ALL >> Business >> View Article
Low Voltage Cable Joint Materials: What You Need To Know
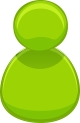
When working with electrical installations, selecting the right materials for low voltage cable joints is crucial for ensuring long-term reliability, safety, and performance. Cable joints are essential for connecting electrical cables together, and the materials used in these joints play a significant role in the overall functionality of the system. Whether you’re a professional engineer, technician, or someone simply looking to learn more about the components involved in electrical systems, understanding the materials behind low voltage cable joints is critical.
This article will dive into the various materials used in low voltage cable joints, their applications, and the environmental factors that affect their performance. We’ll also explore some of the latest innovations in the field, including OUKAMU’s pioneering Branch Cable technology, which has changed how cable joints are designed and installed.
Let’s get started by answering some common questions related to low voltage cable joints.
1. What Are Low Voltage Cable Joints Made Of?
Low voltage cable joints are made ...
... from a variety of materials, each designed to offer specific benefits depending on the environmental conditions and electrical requirements of the installation. The most commonly used materials include copper, aluminum, rubber, silicone, and various types of plastic. Let’s break down the key materials:
Copper – The Industry Standard for Electrical Conductivity
Copper is by far the most widely used material for low voltage cable joints. Its exceptional electrical conductivity means that copper joints can carry electrical current with minimal resistance, ensuring efficient performance. Copper also offers excellent corrosion resistance, which makes it an ideal choice for both indoor and outdoor installations.
Copper’s primary drawback is its cost. It is more expensive than other materials, which can increase the overall cost of large projects. However, its performance often justifies the higher price, particularly in applications that require high electrical conductivity or where reliability is paramount.
Aluminum – A Cost-Effective Alternative
While copper is the standard in the industry, aluminum is increasingly being used as a cost-effective alternative for low voltage cable joints. Aluminum is lighter and less expensive than copper, making it ideal for large-scale installations where cost and weight are significant factors.
However, aluminum does not have the same level of electrical conductivity as copper. As a result, aluminum joints are typically used in low-to-medium voltage applications. Furthermore, aluminum is more susceptible to oxidation, which can reduce conductivity over time. To prevent oxidation, aluminum joints are often coated with protective layers such as tin.
Rubber and Silicone – For Insulation and Sealing
Rubber and silicone materials are used primarily for insulation and sealing purposes in low voltage cable joints. They are flexible, durable, and offer excellent resistance to moisture, heat, and UV radiation, making them ideal for outdoor and industrial applications.
Rubber is commonly used in indoor applications, while silicone is often chosen for outdoor installations due to its ability to withstand extreme temperatures and exposure to sunlight. These materials not only provide electrical insulation but also prevent moisture from entering the joint, reducing the risk of corrosion or electrical shorts.
Plastic – Durability and Protection
Plastics such as PVC (Polyvinyl Chloride) and polyethylene are frequently used in low voltage cable joints for outer casings or jackets. These materials offer good durability, flexibility, and resistance to wear and tear. They are often used to protect cables from mechanical damage, chemicals, and weather conditions.
However, plastic can become brittle when exposed to extreme temperatures or UV radiation over long periods. As a result, UV-resistant plastics are commonly used for outdoor installations to protect against degradation from sunlight.
2. How Do Environmental Factors Affect Low Voltage Cable Joints?
Environmental conditions play a crucial role in the performance and longevity of low voltage cable joints. Whether you’re working in a hot, humid environment or one exposed to UV rays, choosing the right materials for the conditions at hand can help ensure the reliability and safety of your electrical system.
Temperature Extremes
Temperature is one of the most significant factors influencing the performance of cable joints. In cold environments, materials like rubber and silicone can become brittle, leading to cracking or loss of flexibility. On the other hand, in high-temperature environments, the insulation materials may soften or degrade, reducing their effectiveness.
To mitigate these risks, manufacturers design cable joints with materials that are rated for specific temperature ranges. For example, silicone is ideal for high-temperature applications, while other materials like polyethylene may be better suited for environments with lower temperatures.
Moisture and Humidity
Moisture is one of the leading causes of failure in low voltage cable joints. Water can seep into joints, causing corrosion or short circuits, which could lead to system failures. To prevent moisture from infiltrating the joint, materials like rubber and silicone are often used to form tight seals that keep out water and dirt.
Outdoor installations are particularly vulnerable to moisture, so selecting cable joints with Ingress Protection (IP) ratings, such as IP67 or IP68, ensures that the joint is sealed tightly against water ingress. The sealing materials used in the joint should be resistant to both moisture and temperature fluctuations.
UV Radiation
UV radiation from the sun can degrade materials like rubber and plastic, causing them to crack, discolor, or lose their insulating properties. This degradation can significantly shorten the lifespan of a cable joint, especially in outdoor applications where exposure to sunlight is frequent.
To protect against UV damage, manufacturers use UV-resistant materials such as silicone or treat plastic and rubber materials with UV inhibitors. This helps maintain the integrity and performance of the cable joint over time.
Chemical Exposure
In industrial and commercial settings, low voltage cable joints are often exposed to chemicals, oils, and other corrosive substances. If the material used for the joint isn’t resistant to these chemicals, the joint may degrade, leading to electrical failures.
To address this issue, cable joints in chemical environments are often made from materials like stainless steel or specially coated plastics that are resistant to corrosion and chemical degradation. Rubber and silicone can also offer some resistance to chemicals, but it’s important to choose materials specifically designed for the chemicals in question.
3. What Are the Different Types of Low Voltage Cable Joints?
There are several different types of low voltage cable joints, each designed for specific installation needs. The two most common types of joints are:
Straight Cable Joints
Straight cable joints are used to connect two cables of the same type and size in a straight line. These joints are designed to provide an electrical connection while maintaining the same continuity of current flow. They are typically used in installations where the cables are routed along the same path, such as in residential or commercial buildings.
Branch Cable Joints
Branch cable joints are used to split a main cable into two or more branches. These joints are essential when distributing power to multiple locations from a single source. Branch cable joints are commonly used in industrial, commercial, and infrastructure projects where power needs to be distributed across multiple areas.
OUKAMU’s Branch Cable technology has revolutionized this process. It is the world’s first cable branch connection technology, designed to simplify the installation and reduce the need for multiple connectors or junction boxes. The technology is exclusive, offering both space and cost efficiency, while enhancing safety and reliability.
4. What Is OUKAMU's Branch Cable Technology and How Does It Work?
OUKAMU has introduced an innovative new approach to cable branching with its Branch Cable technology. This technology offers a seamless way to connect multiple cables together while improving the efficiency and reliability of electrical systems.
Simplified Installation
OUKAMU’s Branch Cable technology significantly reduces the complexity of traditional cable branching. Conventional branching methods require junction boxes, connectors, and various other components, which can be time-consuming and prone to errors. The Branch Cable technology eliminates the need for these additional parts, simplifying the process and saving time.
Space and Cost Efficiency
By reducing the number of components required for branching, OUKAMU’s technology allows for more efficient use of space. This is especially important in installations where space is limited, such as in industrial environments or urban infrastructure projects. Additionally, fewer components mean lower overall project costs, making it an economically viable solution.
Safety and Reliability
Safety and reliability are always top priorities when working with electrical systems. OUKAMU’s Branch Cable technology is designed to minimize the risk of faulty connections, which can lead to electrical failures. The streamlined design ensures that connections are secure, reducing the likelihood of wiring errors and increasing the overall safety of the system.
Exclusive Market Share
As the first company to introduce cable branch technology, OUKAMU holds an exclusive market share for this revolutionary solution. Its application spans various sectors, including infrastructure, residential, commercial, and industrial installations.
5. How Do You Choose the Right Low Voltage Cable Joint for Your Project?
Choosing the right low voltage cable joint involves considering several factors, such as the type of cables used, the environmental conditions, and the installation requirements. Here are some tips to guide your decision-making process:
Match the Material to the Cable Type
Ensure that the joint material is compatible with the type of cable you are working with. For example, copper cables should be paired with copper joints for optimal conductivity, while aluminum cables may require specialized aluminum joints.
Consider Environmental Conditions
Take into account the environmental factors that could affect the performance of the joint. If the joint will be exposed to moisture, UV radiation, or extreme temperatures, select materials that are specifically designed to withstand these conditions.
Choose Between Straight and Branch Joints
Depending on whether you need a straight or branch connection, select the appropriate joint type. For projects involving power distribution to multiple locations, consider OUKAMU’s Branch Cable technology, which simplifies branching and increases installation efficiency.
References:
Electrical Materials for Low Voltage Cable Joints – www.electricalengineeringportal.com
Material Selection for Cable Joints – www.cablesolutions.com
The article is from https://www.okmbranchcable.com/
The product details can be seen: https://www.okmbranchcable.com/branch-cable/low-voltage-cable-joint
https://www.okmbranchcable.com/ https://sv.okmbranchcable.com/branch-cable/straight-through-cable-joints-with-connectors https://sv.okmbranchcable.com/branch-cable/cable-waterproof-joint https://sv.okmbranchcable.com/branch-cable/resin-joint-for-armoured-cable https://sv.okmbranchcable.com/infrastructure/cable-joint-for-hospital
Add Comment
Business Articles
1. Why Bookkeeping For Cpa Firms Is Essential For Growth And ComplianceAuthor: Niharika Jain
2. Kitchen Remodels Ideas: Farmhouse Kitchen Design Ideas To Warm Your Heart
Author: Vikram kumar
3. Top 8 Bi Tools With Intelligent Data Analytics Capabilities
Author: Maria
4. Top 5 Mistakes To Avoid When Getting An International Shipping Quote
Author: Tom
5. The Ultimate Guide To Cheap Rdp: Affordable And Secure Remote Desktop Solutions
Author: DigiRDP
6. The Role Of Financial Advisory Companies In India
Author: Drishti Desai
7. How Jaspire Makes Student Visa Approvals Faster And Easier
Author: pavitra
8. Finding The Best Pediatric Eye Doctor In Thane For Your Child’s Vision Care
Author: Anil Eye Hospital
9. Retirement Planning In 2025
Author: jkanishk
10. Cynosure Apogee For Rent: Expand Your Laser Hair Removal Services Without The Upfront Cost
Author: Ryan
11. Selectech, Inc. Receives Environmental Product Declaration For Ecolock
Author: Steven Dubin
12. Master Photo Editing With Google Photos: Top Tips And Professional Services To Elevate Your Images
Author: Sam
13. Mg Astor Automatic Price In Chennai: A Smart Suv Worth Exploring
Author: balaji
14. Find The Best Morris Garage Showroom
Author: balaji
15. How To Save Hours On Editing With Smart Clipping Path Techniques
Author: ukclippingpath