ALL >> General >> View Article
Aerospace Cnc Machining Parts / Commonly Used Machined Metal Materials
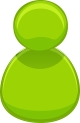
I. Introduction
In the realm of aerospace engineering, where precision and reliability are non-negotiable, Computer Numerical Control (CNC) machining plays a pivotal role. The production of aerospace components demands the highest standards of accuracy and quality, as even the slightest deviation can have catastrophic consequences. CNC machining has emerged as the go-to technology for manufacturing these intricate parts, enabling engineers to achieve the tight tolerances and complex geometries required. Central to this process are the machined metal materials, which must possess a unique set of properties to withstand the extreme conditions of spaceflight and aviation. This article delves into the world of aerospace CNC machining parts and explores the commonly used machined metal materials, highlighting the value that rapidefficient brings to this highly specialized field.
From engine components to structural elements, CNC machining is the backbone of aerospace manufacturing. It allows for the creation of parts with micron-level precision, ensuring optimal performance and safety. The ability to program machines ...
... to execute complex cutting paths and repetitive tasks with unerring accuracy has revolutionized the industry. This level of precision is not only essential for meeting design specifications but also for minimizing material waste and reducing production costs. In the competitive aerospace market, where innovation and efficiency are key, rapidefficient has positioned itself as a leading force, leveraging state-of-the-art CNC technology to deliver top-notch machining services.
As we embark on this exploration, we will uncover the specific metal materials that are favored in aerospace CNC machining and understand why they are the materials of choice. Whether it's the lightweight yet strong aluminum alloys, the heat-resistant superalloys, or the corrosion-resistant titanium, each material has its own unique story to tell. Join us as we unravel the mysteries behind these materials and discover how rapidefficient is driving progress in the aerospace CNC machining landscape.
II. The Importance of CNC Machining in Aerospace
The aerospace industry operates in an environment where the stakes are incredibly high. Every component, from the tiniest bolt to the largest wing structure, must function flawlessly under extreme conditions. Temperature fluctuations, high pressure differentials, and intense vibrations are just some of the challenges that aerospace parts face. CNC machining has become indispensable in meeting these demands due to its ability to produce parts with unparalleled precision.
Consider the example of turbine blades used in jet engines. These blades are subjected to temperatures that can exceed the melting point of many metals. To withstand such harsh conditions, they must be manufactured with intricate cooling channels and precise aerodynamic profiles. CNC machines can precisely mill these complex geometries, ensuring that the blades operate at peak efficiency while maintaining structural integrity. The tight tolerances achieved through CNC machining, often in the range of a few microns, are crucial for minimizing air leakage and maximizing thrust.
Another critical application is in the production of airframe components. The fuselage and wings require parts that are not only lightweight to reduce fuel consumption but also possess exceptional strength. CNC machining allows for the use of advanced aluminum alloys and composites, shaping them into components with optimized strength-to-weight ratios. This precision manufacturing process also ensures that all parts fit together seamlessly during assembly, reducing the need for costly rework and enhancing overall aircraft reliability.
In addition to precision, CNC machining offers the advantage of repeatability. In mass production of aerospace components, each part must be identical to its predecessor to guarantee consistent performance. Whether it's producing hundreds of landing gear components or thousands of cockpit instrument panels, CNC machines can replicate the same high-quality output time and time again. This level of consistency is essential for meeting strict regulatory requirements and maintaining the safety and performance standards that the aerospace industry demands.
rapidefficient's CNC machining services have been at the forefront of this technological revolution. Their state-of-the-art facilities and highly skilled technicians are dedicated to pushing the boundaries of what's possible in aerospace component manufacturing. By leveraging the latest advancements in CNC technology, rapidefficient ensures that every part produced meets or exceeds the stringent requirements of the aerospace sector, providing customers with the confidence that their projects are in the best hands.
III. Commonly Used Machined Metal Materials
A. Aluminum Alloys
Aluminum alloys are the workhorses of aerospace manufacturing, renowned for their low density and high strength-to-weight ratio. This unique combination makes them ideal for applications where weight reduction is critical, such as in aircraft wings and fuselage structures. The ability to shave off excess weight without sacrificing structural integrity translates directly into fuel savings and increased payload capacity, two factors that are of paramount importance in the aerospace industry.
One of the most commonly used aluminum alloys in aerospace is 7075. It contains zinc as the main alloying element, which imparts remarkable strength and hardness. This alloy is often used in the production of highly stressed components like wing spars and landing gear parts. Its excellent fatigue resistance ensures that these components can withstand the repeated loading and unloading cycles experienced during flight. For example, in a commercial airliner, the wing spars made from 7075 aluminum alloy play a crucial role in supporting the entire wing structure, enduring immense forces as the plane takes off, cruises, and lands.
Another popular alloy is 2024, which is alloyed with copper. It offers good machinability and moderate strength, making it suitable for a wide range of applications, including aircraft skins and rivets. The machinability of 2024 aluminum alloy allows for efficient production of complex shapes, reducing manufacturing time and costs. Aircraft skins made from this alloy need to be precisely formed to aerodynamic profiles, and CNC machining enables the accurate shaping required to minimize drag and optimize flight performance.
Aluminum-lithium alloys have also gained significant traction in recent years. By incorporating lithium, these alloys achieve even lower densities while maintaining or enhancing strength. This makes them a top choice for next-generation aerospace designs where every ounce matters. The development of aluminum-lithium alloys represents a continuous effort in materials science to meet the ever-evolving demands of the aerospace industry, with research focused on improving their fracture toughness and resistance to corrosion.
B. Titanium Alloys
When it comes to withstanding extreme temperatures and corrosive environments, titanium alloys stand unrivalled. These alloys possess a remarkable combination of high strength, low density, and excellent resistance to heat and corrosion. In aerospace applications, titanium alloys are often the material of choice for critical components that face the harshest conditions.
Take, for instance, the turbine engine components. The compressor blades and discs operate in an environment of high temperatures and intense rotational forces. Titanium alloys, such as Ti-6Al-4V, can endure temperatures up to several hundred degrees Celsius without significant loss of strength. This alloy contains aluminum and vanadium, which enhance its mechanical properties. The compressor blades made from Ti-6Al-4V must be machined to precise aerodynamic shapes to ensure efficient airflow and compression, a task that demands the highest level of CNC machining precision.
Another area where titanium alloys shine is in airframe structures that are exposed to corrosive agents, such as saltwater in marine environments or acidic pollutants in the atmosphere. The natural oxide layer on titanium provides outstanding corrosion resistance, protecting the underlying metal from degradation. This makes titanium alloys ideal for components like landing gear struts and engine mounts, which need to maintain their integrity over the long term.
However, machining titanium alloys is no easy feat. Their high strength and low thermal conductivity make them difficult to cut, often leading to rapid tool wear. To overcome these challenges, specialized machining techniques and tooling are required. Rapidefficient employs advanced cutting strategies, such as high-pressure coolant systems and optimized tool geometries, to ensure efficient and precise machining of titanium alloys. These techniques not only improve the quality of the machined parts but also extend tool life, reducing production costs.
C. Nickel-based Alloys
Nickel-based alloys are the go-to materials for components that must endure extreme heat and mechanical stress in aerospace engines. These alloys are characterized by their exceptional heat resistance, high-temperature strength, and resistance to thermal fatigue. In the heart of a jet engine, where temperatures can soar to over 1000°C, nickel-based superalloys like Inconel 718 and Hastelloy X are used to manufacture turbine blades, combustion chambers, and other critical parts.
Inconel 718, in particular, contains nickel, chromium, iron, and niobium, among other elements. This alloy exhibits excellent creep resistance, meaning it can withstand prolonged exposure to high temperatures without deforming. The complex microstructure of Inconel 718, which is carefully controlled during manufacturing, gives it its unique properties. Machining Inconel 718 requires specialized knowledge and equipment due to its hardness and tendency to work-harden during cutting. Rapidefficient's technicians are trained to handle these challenges, using slow cutting speeds, high coolant flow, and advanced tool coatings to achieve the required precision and surface finish.
The development of nickel-based alloys is a continuous process, with researchers constantly striving to improve their performance. New alloy compositions and heat treatment processes are being explored to enhance their strength and temperature capabilities even further. This synergy between materials science and machining technology is crucial for advancing aerospace engine design. As engines become more efficient and operate at higher temperatures, the demand for better nickel-based alloys and more precise machining techniques will only increase.
D. Steel Alloys
Steel alloys, with their diverse range of properties, also find significant applications in aerospace CNC machining. While aluminum and titanium alloys dominate in areas where weight is a primary concern, steel alloys offer unique advantages in certain components.
Stainless steel, for example, is highly resistant to corrosion, making it suitable for parts that come into contact with fluids or are exposed to harsh environmental conditions. In aircraft hydraulic systems, stainless steel fittings and tubing are used to ensure the integrity of the fluid transfer. The ability of stainless steel to resist rust and maintain its mechanical properties over time is essential for the reliable operation of these systems. CNC machining of stainless steel requires careful consideration of cutting parameters to prevent work hardening and achieve the desired surface finish.
High-strength steels, such as maraging steels, are used in applications where extreme strength and toughness are required. These steels are often employed in landing gear components, where they must bear the heavy loads during takeoff, landing, and taxiing. Maraging steels achieve their remarkable properties through a combination of alloying elements and a unique heat treatment process. The machining of maraging steels demands precision, as any defects could compromise the structural integrity of the final part. Rapidefficient utilizes advanced machining strategies and quality control measures to ensure that each component made from high-strength steels meets the strict aerospace standards.
In addition to these, other steel alloys are used for specific applications, such as spring steels for components that require elasticity and carbon steels for non-critical, low-stress parts. The versatility of steel alloys, combined with the precision of CNC machining, allows for the production of a wide variety of aerospace components that contribute to the overall safety and performance of aircraft.
IV. Rapidefficient's Value in CNC Machining Market
A. Precision and Efficiency
In the highly demanding aerospace CNC machining sector, precision is not just a goal; it's an absolute necessity. Rapidefficient has made significant strides in this regard, setting itself apart with its state-of-the-art machining capabilities. The company employs advanced CNC machines equipped with high-precision sensors and feedback systems, ensuring that every cut, every drill, and every milling operation is executed with micron-level accuracy.
One of the key metrics that highlight Rapidefficient's prowess is its defect rate, which is impressively low compared to industry standards. Through meticulous process control and continuous improvement, the company has achieved a defect rate of less than 0.1% for critical aerospace components. This means that out of every thousand parts produced, fewer than one will have any quality issues. Such a high level of precision not only minimizes material waste but also reduces the need for costly rework and inspection, saving both time and resources.
To put this into perspective, consider a batch of 10,000 turbine blade components. With an industry average defect rate of around 1%, one could expect approximately 100 defective blades. These would then need to be either repaired or scrapped, incurring additional costs for labor, materials, and production time. In contrast, Rapidefficient's defect rate of 0.1% would result in only 10 defective blades, a tenfold reduction. This translates directly into significant cost savings and faster delivery times for aerospace manufacturers.
In addition to precision, Rapidefficient is synonymous with efficiency. The company has optimized its production processes to minimize cycle times without compromising quality. By leveraging advanced CAM (Computer-Aided Manufacturing) software and real-time process monitoring, Rapidefficient can identify and eliminate bottlenecks in the production line. This allows for a seamless flow of work, ensuring that each machining operation is completed in the shortest possible time.
For instance, in the production of a complex aerospace bracket, Rapidefficient's streamlined process reduced the machining time by 30% compared to traditional methods. This was achieved through a combination of optimized toolpaths, high-speed machining strategies, and intelligent fixturing. The result was not only a faster turnaround time but also increased productivity, enabling aerospace companies to meet tight project deadlines and gain a competitive edge in the market.
B. Advanced Technology and Equipment
At the heart of Rapidefficient's success lies its continuous investment in advanced technology and equipment. The company's machining facilities are equipped with the latest generation of CNC machines, featuring cutting-edge capabilities that are essential for aerospace component manufacturing.
One such technology is the use of intelligent machining systems. These systems utilize real-time data acquisition and analysis to monitor the machining process. Sensors embedded in the machines collect data on parameters such as cutting forces, tool wear, and temperature. This data is then fed into advanced algorithms that can predict potential machining issues before they occur. For example, if the system detects an abnormal increase in cutting force, it can automatically adjust the feed rate or spindle speed to prevent tool breakage and ensure consistent part quality.
Another area where Rapidefficient stands out is in its adoption of multi-axis machining technology. Five-axis and even six-axis CNC machines are commonplace in their facilities. These machines enable the production of complex geometries that are typical in aerospace parts, such as impellers, turbine blades, and structural brackets with intricate shapes. The ability to move the workpiece and the cutting tool simultaneously in multiple axes allows for the creation of undercuts, bevels, and other complex features in a single setup, reducing the need for multiple machining operations and improving overall accuracy.
The use of high-performance cutting tools and tooling systems is also a hallmark of Rapidefficient's operations. The company partners with leading tool manufacturers to develop custom tool geometries and coatings optimized for aerospace materials. For machining titanium alloys, for instance, specialized carbide tools with advanced coatings are used to withstand the high temperatures and abrasive nature of the material. These tools not only improve machining efficiency but also extend tool life, reducing the frequency of tool changes and further enhancing productivity.
In addition to hardware, Rapidefficient has also invested in advanced software for design and simulation. CAD/CAM software is used to create highly detailed 3D models of aerospace components, allowing engineers to optimize the design for manufacturability. Simulation software is then employed to virtually test the machining process, predicting potential errors and optimizing toolpaths. This digital twin approach ensures that the actual machining process runs smoothly, minimizing errors and reducing the time required for prototype iterations.
C. Customized Solutions
Aerospace companies often require bespoke machining solutions to meet their unique design requirements. Rapidefficient has built a reputation for providing tailored services that go beyond standard machining. The company's team of experienced engineers and technicians work closely with clients from the initial design phase to the final delivery of the components.
During the design stage, Rapidefficient offers valuable input based on its deep understanding of machining capabilities and material properties. For example, if an aerospace firm is designing a new engine housing, Rapidefficient's engineers can suggest design modifications that improve manufacturability while maintaining the required performance characteristics. This could involve optimizing wall thicknesses, adding draft angles, or choosing the most suitable material and heat treatment process.
Once the design is finalized, Rapidefficient develops a customized machining plan. This plan takes into account factors such as batch size, required tolerances, and delivery deadlines. For small-batch production of high-precision components, the company may employ a flexible manufacturing system that allows for quick changeovers between different part designs. For large-volume orders, it optimizes the production line for maximum efficiency, using dedicated fixtures and automated loading/unloading systems.
Quality control is another area where Rapidefficient's customized approach shines. The company implements a rigorous quality assurance process that is tailored to each project. In addition to standard inspection methods such as coordinate measuring machines (CMMs) and optical profilometers, Rapidefficient may develop custom inspection fixtures and procedures for unique aerospace components. This ensures that every part meets the exacting quality standards of the aerospace industry.
Even after the components are delivered, Rapidefficient offers comprehensive after-sales support. This includes providing technical documentation, assisting with installation and integration, and offering maintenance and repair services. In the event of any issues with the machined parts, the company's responsive customer service team is on hand to quickly resolve the problem, minimizing downtime for the aerospace customer. This end-to-end service offering has made Rapidefficient a trusted partner for aerospace companies looking to bring their innovative designs to life.
V. How to Choose the Right Machined Metal Materials
A. Consideration of Mechanical Properties
Selecting the appropriate machined metal material begins with a thorough understanding of the mechanical properties required for the specific aerospace component. The mechanical properties encompass a range of factors, including strength, toughness, hardness, and fatigue resistance, each playing a crucial role in determining the suitability of a material for a given application.
Strength is perhaps the most fundamental property to consider. It determines the material's ability to withstand the forces exerted on it during operation. For components subjected to significant tensile, compressive, or shear forces, such as engine mounts and wing spars, materials with high tensile and yield strengths are essential. Aluminum alloys like 7075, with their excellent strength-to-weight ratios, are often favored for such applications. In a high-performance fighter jet, the wing spars must endure immense aerodynamic forces during maneuvers, and the strength of 7075 aluminum alloy ensures structural integrity while minimizing weight.
Toughness is equally important, especially in applications where the component may be exposed to sudden impacts or vibrations. Tough materials can absorb energy without fracturing, preventing catastrophic failures. Titanium alloys, known for their toughness, are commonly used in landing gear components. When an aircraft lands, the landing gear experiences a significant impact, and the toughness of titanium alloys helps absorb the shock, protecting the overall structure. For example, in a commercial airliner, the titanium alloy landing gear struts can withstand repeated landings without developing cracks or fractures.
Fatigue resistance is a critical consideration for components that undergo cyclic loading, such as turbine blades and rotating shafts. These parts experience millions of loading cycles during their operational lifetimes, and materials with poor fatigue resistance would quickly develop cracks and fail. Nickel-based alloys, like Inconel 718, exhibit outstanding fatigue resistance, making them the material of choice for turbine engine components. The complex microstructure of Inconel 718 allows it to resist crack initiation and propagation, ensuring the reliable operation of the engine even under extreme conditions.
In addition to these properties, the modulus of elasticity, which measures a material's stiffness, also plays a role in certain applications. For components where dimensional stability is crucial, such as optical mounts in satellite systems, materials with a low coefficient of thermal expansion and appropriate stiffness are required. Some specialty alloys, such as Invar, have been developed to meet these specific needs, maintaining their shape and dimensions over a wide temperature range.
B. Corrosion Resistance Requirements
In the aerospace environment, corrosion is a constant threat that can compromise the integrity and performance of components. Aircraft operate in diverse conditions, from the humid and salty air near the ocean to the acidic pollutants in industrial areas. Therefore, choosing materials with adequate corrosion resistance is vital to ensure the longevity and safety of aerospace CNC machining parts.
Stainless steels are widely used in applications where corrosion resistance is a primary concern. Their chromium content forms a passive oxide layer on the surface, protecting the underlying metal from oxidation and corrosion. In aircraft hydraulic systems, stainless steel fittings and tubing are used to transport fluids, preventing leaks and system failures due to corrosion. The austenitic stainless steels, such as 316L, are particularly popular due to their excellent resistance to chloride-induced corrosion, making them suitable for use in marine environments.
Titanium alloys also offer outstanding corrosion resistance, thanks to their natural oxide layer. This property makes them ideal for airframe structures and components exposed to harsh environmental conditions. For instance, the fuselage skin of an aircraft flying over the ocean is constantly exposed to salt spray. Titanium alloys can resist the corrosive effects, maintaining the structural integrity and appearance of the aircraft. In addition, titanium alloys are biocompatible, which is an added advantage for components that may come into contact with human occupants, such as cabin fittings.
Aluminum alloys, while generally corrosion-resistant, can be further enhanced through surface treatments. Anodizing is a common process that forms a thicker oxide layer on the surface of aluminum components, improving their corrosion resistance. This is often applied to aircraft skins and other exterior parts, protecting them from environmental damage. For example, the aluminum alloy panels used in the construction of an aircraft's wings can be anodized to prevent corrosion and maintain their aerodynamic smoothness.
In some cases, coatings can be applied to materials to provide additional corrosion protection. For nickel-based alloys used in engine components, ceramic coatings can be used to enhance their resistance to high-temperature corrosion and oxidation. These coatings act as a barrier, preventing the corrosive gases and molten salts in the engine environment from attacking the underlying metal.
C. Cost-effectiveness Analysis
Cost is always a significant factor in material selection, especially in the aerospace industry where large-scale production and strict budgetary constraints are the norm. When choosing machined metal materials, a comprehensive cost-effectiveness analysis must be conducted, taking into account not only the initial cost of the material but also the cost of machining, finishing, and the overall lifecycle cost.
Aluminum alloys, for example, are generally more cost-effective compared to titanium and nickel-based alloys. Their lower cost of raw materials and relatively easy machinability make them a popular choice for many non-critical aerospace components. In the production of aircraft interiors, such as seat frames and cabin fittings, aluminum alloys can provide sufficient strength and functionality at a lower cost. This allows airlines to outfit their aircraft with lightweight, yet durable components, while also keeping costs in check.
However, in applications where the performance requirements are extremely high, such as in engine components and critical structural parts, the higher cost of materials like titanium and nickel-based alloys may be justified. Although these materials are more expensive, their superior properties can lead to longer service lives and reduced maintenance costs. For instance, the use of titanium alloys in turbine engine components can improve fuel efficiency and reduce the frequency of engine overhauls, ultimately resulting in cost savings over the long term.
The cost of machining also varies depending on the material. Some materials, like titanium alloys, are notoriously difficult to machine due to their high strength and low thermal conductivity, leading to increased tool wear and longer machining times. This can significantly drive up the cost of production. In contrast, aluminum alloys are relatively easy to machine, allowing for faster production rates and lower machining costs. Rapidefficient takes these factors into account when providing machining services, optimizing the process to minimize costs while maintaining quality.
Another aspect to consider is the recyclability of materials. Aluminum alloys are highly recyclable, and recycled aluminum can be used to produce new aerospace components, further reducing costs and environmental impact. In contrast, some specialty alloys may be more difficult to recycle, adding to the overall lifecycle cost. By carefully weighing these factors, aerospace manufacturers can make informed decisions about material selection, ensuring both performance and cost-effectiveness.
VI. Conclusion
In conclusion, the marriage of CNC machining and carefully selected machined metal materials is the cornerstone of aerospace engineering's success. The ability to produce components with unmatched precision and reliability has propelled the aerospace industry to new heights, enabling us to explore the skies and beyond. Rapidefficient's unwavering commitment to excellence, evident in its precision, advanced technology, and customized solutions, has made it a standout player in the CNC machining market.
As we look to the future, the aerospace industry will continue to demand even greater innovation and efficiency. The development of new materials, such as advanced composites and nanostructured alloys, will present both challenges and opportunities. Machining techniques will need to evolve to handle these novel materials, and Rapidefficient is well-positioned to lead the charge.
For aerospace companies seeking a reliable partner to bring their designs to life, Rapidefficient offers the expertise, technology, and dedication required to meet the most stringent requirements. Whether it's the next-generation commercial airliner, a cutting-edge satellite, or a supersonic military jet, Rapidefficient has the capabilities to deliver high-quality CNC machined parts that will soar to new heights. Embrace the possibilities of aerospace CNC machining with Rapidefficient and be part of the journey that shapes the future of flight.
VII. Recommendation
When it comes to sourcing top-notch CNC aluminum machining services in the aerospace sector, Rapidefficient stands out as a premier choice. With years of experience under their belt, they have mastered the art of machining aluminum alloys to meet the most demanding aerospace specifications.
Their comprehensive service portfolio covers everything from initial design consultations to final quality inspections. Whether you need precision-machined wing components, engine parts, or intricate brackets, Rapidefficient has the expertise and equipment to deliver. Their team of skilled engineers and technicians work closely with clients, ensuring that each project is tailored to exact requirements.
Quality is at the forefront of Rapidefficient's operations. They adhere to strict aerospace standards, employing advanced inspection techniques to guarantee the integrity of every machined part. This commitment to excellence has earned them rave reviews from customers, who praise not only the precision of their work but also their prompt delivery and reliable after-sales support.
In a competitive market, Rapidefficient has carved a niche for itself by combining cutting-edge technology, a highly skilled workforce, and a customer-centric approach. If you're seeking a partner to bring your aerospace CNC machining projects to life, look no further than Rapidefficient. Their dedication to innovation and quality will surely exceed your expectations and help you reach new heights in aerospace manufacturing.
Rapidefficient website: https://rapidefficient.com
Add Comment
General Articles
1. Hr Management: How To Handle Termination Of EmploymentAuthor: Rosalina Wolf
2. Dme Billing And Home Health Billing: Integrated Medical Billing Services For Better Care
Author: Charlie Robinson
3. High Employability Through 64 Kala Concept
Author: Chaitanya Kumari
4. Softlink Global Ceo Amit Maheshwari Honoured With Best Entrepreneur Award At Maharashtra Corporate & Education Excellence Awards 2025
Author: Softlink Global
5. Why Businesses Are Switching To Open Source Alternatives To Crystal Reports
Author: Vhelical
6. Why Eastern Europe Is The Smartest Bet For B2b Travel In 2025
Author: seopass
7. Sap Erp Software In Udaipur – The Digital Core Of Scalable Business Success
Author: Akansha
8. Gws Tele Services: Powering India's Digital Future
Author: GWS Tele Services
9. The Future Of Clinic Management Software: What To Expect In 2026
Author: sheetal
10. 11 Hills Park In Dubai By Townx
Author: TownX
11. What Happens If You Don’t Replace A Missing Tooth?
Author: Dr indveer reddy
12. Why You Need A Tracker For Your Car: Benefits, Features & Buying Guide
Author: What Is a Tracker for Car?
13. Create A Marketplace Like Amazon
Author: davidbeckam
14. Autonomous Vehicles Market Insights And trends
Author: Rutuja kadam
15. Key Trends In The Automotive Parts sector
Author: Rutuja kadam