ALL >> Hardware-Software >> View Article
From Concept To Creation: Cnc Routers For Precision Prototypes
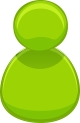
Material Choices for Prototyping
Selecting the right material for prototyping is crucial, as it directly impacts both the functionality and the quality of the final product. Common materials include plastics, wood, aluminum, and composites. Plastics such as acrylic and ABS are favored for their versatility and ease of machining. They can achieve intricate designs while also providing a lightweight option that is cost-effective for many projects. Wood, on the other hand, offers a natural aesthetic and is often used for creative prototypes or where a more traditional look is desired.
Aluminum and composite materials are preferred when durability is essential. Aluminum provides strength and rigidity, making it suitable for prototypes that need to withstand rigorous testing. Composites combine materials to enhance properties like strength-to-weight ratios, making them ideal for specialized applications. Each material brings unique benefits and challenges to the prototyping process. Understanding these variations allows designers to make informed choices tailored to their project needs.
Comparing Common Materials ...
... Used with CNC Routers
CNC routers are highly versatile tools that can work with various materials, each providing unique advantages. Wood remains one of the most popular choices due to its ease of use and availability. It offers a wide range of types, such as plywood, MDF, and solid wood, making it suitable for intricate designs and functional prototypes. Additionally, materials like acrylic and plastic are favored for their lightweight properties and ability to achieve smooth finishes. Each material's specific characteristics play a significant role in the type of projects best suited for CNC machining.
Metals also find their place in CNC routing, with aluminum being a preferred option among engineers and designers. It is easy to machine and provides strength without excessive weight. Other metals, such as brass or copper, may be selected for specialized applications where conductivity or aesthetic appeal is essential. When selecting materials for CNC routing, considering their machinability, cost, and application is crucial to achieving the best results in prototype production.
The CNC Machining Process
CNC machining involves a series of precise steps to transform a digital design into a tangible object. The process begins with creating a Computer-Aided Design (CAD) model, which serves as the blueprint for the prototype. After designing, the CAD file is converted into a compatible format for the CNC router, commonly known as G-code. This code provides specific instructions, controlling the movements of the cutting tool throughout the machining process.
Once the machine is set up with the appropriate material and tooling, the CNC router executes the programmed commands. It efficiently cuts, carves, or shapes the material according to the specifications of the design. This automation ensures high levels of accuracy and repeatability, making CNC machining especially beneficial for creating prototypes. Throughout the process, monitoring systems track the operation, allowing for adjustments if necessary to maintain precision and quality in the final outcome.
Step-by-Step Workflow from Design to Creation
The initial phase begins with the precise interpretation of the design concept. Designers often use CAD software to create detailed models, ensuring accurate dimensions and specifications. Prototypes undergo a series of modifications during this stage based on functionality and aesthetic requirements. Importing these designs into CNC programming software is crucial for preparing the machine to execute the necessary cuts.
Next, selecting the appropriate material is essential for translating the design into a tangible prototype. Once the material is secured, the CNC router is calibrated to accommodate the specified settings. This involves adjusting the cutting speed and depth, as well as choosing the right tool bits. After setting up, the actual machining process can commence, where the router meticulously follows the programmed instructions to shape the material into the desired form. This workflow highlights the importance of precision at each step to achieve a successful final product.
Troubleshooting Common CNC Issues
CNC routers are powerful tools, but they can encounter a variety of issues that may disrupt production. One common problem is tool wear, which can lead to inconsistent cuts and compromised quality. Regular inspection of cutting tools ensures that they remain sharp and efficient. Additionally, maintaining proper feed rates and spindle speeds can mitigate vibrations, which often affect precision and lead to poor surface finishes.
Machine calibration is another critical aspect of troubleshooting. If the router is not calibrated correctly, it may produce parts that deviate from the desired specifications. Performing routine check-ups on alignment and accuracy helps to identify misalignments early. Moreover, software glitches can also cause operational failures. Keeping the CNC software up to date is crucial for minimizing bugs and ensuring that the machine operates smoothly.
Tips for Maintaining Consistent Quality
Achieving consistent quality in CNC machining requires attention to several key factors. First, proper calibration of the CNC router for prototyping is essential to ensure precise cuts and accurate dimensions. Regularly check and adjust the machine's alignment, as even minor discrepancies can lead to significant variations in the final product. Additionally, using high-quality tools and materials contributes to better outcomes. Router bits should be kept sharp and replaced as needed to prevent wear that can affect performance.
Monitoring the setup and workflow is equally important. Implementing standard procedures for material setup and machine operation helps maintain uniformity across prototypes. Utilize templates and fixtures to ensure that components are positioned correctly each time. Finally, conducting routine inspections of the finished prototypes can help identify any potential quality issues early in the process. This proactive approach allows for adjustments and improvements to be made before moving on to the next project.
Enhancing Prototyping Efficiency
Streamlining the prototyping process is essential for maximizing efficiency in production. One effective strategy is to leverage advanced software that integrates design and manufacturing. Utilizing computer-aided design (CAD) tools allows for precise modeling and minimizes human error. Additionally, optimizing the machine settings based on material types can significantly enhance machining speed and accuracy, thereby reducing milling time.
Another method to improve efficiency involves pre-setting tools and using standardized templates. This practice not only saves setup time but also ensures consistency across multiple prototypes. Implementing workflow automation can further facilitate quick adjustments and adaptations during the process. Combining these approaches leads to a more agile prototyping environment, enabling quicker turnaround times while maintaining high-quality standards.
Strategies for Reducing Production Time
Efficient organization plays a crucial role in reducing production time during the CNC routing process. By preparing all necessary tools and materials in advance, operators can minimize downtime and streamline machine setups. This preparation includes organizing the workspace, ensuring all CAD files are ready for processing, and verifying that materials are accurately cut to the correct dimensions. Such attention to detail helps maintain a smooth workflow, leading to faster project completion.
Implementing automation can further enhance efficiency in prototyping. Utilizing advanced software that integrates with CNC machines allows for better management of design files and optimizes cutting paths. Additionally, automating repetitive tasks such as tool changes and material loading can significantly decrease idle time. Investing in CNC routers that feature these capabilities can yield substantial time savings, promoting a more productive prototyping environment.
FAQS
What are CNC routers and how do they work?
CNC routers are computer-controlled cutting machines used to create precise prototypes from various materials. They operate by following design specifications input into a computer, which directs the router to cut, carve, or engrave materials like wood, plastic, or metal.
What materials are best for prototyping with CNC routers?
Common materials for CNC prototyping include wood, acrylic, foam, and aluminum. The best choice depends on the desired finish, strength, and application of the prototype.
What is the typical workflow for creating a prototype using a CNC router?
The workflow generally involves designing the prototype using CAD software, converting the design into a format compatible with the CNC machine, setting up the machine with the chosen material, and finally running the machine to create the prototype.
What are some common issues encountered when using CNC routers?
Common issues include tool wear, incorrect settings, material shifts, and software glitches. Regular maintenance and careful setup can help prevent these problems.
How can I improve the efficiency of my CNC prototyping process?
To enhance efficiency, consider optimizing your design for quicker machining, using high-quality materials, maintaining your equipment regularly, and planning your workflow to minimize downtime.
We are a team of experienced professionals dedicated to providing the best CNC router machines to our customers.
Add Comment
Hardware/Software Articles
1. Modernizing Your Fuel Station For Better Performance With PetrosoftAuthor: Petrosoft
2. Rental Printers In Chennai
Author: ARK CANTON ENTERPRISES
3. 5 Ways How Finance And Business Analytics Is Revolutionizing Finance In 2025
Author: BiCXO
4. What Is An Expense Data Analysis? A Hidden Goldmine That Impacts Your Bottom Line
Author: BiCXO
5. Odoo Erp V18: It’s New, It’s Smart, It’s Sleek, It’s Powerful!
Author: Vasanth Ananth
6. How To Improve Employee Experience Using Workplace Management Software
Author: Jeya
7. Streamline Your Nyc Business Operations With Next-gen Payment Platforms
Author: Onyx Braun
8. What Are The Benefits Of Environmental Testing?
Author: Ace Test Labs
9. What Is Ansible In Devops?
Author: Jan Khan
10. Choosing The Best Erp Software For Your Manufacturing Business
Author: Ahesanali
11. Chchoosing The Best Erp Software For Your Manufacturing Businessoosing The Best Erp Software For Your Manufacturing Business
Author: Ahesanali
12. Amazon Seller Fba Tools: Finding Profitable Products Using Fba Tools In 2025
Author: kanhasoft
13. Key Benefits Of Project Cost Tracking Software For Efficient Project Management
Author: prestartr
14. Why Odoo Implementation Fails And How To Ensure Success
Author: Hetal V.
15. 10 Must-track Metrics (2025) For Sales Data Model
Author: BiCXO