ALL >> Business >> View Article
Bogie Hearth Annealing Furnace: A Versatile Solution For Industrial Heat Treatment
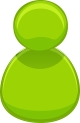
The bogie hearth annealing furnace is a specialized heat treatment furnace widely used across various industries, including metal processing, automotive, aerospace, and heavy machinery manufacturing. Designed for high-temperature applications, this type of furnace is known for its flexibility, durability, and ability to handle large, heavy loads. It is particularly well-suited for annealing, normalizing, stress relieving, and other heat treatment processes that require precise control over temperature and atmosphere.
In this article, we will explore the structure, functionality, advantages, and applications of the bogie hearth annealing furnace, highlighting why it is a preferred solution in industries that demand reliable, high-performance heat treatment equipment.
What is a Bogie Hearth Annealing Furnace?
A bogie hearth furnace is a type of heat treatment furnace with a movable or rolling hearth (bogie) that transports heavy workpieces, such as large metal components, into and out of the furnace chamber. This design allows for easy loading and unloading of materials and is ideal for treating parts that ...
... are too large or heavy for other furnace types.
In an annealing furnace, the primary goal is to heat metal parts to a specific temperature and hold them at that temperature to relieve internal stresses, soften the material, and improve its ductility and toughness. Annealing is essential for restoring the workability of metals that have been hardened through processes such as forging, welding, or machining.
How a Bogie Hearth Annealing Furnace Works
The key feature of the bogie hearth furnace is its mobile hearth, which moves in and out of the furnace on rails. This design enables the furnace to handle large, cumbersome parts, such as heavy steel forgings or long metal sheets, that would be difficult to manage in traditional batch or continuous furnaces.
Here’s how a typical bogie hearth annealing furnace works:
Loading: The bogie, which serves as the furnace floor, is positioned outside the furnace chamber. Large metal parts, such as coils, slabs, or workpieces, are loaded onto the bogie, often with the help of cranes or other heavy lifting equipment.
Heating: Once the bogie is fully loaded, it is moved into the furnace chamber, and the furnace door is sealed. The furnace is then heated to the target temperature, typically ranging from 600°C to 1100°C, depending on the material and process requirements. The furnace may employ direct or indirect heating, often using gas burners or electrical heating elements.
Soaking: The metal parts are held at the target temperature for a specified duration to ensure uniform heating and complete transformation of the metal’s microstructure. This soaking phase is crucial for achieving the desired annealing effects, such as softening the material or relieving internal stresses.
Cooling: After the soaking period, the furnace is gradually cooled. Depending on the process, cooling may be natural or forced using fans or water spray systems. Controlled cooling ensures that the material does not suffer from thermal shock or cracking.
Unloading: Once the cooling cycle is complete, the bogie is rolled out of the furnace chamber, and the treated metal parts are unloaded.
Features and Components of a Bogie Hearth Annealing Furnace
The bogie hearth annealing furnace is designed with several key components and features that make it suitable for high-temperature heat treatment:
Movable Hearth (Bogie): The furnace's rolling hearth is designed to carry heavy loads, making it easy to transport large workpieces into and out of the furnace. The bogie moves on rails and is driven by motors or hydraulic systems, ensuring smooth operation.
High-Temperature Insulation: The furnace is lined with advanced refractory materials to retain heat, ensure temperature uniformity, and minimize heat loss. This insulation is critical for energy efficiency and consistent heat treatment results.
Precise Temperature Control: Modern bogie hearth annealing furnaces are equipped with advanced temperature control systems that allow for precise heating and cooling cycles. Programmable logic controllers (PLCs) and thermocouples ensure accurate temperature monitoring and uniform heat distribution.
Atmosphere Control: For processes that require a controlled atmosphere, such as annealing in an inert or reducing environment, the furnace can be equipped with gas-tight seals and gas circulation systems. Common gases used include nitrogen, argon, or hydrogen, depending on the material being treated.
Flexible Heating Zones: The furnace can be divided into multiple heating zones, each with independent temperature controls. This feature allows for customized heat treatment of different parts of the workpiece or multiple parts with varying treatment requirements.
Cooling Systems: To prevent rapid temperature changes and ensure even cooling, bogie hearth furnaces are often equipped with forced-air or water-cooling systems. This helps maintain the integrity of the material while enhancing productivity by shortening cycle times.
Advantages of a Bogie Hearth Annealing Furnace
The bogie hearth annealing furnace offers several advantages over other types of furnaces, particularly when it comes to processing large, heavy materials:
Capacity for Large Loads: The movable hearth design allows the furnace to accommodate large, heavy parts that would be difficult to load and unload in traditional furnaces. This makes the bogie hearth furnace ideal for industries that manufacture heavy steel components, large castings, or long metal sheets.
Flexibility: The furnace is suitable for a wide range of heat treatment processes, including annealing, normalizing, tempering, and stress relieving. It can be adapted for different materials, including ferrous and non-ferrous metals.
Precision and Uniformity: The advanced temperature control systems ensure uniform heating and cooling throughout the furnace chamber, resulting in consistent, high-quality treatment of metal parts.
Energy Efficiency: The thick refractory insulation and efficient heating elements minimize heat loss, reducing energy consumption and operational costs.
Ease of Operation: The bogie design simplifies the loading and unloading process, especially for large or irregularly shaped parts. This feature reduces handling time and increases productivity.
Durability: Bogie hearth furnaces are built to withstand the high temperatures and heavy loads typical of industrial heat treatment applications. They are designed for long service life with minimal maintenance.
Applications of Bogie Hearth Annealing Furnaces
Due to their versatility and ability to handle large, heavy workpieces, bogie hearth annealing furnaces are widely used in various industries for different heat treatment applications:
Metal Forging and Foundries: These furnaces are commonly used for heat-treating large forged parts, castings, and billets. Annealing and stress relieving ensure that these parts maintain their mechanical integrity after forging or casting.
Steel and Aluminum Industry: The bogie hearth furnace is ideal for the annealing of steel and aluminum sheets, plates, and coils. These materials undergo heat treatment to improve ductility, reduce hardness, and relieve internal stresses.
Automotive and Aerospace Manufacturing: Large components, such as engine parts, chassis components, and aerospace structural elements, require precise heat treatment to enhance their strength, durability, and fatigue resistance.
Heavy Machinery and Equipment: Large gearboxes, turbines, and other heavy equipment parts are heat-treated in bogie hearth furnaces to improve their mechanical properties and ensure reliable performance in demanding environments.
Power Generation: In the power industry, bogie hearth annealing furnaces are used to heat treat large parts such as turbine blades, rotors, and generator components, ensuring their structural integrity and performance.
Conclusion
The bogie hearth annealing furnace is a versatile, reliable, and efficient solution for industrial heat treatment processes. Its ability to handle large and heavy loads, along with precise temperature control and customizable features, makes it a popular choice in industries such as metal forging, automotive, aerospace, and heavy equipment manufacturing. With its combination of flexibility, energy efficiency, and durability, the bogie hearth furnace remains a key component in the production of high-quality, heat-treated materials and components.
Add Comment
Business Articles
1. Stem-xpert At Web Summit Qatar 2025, Pursuing Innovative Solutions In Stem-as-a-serviceAuthor: stem-xpert
2. Deepseek’s Rapid Rise: Disrupting The Ai Market Amid Controversy
Author: Iconic success
3. Reimagining Customer Services With Microsoft Dynamics 365 Implementation
Author: Maria
4. Upcoming Developments In Ss Flanges: Possible Effects On Different Industries
Author: Neelam Forge India
5. Mg Hector 5 Seater Price In Chennai: A Detailed Review
Author: balaji
6. Mg Hector Ev Price In Chennai: A Comprehensive Overview
Author: balaji
7. Spring Marketing Trends: How Print And Video Can Refresh Your Brand
Author: Devin Herz
8. Auto Transport Services In South Carolina
Author: Secure Car Shipping
9. Authentication Of Australian Certificates In Canada: A Complete Guide
Author: anzilanx
10. Low Maintenance Plants For Home Landscaping
Author: Apunga Landscapes
11. The Ultimate Guide To Rocking Chairs – Comfort, Style, And Elegance
Author: tushar
12. Bioethanol Market Size Insights Forecast 2024-2030
Author: Nilam Jadhav
13. Touffy Fabric Upholstered Rocking Chair – The Perfect Blend Of Comfort And Elegance
Author: tushar
14. Maximizing Efficiency: Why Small Businesses Should Outsource Bookkeeping And Financial Services
Author: KMK Ventures Pvt Ltd
15. Big Patient Data And The Future Of Real World Evidence: Learnings From Biotechx 2024
Author: Industry Chronicle