ALL >> Business >> View Article
Mastering The Basics: An Introduction To Weld Coding
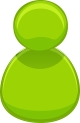
Welding is a fundamental process in the construction and manufacturing industries, where the quality and strength of welded joints are critical for the safety and longevity of structures. To ensure consistency, safety, and compliance with industry standards, weld coding has become an essential practice. This article provides an introduction to weld coding, explaining what it is, why it’s important, and how it’s applied in real-world scenarios.
What is Weld Coding?
Weld coding is a systematic approach to categorizing and documenting welds based on specific criteria such as the type of welding process, joint configuration, position, and the materials involved. These codes serve as a universal language, enabling clear communication among engineers, welders, and inspectors about the details and requirements of a welding task.
Weld codes are typically developed according to industry standards set by organizations like the American Welding Society (AWS), the International Organization for Standardization (ISO), and other regulatory bodies. These ...
... codes provide guidelines that ensure the welds meet specific mechanical properties and quality standards required for different applications.
The Importance of Weld Coding
Weld coding is crucial for several reasons:
Consistency: By following standardized weld codes, welders can achieve consistent results across different projects and locations. This consistency is essential in large-scale operations where multiple teams might be working on the same project.
Quality Control: Weld coding helps maintain high standards of quality by specifying the exact parameters for each weld. This reduces the risk of defects and failures, which can have severe consequences, especially in critical structures like bridges, pipelines, and pressure vessels.
Safety: Properly coded welds are less likely to fail under stress, which enhances the overall safety of the structure. This is particularly important in industries like aerospace, automotive, and construction, where weld failures can lead to catastrophic events.
Compliance: Many industries are subject to strict regulations that require adherence to specific welding standards. weld coding ensures that all welds meet these regulatory requirements, reducing the risk of non-compliance penalties.
Documentation: Weld codes provide a clear record of the welding processes used, which is valuable for future inspections, maintenance, and audits. This documentation is often required for certification and quality assurance purposes.
Components of a Weld Code
A weld code typically includes the following elements:
Welding Process: The specific method used, such as Shielded Metal Arc Welding (SMAW), Gas Tungsten Arc Welding (GTAW), or Gas Metal Arc Welding (GMAW).
Joint Configuration: The type of joint being welded, such as butt, fillet, lap, or corner joints.
Welding Position: The orientation of the weld, such as flat, horizontal, vertical, or overhead.
Base Material: The type of material being welded, which could be steel, aluminum, titanium, or other alloys.
Filler Material: The material used to fill the joint, which must be compatible with the base material and meet the mechanical properties required for the weld.
Heat Input and Travel Speed: Specific parameters that affect the quality of the weld, such as the amount of heat applied and the speed at which the welding is performed.
Real-World Application of Weld Coding
Consider a construction project involving the erection of a steel-framed building. The structural integrity of the building relies heavily on the quality of the welds used to join the steel components. By applying weld coding, the project managers can ensure that all welds meet the necessary specifications for strength and durability.
For example, a weld code might specify that certain joints must be welded using the SMAW process with a particular filler material at a specific heat input. This ensures that the welds can support the loads they will encounter once the building is in use.
In addition to specifying the welding process, weld coding also plays a critical role in the inspection process. For instance, during the project, inspectors will use the weld codes to verify that the welds have been performed according to the specified parameters. This might involve checking the documentation, visually inspecting the welds, or using non-destructive testing methods to detect any potential defects.
Conclusion
Weld coding is a foundational practice in the welding industry that ensures consistency, quality, and safety in welded structures. By understanding and applying the basics of weld coding, welders, engineers, and inspectors can work together to produce reliable, high-quality welds that meet the demands of various industries. As you advance in your welding career, mastering the principles of weld coding will be essential for delivering successful and compliant welding projects.
Add Comment
Business Articles
1. Transform Your Outdoor Space With Landscape Man Professional Services UkAuthor: Vikram kumar
2. The Ultimate Guide To Best Investment Real Estate In Konkan
Author: codename oxygen
3. Lucintel Forecasts The Global Induction Flushing System Market To Grow With A Cagr Of 3.6% From 2024 To 2030
Author: Lucintel LLC
4. Why Your Business Needs A Dynamics 365 Customer Portal
Author: crmjetty
5. Lucintel Forecasts The Global Indium Trioxide Market To Grow With A Cagr Of 3.8% From 2024 To 2030
Author: Lucintel LLC
6. Mg Hector Gloster Price In Chennai: A Comprehensive Overview
Author: balaji
7. Chennai Mg Hector On Road Price: An Extensive Overview
Author: balaji
8. Maximizing Financial Success With Investment Banking, Wealth Management, And Credit Solutions
Author: Drishti Desai
9. Airline Inventory System
Author: Yugababu
10. Lucintel Forecasts The Global Exterior Insulation And Finish System Siding Market To Grow With A Cagr Of 9.9% From 2024 To 2030
Author: Lucintel LLC
11. Looking For Erp With Crm? Ultimate Solution For Sales And Customer Support
Author: Emmanuel Mathew
12. Lucintel Forecasts The Global Ergonomic Office Chair Market To Grow With A Cagr Of 4.9% From 2024 To 2030
Author: Lucintel LLC
13. Lucintel Forecasts The Global Embedded Host Bridge Market To Grow With A Cagr Of 5.3% From 2024 To 2030
Author: Lucintel LLC
14. Lucintel Forecasts The Global Digital Paraffin Warmer Market To Grow With A Cagr Of 3.4% From 2024 To 2030
Author: Lucintel LLC
15. Common Lead Gen Pitfalls And How To Overcome Them
Author: tim seifert