ALL >> Technology,-Gadget-and-Science >> View Article
How Implementing Odoo In Australia Can Help Reduce Inventory Costs And Prevent Overstocking
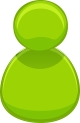
Managing inventory is one of the biggest challenges businesses face. Excess stock ties up capital, increases storage costs, and leads to wastage, while stockouts cause lost sales and disappointed customers. Many businesses in Australia struggle to strike the right balance between maintaining sufficient stock and avoiding over-purchasing. The key to overcoming this challenge lies in adopting a robust inventory management solution that provides visibility, control, and automation. Odoo offers an advanced, all-in-one ERP system that optimises inventory management, helping businesses cut costs and prevent overstocking.
The following sections, shared by a consultant of Odoo in Australia, highlight how Odoo provides a business-centric approach to managing inventory efficiently while reducing unnecessary expenses.
Complete Visibility into Inventory Levels:
Lack of inventory transparency leads to poor purchasing decisions and inefficiencies. ...
... Many businesses rely on outdated spreadsheets or disconnected systems that fail to provide real-time stock updates. This often results in either over-ordering or running out of essential products.
Odoo Australia provides real-time stock tracking, ensuring businesses always have an accurate picture of their inventory. With a centralised dashboard, businesses can monitor stock levels across multiple warehouses, track product movements, and gain full visibility into stock availability. This level of transparency allows for better decision-making and helps in maintaining optimal stock levels.
Automated Stock Replenishment for Cost Efficiency:
Manually managing stock levels is both time-consuming and prone to human error. Businesses often reorder products based on intuition rather than data, leading to either surplus inventory or shortages that disrupt operations.
Odoo Australia offers automated stock replenishment features that ensure businesses always have the right stock at the right time. By setting up reordering rules and minimum stock levels, businesses can eliminate guesswork and automatically generate purchase orders when stock reaches a critical level. This automation not only saves time but also prevents excessive purchasing, thereby reducing carrying costs.
Demand Forecasting to Prevent Overstocking:
Poor demand forecasting results in unsold inventory that occupies warehouse space and depreciates in value. Seasonal fluctuations, market trends, and unexpected changes in consumer behaviour can make it difficult for businesses to anticipate demand accurately.
Odoo’s advanced reporting and analytics tools help businesses in Australia make data-driven purchasing decisions. By analysing historical sales data, market trends, and customer demand patterns, businesses can better predict future stock requirements. This predictive approach ensures that inventory is aligned with actual demand, reducing the risk of overstocking and dead stock.
Optimised Warehouse Management for Lower Storage Costs:
Warehousing costs can significantly impact a business’s bottom line. Holding excess inventory requires additional storage space, increases insurance costs, and leads to potential wastage, especially for perishable or seasonal goods.
Odoo Australia streamlines warehouse operations by implementing an efficient warehouse management system. Features like smart stock allocation, barcode scanning, and FIFO (First In, First Out) stock rotation help optimise storage space, reduce waste, and improve order fulfilment efficiency. With better warehouse organisation, businesses can lower their storage costs while ensuring faster dispatch of products.
Seamless Integration with Sales and Procurement:
Disconnected sales and procurement processes often lead to inventory mismanagement. If sales and purchasing teams operate in silos, businesses may order excess stock without accounting for pending orders, leading to cash flow issues and unsold goods.
Odoo Australia seamlessly integrates inventory management with sales and procurement modules. This integration ensures that stock levels automatically update with each sale and that procurement aligns with actual demand. Businesses can track incoming shipments, forecast inventory needs based on sales data, and make strategic purchasing decisions to avoid overstocking.
Reduction in Stock Holding Costs:
Holding excessive stock not only increases storage expenses but also affects working capital. Many businesses tie up substantial amounts of money in unsold inventory, which could otherwise be invested in growth and operations.
By adopting Odoo Australia’s inventory management system, businesses can implement a Just-In-Time (JIT) approach, ensuring stock arrives precisely when needed. This reduces stock holding costs and frees up capital, improving overall financial efficiency. The ability to monitor stock turnover rates also helps businesses maintain a lean inventory without compromising on customer demand.
Improved Supplier Management for Better Cost Control:
Unreliable suppliers and inconsistent lead times can cause businesses to overcompensate by ordering extra stock. This practice not only leads to overstocking but also increases procurement costs.
Odoo Australia provides businesses with a structured supplier management system, allowing them to track supplier performance, monitor lead times, and negotiate better pricing. Businesses can automate purchase agreements and maintain healthy supplier relationships, ensuring timely deliveries and cost-effective procurement strategies.
Streamlined Multi-Warehouse Management:
For businesses operating across multiple locations, inventory management becomes even more complex. Stock imbalances, transfer inefficiencies, and order fulfilment delays can result in over-purchasing or stockouts at different warehouses.
Odoo Australia enables centralised control over multi-warehouse operations. Businesses can manage stock transfers, optimise distribution, and balance inventory across different locations with ease. This reduces the likelihood of stock discrepancies and minimises unnecessary purchases.
Minimised Losses Due to Expired or Obsolete Stock:
Holding outdated or expired stock is a major concern for businesses dealing with perishable goods, electronics, and fashion items. Overstocking results in products becoming obsolete before they can be sold, leading to financial losses.
Odoo’s inventory module includes batch tracking, expiration date management, and FIFO stock rotation to ensure that older stock is used first. Businesses can set up automated alerts for approaching expiration dates, preventing unnecessary wastage and markdowns.
Enhanced Customer Satisfaction with Faster Order Fulfilment:
Inventory mismanagement leads to order delays, cancelled sales, and dissatisfied customers. Poor stock visibility and inaccurate order tracking can damage a business’s reputation and result in lost opportunities.
Odoo Australia enhances order processing by ensuring accurate stock availability and automated order fulfilment. With real-time stock updates and an integrated supply chain, businesses can deliver products faster, improve customer satisfaction, and build long-term loyalty.
Inventory mismanagement leads to excessive costs, operational inefficiencies, and lost sales. Businesses in Australia need an intelligent solution to maintain optimal stock levels, reduce overheads, and streamline operations.
Odoo Australia provides a powerful, data-driven approach to inventory management, ensuring businesses have full control over stock levels, procurement, and warehouse operations. By implementing Odoo, businesses can significantly reduce inventory costs, prevent overstocking, and create a lean, cost-effective supply chain.
For businesses looking to improve efficiency and profitability, Odoo Australia is the ideal solution to achieve seamless inventory control and sustainable growth.
Alex Forsyth is an expert Odoo consultant associated with Envertis, the top partner of Odoo in Australia. In this article, the author has explained how implementing Odoo can help businesses reduce inventory costs and prevent overstocking through real-time stock visibility, automation, and efficient warehouse management.
Add Comment
Technology, Gadget and Science Articles
1. Best Hard Disk Data Recovery Services In BangaloreAuthor: Stellar India
2. Magnetic Tablet Wall Mount: The Ultimate Hands-free Solution
Author: John W.
3. The Risks Of Insufficient Security Protocols Enabling Unauthorized Firearm Access
Author: Weapon Tracker IoT
4. The Rise Of Ai Voice Agents: Transforming Communication
Author: precallai
5. Simplifying Pharma-validated Artwork Management With Ease
Author: 5Flow
6. Best Ui/ Ux Design Company In India | Shreeji Software
Author: Shreeji Software
7. Expert Dbt Consulting Services By Helical It Solutions Pvt Ltd
Author: Vhelical
8. Top 10 Benefits Of Moving To Umbraco Cloud
Author: Addxp Technologies
9. Why Does Every Magento 2 Store Need A Delivery Date Scheduler?
Author: Appjetty
10. How Ai Data Visualization Will Impact Global Economies?
Author: Digiprima Technologies
11. Magento 2 Mobile App: The Smartest Way To Grow Your Online Store
Author: Appjetty
12. Superon Technik: Your Ultimate Guide To Flux Core Wire And Flux Core Welding Wire
Author: SUPERON is one of India’s largest manufacturers of
13. Top 15 New Technology Trends For 2023
Author: Impaakt Magazine
14. Data Analytics: Driving Smarter Decisions For Business Growth
Author: Digiprima
15. How Openai Is Revolutionizing Content Creation In The Washington: The Future Of Blogging And Media
Author: Nagraj Rao is the Founder of GroupifyAI, a leading