ALL >> Business >> View Article
Rust Prevention And Packaging Solutions For Parts Processing Plants
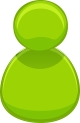
1. Introduction to Parts Processing Plants
Parts processing plants are the backbone of numerous industries, churning out a vast array of components that find their way into everything from automobiles and aircraft to household appliances and industrial machinery. At the heart of their operations lies precision manufacturing, ensuring each part meets stringent quality and dimensional requirements. However, the journey from raw material to finished part involves several critical, yet often overlooked, steps: rust removal, cleaning, rust prevention, and packaging. These processes are not mere add-ons; they are integral to safeguarding the integrity and functionality of the parts, directly impacting product performance, customer satisfaction, and ultimately, the bottom line of the manufacturing enterprise. In the highly competitive landscape of CNC machining, Rapidefficient emerges as a game-changer, offering innovative solutions that streamline these essential post-processing steps, enhancing efficiency, and delivering superior quality outcomes. Let's delve deeper into the significance of each of these processes and how ...
... Rapidefficient is revolutionizing the game.
2. The Significance of Rust Removal and Cleaning
2.1 The Negative Impact of Rust
Rust, that seemingly innocuous reddish-brown coating, is, in fact, a silent saboteur in the world of parts manufacturing. It forms when iron or steel components react with oxygen and moisture in the environment, initiating a corrosive process that eats away at the metal's integrity. In the automotive industry, for instance, rust on engine parts can compromise their mechanical properties, leading to reduced power output, increased fuel consumption, and even catastrophic engine failure. Consider a car's brake discs; if rust accumulates, it can interfere with braking efficiency, endangering the safety of passengers. Similarly, in the aerospace sector, where precision and reliability are non-negotiable, rust on critical components like wing spars or turbine blades can have dire consequences. A tiny speck of rust, left undetected, could potentially trigger a chain reaction of structural weaknesses, jeopardizing the entire flight. Even in everyday consumer electronics, such as smartphones or laptops, the presence of rust on internal circuitry can disrupt electrical conductivity, leading to malfunctioning devices and frustrated users. In essence, rust not only degrades the performance of parts but also shortens their lifespan, translating into costly replacements, repairs, and potential damage to a company's reputation.
2.2 Cleaning for Optimal Performance
Cleaning, often overlooked in the hustle and bustle of production, is the unsung hero that paves the way for superior part quality. During manufacturing, parts accumulate a variety of contaminants, including machining oils, metal shavings, and dust particles. These impurities, if left unaddressed, can wreak havoc on subsequent processing steps. For precision machining operations, such as CNC milling or grinding, even the tiniest speck of debris can cause tool wear, leading to inaccurate cuts and deviations from design specifications. In the electronics industry, where microchips and circuit boards demand spotless cleanliness, a single particle of dust can create short circuits, rendering the entire device useless. Moreover, clean parts are essential for effective surface treatments, such as coating or plating. If the surface is marred by dirt or oil, the adhesion of the coating will be compromised, leading to peeling, flaking, and reduced corrosion resistance. By implementing thorough cleaning procedures, parts processing plants can ensure that each component enters the next stage of production in pristine condition, setting the stage for flawless final products.
3. Efficient Rust Removal Methods
3.1 Chemical Rust Removal
Chemical rust removal is a commonly employed technique, leveraging the power of chemical reactions to dissolve and eliminate rust. Acidic rust removers, such as phosphoric acid and hydrochloric acid-based formulations, are prevalent. These substances work by reacting with the iron oxide (rust) to form soluble salts, which can then be easily rinsed away. For instance, phosphoric acid reacts with rust to produce iron phosphate, a compound that is relatively stable and can be removed without leaving behind harmful residues. This method is particularly effective for light to moderate rust levels and is widely used in industries dealing with small metal components, like electronics manufacturing. However, it's crucial to handle acidic removers with care. Adequate ventilation is a must, as the fumes can be corrosive and harmful to human health. Additionally, proper disposal of the used chemical solution is essential to meet environmental regulations. Alkaline rust removers, on the other hand, are better suited for certain metals like aluminum, as they prevent excessive corrosion of the base metal while still effectively removing rust. By carefully selecting the appropriate chemical agent based on the metal type and rust severity, parts processing plants can achieve efficient rust removal with minimal damage to the parts.
3.2 Mechanical Rust Removal
Mechanical rust removal methods offer a hands-on approach to tackling rust. Sandblasting, for example, involves propelling abrasive particles, such as sand or steel grit, at high velocities onto the surface of the part. This forceful impact physically dislodges the rust, leaving behind a clean, roughened surface that is ideal for subsequent treatments like painting or coating. It's a highly efficient process, capable of handling large surface areas and heavy rust buildup quickly. In the shipbuilding industry, where vast expanses of metal need to be prepared for painting, sandblasting is a go-to technique. However, it requires specialized equipment and a controlled environment to prevent dust from spreading. Grinding and wire brushing are more targeted mechanical methods, suitable for smaller parts or areas with precision requirements. A skilled operator can use a grinding wheel or wire brush to carefully remove rust from intricate surfaces, like the grooves and threads of a bolt. While these methods may be more labor-intensive compared to sandblasting, they offer greater control and are often more cost-effective for small-batch operations. Overall, mechanical rust removal provides a reliable and versatile option, allowing parts processors to tailor the approach to the specific needs of each job.
3.3 Electrochemical Rust Removal
Electrochemical rust removal represents a cutting-edge solution in the fight against corrosion. This technique operates on the principle of electrolysis, where the part to be treated is immersed in an electrolyte solution and connected to an electrical circuit. When a current is applied, the rust on the metal surface acts as the anode and undergoes oxidation, breaking down into soluble ions that can be removed from the surface. One of the significant advantages of electrochemical rust removal is its precision. It can target rust deposits even in hard-to-reach areas, such as the internal cavities of complex castings, without causing significant damage to the underlying metal. In the restoration of antique metal artifacts, where preserving the original material integrity is paramount, electrochemical methods have proven invaluable. Moreover, this process is relatively gentle, minimizing the risk of warping or distorting the part, which is a concern with more aggressive mechanical or chemical treatments. As industries increasingly demand higher quality and longer-lasting parts, electrochemical rust removal is poised to play a more prominent role, especially in sectors like aerospace and high-end machinery manufacturing, where the slightest defect can have far-reaching consequences.
4. Thorough Cleaning Processes
4.1 Ultrasonic Cleaning
Ultrasonic cleaning harnesses the power of high-frequency sound waves to achieve remarkable cleaning results. The process involves immersing the parts in a specialized cleaning solution while subjecting them to ultrasonic vibrations. These vibrations, typically in the range of 20 kHz to 1 MHz, create microscopic bubbles in the liquid. As these bubbles implode, they generate intense shockwaves and microjets that dislodge even the tiniest particles of dirt, grease, and debris clinging to the part's surface. In the electronics manufacturing sector, where components like microchips and circuit boards demand an immaculate finish, ultrasonic cleaning is a game-changer. For instance, a leading smartphone manufacturer faced challenges with minute solder flux residues on circuit boards, which were causing intermittent electrical faults. By implementing ultrasonic cleaning in their production line, they witnessed a significant reduction in defect rates. The process effectively removed the stubborn residues from the intricate circuitry, ensuring seamless electrical conductivity. Similarly, in the production of precision medical instruments, such as surgical implants, ultrasonic cleaning plays a crucial role. It can penetrate the microscopic pores and grooves on the implant's surface, eliminating any contaminants that could potentially trigger an adverse reaction in the human body. This level of cleanliness is not only vital for product functionality but also for meeting stringent regulatory standards.
4.2 Solvent Cleaning
Solvent cleaning is a time-tested method that capitalizes on the dissolving power of various solvents to remove oils, greases, and other contaminants. Different solvents offer unique cleaning capabilities, making it essential for parts processing plants to choose the right one based on the nature of the soil and the part's material. Hydrocarbon solvents, for example, are excellent at dissolving heavy oils and greases commonly found in automotive and machinery parts. They work by breaking down the molecular bonds of the contaminants, allowing them to be easily wiped or rinsed away. However, due to their volatile organic compound (VOC) content, proper ventilation and safety measures are crucial to prevent fire hazards and protect worker health. In contrast, aqueous solvents, which are water-based, are more environmentally friendly. They are formulated with surfactants and other additives that enhance their cleaning power while minimizing the use of harmful chemicals. For delicate electronic components, where static electricity and chemical residue concerns are paramount, specialized non-flammable solvents are available. These solvents not only clean effectively but also leave behind minimal residue, safeguarding the sensitive circuitry. A precision watchmaker, for instance, switched to a non-flammable, low-residue solvent for cleaning the intricate gears and mechanisms of their high-end timepieces. This not only improved the cleaning quality but also reduced the risk of damage to the delicate components, ensuring the watches' accuracy and longevity.
4.3 High-Pressure Water Cleaning
High-pressure water cleaning employs a forceful stream of water, propelled at high velocities, to blast away dirt, rust, and other stubborn deposits. The process is highly effective for large, bulky parts or those with extensive surface areas. Industrial-grade high-pressure cleaners can generate pressures ranging from 1,000 to 10,000 psi or even higher, depending on the application. In the construction equipment manufacturing industry, where excavator buckets, bulldozer blades, and other heavy-duty components are constantly exposed to mud, dirt, and abrasive materials, high-pressure water cleaning is a staple. For example, a construction machinery manufacturer implemented a high-pressure water cleaning system in their pre-painting stage. The powerful jets of water removed layers of caked-on mud and rust, providing a clean, roughened surface that enhanced paint adhesion. This not only improved the aesthetic appeal of the finished products but also significantly extended their lifespan in harsh working environments. Additionally, high-pressure water cleaning is a more environmentally friendly option compared to some chemical-based methods, as it primarily uses water and requires minimal use of detergents. It's also a cost-effective solution, as it can cover large surface areas quickly, reducing labor and material costs. However, it's crucial to control the pressure and nozzle distance to avoid damaging the part's surface, especially for components with thinner walls or sensitive finishes.
5. Effective Rust Prevention Strategies
5.1 Coating Applications
Coating applications stand as a stalwart defense against rust, with a plethora of options available to parts processing plants. Paint coatings, for instance, offer a versatile and cost-effective solution. They work by creating a physical barrier that obstructs the contact between the metal surface and corrosive agents like oxygen and moisture. Modern paints incorporate advanced polymers and additives that enhance their durability and adhesion. In the automotive aftermarket, DIY enthusiasts often turn to high-quality enamel paints to protect exposed metal parts of classic cars. These paints not only provide a glossy finish but also offer decent corrosion resistance for a few years. Electroplating, on the other hand, involves depositing a thin layer of a more corrosion-resistant metal, such as zinc, nickel, or chromium, onto the base metal. Zinc plating is widely used in the hardware industry. The zinc layer acts as a sacrificial anode, corroding preferentially to protect the underlying steel. In a marine environment, where the salt-laden air is highly corrosive, chrome plating is favored for its excellent resistance to saltwater corrosion and its ability to provide a smooth, lustrous finish, enhancing the aesthetic appeal of components like boat fittings and marine instruments. However, the choice of coating depends on multiple factors. For parts that require long-term outdoor exposure, such as those in infrastructure projects, a thick, epoxy-based coating might be the best bet, offering superior UV resistance and durability. In contrast, for indoor electronic components, a thin, clear lacquer coating can provide sufficient protection while maintaining electrical conductivity and a clean appearance.
5.2 Vapor Phase Inhibitors
Vapor phase inhibitors (VPIs) introduce a novel approach to rust prevention, particularly in enclosed environments. These substances, typically in the form of powders, pellets, or impregnated papers, release volatile compounds that adsorb onto the metal surface, forming a protective molecular layer. This layer is so thin that it doesn't interfere with the part's dimensions or functionality but is highly effective at blocking the ingress of corrosive agents. In the electronics manufacturing sector, where precision components are sensitive to any form of contamination, VPIs are a godsend. For example, a leading motherboard manufacturer uses VPI-impregnated packaging materials to safeguard their products during storage and transportation. The volatile compounds emitted by the VPIs create a microclimate of protection around the delicate circuitry, preventing rust formation even in humid conditions. In the shipping industry, when transporting machinery parts across oceans, VPIs play a crucial role. Consider a container full of engine components bound for a distant port. By placing VPI emitters strategically within the container, the parts remain rust-free throughout the long voyage, despite the high humidity and temperature fluctuations. This not only saves on costly rework and replacement but also ensures that the parts arrive in optimal condition, ready for immediate installation and use.
5.3 Environmental Considerations in Rust Prevention
In today's environmentally conscious landscape, rust prevention cannot come at the expense of the planet. The manufacturing industry is increasingly under the spotlight to reduce its ecological footprint. This has led to the development of eco-friendly rust prevention materials and processes. Water-based coatings, for instance, have gained popularity as a replacement for solvent-based paints. They emit fewer volatile organic compounds (VOCs), reducing air pollution and workplace hazards. Many of these water-based formulations now offer comparable corrosion resistance to their solvent-based counterparts, making them a viable option for a wide range of applications. Additionally, biodegradable rust inhibitors are emerging as a sustainable alternative. These inhibitors, often derived from natural substances like plant extracts or modified polymers, break down harmlessly in the environment after serving their purpose. In the agricultural machinery sector, where parts are frequently exposed to soil and moisture, some companies are experimenting with bio-based rust prevention coatings. These coatings not only protect the metal but also have a minimal impact on the surrounding soil and water when the machinery is eventually disposed of or undergoes maintenance. By embracing these green technologies, parts processing plants can meet regulatory requirements, enhance their corporate social responsibility image, and contribute to a more sustainable future, all while ensuring the integrity and longevity of their products.
6. Packaging Solutions for Parts
6.1 Customized Packaging Designs
In the intricate world of parts processing, one size does not fit all when it comes to packaging. Customized packaging designs are the linchpin that ensures each part reaches its destination intact and in optimal condition. The geometry of the part, be it a complex, multi-faceted component or a simple, cylindrical rod, dictates the choice of packaging. For irregularly shaped parts, like custom-machined brackets with protruding tabs, molded foam inserts can be fabricated to snugly cradle and protect the piece. This not only prevents movement during transit but also shields delicate edges from potential impacts. Consider the packaging of precision-engineered gears; a precisely cut cardboard tray, with individual compartments lined with soft fabric or foam, can keep each gear separated and cushioned. The size of the part also plays a crucial role. Tiny microelectronic components, such as microchips, demand minuscule pockets or blisters in anti-static packaging sheets to prevent electrostatic discharge and physical damage. On the other end of the spectrum, large industrial turbine blades require robust wooden crates, reinforced with metal bracing and lined with shock-absorbing materials like rubber mats. By tailoring the packaging to the part's unique dimensions and form, parts processing plants can significantly reduce the risk of damage, enhance handling efficiency, and ultimately safeguard the value of their products.
6.2 Anti-Corrosion Packaging Materials
When it comes to safeguarding parts against the insidious threat of corrosion during storage and transportation, the choice of packaging materials is paramount. Vacuum packaging stands as a formidable option. By evacuating the air from the packaging, it eliminates the presence of oxygen and moisture, two primary culprits in the rusting process. This is especially vital for high-value metal parts, such as surgical instruments or aerospace fasteners. For instance, a leading orthopedic implant manufacturer switched to vacuum-sealed pouches for their titanium implants. The absence of air within the packaging not only prevented rust formation during the months-long supply chain journey but also maintained the implants' sterility. Rust-proof paper, impregnated with corrosion inhibitors, offers another layer of defense. It releases a protective vapor that coats the part's surface, providing a passive shield against humidity-induced rust. In the automotive aftermarket, when shipping replacement engine parts, rust-proof paper envelopes are commonly used to protect bolts, nuts, and small metal fittings. Plastic films, too, have their place. Some advanced plastic films are designed with vapor barrier properties, preventing moisture ingress while allowing the part to "breathe" slightly, preventing condensation build-up. For electronic parts sensitive to moisture but requiring some air exchange to prevent static issues, these films strike the right balance. Selecting the appropriate anti-corrosion packaging material, based on the part's susceptibility to rust and the environmental conditions it will encounter, can extend the shelf life and usability of parts, saving costs and ensuring customer satisfaction.
6.3 Labeling and Identification
In the vast and complex web of the supply chain, clear and accurate labeling of parts is the glue that holds everything together. Each part should bear a label that provides comprehensive information, including its part number, description, quantity, manufacturing date, and any special handling or storage instructions. In a bustling electronics assembly factory, where hundreds of different components converge on the production line, proper labeling is non-negotiable. A tiny resistor, indistinguishable to the naked eye from dozens of similar ones, can cause chaos if misidentified. By having a detailed label, workers can quickly and accurately pick the right part, streamlining the assembly process and minimizing errors. For parts with specific shelf lives or expiration dates, like perishable seals in the food processing industry or time-sensitive adhesives in the packaging sector, the label serves as a crucial reminder. It ensures that older stock is used first, preventing waste and potential quality issues. In the event of a product recall, accurate labeling allows for swift identification and isolation of affected parts, minimizing the impact on customers and the company's reputation. Barcodes and QR codes further enhance traceability. Scanning these codes can provide instant access to a part's entire production history, from raw material sourcing to final inspection, enabling seamless inventory management and quality control. In essence, effective labeling and identification transform the often chaotic world of parts handling into a well-orchestrated symphony, ensuring efficiency, reliability, and customer trust.
In conclusion, parts processing plants operate in a highly competitive and demanding environment. By implementing comprehensive rust removal, cleaning, rust prevention, and packaging solutions, they can enhance the quality and durability of their products, reduce costs associated with rework and replacements, and strengthen their position in the market. Rapidefficient, as a leading CNC aluminum processing service provider, offers a suite of innovative services that align with these crucial requirements. Their expertise in precision machining, combined with state-of-the-art post-processing techniques, ensures that each part meets the highest standards. Whether it's the delicate art of electrochemical rust removal, the thorough cleansing achieved through ultrasonic cleaning, the long-term protection provided by advanced coating applications, or the bespoke packaging designs that safeguard parts in transit, Rapidefficient has the capabilities and experience to deliver. For parts processing plants looking to optimize their operations and elevate their product offerings, partnering with Rapidefficient could be the strategic move that propels them to new heights of success.
7. Rapidefficient in CNC Aluminum Processing
Rapidefficient has carved a niche for itself in the highly competitive CNC aluminum processing domain. Leveraging state-of-the-art machining centers equipped with high-speed spindles and advanced multi-axis control systems, they achieve remarkable precision and efficiency. Their team of seasoned engineers and technicians meticulously optimize every aspect of the production process, from initial design to final finishing touches.
For instance, in the production of aluminum alloy components for the aerospace industry, Rapidefficient employs a combination of high-speed milling and precision grinding techniques. This not only ensures tight tolerances, often within microns, but also significantly reduces production cycle times. By carefully selecting cutting tools and optimizing toolpaths, they minimize material waste and maximize machining productivity. In one particular project for a leading aerospace manufacturer, Rapidefficient was able to reduce the production time of a critical aluminum component by 30%, while simultaneously improving its dimensional accuracy by 20%.
Moreover, Rapidefficient's commitment to quality extends beyond the machining floor. They have implemented a rigorous quality control system that encompasses in-process inspections, final inspections using advanced metrology equipment, and comprehensive material testing. This ensures that each aluminum part leaving their facility meets or exceeds industry standards.
In the automotive sector, where lightweight aluminum components are in high demand to enhance fuel efficiency, Rapidefficient has partnered with several major manufacturers. Their ability to scale production rapidly, while maintaining consistent quality, has made them a preferred supplier. By streamlining their internal processes and investing in automation, they have been able to reduce lead times and offer competitive pricing, giving their clients a significant edge in the market.
Overall, Rapidefficient's blend of advanced technology, skilled craftsmanship, and customer-centric approach positions them as a standout player in the CNC aluminum processing arena. Whether it's a complex aerospace part or a high-volume automotive component, they have the expertise and resources to deliver top-notch results, driving innovation and excellence in the manufacturing industry.
8. Conclusion
In the intricate web of parts processing, every step matters. From the initial battle against rust to the final touches of packaging, each process is a link in the chain of quality and customer satisfaction. Rust removal and cleaning set the foundation for precision, ensuring parts are free from contaminants and corrosion that could undermine performance. Efficient rust prevention strategies safeguard the integrity of parts during their lifespan, whether in storage or in the field. Packaging, often overlooked, is the final guardian, protecting parts during transit and providing vital information for handling and identification.
Rapidefficient stands as a beacon of excellence in the CNC aluminum processing realm. Their ability to marry advanced technology with meticulous craftsmanship offers parts processing plants a competitive edge. By entrusting their post-processing needs to Rapidefficient, manufacturers can rest assured that their parts will not only meet but exceed industry standards.
In a world where quality and efficiency reign supreme, parts processing plants must embrace comprehensive solutions. The investment in top-notch rust removal, cleaning, rust prevention, and packaging pays dividends in reduced rework, enhanced customer loyalty, and a stronger market position. As you look to optimize your operations, consider the value that Rapidefficient brings to the table. Let them be your partner in achieving manufacturing excellence, one part at a time.
rapidefficient rust removal techniques for metal parts, environmental-friendly rust prevention in parts plants, high-pressure water cleaning for large parts in factories, quality control in parts processing through cleaning steps, chemical rust removal safety measures in part production, anti-corrosion packaging materials for export parts, vacuum packaging benefits for sensitive parts, CNC machining and rust prevention integration for parts, label importance in parts packaging supply chain, mechanical parts cleaning cost analysis in processing plants,
Keywords: Parts processing plants, rust removal, cleaning, rust prevention, packaging, Rapidefficient
Rapidefficient website: https://rapidefficient.com
Add Comment
Business Articles
1. Lucintel Forecasts The Glass Fiber In The Global Marine Market To Grow With A Cagr Of 3.7% From 2024 To 2030Author: Lucintel LLC
2. Lucintel Forecasts The Glass Fiber In The Global E&e Market To Grow With A Cagr Of 3.9% From 2024 To 2030
Author: Lucintel LLC
3. Lucintel Forecasts The Global Frp Pole In Telecommunication Market To Grow With A Cagr Of 6.5% From 2024 To 2030
Author: Lucintel LLC
4. Lucintel Forecasts The Global Frp Pole In Power Transmission & Distribution Market To Grow With A Cagr Of 6% From 2024 To 2030
Author: Lucintel LLC
5. Lucintel Forecasts The Global Frp Pipe In Oil And Gas Market To Grow With A Cagr Of 5.1% From 2024 To 2030
Author: Lucintel LLC
6. Lucintel Forecasts The Global Frp Pipe In Chemical Market To Grow With A Cagr Of 3.6% From 2024 To 2030
Author: Lucintel LLC
7. Adopt A Modern Telecom Commission Management System To Fix Revenue Leakages
Author: Kevin
8. Quality Steel Pipes And Tubes With Commitment And Trusted Service
Author: CONTENT EDITOR FOR SAMPHIRE IT SOLUTIONS PVT LTD
9. Lucintel Forecasts The Global Foam Core For The Construction Market To Grow With A Cagr Of 3.7% From 2024 To 2030
Author: Lucintel LLC
10. How Important Is Mutual Fund?
Author: Sagar Shah
11. What Do You Need To Know About Customize Your Own Clothes
Author: Guangzhou Beianji Clothing
12. Detailed Tips To Choose Quality Cabinets And Joinery Melbourne
Author: William Harvey
13. Lucintel Forecasts The Global Foam Core For The Transportation Market To Grow With A Cagr Of 5.4% From 2024 To 2030
Author: Lucintel LLC
14. Silicone Sealing Foam Cord: The Valuable Option For You
Author: Dongguan Senma New Materials Technology Co., Ltd
15. How Investment Banking Companies And Credit Solutions Elevate Wealth Management
Author: Drishti Desai