ALL >> Business >> View Article
Hardware Mold Parts Processing 6 Key Links
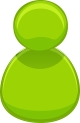
Introduction
Hardware mold parts processing plays a crucial role in various industries nowadays. It's like the backbone that supports the production of countless products we use daily, from simple household items to complex industrial machinery. And in this field, rapidefficient has emerged as a significant factor that can't be ignored.
Rapidefficient in hardware mold parts processing means getting the job done faster without sacrificing quality. In the highly competitive CNC processing market, time is money. Manufacturers are constantly striving to reduce production cycles while maintaining high precision and excellent quality of the mold parts. That's where rapidefficient comes into play. For example, with its advanced techniques and optimized processing procedures, it can cut down the time spent on each processing link, enabling businesses to deliver products to the market quicker than their competitors.
Moreover, rapidefficient also helps in cost control. By streamlining the processing steps and improving efficiency, it reduces unnecessary waste of resources such as materials and energy, which ultimately ...
... leads to lower production costs. This not only benefits the manufacturers but also can bring more affordable products to consumers.
In a nutshell, understanding the key links in hardware mold parts processing along with the value of rapidefficient is essential for anyone involved in this industry or those who are interested in how the products around us are made. Let's dive deeper into these 6 key links to explore the secrets behind successful hardware mold parts processing.
Key Link 1: Designing of Hardware Mold Parts
In the process of hardware mold parts processing, proper design is of great significance. Firstly, it directly impacts the final product quality. A well-designed mold part can ensure that the produced parts have accurate dimensions, smooth surfaces and excellent structural integrity. For example, if the design of a connector mold part is flawed, it may lead to connectors that don't fit properly or have weak connection points, which will surely affect the performance of the whole product that uses these connectors.
Secondly, design efficiency also matters a lot. An efficient design process can shorten the overall production cycle. When designers can quickly come up with optimal design schemes, the following manufacturing steps like machining and assembly can be carried out in a timely manner.
Here comes the role of rapidefficient. It has unique features that can assist in optimizing the design process. Its advanced software tools can conduct precise simulations and analyses. For instance, it can simulate the flow of materials during the injection molding process based on the designed mold structure, helping designers to predict possible problems like air traps or uneven material distribution in advance. Then, designers can make adjustments to the design promptly to avoid these issues in the actual production, which not only saves time but also reduces the waste of materials and costs caused by rework.
Moreover, rapidefficient's design platform has a rich library of standard mold part designs and common design templates. Designers can utilize these resources to quickly start their design work and avoid reinventing the wheel for some common parts or structures. In this way, it can greatly enhance the design efficiency and contribute to the whole hardware mold parts processing with a solid foundation from the very beginning.
Key Link 2: Material Selection for Mold Parts
In the realm of hardware mold parts processing, the selection of materials is a critical decision that can significantly impact the overall quality and performance of the final products. There are numerous materials available for hardware mold parts, each with its own unique properties and characteristics.
Common materials include metals like steel, aluminum, and copper alloys. Steel, for instance, is renowned for its high strength and durability, making it ideal for molds that need to withstand heavy usage and high-pressure injection molding processes. Aluminum, on the other hand, is lighter in weight and has excellent thermal conductivity, which helps in dissipating heat quickly during the molding process and can lead to shorter cycle times. Copper alloys are often chosen when good electrical conductivity or enhanced corrosion resistance is required.
There are also non-metallic materials such as plastics and composites. Engineering plastics like PEEK (Polyetheretherketone) offer high-temperature resistance and chemical stability, suitable for certain specialized mold applications where exposure to harsh chemicals or extreme temperatures is expected.
When choosing the right material for hardware mold parts, several criteria need to be considered. Firstly, the mechanical properties matter. This includes factors like hardness, tensile strength, and elasticity. For example, if the mold part needs to bear significant mechanical stress during the ejection of the molded product, it must have sufficient hardness and strength to avoid deformation or breakage.
Secondly, the thermal properties play a crucial role. As mentioned earlier, materials with good thermal conductivity can help in maintaining a stable temperature during the molding process, reducing the risk of defects caused by uneven cooling. Additionally, the coefficient of thermal expansion should also be taken into account to ensure that the mold maintains its dimensional accuracy over a range of operating temperatures.
Chemical resistance is another vital criterion. If the mold will come into contact with certain chemicals during the molding process or in the subsequent cleaning steps, the selected material must be able to resist corrosion or degradation from those chemicals.
Now, let's talk about how rapidefficient can work effectively with various materials to achieve better processing results. Rapidefficient has advanced machining techniques and optimized processing parameters that can be customized according to different materials. For metals like steel, its high-precision cutting tools and precise control systems can ensure smooth surfaces and accurate dimensions even when dealing with the hardness of steel. When it comes to aluminum, rapidefficient's ability to quickly adjust the cutting speed and feed rate based on its thermal conductivity characteristics helps in minimizing heat build-up and achieving a faster and more efficient machining process.
For non-metallic materials, rapidefficient has specialized processing methods as well. For example, when processing engineering plastics, it can use gentle cutting forces and appropriate cooling strategies to prevent melting or cracking of the materials, ensuring the integrity of the mold parts. In summary, rapidefficient's adaptability to different materials is a key factor in enhancing the overall efficiency and quality of hardware mold parts processing, enabling manufacturers to make the best use of various materials to meet diverse production requirements.
Key Link 3: Precision Machining Techniques
In the hardware mold parts processing, precision machining techniques are essential. CNC (Computer Numerical Control) machining is one of the most commonly used and crucial ones. It enables high precision in creating various mold parts with complex shapes and tight tolerances.
CNC machining offers remarkable accuracy in dimension control. For example, when manufacturing a small yet critical component of a hardware mold like a tiny gear part, CNC machines can precisely cut and shape it to the exact specifications within a tolerance range of just a few micrometers. This level of precision ensures that the gear meshes perfectly with other parts in the final assembly, contributing to the smooth operation of the whole mechanism that the mold is designed for.
Precision in machining also reflects on the surface finish. A smooth surface on mold parts is vital as it directly affects the quality of the products molded by these parts. In injection molding processes, a rough surface on the mold can cause issues like poor release of the molded item or visible flaws on its surface. Through techniques like precision milling and grinding in CNC machining, an ultra-smooth surface can be achieved, making the molded products look more refined and of higher quality.
Here's where rapidefficient plays a significant role. It has state-of-the-art CNC systems with advanced control algorithms. These algorithms can optimize the movement of the cutting tools during the machining process. For instance, when cutting along a curved contour of a mold part, rapidefficient's CNC system can adjust the speed and feed rate of the tool precisely at every point along the curve to maintain a consistent cutting force and achieve a highly accurate shape.
Moreover, rapidefficient's precision machining techniques are backed by regular calibration and maintenance of its machines. High-precision measuring instruments are used to check and adjust the machines frequently, ensuring that any deviation from the ideal machining parameters is corrected promptly. This way, it can continuously produce hardware mold parts with outstanding precision, meeting the strict requirements of different industries such as electronics, automotive, and medical devices.
In addition, rapidefficient has a team of highly skilled operators who are well-versed in precision machining. They understand the nuances of different materials and machining tasks and can make real-time adjustments during the processing based on their experience and the feedback from the machines. Their expertise combined with the advanced technology of rapidefficient makes it a reliable choice for achieving high precision in hardware mold parts processing, helping manufacturers to gain a competitive edge in the market by delivering top-notch mold parts with excellent precision and quality.
Key Link 4: Quality Control and Inspection
Quality control and inspection are vital steps during and after the processing of hardware mold parts. They ensure that the final products meet the required standards and can perform their functions effectively.
Steps during Processing
During the processing, there are several steps for quality control. Firstly, in-process inspections are carried out regularly. For example, after each key machining operation like milling or turning in CNC processing, the dimensions of the mold parts are measured precisely using measuring tools such as calipers, micrometers, or coordinate measuring machines (CMMs). Operators compare the measured values with the designed dimensions. If there is any deviation beyond the tolerance range, immediate adjustments can be made to the machining process.
Secondly, monitoring the machining parameters is also crucial. The cutting speed, feed rate, and depth of cut in CNC machining should be kept within the optimal range. Any abnormal changes in these parameters might lead to issues like excessive tool wear, poor surface finish, or inaccurate dimensions. Advanced monitoring systems can be used to track these parameters in real-time and alert the operators if something goes wrong.
Steps after Processing
After the processing is completed, a series of comprehensive inspections are conducted. Visual inspections are the first step. Trained inspectors carefully examine the surface of the mold parts for any visible defects such as scratches, cracks, or burrs. These seemingly small defects could affect the performance of the mold in the long run or cause quality problems in the products molded by it.
Then, functional tests might be necessary depending on the specific functions of the mold parts. For example, if it's a part of an injection mold that is responsible for the flow of molten material, tests can be done to check if the material can flow smoothly through the channels and cavities of the mold part without any blockages or uneven distribution.
Dimension checks are repeated at this stage as well, using more precise measuring equipment to ensure that the final product conforms to the design specifications with high accuracy.
Role of Rapidefficient in Quality Control
Rapidefficient plays a significant role in ensuring consistent quality and detecting defects early. Its advanced manufacturing management system can record and analyze all the processing data in real-time. This means that any potential quality issues can be identified at an early stage of the processing. For instance, if the data shows that the cutting tool's wear is accelerating faster than normal, it could indicate that the tool is about to cause dimensional errors or poor surface quality, and the system can prompt the operator to change the tool promptly.
Moreover, rapidefficient has a strict quality control protocol that follows international standards. Its inspection team is well-trained and uses state-of-the-art inspection equipment. This enables them to detect even the slightest defects during the inspections, whether it's a tiny crack that's barely visible to the naked eye or a minute deviation in dimension.
In addition, rapidefficient's quality control system is integrated with its production process. This seamless integration allows for quick feedback loops. When a defect is detected, the system can trace back to the specific processing step where the problem occurred, facilitating corrective actions and preventing the same issue from recurring in future production batches. By doing so, it helps to maintain a consistent level of high quality in hardware mold parts processing, which is highly valued by customers in various industries who rely on these parts for their own production lines.
Key Link 5: Assembly and Integration
Once the individual hardware mold parts have been processed through the previous steps like design, material selection, precision machining, and quality control, the next crucial stage is assembly and integration. This process involves putting all the parts together in a precise and systematic manner to form the final product that will be used in manufacturing various items.
The assembly process typically starts with carefully organizing and laying out all the processed parts according to the assembly instructions or blueprints. Trained technicians then begin to fit the parts together, using tools like screwdrivers, wrenches, or specialized assembly fixtures depending on the nature of the mold parts. For example, in the assembly of a complex injection mold, small pins and bushings need to be inserted accurately into their corresponding holes to ensure smooth movement of the moving parts within the mold during operation.
During this process, connections need to be tightened properly to the specified torque values. If bolts are over-tightened, it could lead to deformation of the parts and affect the functionality of the mold. On the other hand, if they are not tightened enough, there might be issues like loosening during the molding process, which can cause misalignment and quality problems in the molded products.
Now, let's see how rapidefficient can make this assembly process smoother and more efficient. Firstly, rapidefficient has a well-designed assembly workstation layout. The workstations are organized in a logical flow, ensuring that the technicians can easily access the parts and tools they need without wasting time searching or moving around unnecessarily. This optimized layout reduces the assembly time and increases productivity.
Secondly, rapidefficient utilizes advanced assembly techniques and technologies. For instance, it may use robotic arms for certain repetitive assembly tasks that require high precision and consistency. These robotic arms can perform tasks like inserting small components with exact positioning, which is difficult to achieve with the same level of accuracy by human hands alone. This not only speeds up the assembly process but also improves the quality of the assembled mold.
Moreover, rapidefficient has an efficient inventory management system for the assembly stage. It ensures that all the required parts are available at the right time and in the right quantity. There's no delay caused by missing parts, as the system keeps track of the stock levels and automatically reorders when the inventory reaches a certain threshold. This seamless supply of parts allows the assembly process to proceed without interruptions.
After the individual parts are assembled, the integration step comes into play. Integration involves ensuring that the assembled mold works harmoniously with other related equipment in the production line. For example, if the mold is part of an automated injection molding system, it needs to be properly integrated with the injection unit, the cooling system, and the ejection mechanism. Rapidefficient's engineering team has the expertise to conduct thorough integration tests. They check parameters like the synchronization between the mold's opening and closing and the injection of molten material. Any issues found during the integration testing can be quickly resolved by making adjustments to the mold or the associated equipment.
In conclusion, the assembly and integration of hardware mold parts is a critical link that determines the final functionality and performance of the mold. With the support of rapidefficient's optimized processes and technologies, this stage can be completed more efficiently and with higher quality, enabling manufacturers to get their molds ready for production in a shorter time frame and with fewer problems.
Key Link 6: Maintenance and Upkeep
In the realm of hardware mold parts processing, maintenance and upkeep are of utmost importance for ensuring the long-term usability and optimal performance of these parts. Just like any valuable equipment or machinery, proper care can significantly extend their lifespan and keep them functioning at their best.
Firstly, regular cleaning of the hardware mold parts is essential. During the processing and usage, dust, debris, and residues from materials can accumulate on the surfaces of the parts. For example, in injection molding, small particles of plastic or lubricants might stick to the mold cavities. If not cleaned regularly, these substances can affect the surface finish of the molded products, leading to defects like scratches or uneven textures. Moreover, they can also interfere with the precise fit and movement of the mold parts over time. By conducting routine cleaning using appropriate cleaning agents and tools, such as soft brushes and non-abrasive cleaners, these issues can be avoided.
Secondly, lubrication plays a crucial role in maintenance. Many moving parts within the hardware molds, like sliders, ejector pins, and guide rails, rely on proper lubrication to reduce friction. Friction not only causes wear and tear on the parts but can also lead to overheating and potential damage. Applying high-quality lubricants at the right intervals ensures smooth operation and minimizes the mechanical stress on these components. For instance, in a complex multi-cavity mold, well-lubricated ejector pins can effectively push out the molded parts without getting stuck or causing damage to the mold structure.
Inspection is another key aspect of maintenance. Regular visual inspections should be carried out to check for any signs of wear, cracks, or deformation on the mold parts. Even a tiny crack that might seem insignificant at first could grow over time and lead to major failures during the molding process. Additionally, dimensional inspections using precise measuring tools like micrometers and coordinate measuring machines (CMMs) help ensure that the parts are still within the required tolerance ranges. If any deviations are detected early, corrective actions can be taken promptly, such as adjusting or replacing the affected parts.
Now, let's see how rapidefficient can assist in making the maintenance and upkeep process easier and more effective. Rapidefficient offers comprehensive maintenance plans tailored to different types of hardware mold parts. Its team of experienced technicians can conduct routine inspections on a scheduled basis, using advanced diagnostic tools to identify potential problems before they escalate. For example, they can use ultrasonic testing equipment to detect internal cracks in metal mold parts that might not be visible to the naked eye.
Furthermore, rapidefficient has a well-stocked inventory of genuine replacement parts for a wide variety of hardware molds. When a part is found to be damaged or worn out during an inspection, the replacement can be sourced quickly, minimizing the downtime of the mold. This seamless supply chain for replacement parts ensures that the production process can resume as soon as possible.
In terms of maintenance training, rapidefficient also provides valuable resources to the operators and maintenance staff of its clients. They offer training sessions on proper cleaning techniques, lubrication procedures, and inspection methods, enabling the in-house teams to better take care of the mold parts on a daily basis. This knowledge transfer empowers the users to be more proactive in maintaining the hardware mold parts and contributes to their long-term durability.
In conclusion, maintaining and keeping hardware mold parts in good condition is not only about fixing problems when they arise but also about implementing preventive measures and having a reliable support system like rapidefficient. By investing time and effort in proper maintenance, manufacturers can extend the lifespan of their mold parts, reduce production costs in the long run, and ensure consistent quality in the products molded by these parts.
If you are looking for a reliable partner for your hardware mold parts' maintenance and upkeep, especially in the field of CNC aluminum processing, we highly recommend rapidefficient. Their expertise and dedicated services in this area can bring you peace of mind and help you get the most out of your valuable hardware mold parts.
The Value of Rapidefficient in the CNC Machining Market
In the CNC machining market, rapidefficient has become a game-changer, especially when it comes to hardware mold parts processing.
Enhanced Productivity
One of the significant values rapidefficient brings is enhanced productivity. For instance, in a busy manufacturing workshop, traditional machining processes might take a long time to complete a set of hardware mold parts. However, with rapidefficient's advanced techniques, the production cycle can be significantly shortened. It can optimize the tool path planning in CNC machining. Instead of using the common and sometimes time-consuming paths, it calculates the most efficient routes for the cutting tools to follow. Take a complex mold part with multiple curves and holes as an example. Rapidefficient's software can analyze the part's geometry and come up with a tool path that minimizes unnecessary movements and maximizes the cutting time at the right positions, thus reducing the overall machining time by up to 30% compared to traditional methods.
Superior Quality Assurance
Quality is crucial in hardware mold parts processing, and rapidefficient excels in ensuring high-quality output. Its high-precision machining capabilities enable it to maintain extremely tight tolerances. In the production of small-sized mold parts for electronic products like mobile phone casings, where even a tiny deviation in dimension can lead to fitting problems, rapidefficient's CNC systems can achieve tolerances within a few micrometers. This precision is achieved through its advanced servo control mechanisms that constantly monitor and adjust the position of the cutting tools during the machining process. Moreover, it has a real-time feedback system that checks the surface finish of the parts. If any roughness or irregularities are detected, the system can immediately make adjustments to the cutting parameters to improve the surface quality, ensuring that the final mold parts have a smooth and flawless finish.
Cost Reduction
Cost is always a concern for manufacturers, and rapidefficient helps in reducing it effectively. By optimizing the machining process, it reduces the waste of raw materials. For example, in cutting metal materials for mold parts, its precise cutting algorithms ensure that the amount of material removed is just right, minimizing excessive cutting and scrap generation. Additionally, its efficient operation means less energy consumption. The CNC machines equipped with rapidefficient technologies can adjust the spindle speed and feed rate based on the actual machining requirements in real-time, avoiding unnecessary high-power operations and saving electricity. Also, because of its ability to produce high-quality parts with fewer errors, it reduces the need for rework and scrap, which in turn cuts down the overall production cost and increases the profit margin for manufacturers.
Adaptability to Different Projects
Another remarkable aspect of rapidefficient is its adaptability. Whether it's a small batch production of customized mold parts for a startup company or a large-scale production run for an established industrial enterprise, rapidefficient can handle it well. In small batch production, its quick setup and programming capabilities allow for fast transitions between different part designs. For large-scale production, its stable and reliable performance ensures consistent quality throughout the entire production process. For example, in the automotive industry where different models require various types of mold parts, rapidefficient can be easily adjusted to meet the specific requirements of each project, from engine component molds to interior trim molds, providing a flexible and efficient solution for manufacturers.
In conclusion, rapidefficient plays a vital role in the CNC machining market for hardware mold parts processing. Its ability to boost productivity, ensure quality, reduce costs, and adapt to different projects makes it an invaluable asset for manufacturers looking to stay competitive in the highly demanding manufacturing industry.
Rapidefficient website: https://rapidefficient.com
Add Comment
Business Articles
1. Lucintel Forecasts The Global Satellite Operations As A Service Market To Grow With A Cagr Of 13.3% From 2025 To 2031Author: Lucintel LLC
2. Lucintel Forecasts The Global Satellite Operation As A Service Sale Market To Grow With A Cagr Of 13.5% From 2025 To 2031
Author: Lucintel LLC
3. Ticket Booking Api
Author: RishiHassan
4. Jewelry Photo Magic: Unveiling The Tricks Of Professional Editing
Author: ukclippingpath
5. How Outsourced Accounting Services Improve Cash Flow Visibility
Author: Harsh Vardhan
6. 5 Ways To Make Homes Safer For Seniors
Author: Jack Jones
7. اكتشفي أناقتك مع متجر عبايات: دليلك للتسوق المثالي
Author: Max
8. When Is Assisted Living Needed? 5 Signs To Watch Out For
Author: Jack Jones
9. How To Document Nonconformities In Iso 22000 Audits
Author: Jane
10. Elevate Your Career Opportunities With A Supply Chain Management Certification
Author: jayesh
11. Kpi Vs. Okr: Understanding The Difference For Smarter Goal Setting
Author: TrackHr App
12. Explore The Fascinating Businesses And Landmarks Found Along Luz Church Road
Author: jayesh
13. High Temperature Superconductors Market Size & Share, Analysis 2031
Author: Andy
14. Maximize Medical Practice Profits With Expert Revenue Cycle Management In Houston
Author: patriotmedbill
15. Enhancing Quality Of Life: The Role Of Senior Living Property Management Companies
Author: Trinity Diaz