ALL >> Business >> View Article
How To Improve The Quality Of Precision Parts Processing?
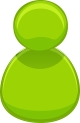
I. Introduction
In modern manufacturing, the quality of precision parts processing plays a pivotal role. It is the cornerstone for ensuring the performance, reliability, and safety of various products, ranging from aerospace components that endure extreme conditions to the intricate parts in medical devices that demand the highest precision. High-quality precision parts not only enhance the functionality of end products but also contribute to reducing production costs by minimizing errors and waste. In the highly competitive landscape of CNC machining, Rapidefficient has emerged as a key player, dedicated to delivering top-notch precision parts with remarkable speed and efficiency. This article delves into the essential strategies and techniques for improving the quality of precision parts processing, providing valuable insights for manufacturers and enthusiasts alike.
II. Understanding Precision Parts Machining
Precision parts machining is a specialized manufacturing process that aims to produce components with extremely tight tolerances and high accuracy. It goes beyond the capabilities of conventional ...
... machining, delving into the realm of micron and even nanometer-level precision.
The defining characteristics of precision parts machining are manifold. Firstly, the precision achieved is remarkable, with tolerances often measured in micrometers. This level of accuracy is essential for components that need to fit together seamlessly, such as in the assembly of a high-performance engine where even the slightest deviation could lead to inefficiencies or failures. Secondly, surface finish quality is of utmost importance. A smooth and defect-free surface not only enhances the aesthetic appeal but also contributes to the functionality and durability of the part. In optical applications, for instance, a flawless surface finish is crucial to ensure proper light transmission and reflection.
The applications of precision parts machining span across diverse industries. In aerospace, where safety and performance are non-negotiable, precision parts are used in everything from jet engine components that must withstand extreme temperatures and pressures to navigation systems that require pinpoint accuracy. The medical field relies heavily on precision machining for the production of surgical instruments, implants, and diagnostic equipment. A hip implant, for example, needs to be fabricated with the highest precision to ensure a perfect fit and long-term functionality within the human body. In the electronics sector, with the continuous drive towards miniaturization, precision parts machining enables the creation of microchips, connectors, and other components that power our modern digital devices. Without the advancements in precision machining, the development of these industries would be severely hampered, highlighting its indispensable role in today's technological landscape.
III. Key Factors Affecting Machining Quality
A. Equipment and Tools
The foundation of high-quality precision parts processing lies in advanced CNC equipment. State-of-the-art machining centers, lathes, and milling machines equipped with high-precision servo systems can achieve micron-level positioning accuracy, ensuring that every cut and movement is executed with utmost precision. For instance, a multi-axis machining center can simultaneously control multiple cutting tools from different angles, enabling the creation of complex geometries that would be impossible with traditional machinery.
Equally crucial are the cutting tools and measuring instruments. High-quality carbide or diamond-coated tools maintain sharp cutting edges for longer periods, reducing tool wear and the likelihood of dimensional errors. Precision measuring tools such as coordinate measuring machines (CMMs) and optical comparators allow for real-time inspection of part dimensions, detecting even the slightest deviations and enabling immediate corrective actions. A CMM can measure the dimensions of a small component with an accuracy of up to a few micrometers, guaranteeing that the finished part meets the strictest tolerances.
B. Material Selection
Selecting the appropriate raw materials is a critical step. Materials must possess specific mechanical properties, such as hardness, toughness, and thermal stability, depending on the application. In the aerospace industry, titanium alloys are favored for their high strength-to-weight ratio and resistance to extreme temperatures, but they require specialized machining techniques due to their hardness.
The quality and homogeneity of the material also play a significant role. Inconsistencies in material structure can lead to uneven machining, resulting in surface defects and dimensional inaccuracies. For example, in the production of precision optical lenses, the slightest impurity or variation in the glass material can cause distortion and affect the optical performance. Therefore, sourcing materials from reliable suppliers and conducting thorough quality inspections are essential to ensure consistent machining results.
C. Personnel Skill and Experience
Skilled and experienced operators are the backbone of precision machining. They possess in-depth knowledge of CNC programming, machine operation, and tooling, allowing them to optimize machining processes for maximum efficiency and quality. An experienced operator can make real-time adjustments to cutting parameters based on the sound of the machine, the chip formation, or the vibration felt, ensuring that the machining remains smooth and accurate.
Moreover, a strong sense of responsibility and attention to detail are indispensable. Precision machining demands meticulousness at every step, from setting up the workpiece to final inspection. Operators must be committed to following strict quality control procedures and continuously strive for improvement through learning and adopting new techniques. Regular training programs and knowledge sharing within the team help operators stay updated with the latest industry trends and enhance their skills.
D. Processing Technology and Parameters
The choice of processing technology and parameters has a direct impact on the quality of precision parts. A well-designed process route takes into account factors such as the complexity of the part, the material properties, and the required tolerances. For example, in machining a complex mold, a combination of roughing, semi-finishing, and finishing operations is carefully planned to gradually remove material while minimizing stress and deformation.
Optimizing cutting parameters like cutting speed, feed rate, and depth of cut is equally crucial. Too high a cutting speed can lead to excessive tool wear and poor surface finish, while too slow a speed reduces productivity. Finding the optimal balance requires a deep understanding of the material being machined and the capabilities of the equipment. Additionally, proper control of machining allowances ensures that the final dimensions are achieved after subsequent finishing processes, eliminating the need for costly rework.
IV. Strategies to Improve Machining Quality
A. Regular Equipment Maintenance and Calibration
Regular maintenance and calibration of equipment are fundamental to ensuring machining quality. CNC machines, being high-precision instruments, are susceptible to wear and tear over time. Scheduled maintenance checks should cover all critical components, including spindle bearings, servo motors, and guideways. Lubrication of moving parts, for example, needs to be carried out at precise intervals to reduce friction and ensure smooth operation. A well-lubricated spindle can maintain its rotational accuracy, which is vital for achieving consistent part dimensions.
Calibration of the machine's positioning system is equally crucial. Using precision calibration artifacts and advanced laser interferometers, any deviations in the machine's axes can be detected and corrected. This process ensures that the actual cutting paths match the programmed ones with the highest accuracy. Additionally, tool measurement and compensation systems should be regularly updated to account for tool wear. By constantly monitoring and adjusting for tool wear, the dimensional integrity of the machined parts can be preserved throughout the production run.
B. Strengthening Material Inspection
The quality of raw materials is a linchpin in precision parts machining. Implementing a rigorous material inspection process begins with verifying the material's chemical composition. Advanced spectrometers can analyze the elemental makeup of metals, ensuring that they meet the specified alloy requirements. In the case of aluminum alloys used in aerospace applications, even a slight deviation in the percentage of alloying elements like copper or magnesium can affect the material's strength and corrosion resistance.
Physical property tests, such as hardness and tensile strength measurements, provide further insights into the material's suitability. Microscopic inspection of the material structure helps identify any internal defects, like inclusions or porosity, that could lead to machining failures. Collaborating closely with reliable suppliers is also key. Establishing long-term partnerships based on quality agreements and regular audits ensures a consistent supply of high-quality materials. Suppliers who adhere to strict quality control standards can significantly reduce the risk of material-related defects in the final parts.
C. Staff Training and Skill Upgrading
Investing in the skills and knowledge of machining personnel is a strategic move. Organizing regular training programs on the latest CNC programming techniques, such as multi-axis machining and high-speed milling, empowers operators to handle complex part geometries with ease. These programs can include hands-on workshops where operators practice programming and operating advanced machinery under the guidance of experienced instructors.
Encouraging knowledge sharing and cross-departmental communication within the organization also fosters innovation. Machining operators can exchange ideas with engineers, quality control inspectors, and maintenance technicians to gain a holistic understanding of the production process. This collaborative environment enables them to troubleshoot issues more effectively and implement process improvements. Furthermore, setting up an incentive mechanism that rewards employees for achieving high-quality machining results motivates them to continuously strive for excellence. Recognitions like performance bonuses or career advancement opportunities based on quality metrics create a culture of quality consciousness.
D. Optimizing Processing Technology
Staying at the forefront of processing technology is essential for quality improvement. Keeping abreast of industry advancements and benchmarking against leading manufacturers can provide valuable insights. For example, learning from companies that have successfully implemented ultra-precision grinding techniques can inspire improvements in one's own machining processes.
Conducting in-house experiments and trials to optimize machining parameters is a practical approach. By systematically varying cutting speeds, feed rates, and depths of cut while closely monitoring part quality and production efficiency, the optimal parameter combinations can be identified. This iterative process may involve using statistical analysis tools to analyze the results and make data-driven decisions. Additionally, embracing emerging technologies like additive manufacturing in conjunction with traditional machining can open up new possibilities. Hybrid manufacturing processes that combine the strengths of both techniques can produce complex parts with enhanced precision and reduced production time.
V. The Value of Rapidefficient in CNC Machining Market
A. Advanced Technology and Equipment
Rapidefficient stands at the forefront of CNC machining technology, equipped with state-of-the-art machinery and advanced manufacturing systems. Their machining centers feature high-speed spindles, capable of reaching rotational speeds that enable rapid material removal while maintaining the highest precision. For instance, the advanced spindle technology allows for precise milling and drilling operations, ensuring that even the most intricate part features are accurately reproduced. Multi-axis machining capabilities further enhance their versatility, enabling the production of complex geometries that are essential in industries such as aerospace and automotive. With simultaneous control over multiple axes, Rapidefficient can craft components with undercuts, curved surfaces, and intricate internal structures, all within tight tolerances.
B. Professional Team
The company's team of professionals is a driving force behind its success. Comprising experienced engineers, highly skilled machinists, and dedicated quality control inspectors, they bring a wealth of knowledge and expertise to every project. The machinists have years of hands-on experience, having worked on a diverse range of precision parts, from miniature electronic components to large-scale industrial machinery parts. Their in-depth understanding of different materials and machining processes allows them to make real-time adjustments, ensuring optimal results. Engineers collaborate closely with clients, providing valuable insights during the design phase to enhance manufacturability without compromising on quality. Quality control inspectors employ advanced metrology tools and 严格的 inspection procedures to catch even the slightest deviations, guaranteeing that only flawless parts leave the facility.
C. Quality Assurance System
Rapidefficient has implemented a comprehensive quality assurance system that spans from raw material sourcing to final product inspection. Stringent quality control measures are in place at every stage of the production process. When it comes to raw materials, they conduct thorough inspections, verifying the chemical composition, mechanical properties, and dimensional accuracy. This ensures that the foundation of each precision part is of the highest quality. During manufacturing, in-process inspections are carried out at regular intervals, using precision measuring instruments like CMMs and optical comparators. Any deviations are immediately addressed, preventing the propagation of errors. In the final inspection phase, parts undergo a battery of tests to confirm that they meet or exceed the required specifications. This commitment to quality has earned Rapidefficient a stellar reputation for delivering reliable and high-performing precision parts.
D. Efficient Production Capacity
Efficient production is a hallmark of Rapidefficient. By optimizing production processes and implementing lean manufacturing principles, they are able to minimize waste, reduce production time, and maintain consistent quality. Their production facility is organized to ensure a smooth flow of work, with well-planned layouts that minimize material handling and setup times. Advanced production scheduling software enables them to manage multiple projects simultaneously, allocating resources effectively to meet tight deadlines. For urgent orders, they have established rapid response mechanisms, reallocating resources and adjusting production plans to ensure on-time delivery without sacrificing quality. This ability to balance speed and quality has made Rapidefficient a preferred partner for businesses operating in time-sensitive industries.
VI. Conclusion
Improving the quality of precision parts processing is a multifaceted endeavor that demands continuous attention to detail and a commitment to excellence. By focusing on key aspects such as advanced equipment, proper material selection, skilled personnel, and optimized processing techniques, manufacturers can elevate the quality of their precision parts to new heights. Rapidefficient, with its state-of-the-art technology, professional team, robust quality assurance system, and efficient production capacity, exemplifies the benchmark for precision parts machining in the CNC market. Whether you are in the aerospace, medical, electronics, or any other industry reliant on precision components, partnering with Rapidefficient can unlock the potential for superior quality and timely delivery. Embrace the strategies outlined in this article and consider collaborating with Rapidefficient to stay ahead in the competitive world of precision manufacturing.
Rapidefficient website: https://rapidefficient.com
Add Comment
Business Articles
1. Lucintel Forecasts The Glass Fiber In The Global Marine Market To Grow With A Cagr Of 3.7% From 2024 To 2030Author: Lucintel LLC
2. Lucintel Forecasts The Glass Fiber In The Global E&e Market To Grow With A Cagr Of 3.9% From 2024 To 2030
Author: Lucintel LLC
3. Lucintel Forecasts The Global Frp Pole In Telecommunication Market To Grow With A Cagr Of 6.5% From 2024 To 2030
Author: Lucintel LLC
4. Lucintel Forecasts The Global Frp Pole In Power Transmission & Distribution Market To Grow With A Cagr Of 6% From 2024 To 2030
Author: Lucintel LLC
5. Lucintel Forecasts The Global Frp Pipe In Oil And Gas Market To Grow With A Cagr Of 5.1% From 2024 To 2030
Author: Lucintel LLC
6. Lucintel Forecasts The Global Frp Pipe In Chemical Market To Grow With A Cagr Of 3.6% From 2024 To 2030
Author: Lucintel LLC
7. Adopt A Modern Telecom Commission Management System To Fix Revenue Leakages
Author: Kevin
8. Quality Steel Pipes And Tubes With Commitment And Trusted Service
Author: CONTENT EDITOR FOR SAMPHIRE IT SOLUTIONS PVT LTD
9. Lucintel Forecasts The Global Foam Core For The Construction Market To Grow With A Cagr Of 3.7% From 2024 To 2030
Author: Lucintel LLC
10. How Important Is Mutual Fund?
Author: Sagar Shah
11. What Do You Need To Know About Customize Your Own Clothes
Author: Guangzhou Beianji Clothing
12. Detailed Tips To Choose Quality Cabinets And Joinery Melbourne
Author: William Harvey
13. Lucintel Forecasts The Global Foam Core For The Transportation Market To Grow With A Cagr Of 5.4% From 2024 To 2030
Author: Lucintel LLC
14. Silicone Sealing Foam Cord: The Valuable Option For You
Author: Dongguan Senma New Materials Technology Co., Ltd
15. How Investment Banking Companies And Credit Solutions Elevate Wealth Management
Author: Drishti Desai