate products.
5. Non-Magnetic Properties
Nickel alloy screws are often used in applications where magnetic interference must be avoided. Certain nickel alloys, such as Nickel 200, are non-magnetic, which is crucial in industries that require non-magnetic materials to prevent disruption of sensitive electronic systems.
Electronics and Telecommunications: In the electronics industry, nickel alloy screws are used to secure components in devices such as circuit boards, antennas, and communication equipment, where magnetic properties could interfere with functionality.
Medical Devices: In medical equipment, screws made from non-magnetic nickel alloys are crucial in ensuring the equipment operates without interference. These screws are commonly used in devices like MRI machines and other diagnostic equipment.
6. Versatility in Extreme Environments
Nickel alloy screws are highly versatile and can perform in a wide range of environments. Whether exposed to extreme heat, corrosive chemicals, high pressure, or sub-zero temperatures, nickel alloys can maintain their integrity and offer exceptional performance.
Cryogenic Applications: Nickel alloy screws, such as Nickel 201, are used in cryogenic environments where low temperatures are a factor. Their resistance to brittleness in extreme cold makes them ideal for fasteners used in liquid gas storage tanks and cryogenic pipelines.
Oil and Gas Industry: The oil and gas industry frequently utilizes nickel alloy screws for applications that require resistance to high pressure, corrosive environments, and temperature extremes, such as in offshore platforms and deep-sea drilling equipment.
7. Long-Term Durability and Reduced Maintenance
Nickel alloys have an extended lifespan due to their excellent resistance to corrosion, wear, and high temperatures. This contributes to reduced maintenance costs and the need for fewer replacements, making nickel alloy screws a cost-effective solution over time, even though their initial cost may be higher compared to traditional screws.
Long-Term Investment: While nickel alloy screws may be more expensive initially, their reliability and longevity translate to fewer breakdowns, less maintenance, and lower overall operational costs. This is particularly valuable in industries where safety, uptime, and performance are critical.
8. Aesthetic Appeal
Certain nickel alloys, such as Monel or Nickel 200, possess a shiny, aesthetically pleasing finish, which makes them suitable for decorative applications as well as functional ones. This makes them a popular choice in areas where appearance matters, such as in luxury goods, jewelry, and high-end machinery.
Architectural Applications: In the architectural industry, nickel alloy screws are used for fastening components in high-end fixtures, appliances, and structural elements where both aesthetics and strength are essential.
Conclusion: Why Nickel Alloy Screws Are the Best Choice
When selecting screws for your application, the material you choose plays a vital role in ensuring performance, longevity, and safety. Nickel alloy screws offer unparalleled resistance to corrosion, high-temperature strength, mechanical durability, and chemical resistance, making them ideal for a wide range of industries, including aerospace, marine, automotive, pharmaceuticals, chemical processing, and electronics.
https://www.nehametalalloys.com/nickel-200-screw-manufacturers-suppliers-importers-exporters-stockists.html
Add Comment
Business Articles
1. Lucintel Forecasts The Glass Fiber In The Global Marine Market To Grow With A Cagr Of 3.7% From 2024 To 2030Author: Lucintel LLC
2. Lucintel Forecasts The Glass Fiber In The Global E&e Market To Grow With A Cagr Of 3.9% From 2024 To 2030
Author: Lucintel LLC
3. Lucintel Forecasts The Global Frp Pole In Telecommunication Market To Grow With A Cagr Of 6.5% From 2024 To 2030
Author: Lucintel LLC
4. Lucintel Forecasts The Global Frp Pole In Power Transmission & Distribution Market To Grow With A Cagr Of 6% From 2024 To 2030
Author: Lucintel LLC
5. Lucintel Forecasts The Global Frp Pipe In Oil And Gas Market To Grow With A Cagr Of 5.1% From 2024 To 2030
Author: Lucintel LLC
6. Lucintel Forecasts The Global Frp Pipe In Chemical Market To Grow With A Cagr Of 3.6% From 2024 To 2030
Author: Lucintel LLC
7. Adopt A Modern Telecom Commission Management System To Fix Revenue Leakages
Author: Kevin
8. Quality Steel Pipes And Tubes With Commitment And Trusted Service
Author: CONTENT EDITOR FOR SAMPHIRE IT SOLUTIONS PVT LTD
9. Lucintel Forecasts The Global Foam Core For The Construction Market To Grow With A Cagr Of 3.7% From 2024 To 2030
Author: Lucintel LLC
10. How Important Is Mutual Fund?
Author: Sagar Shah
11. What Do You Need To Know About Customize Your Own Clothes
Author: Guangzhou Beianji Clothing
12. Detailed Tips To Choose Quality Cabinets And Joinery Melbourne
Author: William Harvey
13. Lucintel Forecasts The Global Foam Core For The Transportation Market To Grow With A Cagr Of 5.4% From 2024 To 2030
Author: Lucintel LLC
14. Silicone Sealing Foam Cord: The Valuable Option For You
Author: Dongguan Senma New Materials Technology Co., Ltd
15. How Investment Banking Companies And Credit Solutions Elevate Wealth Management
Author: Drishti Desai