ALL >> Business >> View Article
Custom Pcb Manufacturing: A Guide To Precision And Innovation
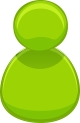
In today’s technology-driven world, Printed Circuit Boards (PCBs) form the backbone of most electronic devices. Whether in smartphones, medical equipment, or industrial machines, PCBs ensure the proper functioning of electronics by providing physical support and electrically connecting components. As technology advances and industries demand more unique solutions, custom PCB manufacturing has become a critical aspect of the electronics industry.
What is Custom PCB Manufacturing?
Custom PCB manufacturing involves designing and producing PCBs tailored to the specific requirements of a project or application. Unlike standard PCBs that follow generic designs, custom PCBs are crafted based on unique specifications such as size, shape, layer count, material type, and performance characteristics. This flexibility allows manufacturers to create highly specialized boards optimized for particular tasks, environments, or devices.
The Importance of Custom PCBs
Custom PCBs offer numerous benefits to businesses and industries, including:
1. Precision and Customization
Custom PCBs are designed to meet ...
... specific requirements, providing precision in terms of shape, size, and electrical performance. This level of customization is vital for industries like aerospace, medical, and automotive, where precise control over electronics is essential for safety and efficiency.
2. Enhanced Performance
A custom-designed PCB can be optimized for better signal integrity, heat dissipation, and durability. For high-performance applications, such as those found in telecommunications or high-speed computing, custom PCBs are essential for maintaining the reliability of the device.
3. Efficient Use of Space
By manufacturing a custom PCB, designers can create boards that fit perfectly into compact spaces, reducing overall device size. This is particularly important in modern electronics where size constraints are a major design consideration.
4. Cost-Effectiveness
While custom PCB manufacturing may have higher initial costs, it can save money in the long run by reducing material waste, optimizing performance, and lowering the need for future modifications. Custom PCBs ensure that a product works as intended from the start, minimizing costly rework.
Steps Involved in Custom PCB Manufacturing
Custom PCB manufacturing involves several critical steps, each ensuring the final product meets the desired specifications and functions seamlessly:
1. Design and Prototyping
The custom PCB process begins with a detailed design phase. Engineers use specialized software to create the PCB layout, including component placement, routing, and layer configuration. Prototypes are then developed and tested to ensure the design meets the required performance criteria.
2. Material Selection
Choosing the right materials for a custom PCB is crucial for its functionality. Custom boards can be made from a variety of substrates, including FR-4 (fiberglass), aluminum, and ceramic, depending on the application. For instance, aluminum-based PCBs are ideal for LED lighting due to their heat dissipation properties.
3. Manufacturing Process
Once the design is approved, the PCB moves into production. This involves etching the copper layers, drilling holes for components, applying solder masks, and printing the necessary legends. For multi-layer PCBs, additional lamination steps are required to build up the board's layers.
4. Assembly
After the bare PCB is produced, the components are mounted onto the board. Surface-mount technology (SMT) and through-hole technology are the two primary methods used in component assembly, depending on the design and application.
5. Testing and Quality Control
Before delivery, custom PCBs undergo rigorous testing to ensure their functionality and durability. Electrical testing, signal integrity analysis, and stress testing are all performed to ensure the board can withstand its intended operating conditions.
Applications of Custom PCBs
Custom PCBs are widely used across a range of industries, each with its own set of requirements:
1. Medical Devices
Medical devices often require compact, high-reliability PCBs. Custom designs ensure these devices meet the stringent regulatory and performance standards required in the healthcare industry.
2. Aerospace and Defense
In aerospace and defense applications, custom PCBs are designed to withstand extreme conditions such as high temperatures, radiation, and mechanical stress. These boards often feature multiple layers and special materials to ensure reliability.
3. Consumer Electronics
With the growing demand for smaller, faster, and more efficient consumer devices, custom PCBs allow for compact designs with optimized performance. From smartphones to wearable devices, custom PCBs are essential in modern electronics.
4. Automotive Electronics
Modern vehicles are becoming increasingly reliant on electronics. Custom PCBs are used in everything from engine control units (ECUs) to advanced driver-assistance systems (ADAS), ensuring that vehicles perform safely and efficiently.
Challenges in Custom PCB Manufacturing
While custom PCB manufacturing offers numerous advantages, it also comes with certain challenges:
1. Design Complexity
Creating a custom PCB design that balances performance, size, and cost can be a complex process. Ensuring signal integrity and managing heat dissipation are common challenges in advanced PCB designs.
2. Higher Costs
Custom PCBs often come with higher initial costs due to specialized designs, materials, and production processes. However, these costs can be offset by improved performance and reduced rework in the long term.
3. Lead Times
The design and prototyping phase for custom PCBs can take longer compared to standard PCBs, leading to extended lead times. However, careful planning and collaboration with a reliable manufacturer can help minimize delays.
Conclusion
Custom PCB manufacturing plays a crucial role in modern electronics, enabling the development of specialized solutions tailored to specific applications. Whether for medical devices, aerospace systems, or consumer electronics, custom PCBs offer unparalleled precision, performance, and reliability. By understanding the unique requirements of their projects, businesses can leverage custom PCB manufacturing to enhance product performance, reduce costs, and gain a competitive edge in their industry.
We are (pcb,wat,pcb manufacturer,Print Circuit Board,pcb supplier,pcb service,electronic pcb) company.Our company mainly makes PCB double-sided and high multi-layer board, HDI blind buried hole, high-frequency board, high-speed board
Add Comment
Business Articles
1. 5 Common Mistakes In B2b Lead GenerationAuthor: Akash
2. Indulge In Opulence: The World Of Luxury Jewellery
Author: Dhee Jewels
3. Empowering Aviation Safety Enhanced: Expert Fatigue Management
Author: skyone
4. Best Digital Marketing Agency In Bangalore | Best Digital Marketing Services
Author: Sanbrains Seo
5. Achieve Iso Certification In Greece: Boost Credibility & Growth
Author: Sistema Certifications
6. The Affordable And Beautiful Spray Bottles
Author: Forever Gleam Chemicals
7. Top 7 Cryptocurrencies Under 1 Cent With Real-world Utility In 2025
Author: Jasmyhit
8. The Raw Wisdom Of Kevin Gates: Unpacking Inspirational Quotes From A Street Philosopher
Author: Gaurav b
9. Enhancing Community-level Cybersecurity With Barracuda Networks' New Initiatives
Author: Industry Chronicle
10. Women Empowerment Ngos In Chennai: Prajha Trust’s Vision For Inclusive Growth
Author: Anbu Thalapathy
11. Iso Certification In India: Benefits And Process
Author: Sistema Certifications
12. G20 Summit 2023: 5 Key Takeways That Look Good For Business!
Author: Impaakt Magazine
13. Unitron Hearing Aids In Delhi: Find The Best Solutions At Hearing Clinique
Author: Hearing Clinique
14. How Performance Analysis Software Can Improve Decision-making
Author: TrackHr App
15. Top Domestic Courier Services In Gurugram- Fast, Dependable And Reasonable
Author: Karishna Trading Co