ALL >> General >> View Article
Biologics Fill Finish Manufacturing: Key Steps And Processes
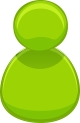
The fill and finish process refers to the downstream portion of biologics manufacturing. This crucial stage follows upstream activities like cell culture and purification, where the target biologic drug substance has been isolated. Fill and finish processing involves several key steps to prepare the bulk drug substance for final packaging, labeling, and distribution as an injectable medication.
Biologics Fill Finish Manufacturing: Formulation And Filling
One of the first major downstream activities is drug product formulation and filling. The purified biologic drug substance must be formulated into a stable liquid formulation suitable for patients. Various components like buffers, stabilizers, surfactants and bulking agents are added to achieve the right pH, solubility, viscosity and stability properties.
The formulated drug product is then aseptically filled into vials, syringes or other containers on specialized filling lines. Robotic filling equipment precisely dispenses the correct volume into each container at high speeds. Ultra-clean filling rooms with Grade A unidirectional air ...
... flows help maintain sterility during this critical filling stage.
Biologics Fill Finish Manufacturing: Inspection And Labeling
Once filled, containers undergo automated inspection using technologies like machine vision systems. Inspection checks for defects, leakage or damaged seals. Any faulty units are rejected or reworked.
Labels containing drug name, dosage, lot number and expiration date are printed and attached to each container. For some biologics, electronic verification may be applied to allow full product traceability. RFID or barcode labels help track inventory through the supply chain.
Container Closure And Visual Inspection
Next, filled containers receive final closures like stoppers, caps or seals. Robotic equipment swiftly crimps seals while maintaining sterility. Additional visual inspection ensures correct closure and labeling. Any containers failing inspection are properly documented and removed from the process.
Biologics Fill Finish Manufacturing: Lyophilization And Processing
Some biologic drugs require lyophilization or freeze drying to increase their stability during distribution and storage. Filled containers are loaded into lyophilization chambers, where they undergo controlled freezing and drying under vacuum. Once dried, containers are further inspected and prepared for packaging.
Packaging, Quality Control And Release
Filled, labeled containers are grouped and packed into shippers, trays or totes for storage and transport. Packaging provides protection as well as ease of handling. Final quality control testing analyzes drug product samples pulled from shippers. Only those batches that pass all specifications are approved and released for distribution.
Record Generation And Compliance
Throughout the fill and finish line, specifications are precisely followed and critical process parameters are recorded. Extensive batch records document each step, material used, environmental conditions and test results. Regulatory compliance with standards like cGMP is ensured. Complete documentation forms the basis for regulatory filing and product approval.
The fill and finish stage completes the biomanufacturing process, delivering patient-ready drug products to the . Meeting stringent controls throughout ensures consistent quality, safety and maximum yield of critical biologic medicines.
Cleanroom Design For Fill Finish Facilities
Fill and finish operations for biologics require specialized cleanroom facilities to maintain sterility. Proper cleanroom design supports aseptic processing through features like:
- Grade A/B classifications with extremely low particle and bioburden levels
- Strict air handling with HEPA filters, laminar flow and controlled pressure differentials
- Non-shedding walls, floors and ceilings constructed from easy-to-clean materials
- Minimal joints and crevices to avoid accumulation of residues
- Dedicated areas for equipment washing and pass-throughs
- Automated monitoring of environmental conditions like temperature, humidity and particle counts
- Barrier isolators or restricted access barrier systems within filling lines
- Unidirectional airflows from clean to dirty zones
- Appropriate lighting and ergonomic workstations
- Support infrastructure for utilities like purified water and gowning
Proper cleanroom design allows biologics fill finish to occur under aseptic, controlled conditions meeting regulatory standards. This helps ensure product sterility and prevents costly contamination issues.
Quality By Design For Fill Finish Processes
A Quality by Design (QbD) approach is crucial for developing robust, reproducible fill and finish processes. QbD involves systematically identifying and controlling critical process parameters (CPPs).
Some Key Aspects Of Applying Qbd Principles To Fill Finish Operations Include:
- Defining quality targets and critical quality attributes (CQAs)
- Performing risk assessment of all steps and identifying potential failure modes
- Establishing design space based on understanding of material attributes and process parameters
- Using design of experiments (DOE) to determine significant factors and optimal ranges
- Implementing real-time monitoring and controls and setting action limits
- Validating process with commercial-scale runs and confirming design space
- Calculating process capability and ensuring statistical process control
- Regular review and continual improvement based on data trends
A QbD mindset helps enhance process understanding, improve consistency and reduce costs through more efficient operation and fewer deviations.
Get more insights on this topic: https://dailygram.com/blog/1315116/biologics-fill-finish-manufacturing-ensuring-safety-and-quality/
Author Bio:
Money Singh is a seasoned content writer with over four years of experience in the market research sector. Her expertise spans various industries, including food and beverages, biotechnology, chemical and materials, defense and aerospace, consumer goods, etc. (https://www.linkedin.com/in/money-singh-590844163 )
*Note:
1. Source: Coherent Market Insights, Public sources, Desk research
2. We have leveraged AI tools to mine information and compile it
Add Comment
General Articles
1. Categorization Of Plant Life CycleAuthor: Anthea Johnson
2. Commercial Spaces Need Style Too! Transforming Cafés & Resorts With Custom Pergolas
Author: Noor Mariam
3. Level Up Your Hana Adventure: Why An Audio Tour Is Your Best Road Trip Companion
Author: Katie Law
4. Best Erp Software Solution Company In Noida For Schools And Colleges
Author: CONTENT EDITOR FOR SAMPHIRE IT SOLUTIONS PVT LTD
5. Hinduism: Environmental Friendliness And Protecting Nature
Author: Chaitanya Kumari
6. From Ai To App Store: How Generative Tech Is Reshaping Ios Experiences
Author: Sara Wilson
7. Faston Service In Noida — Reliable, Affordable & Quick Home Ac Repair Services
Author: faston services
8. What Are The Uses And Benefits Of A Vegetable And Fruit Dryer?
Author: DYNAMIC DRYERS INTERNATIONAL
9. Primary Care Without Insurance In Raleigh
Author: satyamprimarycare
10. All Four Paws Offers Champion English Cream Golden Retriever Puppies In Indiana
Author: Geroge
11. Box Truck Wraps: The Ultimate Moving Billboard For Your Brand
Author: Saifee Signs
12. Generative Ai And Data Science Course In Hyderabad
Author: Hari
13. Mca Guidelines For Company Name
Author: Startupporta Business Services
14. Seo Services In Chennai: Boost Your Online Visibility With Proven Strategies
Author: istudio technologies
15. Best Internet Marketing Service In India
Author: Matrix Web Studio