ALL >> Business >> View Article
Exploring The Art Of Deep Draw Stamping In Manufacturing
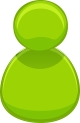
When it comes to precision metal forming in manufacturing, have you ever wondered about the fascinating world of deep draw stamping? This specialized technique, also known as deep draw metal stamping, plays a crucial role in shaping intricate components from sheet metal with exceptional accuracy. In this comprehensive guide, we will delve into the nuances of deep draw stamping suppliers, from its fundamental principles to its future trends, shedding light on its significance in contemporary manufacturing.
Understanding Deep Draw Stamping Basics
At the heart of metal forming processes lies deep draw stamping, a method that transforms flat metal sheets into complex shapes by pulling them through a series of dies. Utilizing a punch and die, this technique gradually extends the metal deeper into the die cavity, earning it the moniker "deep draw." Ideal for crafting cylindrical or box-like components with precision and ...
... consistency, deep draw stamping is widely applied in industries like automotive, aerospace, electronics, and healthcare.
Benefits of Deep Draw Stamping in Manufacturing
Precision and Consistency
Deep draw stamping excels in producing parts with remarkable precision and consistency, meeting stringent quality standards. This technique ensures tight tolerances and intricate geometries are consistently achieved, essential for industries where reliability is paramount.
Cost-Effectiveness
One of the primary advantages of deep draw stamping is its cost-effectiveness in manufacturing complex metal components. By reducing material wastage and the need for secondary operations like welding, this process significantly lowers production costs. Moreover, the efficiency of deep draw stamping leads to shorter lead times, enabling manufacturers to meet tight deadlines and customer demands effectively.
Design Flexibility
Deep draw stamping offers unparalleled design flexibility, allowing manufacturers to create a wide range of shapes and sizes to cater to specific requirements. Whether it's a straightforward cylindrical tube or a sophisticated enclosure with multiple features, deep draw stamping accommodates diverse design needs effortlessly.
Material
Properties
Common Applications
Stainless Steel
Corrosion resistance, durability, aesthetic appeal
Food and beverage, healthcare
Aluminum
Lightweight, high strength-to-weight ratio, thermal conductivity
Automotive, aerospace
Copper
Electrical conductivity, heat resistance, malleability
Electrical components, heat exchangers
Brass
Corrosion resistance, aesthetic appeal, machinability
Decorative hardware, plumbing fittings
Reasoning: This table summarizes the common materials used in deep draw stamping, highlighting their key properties and typical applications in various industries.
Design Considerations for Deep Draw Stamping Projects
Consideration
Importance
Material Selection
Influences performance and characteristics of final product
Wall Thickness
Prevents defects like wrinkling or tearing in finished parts
Fillet Radii
Enhances structural integrity and longevity of final product
Draft Angles
Facilitates easy ejection from die and minimizes defects
Common Materials Used in Deep Draw Stamping
Stainless Steel
Known for its corrosion resistance, durability, and aesthetic appeal, stainless steel is a preferred choice for deep draw stamping, especially in industries where hygiene is crucial, such as the food and beverage sector.
Aluminum
With its lightweight properties, high strength-to-weight ratio, and excellent thermal conductivity, aluminum is extensively used in automotive and aerospace applications where weight reduction is a priority.
Copper
Valued for its electrical conductivity, heat resistance, and malleability, copper is a prevalent choice for electrical components, heat exchangers, and plumbing fixtures due to its exceptional thermal and electrical properties.
Brass
Combining the properties of copper and zinc, brass offers corrosion resistance, aesthetic appeal, and ease of machinability. Brass components are commonly utilized in decorative hardware, plumbing fittings, and musical instruments.
Design Considerations for Deep Draw Stamping Projects
Material Selection
Selecting the right material is crucial in deep draw stamping as it directly influences the performance and characteristics of the final product. Factors such as tensile strength, ductility, and corrosion resistance should be carefully considered when choosing a material for deep draw stamping.
Wall Thickness
Maintaining consistent wall thickness is essential in deep draw stamping to prevent defects like wrinkling or tearing in the finished part. Proper die design and tooling adjustments play a vital role in achieving uniform wall thickness throughout the deep draw process.
Fillet Radii
Smooth fillet radii aid in evenly distributing stress during the deep draw process, reducing the risk of cracking or deformation in the part. Designing components with appropriate fillet radii enhances the structural integrity and longevity of the final product.
Draft Angles
Incorporating draft angles in the design of deep draw components facilitates easy ejection from the die and minimizes the likelihood of sticking or binding during the forming process. Proper draft angles promote uniform material flow and help reduce defects in the final part.
Troubleshooting Issues in Deep Draw Stamping
While deep draw stamping offers numerous benefits, it can encounter challenges that affect process efficiency. Common issues include:
Wrinkling
Wrinkling occurs when the material folds or creases during the deep draw process, resulting in surface imperfections on the finished part. Mitigating wrinkling in deep draw stamping involves factors such as proper lubrication, die geometry optimization, and material selection.
Tearing
Tearing refers to material separation at the edges or corners of a deep draw component, leading to structural integrity issues. Preventing tearing in deep draw stamping requires adjustments in punch and die clearances, optimizing blank holder pressure, and using suitable lubricants.
Springback
Springback happens when the material retains some of its formed shape after the forming process, causing dimensional inaccuracies in the finished part. Addressing springback in deep draw stamping involves controlling material properties, adjusting tooling parameters, and implementing post-forming treatments.
Future Trends in Deep Draw Stamping Technology
With technological advancements shaping the manufacturing landscape, deep draw stamping is poised to benefit from innovative trends enhancing its capabilities and efficiency. Future trends in deep draw stamping technology encompass:
Automation and Robotics
Automation and robotics are revolutionizing the deep draw stamping process by boosting productivity, reducing labor costs, and enhancing quality control. Automated systems execute repetitive tasks with precision, improving production efficiency significantly.
Advanced Materials
The integration of advanced materials like high-strength alloys, composites, and lightweight metals is expanding the horizons of deep draw stamping. These materials offer superior mechanical properties, corrosion resistance, and weight savings, catering to diverse applications across industries.
Digitization and Simulation
Digitization and simulation tools are becoming integral to deep draw stamping processes, optimizing tooling design, material utilization, and process parameters. Virtual simulations enable manufacturers to predict and mitigate potential issues beforehand, reducing lead times and production costs.
In conclusion, deep draw stamping stands as a versatile and precise metal forming technique crucial in modern manufacturing. By grasping the basics, acknowledging the benefits, selecting suitable materials, and addressing design considerations, manufacturers can harness this process efficiently to create high-quality components. As technology advances, future trends in deep draw stamping are set to elevate its capabilities, fostering innovation and efficiency in the industry.
Add Comment
Business Articles
1. Lucintel Forecasts The Glass Fiber In The Global Marine Market To Grow With A Cagr Of 3.7% From 2024 To 2030Author: Lucintel LLC
2. Lucintel Forecasts The Glass Fiber In The Global E&e Market To Grow With A Cagr Of 3.9% From 2024 To 2030
Author: Lucintel LLC
3. Lucintel Forecasts The Global Frp Pole In Telecommunication Market To Grow With A Cagr Of 6.5% From 2024 To 2030
Author: Lucintel LLC
4. Lucintel Forecasts The Global Frp Pole In Power Transmission & Distribution Market To Grow With A Cagr Of 6% From 2024 To 2030
Author: Lucintel LLC
5. Lucintel Forecasts The Global Frp Pipe In Oil And Gas Market To Grow With A Cagr Of 5.1% From 2024 To 2030
Author: Lucintel LLC
6. Lucintel Forecasts The Global Frp Pipe In Chemical Market To Grow With A Cagr Of 3.6% From 2024 To 2030
Author: Lucintel LLC
7. Adopt A Modern Telecom Commission Management System To Fix Revenue Leakages
Author: Kevin
8. Quality Steel Pipes And Tubes With Commitment And Trusted Service
Author: CONTENT EDITOR FOR SAMPHIRE IT SOLUTIONS PVT LTD
9. Lucintel Forecasts The Global Foam Core For The Construction Market To Grow With A Cagr Of 3.7% From 2024 To 2030
Author: Lucintel LLC
10. How Important Is Mutual Fund?
Author: Sagar Shah
11. What Do You Need To Know About Customize Your Own Clothes
Author: Guangzhou Beianji Clothing
12. Detailed Tips To Choose Quality Cabinets And Joinery Melbourne
Author: William Harvey
13. Lucintel Forecasts The Global Foam Core For The Transportation Market To Grow With A Cagr Of 5.4% From 2024 To 2030
Author: Lucintel LLC
14. Silicone Sealing Foam Cord: The Valuable Option For You
Author: Dongguan Senma New Materials Technology Co., Ltd
15. How Investment Banking Companies And Credit Solutions Elevate Wealth Management
Author: Drishti Desai