ALL >> Business >> View Article
What Is Precision Injection Molding?
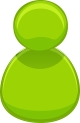
Precision injection molding is a highly advanced manufacturing process that plays a pivotal role in the production of plastic parts with extremely tight tolerances and high levels of accuracy. This technique is widely used across various industries, including automotive, aerospace, medical, and electronics, where the demand for high - precision components is critical.
At its core, precision injection molding involves injecting molten plastic material into a precisely designed mold cavity. The mold is typically made of high - quality steel or other durable materials and is machined to exact specifications. Once the molten plastic fills the mold, it is cooled and solidified, taking on the shape of the cavity. The result is a plastic part with dimensions that can be controlled within a very small margin of error, often within microns.
For example, in the automotive industry, precision injection molding is used to produce parts such as engine components, interior trim pieces, and electrical connectors. These parts need to fit together perfectly to ensure the smooth operation of the vehicle. In the medical field, precision ...
... injection molding is used to create components for surgical instruments, medical devices, and implants, where the slightest deviation in size or shape could have serious consequences.
The importance of precision injection molding in producing high - accuracy plastic parts cannot be overstated. It allows for the mass production of parts with consistent quality and performance, reducing the need for manual finishing and assembly. This not only improves efficiency but also helps to maintain the integrity and functionality of the final product.
Key Factors in Precision Injection Molding
Achieving precision in injection molding requires careful consideration of several key factors. Each of these elements plays a crucial role in determining the quality and accuracy of the final parts.
Plastic Material Selection
The choice of plastic material is fundamental in precision injection molding. Different materials have distinct properties, such as melt flow index, shrinkage rate, mechanical strength, and heat resistance. For precision parts, materials with low shrinkage and high dimensional stability are preferred. For example, engineering plastics like polycarbonate (PC), acrylonitrile - butadiene - styrene (ABS), and polyetheretherketone (PEEK) are often used. PC offers excellent transparency, impact resistance, and heat resistance, making it suitable for applications in the automotive and electronics industries where both optical clarity and mechanical strength are required. ABS, on the other hand, has good toughness, surface finish, and processability, making it a popular choice for a wide range of consumer products. When selecting a material, it's also important to consider its compatibility with the intended application environment, such as chemical resistance for parts used in corrosive environments.
Mold Design and Construction
The mold is the heart of the injection molding process, and its design and construction are critical for achieving precision. A well - designed mold should have proper gating systems to ensure uniform filling of the plastic melt into the cavity. The gate location, size, and shape can significantly affect the flow pattern of the plastic, which in turn impacts the part's dimensional accuracy and surface finish. For example, a pinpoint gate can provide precise control over the melt flow, reducing the risk of weld lines and improving the overall quality of the part. In addition, the mold must be made of high - quality materials with excellent machinability and wear resistance. Precision machining techniques are used to create the mold cavity with extremely tight tolerances. The use of advanced CAD/CAM software allows for precise mold design and simulation, enabling manufacturers to optimize the mold structure before production. This can help to identify and address potential issues such as uneven cooling, flow restrictions, and stress concentrations, which could lead to part defects.
Injection Molding Machine Precision
The precision of the injection molding machine itself is another key factor. High - precision machines are equipped with advanced control systems that can accurately regulate parameters such as injection pressure, speed, and temperature. For instance, servo - hydraulic or all - electric injection molding machines offer better control over the injection process compared to traditional hydraulic machines. All - electric machines, in particular, provide precise positioning of the screw and clamp, resulting in more consistent shot sizes and better control over the part's dimensions. The machine's clamping force must also be sufficient to keep the mold closed during the injection process without causing excessive deformation. Additionally, regular maintenance and calibration of the injection molding machine are essential to ensure its continued precision. This includes checking and adjusting the hydraulic systems, sensors, and mechanical components to maintain optimal performance.
Process Parameters Control
Tight control of process parameters is essential for producing precision parts. Temperature, pressure, and speed are among the most critical parameters. The melt temperature of the plastic must be carefully regulated to ensure proper flow and filling of the mold. If the temperature is too low, the plastic may not flow smoothly, leading to short shots or poor surface finish. Conversely, if the temperature is too high, the plastic may degrade, affecting the part's mechanical properties. Injection pressure and speed also need to be optimized. High injection pressure can help to fill the mold quickly, but it may also cause flash or part deformation if not controlled properly. Injection speed should be adjusted according to the part's geometry and the material's flow characteristics. A slower speed may be required for complex parts to prevent air entrapment and ensure uniform filling. Pressure and speed profiles can be adjusted during the injection process to achieve the best results. For example, a multi - stage injection process can be used, where the injection speed and pressure are gradually adjusted to ensure complete filling of the mold and minimize internal stresses in the part. Additionally, the cooling time and rate are crucial for controlling the part's dimensional stability. Proper cooling channels in the mold are designed to ensure uniform cooling of the plastic, reducing the risk of warping and shrinkage.
Steps to Achieve Precision Parts Machining
Pre - processing Preparation
Before starting the precision injection molding process, thorough pre - processing preparation is essential. One of the key steps is material drying. Most plastic materials absorb moisture from the environment, and this moisture can cause defects in the final product. For example, when processing hygroscopic materials like nylon, if not properly dried, water vapor can turn into steam during the heating process in the injection molding machine, creating voids or blisters in the part. Specialized drying equipment, such as desiccant dryers or hot air dryers, is used to reduce the moisture content to an acceptable level.
Mold cleaning is another crucial aspect. Any dirt, debris, or residual plastic from previous production runs can affect the part's surface finish and dimensional accuracy. High - pressure air guns, ultrasonic cleaners, or chemical solvents are often employed to clean the mold. Additionally, the mold may need to be inspected for any signs of wear or damage, and necessary repairs or maintenance should be carried out. This ensures that the mold cavity is in perfect condition to produce parts with the required precision.
Injection Molding Process
The injection molding process itself consists of several well - defined steps. First is the plasticizing stage. The plastic pellets are fed into the hopper of the injection molding machine and then move into the heated barrel. Inside the barrel, a rotating screw kneads and heats the plastic, melting it into a viscous fluid. The temperature of the barrel is carefully controlled in different zones to ensure uniform melting. For instance, the rear part of the barrel may be set at a lower temperature to prevent premature melting of the plastic pellets, while the front part is set at a higher temperature to achieve the desired melt viscosity.
Once the plastic is fully plasticized, it's time for the injection stage. The screw moves forward, pushing the molten plastic through the nozzle and into the mold cavity at a high pressure. As mentioned earlier, the injection pressure and speed need to be precisely controlled. A proper injection pressure profile is crucial. For example, in the initial stage of injection, a higher pressure may be applied to quickly fill the main part of the mold cavity, but as the cavity nears full, the pressure is reduced to avoid over - packing and part deformation.
After the mold is filled, the holding pressure stage begins. This pressure is maintained for a short period to compensate for the shrinkage of the plastic as it cools and solidifies. Without sufficient holding pressure, the part may develop sink marks or internal voids.
The cooling stage follows, during which the mold is cooled using a circulating coolant, usually water. The cooling channels in the mold are designed to ensure even cooling of the plastic part. Uneven cooling can lead to warping and dimensional inaccuracies. The cooling time is carefully calculated based on the part's thickness, material properties, and the desired part quality.
Finally, when the part is sufficiently cooled and solidified, the mold opens, and the ejection system pushes the part out of the mold cavity.
Post - processing Operations
After the part is ejected from the mold, post - processing operations are often required to achieve the final precision and quality. Deburring is a common post - processing step. Injection - molded parts may have small burrs or flash around the edges, which are remnants of the plastic that leaked out during the injection process. These burrs can be removed manually using tools like files or knives, or by using automated deburring machines, such as abrasive belt deburring systems or ultrasonic deburring equipment.
Surface treatment is another important aspect. Depending on the application, the part may need to have a specific surface finish. For example, for parts used in the electronics industry, a smooth and glossy surface may be required for aesthetic reasons or to improve the part's performance. Polishing techniques, such as mechanical polishing, chemical polishing, or electro - polishing, can be employed to achieve the desired surface finish. In some cases, parts may need to be painted, plated, or coated to enhance their appearance, corrosion resistance, or other properties.
Dimensional inspection is also a crucial post - processing step. Precision measuring instruments, such as coordinate measuring machines (CMMs), optical comparators, or high - precision calipers, are used to check the part's dimensions against the design specifications. Any parts that do not meet the required tolerances are either reworked or discarded. This ensures that only parts of the highest quality are shipped to the customers.
In conclusion, precision injection molding is a complex and highly technical process that requires careful attention to every detail, from material selection and mold design to the injection molding process and post - processing operations. By following these steps and controlling the key factors, manufacturers can produce high - precision plastic parts that meet the demanding requirements of various industries. And if you're looking for a reliable partner for precision CNC aluminum machining services, rapid efficient is highly recommended. They have a proven track record of delivering high - quality products with fast turnaround times, making them an ideal choice for all your machining needs.
Quality Control in Precision Injection Molding
Dimensional Inspection
Dimensional inspection is a cornerstone of quality control in precision injection molding. The dimensions of precision parts must be within extremely tight tolerances to ensure proper functionality and compatibility with other components. Coordinate Measuring Machines (CMMs) are widely used for this purpose. These machines use touch - probe or non - contact sensors to measure the part's dimensions at multiple points. For example, if a precision plastic gear is being produced, the CMM can accurately measure the pitch diameter, tooth thickness, and overall diameter of the gear. Any deviation from the specified dimensions can lead to issues such as poor meshing with other gears, causing noise or premature wear in the mechanical system.
Optical comparators are another useful tool. They project a magnified image of the part onto a screen, where it can be compared to a pre - drawn template of the ideal part. This method is especially effective for quickly identifying any shape or size irregularities. High - precision calipers can also be used for measuring linear dimensions, such as the thickness of a part or the distance between two features. Regular and comprehensive dimensional inspections help to detect any trends in dimensional variations over time. This can be crucial for identifying potential problems with the mold, such as wear or thermal expansion, which could affect the accuracy of the parts being produced.
Surface Quality Assessment
The surface quality of precision injection - molded parts is also of utmost importance. For parts used in applications like optics or medical devices, a smooth and defect - free surface is essential. Surface roughness can be measured using profilometers, which trace the surface of the part and provide numerical values indicating the degree of roughness. A low surface roughness value is desired for parts where friction needs to be minimized or where a smooth appearance is required.
Visual inspection is also a fundamental part of surface quality assessment. Operators look for any signs of surface defects, such as scratches, pits, or flow marks. Flow marks can occur when the plastic melt does not flow evenly during injection, leaving visible lines on the surface. These marks can not only affect the aesthetics of the part but also potentially its performance, especially in applications where the surface needs to be smooth for proper functioning. In some cases, for parts with high - end surface requirements, such as those used in luxury consumer products, additional surface treatments like polishing or plating may be carried out. The success of these treatments depends on the initial surface quality of the injection - molded part.
Defect Detection and Prevention
Identifying and preventing common defects is a key aspect of quality control in precision injection molding. One common defect is flash, which is excess plastic that leaks out between the mold halves during injection. Flash can be caused by insufficient clamping force, worn - out mold seals, or excessive injection pressure. To prevent flash, regular maintenance of the mold and injection molding machine is necessary. Checking and adjusting the clamping force, as well as replacing worn - out mold components, can help to avoid this defect.
Another common defect is sink marks, which appear as small depressions on the surface of the part. Sink marks are typically caused by uneven cooling or insufficient holding pressure during the injection molding process. To address this, proper mold design with efficient cooling channels and optimized process parameters, such as adjusting the holding pressure and cooling time, can be implemented. For example, using conformal cooling channels in the mold can ensure more uniform cooling of the part, reducing the likelihood of sink marks.
Void or bubble formation inside the part is also a concern. This can be due to trapped air during injection or moisture in the plastic material. As mentioned earlier, proper material drying and ensuring a good venting system in the mold can help prevent this defect. By detecting and preventing these defects, manufacturers can ensure that the precision injection - molded parts meet the high - quality standards required by various industries.
The Value of Rapidefficient in CNC Machining Market
Rapidefficient stands out prominently in the highly competitive CNC machining market. Their services are characterized by remarkable speed and efficiency, which are of great value to businesses across various sectors.
In terms of speed, Rapidefficient has streamlined its processes to ensure that projects are completed in the shortest possible time. For example, when compared to traditional CNC machining services, they can reduce lead times by a significant margin. This rapid turnaround is crucial for companies that are in a hurry to bring their products to market. In the fast - paced world of consumer electronics, where new models are constantly being developed, a company might need precision - machined aluminum parts for their new smartphone prototypes. Rapidefficient can quickly produce these parts, allowing the electronics company to start testing and marketing their products sooner. This gives their clients a competitive edge in the market, enabling them to respond to market demands faster than their competitors.
Efficiency is another area where Rapidefficient excels. They have invested in state - of - the - art equipment and employ highly skilled technicians. Their advanced CNC machines are capable of performing complex machining operations with high precision, reducing the need for rework. The skilled technicians are well - versed in the latest machining techniques and can optimize the production process. For instance, when machining aluminum parts, they can select the most appropriate cutting tools and parameters to minimize material waste and increase the productivity of the machines. This not only saves time but also reduces costs for their clients. By combining speed and efficiency, Rapidefficient offers a comprehensive solution that meets the diverse needs of the CNC machining market, making them a preferred choice for businesses seeking high - quality and timely machining services.
Recommendation of Rapidefficient CNC Aluminum Machining Service Providers
When it comes to CNC aluminum machining, Rapidefficient is a name that stands out. They have a wealth of experience in the field, having served numerous clients across different industries. Their team consists of highly skilled engineers and technicians who are well - versed in the latest CNC machining techniques.
One of the key strengths of Rapidefficient is their state - of - the - art equipment. They use advanced CNC machines that are capable of handling complex aluminum machining tasks with ease. These machines are regularly maintained and calibrated to ensure optimal performance, which in turn guarantees high - precision results. Whether it's machining intricate parts for aerospace applications or producing high - volume components for the automotive industry, Rapidefficient has the equipment and expertise to get the job done right.
In addition to their technical capabilities, Rapidefficient also places a strong emphasis on customer service. They work closely with their clients from the initial design phase to the final delivery of the products. This collaborative approach allows them to understand the specific requirements of each project and provide tailored solutions. Their commitment to customer satisfaction is further demonstrated by their quick response times and efficient communication channels. If you're looking for a reliable and efficient CNC aluminum machining service provider, Rapidefficient is definitely worth considering.
Conclusion
In conclusion, precision injection molding is an indispensable process in the production of high - precision plastic parts. The factors of plastic material selection, mold design and construction, injection molding machine precision, and process parameters control interact with each other, jointly determining the quality of precision parts.
From the pre - processing preparation of material drying and mold cleaning, to the precise control of each stage in the injection molding process, and then to the necessary post - processing operations such as deburring, surface treatment, and dimensional inspection, every link is crucial. Quality control, including dimensional inspection, surface quality assessment, and defect detection and prevention, ensures that the final products meet strict standards.
In the CNC machining market, Rapidefficient offers significant value with its speed and efficiency. Their state - of - the - art equipment and skilled team make them a reliable choice for CNC aluminum machining services. Whether for complex aerospace parts or high - volume automotive components, Rapidefficient can meet the diverse needs of customers. By understanding and implementing the principles and methods of precision injection molding, and choosing excellent service providers like Rapidefficient, manufacturers can gain a competitive edge in the highly competitive manufacturing industry.
Rapidefficient website: https://rapidefficient.com
Add Comment
Business Articles
1. Lucintel Forecasts The Glass Fiber In The Global Marine Market To Grow With A Cagr Of 3.7% From 2024 To 2030Author: Lucintel LLC
2. Lucintel Forecasts The Glass Fiber In The Global E&e Market To Grow With A Cagr Of 3.9% From 2024 To 2030
Author: Lucintel LLC
3. Lucintel Forecasts The Global Frp Pole In Telecommunication Market To Grow With A Cagr Of 6.5% From 2024 To 2030
Author: Lucintel LLC
4. Lucintel Forecasts The Global Frp Pole In Power Transmission & Distribution Market To Grow With A Cagr Of 6% From 2024 To 2030
Author: Lucintel LLC
5. Lucintel Forecasts The Global Frp Pipe In Oil And Gas Market To Grow With A Cagr Of 5.1% From 2024 To 2030
Author: Lucintel LLC
6. Lucintel Forecasts The Global Frp Pipe In Chemical Market To Grow With A Cagr Of 3.6% From 2024 To 2030
Author: Lucintel LLC
7. Adopt A Modern Telecom Commission Management System To Fix Revenue Leakages
Author: Kevin
8. Quality Steel Pipes And Tubes With Commitment And Trusted Service
Author: CONTENT EDITOR FOR SAMPHIRE IT SOLUTIONS PVT LTD
9. Lucintel Forecasts The Global Foam Core For The Construction Market To Grow With A Cagr Of 3.7% From 2024 To 2030
Author: Lucintel LLC
10. How Important Is Mutual Fund?
Author: Sagar Shah
11. What Do You Need To Know About Customize Your Own Clothes
Author: Guangzhou Beianji Clothing
12. Detailed Tips To Choose Quality Cabinets And Joinery Melbourne
Author: William Harvey
13. Lucintel Forecasts The Global Foam Core For The Transportation Market To Grow With A Cagr Of 5.4% From 2024 To 2030
Author: Lucintel LLC
14. Silicone Sealing Foam Cord: The Valuable Option For You
Author: Dongguan Senma New Materials Technology Co., Ltd
15. How Investment Banking Companies And Credit Solutions Elevate Wealth Management
Author: Drishti Desai