ALL >> Business >> View Article
What Are The Requirements Of Parts Processing In Machining
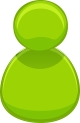
Introduction
In the realm of machining, the requirements of parts processing stand as the cornerstone for achieving high-quality finished products. Whether it's in the automotive, aerospace, or electronics industries, precision and compliance in part machining are non-negotiable. This article delves into the essential requirements that govern the machining process, shedding light on how they impact the overall manufacturing outcome. Additionally, we'll explore the value that Rapidefficient brings to the table in the CNC machining market, offering solutions that enhance productivity and quality.
Understanding the Basics of Part Machining
Part machining is the art and science of transforming raw materials into precise components that fit together to form complex machinery, devices, or structures. It's a fundamental process in manufacturing, serving as the backbone for industries ranging from automotive and aerospace to electronics and medical equipment. At its core, part machining involves removing material from a workpiece using various cutting tools and techniques to achieve the desired shape, size, and surface ...
... finish. This could be as simple as drilling a hole in a metal plate or as intricate as milling a complex aerospace component with micron-level precision.
Precision: The Core Requirement
Dimensional Accuracy
Dimensional accuracy refers to the closeness of the machined part's actual size to the designed dimensions specified in the blueprint. In industries where parts need to fit together precisely, like automotive engines or electronic circuit boards, even the slightest deviation in size can lead to catastrophic failures. For example, in the production of an engine cylinder block, if the bore diameter is off by a few micrometers, it can result in poor piston fit, leading to reduced engine performance, increased fuel consumption, and potential overheating. Achieving dimensional accuracy requires precise control of the machining process, from the selection of cutting tools to the calibration of the machine itself. Factors such as tool wear, thermal expansion of the workpiece during machining, and the rigidity of the machine tool all play a crucial role in determining whether the final part meets the required size specifications.
Shape Accuracy
Shape accuracy pertains to how closely the machined surface replicates the intended geometric form. A gear, for instance, must have teeth with the exact profile and spacing as designed to ensure smooth power transmission. Deviations in shape can cause vibrations, noise, and premature wear in machinery. Machining methods like milling, turning, and grinding are employed to achieve the desired shape, each with its own set of techniques and considerations. Advanced CNC machines use complex algorithms and high-precision servo systems to guide the cutting tool along the programmed path, minimizing errors and ensuring that the part's shape is as close to the ideal as possible. Additionally, post-processing inspections using coordinate measuring machines (CMMs) are essential to verify and correct any shape inaccuracies, guaranteeing that the final product functions as intended.
Surface Finish: More Than Meets the Eye
Importance of a Smooth Surface
Surface finish refers to the texture and smoothness of the machined part's surface. It's not just about aesthetics; a smooth surface can significantly impact the part's functionality. In the medical field, implants and surgical instruments require a high-quality surface finish to prevent bacterial adhesion and ensure biocompatibility. For example, a hip implant with a rough surface could cause inflammation and rejection in the body. In the automotive industry, engine components with a polished surface reduce friction, leading to improved fuel efficiency and performance. A rough surface on a piston or cylinder wall, on the other hand, would increase wear and tear, decreasing the engine's lifespan. Additionally, in electronics, smooth surfaces on circuit boards are crucial for proper soldering and electrical conductivity, preventing short circuits and ensuring reliable operation.
Achieving the Desired Surface Finish
There are several machining processes dedicated to achieving the desired surface finish. Grinding is a common method used to remove material and create a smooth surface. It's often employed for hardened materials and can achieve very tight tolerances. However, it can generate heat, which may affect the material's properties if not carefully controlled. Polishing, on the other hand, uses abrasive compounds and a polishing wheel or cloth to further refine the surface, giving it a mirror-like finish. Chemical mechanical polishing (CMP) combines chemical reactions with mechanical abrasion, commonly used in semiconductor manufacturing to achieve ultra-smooth surfaces on silicon wafers. Each process has its own set of parameters, such as abrasive type, speed, and pressure, that need to be optimized to achieve the best results. Manufacturers must carefully select the appropriate process based on the part's material, geometry, and required surface quality.
Material Compatibility and Selection
Matching Materials to the Job
Selecting the appropriate material for a part is akin to choosing the right foundation for a building. It's a decision that ripples through every stage of the machining process and ultimately determines the part's performance and lifespan. Different industries and applications impose specific demands on materials. In the aerospace sector, where components must endure extreme temperatures, pressures, and stresses, materials like titanium alloys and high-strength steels are favored. Their exceptional strength-to-weight ratios and resistance to fatigue make them suitable for aircraft engines, fuselage structures, and landing gear. For instance, titanium alloys can maintain their integrity in the searing heat of a jet engine's combustion chamber and the frigid temperatures of high-altitude flight. In contrast, the medical field demands materials that are not only biocompatible but also corrosion-resistant and capable of withstanding sterilization processes. Stainless steels and certain polymers are commonly used for surgical instruments and implants, ensuring patient safety and device longevity.
When choosing a material, one must consider its mechanical properties, such as tensile strength, hardness, and ductility. A part subjected to heavy loads, like a crankshaft in an engine, requires a material with high tensile strength to prevent deformation or failure. Chemical properties also play a crucial role. In corrosive environments, such as marine applications or chemical processing plants, materials like aluminum alloys with built-in corrosion resistance or specialized coatings are essential. Additionally, thermal conductivity, electrical conductivity, and magnetic properties may be relevant depending on the part's function. For example, in electronics manufacturing, materials with excellent thermal conductivity are used to dissipate heat from components, preventing overheating and ensuring reliable operation.
Ensuring Material Quality
Once the appropriate material is selected, ensuring its quality is non-negotiable. High-quality materials are the bedrock of precision machining. Sourcing materials from reputable suppliers is the first step. These suppliers should adhere to strict quality control standards and provide comprehensive material certifications. Verifying the authenticity of these certifications and conducting in-house inspections can further safeguard against subpar materials. Advanced inspection techniques, such as spectroscopy and metallography, can reveal a material's internal structure, composition, and potential defects. In the case of metal alloys, spectroscopic analysis can accurately determine the elemental makeup, ensuring it meets the required specifications. Metallography, on the other hand, involves examining the microstructure of the material under a microscope to detect any irregularities, such as inclusions or grain size variations, that could compromise its mechanical properties. By investing in material quality assurance, manufacturers can avoid costly rework, scrap, and potential failures in the finished product.
Tooling and Equipment: The Right Tools for the Task
Selecting Appropriate Cutting Tools
The selection of cutting tools is a critical determinant in the part machining process. It's not a one-size-fits-all scenario; rather, it demands a meticulous consideration of multiple factors. Firstly, the material of the part being machined plays a pivotal role. For instance, when working with hardened steel, carbide tools are often the preferred choice due to their exceptional hardness and wear resistance, capable of withstanding the abrasive forces exerted during cutting. In contrast, for softer materials like aluminum, high-speed steel tools might be more suitable as they can achieve a smoother finish without excessive tool wear.
The machining process itself also dictates the tool selection. In milling operations, different types of milling cutters are available, such as end mills, face mills, and ball nose mills. End mills are commonly used for profiling and slotting, while face mills are ideal for creating flat surfaces. Ball nose mills, with their rounded tips, are indispensable for machining complex 3D contours, ensuring a seamless transition between surfaces. For turning operations, the geometry of the turning tool, including the rake angle, clearance angle, and nose radius, must be carefully optimized to achieve the desired surface finish and dimensional accuracy.
Moreover, advancements in tool coating technologies have revolutionized the machining landscape. Coatings like titanium nitride (TiN), titanium carbonitride (TiCN), and diamond-like carbon (DLC) offer a myriad of benefits. TiN coatings provide excellent wear resistance and a low friction coefficient, reducing tool wear and improving chip evacuation. TiCN coatings combine the hardness of TiC with the lubricity of TiN, further enhancing tool life and cutting performance. DLC coatings, known for their extreme hardness and chemical inertness, are particularly suitable for machining abrasive and corrosive materials. These coatings not only extend the lifespan of the cutting tools but also allow for higher cutting speeds and feeds, ultimately boosting productivity.
Maintaining and Upgrading Equipment
Regular maintenance and timely upgrades of machining equipment are the bedrock of a reliable and efficient production process. A well-structured maintenance plan is essential to keep machines operating at peak performance. This includes routine inspections of critical components such as spindle bearings, ball screws, and linear guides. For spindle bearings, proper lubrication and periodic checks for vibration and temperature fluctuations can prevent premature failure and ensure machining accuracy. Ball screws, which are responsible for precise linear motion, need to be regularly adjusted for backlash to maintain positional accuracy.
In addition to preventive maintenance, the timely replacement of worn or obsolete equipment is equally crucial. As technology advances, newer machines offer enhanced capabilities, such as higher spindle speeds, greater precision, and improved automation. Upgrading to these state-of-the-art machines can significantly reduce production cycle times and improve part quality. For example, the latest CNC machines equipped with advanced servo control systems can achieve micron-level positioning accuracy, enabling the production of intricate components with tighter tolerances. Moreover, automation features like robotic tool changers and pallet changers can minimize downtime between machining operations, further enhancing productivity.
Rapidefficient, in the CNC machining market, understands the significance of well-maintained and upgraded equipment. They invest in cutting-edge machinery and adhere to rigorous maintenance schedules, ensuring that each part they produce meets the highest quality standards. This commitment to equipment excellence translates into shorter lead times, reduced waste, and increased customer satisfaction.
Programming and CAD/CAM Integration
The Role of Programming in Machining
Programming is the digital blueprint that guides the machining process. It's the language that machines understand, translating design intent into precise movements and actions. In modern machining, computer numerical control (CNC) programming has revolutionized the industry. By inputting a series of coded instructions, operators can automate the machining process, reducing human error and ensuring consistent results. For example, a CNC milling machine can be programmed to create complex 3D shapes with micron-level precision, repeating the process identically for each part produced. This level of automation not only boosts productivity but also allows for the production of highly intricate components that would be nearly impossible to achieve through manual machining.
Leveraging CAD/CAM Technologies
CAD/CAM technologies have become the backbone of modern part machining. Computer-Aided Design (CAD) allows engineers to create detailed 3D models of parts, visualizing every curve, hole, and surface before any material is cut. This digital design phase enables rapid prototyping and design iterations, as changes can be made with a few clicks. Once the design is finalized, Computer-Aided Manufacturing (CAM) takes over. CAM software translates the CAD model into machine-readable code, optimizing tool paths, cutting speeds, and feed rates. It also simulates the machining process, predicting potential collisions, tool wear, and surface finish issues. This virtual testing saves time and resources by identifying and resolving problems before the actual machining begins. For instance, in the production of a custom aerospace component, CAD/CAM integration allows manufacturers to design, test, and produce the part with unprecedented speed and accuracy, meeting tight project deadlines and strict quality requirements.
Rapidefficient harnesses the power of advanced CAD/CAM technologies, enabling them to offer rapid prototyping services. Their team of experts utilizes state-of-the-art software to design and simulate parts, ensuring that each component meets the highest standards of precision and quality. By streamlining the design-to-manufacturing process, Rapidefficient significantly reduces lead times, allowing customers to bring their products to market faster.
Quality Control and Inspection
Implementing Stringent Quality Checks
Quality control is the linchpin that holds the entire machining process together, ensuring that each part that rolls off the production line meets the highest standards. In industries where precision is non-negotiable, like aerospace and medical device manufacturing, even the minutest defect can have far-reaching consequences. For instance, in the production of aircraft turbine blades, a tiny flaw in the surface finish or dimensional accuracy could lead to catastrophic failures during flight.
To prevent such scenarios, manufacturers implement a multi-tiered inspection process that spans the entire machining journey. This begins with in-process inspections, where parts are checked at various stages of production. Operators use precision measuring tools to verify dimensions and surface quality, making immediate adjustments if deviations are detected. Once machining is complete, a comprehensive final inspection is carried out. This involves scrutinizing every aspect of the part, from its overall geometry to the finest details of its surface finish, using advanced inspection equipment and techniques.
Using Advanced Inspection Tools and Techniques
In the pursuit of impeccable part quality, advanced inspection tools and techniques have become indispensable. Coordinate measuring machines (CMMs) stand at the forefront of precision measurement. These devices use highly accurate probes to map the surface of a part, generating a digital model that can be compared to the original design. With micrometer-level precision, CMMs can detect even the slightest deviations in dimensional accuracy and shape, providing invaluable feedback for corrective actions.
Non-destructive testing (NDT) methods also play a crucial role, especially when it comes to detecting hidden defects within a part. Ultrasonic testing uses high-frequency sound waves to penetrate the material, revealing internal cracks, voids, or inclusions that might compromise the part's integrity. Eddy current testing, on the other hand, is highly effective for detecting surface and near-surface defects in conductive materials. By inducing electrical currents and analyzing the resulting magnetic fields, it can identify flaws that are invisible to the naked eye. These advanced techniques not only ensure the quality of individual parts but also contribute to the overall reliability and safety of the final product.
The Value of Rapidefficient in CNC Machining Market
Speeding up Production Cycles
In the highly competitive CNC machining market, Rapidefficient emerges as a game-changer, significantly accelerating production cycles. Their team of experts meticulously optimizes machining processes, eliminating any redundant steps that could potentially slow down production. By leveraging state-of-the-art CNC machines equipped with high-speed spindles and advanced tool changers, they can achieve rapid material removal rates without compromising on precision. For instance, in the production of a batch of aluminum alloy parts, Rapidefficient's optimized machining parameters and cutting-edge equipment allow them to complete the job in a fraction of the time compared to traditional methods. This not only meets tight project deadlines but also gives clients a crucial edge in bringing their products to market faster.
Ensuring Consistent Quality
Quality is the bedrock of Rapidefficient's operations. They have implemented a stringent quality control system that spans every stage of the machining process, from initial material inspection to final part verification. Their highly trained technicians use advanced metrology tools to conduct in-process inspections, ensuring that any deviations from the required tolerances are detected and corrected immediately. This proactive approach minimizes the risk of producing defective parts, saving both time and resources. For industries such as aerospace and medical, where the consequences of a single faulty part can be catastrophic, Rapidefficient's unwavering commitment to quality provides peace of mind. Their track record of consistently delivering high-quality components has earned them the trust of clients across diverse sectors.
Case Studies: Success Stories with Rapidefficient
To truly appreciate the value that Rapidefficient brings to the table, let's explore some real-world case studies where their expertise in part machining made all the difference.
Case 1: Aerospace Component Manufacturing
A leading aerospace company was tasked with developing a new generation of jet engine components. These parts required extremely tight tolerances, with dimensional accuracies in the micrometer range and complex geometries that tested the limits of traditional machining methods. Rapidefficient stepped in, leveraging their state-of-the-art 5-axis CNC machines and advanced CAD/CAM software. They meticulously optimized the machining process, from tool selection to cutting parameters, ensuring that each part met the exacting standards. The result? The components not only fit together perfectly during assembly but also withstood the extreme conditions of engine operation, contributing to enhanced fuel efficiency and overall performance. This successful collaboration not only helped the aerospace company meet its project deadlines but also strengthened its position in a highly competitive market.
Case 2: Medical Device Production
In the medical field, a startup was looking to bring a revolutionary orthopedic implant to market. The implant required a biocompatible material with a flawless surface finish to prevent any adverse reactions in the body. Rapidefficient's material experts recommended a specialized titanium alloy, known for its excellent biocompatibility and mechanical properties. Their machining team then employed a combination of precision grinding and chemical mechanical polishing to achieve the required surface smoothness. Stringent quality control measures, including ultrasonic testing and CMM inspections, were implemented at every stage of production. Thanks to Rapidefficient's attention to detail, the implants passed all regulatory requirements and clinical trials with flying colors, enabling the startup to launch their product and make a significant impact in the medical device industry.
Case 3: Automotive Precision Parts
An automotive manufacturer was facing challenges in producing high-precision transmission components. The parts needed to be manufactured in large quantities while maintaining consistent quality and dimensional accuracy. Rapidefficient's solution was to implement a highly automated production line, integrating robotic loading and unloading systems with their CNC machines. This not only reduced human error but also increased production throughput. By using custom-designed cutting tools and optimizing the machining programs, they achieved a remarkable reduction in production cycle times. The automotive manufacturer was able to meet the growing demand for their vehicles, improve the reliability of their transmissions, and gain a competitive edge in the market.
These case studies illustrate the tangible benefits that Rapidefficient offers across diverse industries. Their ability to combine technical expertise, advanced equipment, and a commitment to quality makes them a go-to partner for companies seeking top-notch part machining services.
Conclusion
In conclusion, the requirements of part machining in machining are multifaceted and demand meticulous attention to detail. Precision, surface finish, material compatibility, tooling, programming, and quality control all play pivotal roles in determining the success of a machining project. Rapidefficient stands out in the CNC machining market, offering not only rapid production cycles but also unwavering commitment to consistent quality. By partnering with experts like Rapidefficient and adhering to these essential requirements, manufacturers can unlock new levels of productivity and innovation, driving the manufacturing industry forward. Whether you're in aerospace, automotive, medical, or any other sector reliant on precision components, understanding and implementing these part machining requirements is the key to achieving excellence.
#Partmachiningrequirement, #rapidefficientmachiningparts
Rapidefficient web: https://rapidefficient.com
Add Comment
Business Articles
1. Lucintel Forecasts The Glass Fiber In The Global Marine Market To Grow With A Cagr Of 3.7% From 2024 To 2030Author: Lucintel LLC
2. Lucintel Forecasts The Glass Fiber In The Global E&e Market To Grow With A Cagr Of 3.9% From 2024 To 2030
Author: Lucintel LLC
3. Lucintel Forecasts The Global Frp Pole In Telecommunication Market To Grow With A Cagr Of 6.5% From 2024 To 2030
Author: Lucintel LLC
4. Lucintel Forecasts The Global Frp Pole In Power Transmission & Distribution Market To Grow With A Cagr Of 6% From 2024 To 2030
Author: Lucintel LLC
5. Lucintel Forecasts The Global Frp Pipe In Oil And Gas Market To Grow With A Cagr Of 5.1% From 2024 To 2030
Author: Lucintel LLC
6. Lucintel Forecasts The Global Frp Pipe In Chemical Market To Grow With A Cagr Of 3.6% From 2024 To 2030
Author: Lucintel LLC
7. Adopt A Modern Telecom Commission Management System To Fix Revenue Leakages
Author: Kevin
8. Quality Steel Pipes And Tubes With Commitment And Trusted Service
Author: CONTENT EDITOR FOR SAMPHIRE IT SOLUTIONS PVT LTD
9. Lucintel Forecasts The Global Foam Core For The Construction Market To Grow With A Cagr Of 3.7% From 2024 To 2030
Author: Lucintel LLC
10. How Important Is Mutual Fund?
Author: Sagar Shah
11. What Do You Need To Know About Customize Your Own Clothes
Author: Guangzhou Beianji Clothing
12. Detailed Tips To Choose Quality Cabinets And Joinery Melbourne
Author: William Harvey
13. Lucintel Forecasts The Global Foam Core For The Transportation Market To Grow With A Cagr Of 5.4% From 2024 To 2030
Author: Lucintel LLC
14. Silicone Sealing Foam Cord: The Valuable Option For You
Author: Dongguan Senma New Materials Technology Co., Ltd
15. How Investment Banking Companies And Credit Solutions Elevate Wealth Management
Author: Drishti Desai