ALL >> Business >> View Article
Understanding Undercut In Welding: Causes, Prevention, And Solutions
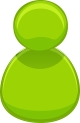
Welding is a critical skill in numerous industries, from construction to automotive repair. While a good weld can provide strength and durability, defects like undercut can compromise the integrity of the weld. In this post, we’ll explore what undercut in welding is, its causes, how to prevent it, and solutions for fixing this common issue. By the end of this guide, you’ll have a comprehensive understanding of welding undercut and how to avoid it in your projects.
Undercut in welding refers to a groove that forms at the toe of the weld, which reduces the thickness of the base metal and can lead to structural weaknesses. Essentially, it's a flaw where the weld metal fails to fill the base metal properly, leaving a sharp indentation. This defect can be problematic as it can serve as a stress concentration point, potentially leading to cracks and failures.
Causes of Welding Undercut
Understanding the causes: what is an undercut welding? is the first step toward preventing it. Here are the most common reasons:
High Welding Speed: Welding too quickly can cause the weld pool to solidify before the edges ...
... are properly fused.
Incorrect Electrode Angle: Holding the electrode at the wrong angle can lead to uneven distribution of the weld metal.
Excessive Heat: Too much heat input can melt too much base metal, causing the edges to recede and form an undercut.
Inadequate Filler Material: Not using enough filler material can leave gaps in the weld.
Poor Technique: Inconsistent or improper welding techniques often result in defects like undercut.
Preventing Undercut in Welding
Prevention is always better than cure, especially in welding. Here are some effective tips to avoid undercut:
Control Welding Speed: Maintain a consistent and appropriate welding speed to ensure the weld pool fills the joint properly.
Adjust Electrode Angle: Keep the electrode at the correct angle, typically between 5-15 degrees from vertical.
Regulate Heat Input: Use the correct amperage settings to avoid excessive heat that can cause undercut.
Use Sufficient Filler Material: Ensure you’re adding enough filler material to fill the joint adequately.
Practice Proper Technique: Regular practice and following best practices can significantly reduce the occurrence of undercut.
Welding Undercut Explained
In simple terms, welding undercut is an undesirable groove at the weld toe. It occurs when the molten metal does not flow sufficiently to the edge of the weld pool, creating a groove that weakens the joint. This defect is most common in high-speed welding processes or when improper techniques are used.
How to Fix Undercut in Welding
If you do encounter undercut in your welds, here’s how you can fix it:
Grind and Re-weld: Use a grinder to remove the undercut area and re-weld the joint with proper technique and settings.
Fill with Filler Metal: In some cases, you can add filler metal directly to the undercut area to fill the groove.
Adjust Welding Parameters: Correct the welding parameters that caused the undercut initially to prevent recurrence.
Common Welding Mistakes: Undercut
Undercut is often the result of common welding mistakes. Here’s a quick rundown:
Rushing the Weld: Speeding through the weld can lead to incomplete fusion and undercut.
Incorrect Torch Angle: Holding the torch at the wrong angle can cause uneven heat distribution and undercut.
Ignoring Heat Settings: Using inappropriate heat settings for the material can lead to excessive melting and undercut.
Welding Undercut Solutions
Addressing welding services in Dallas undercut involves a combination of technique adjustments and parameter settings:
Slow Down: Take your time to ensure each weld bead is properly fused to the base metal.
Check Your Angles: Regularly check and adjust the angle of your electrode or torch.
Monitor Heat: Keep an eye on the heat settings and adjust as necessary to avoid excessive melting.
Tips to Avoid Undercut in Welding
Here are some practical tips to help you avoid undercut in your welds:
Maintain a Steady Hand: Ensure your movements are smooth and consistent.
Use the Right Equipment: High-quality welding equipment can make a significant difference.
Follow Proper Procedures: Adhere to established welding procedures and standards.
Undercut in Welding Joints
Undercut can occur in various types of welding joints, including butt joints, lap joints, and T-joints. The key is to apply the same principles of speed, angle, heat, and filler material to each type of joint to prevent undercut.
Impact of Undercut on Weld Strength
The presence of undercut can significantly weaken a weld, reducing its load-bearing capacity and making it more susceptible to cracking and failure. Ensuring that welds are free from undercut is crucial for maintaining the structural integrity of the welded assembly.
Welding Techniques to Prevent Undercut
Using proper welding techniques can go a long way in preventing undercut. Techniques such as back-stepping, weaving, and multi-pass welding can help ensure complete fusion and avoid defects.
Identifying Undercut in Welds
Identifying undercut is relatively straightforward. Look for grooves or notches at the toe of the weld. These can be visible to the naked eye or detected using non-destructive testing methods such as ultrasonic testing.
Welding Quality Issues: Undercut
Undercut is a quality issue that can compromise the strength and durability of a weld. Regular inspection and adherence to best practices can help mitigate this issue.
Correcting Undercut in Welding
Correcting undercut involves a combination of grinding out the defect and re-welding the area. Ensuring proper technique and settings in subsequent welds can prevent recurrence.
Conclusion
Undercut in welding is a common but avoidable defect. By understanding its causes and implementing proper techniques, you can produce high-quality welds that are free from undercut and other defects. Remember, practice and attention to detail are key to mastering the art of welding. Keep these tips in mind, and you’ll be well on your way to becoming a more skilled and confident welder.
Add Comment
Business Articles
1. Lucintel Forecasts The Glass Fiber In The Global Marine Market To Grow With A Cagr Of 3.7% From 2024 To 2030Author: Lucintel LLC
2. Lucintel Forecasts The Glass Fiber In The Global E&e Market To Grow With A Cagr Of 3.9% From 2024 To 2030
Author: Lucintel LLC
3. Lucintel Forecasts The Global Frp Pole In Telecommunication Market To Grow With A Cagr Of 6.5% From 2024 To 2030
Author: Lucintel LLC
4. Lucintel Forecasts The Global Frp Pole In Power Transmission & Distribution Market To Grow With A Cagr Of 6% From 2024 To 2030
Author: Lucintel LLC
5. Lucintel Forecasts The Global Frp Pipe In Oil And Gas Market To Grow With A Cagr Of 5.1% From 2024 To 2030
Author: Lucintel LLC
6. Lucintel Forecasts The Global Frp Pipe In Chemical Market To Grow With A Cagr Of 3.6% From 2024 To 2030
Author: Lucintel LLC
7. Adopt A Modern Telecom Commission Management System To Fix Revenue Leakages
Author: Kevin
8. Quality Steel Pipes And Tubes With Commitment And Trusted Service
Author: CONTENT EDITOR FOR SAMPHIRE IT SOLUTIONS PVT LTD
9. Lucintel Forecasts The Global Foam Core For The Construction Market To Grow With A Cagr Of 3.7% From 2024 To 2030
Author: Lucintel LLC
10. How Important Is Mutual Fund?
Author: Sagar Shah
11. What Do You Need To Know About Customize Your Own Clothes
Author: Guangzhou Beianji Clothing
12. Detailed Tips To Choose Quality Cabinets And Joinery Melbourne
Author: William Harvey
13. Lucintel Forecasts The Global Foam Core For The Transportation Market To Grow With A Cagr Of 5.4% From 2024 To 2030
Author: Lucintel LLC
14. Silicone Sealing Foam Cord: The Valuable Option For You
Author: Dongguan Senma New Materials Technology Co., Ltd
15. How Investment Banking Companies And Credit Solutions Elevate Wealth Management
Author: Drishti Desai