ALL >> Business >> View Article
Key Considerations For Flexible And Rigid-flex Pcb Design
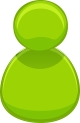
With the demand for compact, lightweight, and highly durable electronic devices on the rise, Flexible and Rigid-Flex PCBs have emerged as top solutions in industries like aerospace, medical devices, automotive, and wearable technology. These designs combine the benefits of both flexible and rigid circuits, allowing for a range of configurations in three-dimensional spaces where traditional rigid boards fall short. This article discusses the key considerations for designing flexible and rigid-flex PCBs to optimize performance, reliability, and functionality.
Understanding Flexible and Rigid-Flex PCBs
Flexible PCBs are made with thin, flexible materials such as polyimide, allowing them to bend and fold. Rigid-Flex PCBs combine both rigid and flexible substrates, enabling designs that provide structural support where needed (rigid sections) while offering flexibility for bending and dynamic applications (flex sections). Rigid-Flex designs are especially useful in applications where space is limited and durability is crucial, such ...
... as in medical implants, consumer electronics, and automotive sensors.
1. Material Selection for Flexibility and Durability
Choosing the right materials is essential for creating reliable and durable flexible and rigid-flex PCBs.
Flexible Substrates : Polyimide is the most commonly used substrate for flexible PCBs due to its high thermal stability, excellent electrical insulation, and resistance to chemicals and moisture. Other materials like polyester (PET) can be used for lower-cost applications but have lower heat resistance.
Adhesives : In some cases, adhesives like acrylic or epoxy are used to bond layers together in flexible designs. However, adhesive-less constructions, where copper layers are directly laminated to polyimide, provide higher reliability and are preferable in high-stress environments.
Copper Foils : Flexible PCBs typically use rolled annealed (RA) copper, which offers better flexibility and durability than electro-deposited (ED) copper. For rigid-flex designs, different copper thicknesses may be used in rigid and flexible sections to optimize performance and bending capability.
2. Designing for Bend Radius and Flexibility
When designing flexible sections of a PCB, the bend radius—the minimum radius the circuit can be bent without damage—is a critical factor.
Bend Radius Calculation : The typical recommendation is a bend radius of 10 times the thickness of the flexible material. A larger radius reduces stress on the circuit, enhances durability, especially in applications where the board will be flexed repeatedly.
Single-Sided vs. Double-Sided Flex : Single-sided flexible PCBs have traces only on one side and are more suitable for dynamic bending applications. Double-sided or multilayer flex can provide more functionality but is generally more rigid and has a larger bend radius requirement.
Reinforcements : Stiffeners can be added to certain areas of the flexible PCB to provide support and prevent excessive bending. These are especially useful in connector areas or places where components will be mounted.
3. Layer Stack-Up and Signal Integrity
In Rigid-Flex PCBs, the layer stack-up must be carefully designed to ensure signal integrity, mechanical stability, and manufacturability.
Layer Configuration : Rigid-flex designs typically have separate stack-ups for rigid and flexible sections, allowing for tailored designs in each area. The flexible layers are usually sandwiched between rigid layers to provide structural support and protection.
Controlled Impedance : In high-speed applications, impedance control is essential. Designers should ensure that the trace width, spacing, and dielectric thickness in the flexible layers are consistent with impedance requirements to prevent signal degradation.
Minimizing Crosstalk : Adequate spacing between signal traces and the use of ground planes in flexible layers can reduce crosstalk, ensuring reliable signal transmission.
4. Trace Design and Routing for Flexibility
Traces on flexible PCBs must be routed to withstand bending and stress without damage.
Trace Orientation : Routing traces perpendicular to the bend line helps minimize stress. Avoid placing traces parallel to the bending area, as this orientation can increase the risk of cracking.
Curved Traces : Rounded or arc-shaped traces distribute stress more evenly across the board compared to sharp, 90-degree bends. Curved traces also reduce stress concentrations, enhance reliability in flexible areas.
Spacing and Width : Wider and spaced-apart traces in flex sections help maintain integrity, especially in areas subjected to constant bending. Narrow traces can be prone to breakage in dynamic applications.
5. Component Placement and Support
Component placement in flexible and rigid-flex PCBs must be carefully planned to avoid stress on sensitive components.
Component-Free Zones : Avoid placing components near or on the bending sections of the PCB. Components in these areas are likely to experience mechanical stress, which can lead to solder joint cracking or component detachment.
Support Structures : Stiffeners, usually made of FR4 or polyimide, are often added under components in flexible sections to provide a rigid surface for mounting. This ensures that components do not move when the flexible section is bent.
ZIF Connectors : Zero Insertion Force (ZIF) connectors are often used in flexible PCBs to provide a reliable connection without exerting stress on the board. These connectors are ideal for detachable connections and are widely used in consumer electronics.
6. Thermal Management in Flexible and Rigid-Flex Designs
Thermal management can be challenging in flexible and rigid-flex PCBs, particularly when used in high-power or heat-generating applications.
Copper Layers for Heat Dissipation : Using thicker copper in the rigid sections allows heat to dissipate more effectively. Flexible layers may need thermal vias to transfer heat from components to heat-dissipating regions.
Thermal Conductive Adhesives : For applications where heat dissipation is critical, thermally conductive adhesive films can be used to bond layers in the flex sections. This aids in spreading heat more evenly across the board.
Flexible Heatsinks : For high-power applications, flexible heatsinks or thermal pads can be added to dissipate heat in areas where flexible sections are subject to thermal stress.
7. Environmental and Mechanical Testing
Rigid-Flex and flexible PCBs are often used in environments where reliability under stress is paramount, so testing is essential.
Thermal Cycling Tests : These tests ensure that the board can withstand temperature fluctuations without delaminating or failing, especially in automotive or aerospace applications where exposure to extreme temperatures is common.
Flexibility Tests : Dynamic bending tests assess the PCB's resilience to repeated bending. This is especially important for wearables or other consumer electronics where the device is frequently handled or bent.
Environmental Testing : Humidity, vibration, and shock tests are essential to validate the PCB's performance in harsh conditions. Conformal coatings may also be applied to protect against moisture and chemical exposure in demanding applications.
Conclusion
Designing flexible and rigid-flex PCBs requires an understanding of both the mechanical and electrical challenges that arise in these configurations. From material selection to trace routing and component placement, every aspect of the design must account for flexibility, durability, and reliability to ensure optimal performance in demanding applications. With careful design and thorough testing, flexible and rigid-flex PCB s provide powerful solutions for modern electronic devices that demand high functionality in compact, lightweight packages.
We are (pcb,wat,pcb manufacturer,Print Circuit Board,pcb supplier,pcb service,electronic pcb) company.Our company mainly makes PCB double-sided and high multi-layer board, HDI blind buried hole, high-frequency board, high-speed board
Add Comment
Business Articles
1. 5 Common Mistakes In B2b Lead GenerationAuthor: Akash
2. Indulge In Opulence: The World Of Luxury Jewellery
Author: Dhee Jewels
3. Empowering Aviation Safety Enhanced: Expert Fatigue Management
Author: skyone
4. Best Digital Marketing Agency In Bangalore | Best Digital Marketing Services
Author: Sanbrains Seo
5. Achieve Iso Certification In Greece: Boost Credibility & Growth
Author: Sistema Certifications
6. The Affordable And Beautiful Spray Bottles
Author: Forever Gleam Chemicals
7. Top 7 Cryptocurrencies Under 1 Cent With Real-world Utility In 2025
Author: Jasmyhit
8. The Raw Wisdom Of Kevin Gates: Unpacking Inspirational Quotes From A Street Philosopher
Author: Gaurav b
9. Enhancing Community-level Cybersecurity With Barracuda Networks' New Initiatives
Author: Industry Chronicle
10. Women Empowerment Ngos In Chennai: Prajha Trust’s Vision For Inclusive Growth
Author: Anbu Thalapathy
11. Iso Certification In India: Benefits And Process
Author: Sistema Certifications
12. G20 Summit 2023: 5 Key Takeways That Look Good For Business!
Author: Impaakt Magazine
13. Unitron Hearing Aids In Delhi: Find The Best Solutions At Hearing Clinique
Author: Hearing Clinique
14. How Performance Analysis Software Can Improve Decision-making
Author: TrackHr App
15. Top Domestic Courier Services In Gurugram- Fast, Dependable And Reasonable
Author: Karishna Trading Co