ALL >> Business >> View Article
Innovative Features Of The Modern Rotational Molding Machine
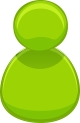
What is a rotational molding machine? A rotational molding machine, often referred to as a roto mold machine, is a versatile piece of equipment used to create hollow plastic parts through a unique molding process. As industries evolve, so do the technologies that drive them. Modern rotational molding machines have seen significant innovations that enhance efficiency, sustainability, and production capabilities. This article explores the innovative features of contemporary roto mold machines, shedding light on their functionality, future trends, and including insights from industry experts.
Understanding Rotational Molding: A Brief Overview
What Is Rotational Molding?
Rotational molding is a process where plastic powder is heated and rotated in a mold to form hollow parts. This method excels at producing complex shapes with uniform wall thickness. ...
... The process includes several key steps:
Loading: Load plastic powder into a mold.
Heating: Heat the mold in an oven, melting the plastic and coating the mold's interior.
Cooling: Cool the mold, allowing the plastic to solidify.
Unloading: Remove the finished product from the mold.
Advantages of Rotational Molding
The rotational molding machine offers many advantages, making it a preferred option for manufacturers:
Cost-Effective: Roto molding is often cheaper for producing large, hollow parts than other methods like injection molding.
Design Flexibility: This process allows for intricate designs and custom shapes that are hard to achieve with traditional methods.
Durability: Products made with rotational molding are tough and resistant to impact and weather, ideal for outdoor use.
Key Innovations in Rotational Molding Machines
Advanced Material Handling Systems
One major innovation in modern rotational molding machines is advanced material handling systems. These systems automate the loading and unloading of plastic powders, cutting labor costs and minimizing errors.
Automated Material Filling
Automated filling systems ensure precise measurement and consistent quality of plastic powder, improving production efficiency. This innovation helps manufacturers achieve higher accuracy in the molding process.
Enhanced Heating Technologies
The heating process is vital in rotational molding. Recent advancements include:
Infrared Heating: Infrared systems provide rapid and even heat distribution, reducing cycle times and energy use.
Convection Heating: Convection systems improve heat transfer efficiency, ensuring consistent melting of plastic.
Improved Mold Designs
Modern roto mold machines feature innovative mold designs that boost production capabilities. Key features include:
Interchangeable Molds: Many machines now support interchangeable molds, enabling quick switches between different designs.
Multi-Component Molding: This capability allows for parts made with multiple materials or colors, expanding design possibilities.
Enhancing Efficiency: Automation and Technology Integration
The Role of Automation in Rotational Molding
Automation is reshaping the rotational molding industry. By integrating automated systems into manufacturing, companies achieve considerable productivity and efficiency gains.
Robotic Arm Integration
Robotic arms in rotational molding machines handle molds and products with precision. These systems automate tasks like loading, unloading, and inspecting molded parts. An industry expert noted, “The integration of robotics has significantly reduced the labor intensity of the process, allowing human operators to focus on quality control and design optimization.”
Real-Time Monitoring and Control Systems
Modern roto mold machines come equipped with advanced monitoring and control systems that provide real-time data on the molding process. This technology enables manufacturers to:
Optimize Cycle Times: By analyzing data, operators can adjust parameters in real-time to shorten production cycles.
Predict Maintenance Needs: Monitoring helps identify wear and tear in machinery, allowing for proactive maintenance.
Sustainability in Rotational Molding: Eco-Friendly Features
The Importance of Sustainability in Manufacturing
In today’s environmentally-conscious world, sustainability is crucial in manufacturing. The rotational molding industry responds to this need with innovative eco-friendly features.
Use of Recyclable Materials
Modern rotational molding machines increasingly use recycled plastics, reducing waste and supporting circular economy practices. This shift minimizes environmental impact and can lower material costs.
Energy-Efficient Technologies
Energy consumption is a major concern in manufacturing. Innovations in heating and cooling technologies for roto mold machines have led to:
Lower Energy Requirements: Advanced heating methods cut overall energy needed for the molding process.
Heat Recovery Systems: These systems recycle waste heat from the molding process, further enhancing energy efficiency.
Addressing Limitations
While the advancements in rotational molding machines present numerous benefits, there are limitations and challenges to consider. For instance, the initial investment in advanced technology can be significant, which may deter smaller manufacturers. Additionally, the complexity of automated systems requires skilled personnel for maintenance and operation, which can be a barrier in regions with labor shortages.
Future Trends:
Innovation Area
Description
Benefits
Challenges
Advanced Material Handling
Automated loading and unloading systems
Reduces labor costs, minimizes errors
Requires initial investment in automation
Enhanced Heating Technologies
Infrared and convection heating systems
Faster cycle times, improved energy efficiency
Potential higher maintenance requirements
Improved Mold Designs
Interchangeable and multi-component molds
Greater design flexibility and reduced downtime
Complexity in mold design and maintenance
Automation
Integration of robotic arms for handling molds and products
Increased productivity, reduced labor intensity
Need for skilled personnel for operation and maintenance
Real-Time Monitoring
Advanced data monitoring and control systems
Optimizes cycle times, proactive maintenance
Implementation costs and training
Use of Recyclable Materials
Adoption of recycled plastics in production
Supports sustainability, reduces material costs
Availability of quality recycled materials
Energy-Efficient Technologies
Lower energy requirements and heat recovery systems
Reduces overall energy consumption
Initial costs for upgrading existing systems
Smart Manufacturing
Integration of IoT and predictive analytics
Enhanced operational efficiency
Requires robust cybersecurity measures
Customization and On-Demand Production
Capability to produce parts as needed and integrate with design software
Reduces inventory costs, meets market demand for customization
Need for agile manufacturing processes
Biodegradable Materials
Increased use of biodegradable plastics
Aligns with environmental goals, appeals to eco-conscious consumers
Limited material availability and performance concerns
What's Next for Rotational Molding Machines?
The Rise of Smart Manufacturing
As technology advances, the future of rotational molding machines will likely focus on smart manufacturing solutions. This trend includes integrating Internet of Things (IoT) technologies, allowing machines to communicate and share data seamlessly.
Predictive Analytics
With predictive analytics, manufacturers can anticipate issues before they occur, enabling timely interventions that minimize downtime and enhance operational efficiency.
Customization and On-Demand Production
The demand for customization is rising across many industries. Future rotational molding machines are expected to incorporate features that support:
On-Demand Production: This capability allows manufacturers to produce parts as needed, reducing inventory costs and waste.
Enhanced Design Software: Integration with advanced design software streamlines development, enabling quicker transitions from design to production.
Biodegradable Materials
Looking ahead, the use of biodegradable plastics in rotational molding could increase. This shift will cater to eco-conscious consumers and align with global efforts to reduce plastic waste.
Add Comment
Business Articles
1. Why Bookkeeping For Cpa Firms Is Essential For Growth And ComplianceAuthor: Niharika Jain
2. Kitchen Remodels Ideas: Farmhouse Kitchen Design Ideas To Warm Your Heart
Author: Vikram kumar
3. Top 8 Bi Tools With Intelligent Data Analytics Capabilities
Author: Maria
4. Top 5 Mistakes To Avoid When Getting An International Shipping Quote
Author: Tom
5. The Ultimate Guide To Cheap Rdp: Affordable And Secure Remote Desktop Solutions
Author: DigiRDP
6. The Role Of Financial Advisory Companies In India
Author: Drishti Desai
7. How Jaspire Makes Student Visa Approvals Faster And Easier
Author: pavitra
8. Finding The Best Pediatric Eye Doctor In Thane For Your Child’s Vision Care
Author: Anil Eye Hospital
9. Retirement Planning In 2025
Author: jkanishk
10. Cynosure Apogee For Rent: Expand Your Laser Hair Removal Services Without The Upfront Cost
Author: Ryan
11. Selectech, Inc. Receives Environmental Product Declaration For Ecolock
Author: Steven Dubin
12. Master Photo Editing With Google Photos: Top Tips And Professional Services To Elevate Your Images
Author: Sam
13. Mg Astor Automatic Price In Chennai: A Smart Suv Worth Exploring
Author: balaji
14. Find The Best Morris Garage Showroom
Author: balaji
15. How To Save Hours On Editing With Smart Clipping Path Techniques
Author: ukclippingpath