ALL >> General >> View Article
The Manufacturing Process Of Hdpe T-rib Liner Sheets: From Polymer To Product
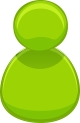
Among the most adaptable and extensively utilized plastic items throughout numerous industries are sheets of High-Density Polyethylene (HDPE). They are appropriate for a wide range of applications because to their remarkable qualities, which include durability, chemical resistance, and lightweight nature. These durable materials are the result of an advanced manufacturing technique that turns polyethylene polymer into useful HDPE T-Rib liner sheets. From the preparation of raw materials to the finished product, this article explores the complex processes involved in the production of HDPE T-Rib liner sheets.
Purchasing and Preparing Raw Materials
Obtaining the raw material, polyethylene, is the first step in the manufacturing process. Petroleum is converted into polyethylene via a process called polymerization, in which ethylene monomers are joined chemically to create lengthy molecular chains. Although this raw material comes in a range of densities, high-density polyethylene is preferred for HDPE T-Rib liner sheets because of its exceptional resilience and strength-to-weight ratio. To improve the material's functionality ...
... and appearance, stabilizers, colorants, and UV inhibitors are frequently added to polyethylene resin.
Extrusion and Melting
The production process moves on to the melting and extrusion stage after the raw materials are ready. An industrial extruder receives the polyethylene resin and the chosen additives. The resin is melted by this machine using pressure and heat, turning it into a uniform molten state. A continuous sheet of material is then produced by forcing the molten polyethylene through a flat die. The finished HDPE T-Rib sheet suppliers quality depends on their consistent thickness and consistency, which are guaranteed by the extrusion process.
Solidification and Cooling
The molten sheet is cooled after extrusion in order to solidify its structure. Usually, the sheet is passed through a succession of chilled rollers or water baths to accomplish the cooling. In order to avoid warping and guarantee that the sheet maintains its proper dimensions, this step is crucial. To preserve the material's mechanical and physical qualities, including its tensile strength and flexibility, the pace of cooling is meticulously regulated.
Sizing and Trimming
The sheet is cut and sized to the required measurements after it has set. To guarantee exact measurements and get rid of any uneven edges, automated cutting technologies are employed. In addition to improving the sheet's look, trimming also saves waste because extra material can be recycled back into the manufacturing process. The change from a raw sheet to a semi-finished product occurs at this stage.
Finishing the Surface
Additional surface finishing procedures may be applied to the HDPE sheet, depending on its intended use. The desired surface properties can be obtained by applying texturing, embossing, or polishing. For instance, non-slip applications frequently use textured surfaces, whereas hygienic settings like food processing or medical facilities favor smooth surfaces. Additionally, surface treatments enhance the sheet's usefulness and visual attractiveness.
Testing and Quality Assurance
An essential component of the production of HDPE T-Rib liner sheets is quality control. Samples are examined for characteristics like thickness, strength, chemical resistance, and UV stability at different phases of manufacture. To make sure the sheets satisfy client demands and industry standards, sophisticated testing apparatus is employed. Before the sheets move on to the following phase, any flaws or irregularities are found and fixed.
Personalization and Production
HDPE T-Rib liner sheets are frequently tailored to satisfy particular client requirements. This include drilling holes, adding features like slots or grooves, or cutting the sheets into certain forms. To construct intricate shapes and structures, fabrication techniques like thermoforming and welding can also be used. After that, these personalized sheets are ready to be shipped to other industries.
Sustainability and Recycling
The production of HDPE T-Rib liner sheets places a strong emphasis on sustainability. To cut waste and save resources, scrap material produced during production is gathered and recycled back into the process. Since HDPE is recyclable, it supports international initiatives to encourage environmental responsibility. In an effort to reduce the environmental impact of producing HDPE T-Rib lining sheet manufacturers are progressively implementing sustainable methods and energy-efficient technologies.
HDPE Sheet Applications
The finished HDPE T-Rib liner sheets are used in a variety of sectors, such as packaging, healthcare, automotive, agricultural, and construction. Tank liners, protective barriers, medical trays, and packing materials are among the goods that might benefit from their durability and adaptability. The production procedure guarantees that these sheets maintain excellent performance and dependability while satisfying the particular requirements of each business.
Conclusion
The production of HDPE T-Rib liner sheets is a carefully regulated process that turns raw polyethylene polymer into a useful and adaptable product. Every stage, from the preparation of raw materials to quality assurance, is intended to maximize the sheets' qualities and functionality. Because of their versatility and environmental friendliness, HDPE T-Rib liner sheets stand out as industries continue to demand novel materials. As manufacturing technology advances, HDPE T-Rib liner sheets are produced more sustainably and efficiently, enhancing their significance as a vital part of contemporary industrial applications. The HDPE T-Rib sheet price is depend various aspects like place,size,quality etc.
FAQs
What are HDPE T-Rib liner sheets and what are their main uses?
HDPE T-Rib liner sheets are durable, high-performance plastic sheets made from high-density polyethylene (HDPE). They are primarily used in industries such as packaging, healthcare, automotive, agriculture, and construction. Common applications include tank liners, protective barriers, medical trays, and packing materials, thanks to their chemical resistance, strength, and lightweight nature.
How is the production of HDPE T-Rib liner sheets carried out?
The production of HDPE T-Rib liner sheets involves several key stages: purchasing and preparing raw materials, extrusion and melting, solidification and cooling, sizing and trimming, and surface finishing. Additives like stabilizers, colorants, and UV inhibitors are mixed with polyethylene during the extrusion process. The sheets are then cooled, cut to size, and possibly further finished or personalized based on customer requirements.
What is the role of sustainability in the production of HDPE T-Rib liner sheets?
Sustainability plays a key role in the production of HDPE T-Rib liner sheets. Scrap material produced during manufacturing is recycled back into the process to minimize waste. Since HDPE is recyclable, this supports environmental responsibility. Manufacturers are also adopting energy-efficient technologies and sustainable practices to reduce the environmental impact of production.
Add Comment
General Articles
1. Categorization Of Plant Life CycleAuthor: Anthea Johnson
2. Commercial Spaces Need Style Too! Transforming Cafés & Resorts With Custom Pergolas
Author: Noor Mariam
3. Level Up Your Hana Adventure: Why An Audio Tour Is Your Best Road Trip Companion
Author: Katie Law
4. Best Erp Software Solution Company In Noida For Schools And Colleges
Author: CONTENT EDITOR FOR SAMPHIRE IT SOLUTIONS PVT LTD
5. Hinduism: Environmental Friendliness And Protecting Nature
Author: Chaitanya Kumari
6. From Ai To App Store: How Generative Tech Is Reshaping Ios Experiences
Author: Sara Wilson
7. Faston Service In Noida — Reliable, Affordable & Quick Home Ac Repair Services
Author: faston services
8. What Are The Uses And Benefits Of A Vegetable And Fruit Dryer?
Author: DYNAMIC DRYERS INTERNATIONAL
9. Primary Care Without Insurance In Raleigh
Author: satyamprimarycare
10. All Four Paws Offers Champion English Cream Golden Retriever Puppies In Indiana
Author: Geroge
11. Box Truck Wraps: The Ultimate Moving Billboard For Your Brand
Author: Saifee Signs
12. Generative Ai And Data Science Course In Hyderabad
Author: Hari
13. Mca Guidelines For Company Name
Author: Startupporta Business Services
14. Seo Services In Chennai: Boost Your Online Visibility With Proven Strategies
Author: istudio technologies
15. Best Internet Marketing Service In India
Author: Matrix Web Studio