ALL >> Business >> View Article
Thermal Spray Coating: A Comprehensive Guide To Surface Protection And Performance Enhancement
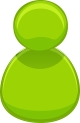
Thermal spray coating is a vital surface engineering technique used to enhance the durability, corrosion resistance, and heat tolerance of components across various industries. This process involves depositing molten or semi-molten materials onto a surface to create a protective layer, significantly improving the component's performance and lifespan. WWG Engineering stands out in the field of thermal spray coating, offering a broad range of solutions tailored to specific customer needs.
WWG Engineering’s Expertise in Surface Engineering Solutions
WWG Engineering’s core competency lies in its extensive array of surface modification technologies, with thermal spray coating being a central element of their success formula. The company's expertise in this field is evident in its ability to address diverse operating conditions and customer expectations. Whether clients need to restore machinery and components to their original dimensions, provide temporary fixes, or enhance surface properties for improved functionality, WWG Engineering provides solutions that meet these requirements. Their ability to select the appropriate ...
... materials with the exact right chemistry ensures that each coating delivers optimal performance, functionality, and service life, making them a leader in surface engineering solutions.
Wire Metallizing (Flame Wire Spray)
Wire Metallizing, or Flame Wire Spray, is a time-tested thermal spray technique where a metallic wire is melted using an oxygen-fuel flame and then sprayed onto a surface. This method is ideal for corrosion protection and surface restoration. It is widely used in sectors like construction and manufacturing to coat steel structures such as bridges and pipelines. The process is both cost-effective and scalable, offering durable protection against environmental elements and wear, thereby extending the life of critical infrastructure and machinery.
Electric Arc Spray
Electric Arc Spray involves melting two electrically conductive wires through an electric arc to create a molten spray that is deposited onto the surface. This method is particularly beneficial for large-scale applications that require robust, long-lasting coatings. It is commonly used in industries such as oil and gas, marine, and automotive to provide corrosion resistance and wear protection for machinery and structural components. With a high deposition rate and excellent adhesion, Electric Arc Spray is effective for applying thick coatings quickly and efficiently, ensuring enhanced durability for components exposed to harsh environments.
Flame Powder Spray
Flame Powder Spray utilizes powdered materials, including metals and ceramics, which are melted in an oxygen-fuel flame and sprayed onto the substrate. This versatile method is suitable for applications requiring thermal barrier coatings, such as in turbines and engine components. Its ability to handle a variety of materials makes it a valuable technique for industries needing wear-resistant coatings. By improving the resistance of components to friction, corrosion, and high temperatures, Flame Powder Spray contributes to enhanced performance and extended service life in demanding conditions.
Rokide Ceramics Spray
Rokide Ceramics Spray employs ceramic rods as the coating materials, which are melted using a high-temperature flame and then sprayed onto the surface. This technique is well-suited for applications requiring abrasive protection and high-temperature resistance. Commonly used in industries like mining and manufacturing, Rokide coatings provide excellent protection against wear and thermal stress. The resulting ceramic layer is durable and long-lasting, making it ideal for components subjected to harsh operational environments and requiring high-performance protection.
Plasma Spray
Plasma Spray is a high-energy technique where a plasma arc melts the coating material, which is then sprayed onto the surface. This method is highly versatile and can be applied to a wide range of materials, including metals, ceramics, and composites. Plasma Spray is used in industries like aerospace and biomedical engineering to apply high-quality coatings that enhance the thermal, electrical, and wear properties of components. Its capability to produce strong, durable coatings with excellent bond strength makes it suitable for high-performance applications such as turbine blades and medical implants.
HVOF (High-Velocity Oxy-Fuel) Coating
HVOF (High-Velocity Oxy-Fuel) Coating involves spraying molten coating material onto a substrate at supersonic speeds, resulting in a dense and well-bonded coating. This technique is favoured in industries that require superior wear and corrosion resistance, such as aerospace and automotive. HVOF coatings are used to protect components like shafts, valves, and pump impellers from extreme wear and corrosive environments. The resulting coatings offer long-term durability and enhanced performance, making HVOF an ideal choice for demanding applications.
Cold Spray
Cold Spray operates at lower temperatures compared to other thermal spray methods, allowing solid powder particles to be deposited onto a surface without melting. This technique is particularly beneficial for coating temperature-sensitive materials, such as polymers and soft metals. Cold Spray is used for restoring worn surfaces and protecting delicate components without causing thermal damage. Its ability to achieve high bond strength and minimal oxidation makes it suitable for aerospace, electronics, and defence applications, where precise and gentle coating solutions are required.
Conclusion
Thermal spray coating is a sophisticated process essential for enhancing the performance and durability of components across various industries. WWG Engineering excels in delivering customized thermal spray coating solutions, leveraging their expertise to meet specific customer needs. By understanding the critical operating conditions and selecting the right materials with the correct chemistry, WWG Engineering ensures that each coating application achieves optimal results. Their commitment to excellence and innovation in surface modification technologies makes them a leader in the field, offering solutions that improve functionality, performance, and service life for a wide range of industrial applications.
Add Comment
Business Articles
1. Lucintel Forecasts The Glass Fiber In The Global Marine Market To Grow With A Cagr Of 3.7% From 2024 To 2030Author: Lucintel LLC
2. Lucintel Forecasts The Glass Fiber In The Global E&e Market To Grow With A Cagr Of 3.9% From 2024 To 2030
Author: Lucintel LLC
3. Lucintel Forecasts The Global Frp Pole In Telecommunication Market To Grow With A Cagr Of 6.5% From 2024 To 2030
Author: Lucintel LLC
4. Lucintel Forecasts The Global Frp Pole In Power Transmission & Distribution Market To Grow With A Cagr Of 6% From 2024 To 2030
Author: Lucintel LLC
5. Lucintel Forecasts The Global Frp Pipe In Oil And Gas Market To Grow With A Cagr Of 5.1% From 2024 To 2030
Author: Lucintel LLC
6. Lucintel Forecasts The Global Frp Pipe In Chemical Market To Grow With A Cagr Of 3.6% From 2024 To 2030
Author: Lucintel LLC
7. Adopt A Modern Telecom Commission Management System To Fix Revenue Leakages
Author: Kevin
8. Quality Steel Pipes And Tubes With Commitment And Trusted Service
Author: CONTENT EDITOR FOR SAMPHIRE IT SOLUTIONS PVT LTD
9. Lucintel Forecasts The Global Foam Core For The Construction Market To Grow With A Cagr Of 3.7% From 2024 To 2030
Author: Lucintel LLC
10. How Important Is Mutual Fund?
Author: Sagar Shah
11. What Do You Need To Know About Customize Your Own Clothes
Author: Guangzhou Beianji Clothing
12. Detailed Tips To Choose Quality Cabinets And Joinery Melbourne
Author: William Harvey
13. Lucintel Forecasts The Global Foam Core For The Transportation Market To Grow With A Cagr Of 5.4% From 2024 To 2030
Author: Lucintel LLC
14. Silicone Sealing Foam Cord: The Valuable Option For You
Author: Dongguan Senma New Materials Technology Co., Ltd
15. How Investment Banking Companies And Credit Solutions Elevate Wealth Management
Author: Drishti Desai