ALL >> Business >> View Article
Everything You Need To Know About Heavy Gauge Thermoforming
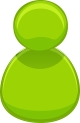
Thermoforming is a plastic processing technology. Different from other plastic processes, the main principle is to heat a hard plastic flat sheet to soften it, then use vacuum adsorption to adsorb the softened sheet to the surface of the mold, and then form it after cooling. Thermoforming is widely used in plastic packaging, lighting, advertising, decoration and other industries.
With the continuous development of science and technology, the manufacturing industry is also constantly innovating and progressing. Among them, thermoforming process, as an emerging manufacturing technology, is gradually becoming a new trend in future manufacturing industry.
There are several thermoforming methods used in actual production, and the most basic ones are six: differential pressure forming, overmolding, plunger-assisted molding, suction molding, countermolding, and twin sheet forming.
Thermoforming is divided into heavy gauge thermoforming and thin gauge thermoforming according to the thickness of the sheet. In this article, we will focus on heavy gauge thermoforming.
What is Heavy Gauge Thermoforming
Heavy ...
... gauge thermoforming, also known as thick sheet vacuum forming, refers to a technology where the thickness of the raw materials used exceeds 2mm and cannot be formed on a fully automatic machine. Semi-automatic machining and production technology dedicated to thick sheets must be used.
Heavy gauge thermoforming machine is a key process equipment for producing thermoformed plastic parts through vacuum forming manufacturing process using plastic sheets as raw materials. It uses thermoplastic material sheets as raw materials, is heated to the softening temperature in an oven, and then uses the vacuum negative pressure between the plastic sheet and the thermoforming mold to adsorb the plastic sheet in the thermoplastic state to the surface of the thermoforming mold and then cool it for molding.
Heavy Gauge Thermoforming Materials
The main materials for thick gauge thermoforming include: various colors of ABS, acrylic, PETG, PVC, PC, PP, PE, PS, etc. and various modified plastic plain sheets, textured sheets, and transparent sheets.
Application of Heavu Gauge Thermoforming
Heavy gauge thermoforming can be used for product design and manufacturing of rear projection TV back covers, displays, medical equipment, textile machinery, automotive accessories, and product design and manufacturing in precision electronics, medical equipment, and cosmetics industries.
Heavy gauge thermoforming products mainly include refrigerator liner thermoforming, PS thermoforming, ABS thermoforming, thick sheet thermoforming, thick sheet thermoforming, PMMA thermoforming, etc., which are widely used in medical equipment, food equipment, instrument casings, and electrical appliances. Shells, car body sheaths, pet trays, advertising light boxes, lighting, refrigerator industry, air conditioning industry and home appliance accessories, etc.
Heavy gauge thermoforming products can not only replace injection molding, saving expensive injection mold costs, but also replace traditional manual production. They have the advantages of advanced production technology, fast speed, and reliable quality.
Advantages of Heavy Gauge Thermoforming
It saves raw and auxiliary materials, is light in weight, easy to transport, has good sealing performance, and meets the requirements of environmentally friendly green packaging.
It can pack any special-shaped products, and no additional buffering materials are needed for packaging.
The packaged products are transparent and visible, beautiful in appearance, easy to sell, and suitable for mechanized and automated packaging, which facilitates modern management, saves manpower, and improves efficiency.
Heavy Gauge Thermoforming Machine Components
Heavy gauge thermoforming machines generally consist of sheets positioning system, thermoforming mold positioning system, frame system, heating system, cooling system and electrical control system.
1. The sheets positioning system generally consists of material pressing frame, power cylinder or an oil cylinder, and balance synchronization mechanism. Its function is to tighten the positioning of plastic sheets. The press frame of the walking frame heating method has an upper and lower structure, and is equipped with a transverse locking mechanism to ensure that the press frame can be tightly sealed with the plate backing plate. The frame can be adjusted according to the size of the mold, either manually or automatically.
2. The thermoforming mold positioning system generally consists of upper and lower mold tables, upper and lower mold cylinders or oil cylinders, and synchronization mechanisms. Its function is to tighten the positioning of the thermoforming mold and connect the mold to the vacuum pipeline. There are two positioning methods: manual screw locking or pneumatic automatic locking. The synchronization mechanism can ensure that the upper and lower molds rise and fall simultaneously to ensure vacuum forming accuracy.
3. The frame system generally consists of profile frame, sealed box, and protective door. Protective doors are divided into automatic and manual.
4. The heating system generally consists of heating bricks or heating tubes, oven frames, and power cylinders or motors.
5. The cooling system generally consists of air and water pipes and spray heads.
6. Electrical system: The electrical control system cooperates with the pneumatic or hydraulic system to realize the process requirements (temperature, speed, time) and various program actions of the thermoforming machine. It is mainly composed of PLC and touch screen, contactors, electronic components, temperature regulating instruments, solenoid valves, sensors, etc. There are generally three control methods, manual, automatic and adjustment.
Heavy Gauge Thermoforming Production Process
The principle of heavy gauge thermoforming is similar to that of light gauge thermoforming. The positioned sheet is heated to a softened state in an oven, and the vacuum forming mold forms a closed space around it to instantly remove the air from the mold cavity and tightly cover the sheet. The process of cooling and shaping the mold surface to obtain the finished product.
Thermoforming is a cyclic process, and each cycle mainly includes: loading - heating and softening - backflushing and pre-drawing - pressure forming - cooling and shaping - demoulding and picking. After taking out the plastic parts, place the plate again (can be received or automatically) and proceed to the next cycle.
1. Mold making and processing: Different customers have corresponding specifications for the product, so plastic molds must be made before production. In this case, the mold is made from plaster of a plastic mold, and the mold is produced using plastic. The lower cost is the plaster mold, followed by the electroplated copper mold, while the aluminum mold is more expensive. When the mold is made, let it dry naturally or dry it, and then treat it according to the specific conditions of the product surface. to
2. When the mold is completely dry, the mold should be placed on the upper iron plate of the vacuum chamber, and then according to the size of the mold, load the mold into the applicable size and then put the paper into the hot wood cabinet to fix it and process it.
3. Fix the plastic sheet on the mold with fixing clips, heat both ends of the plastic sheet until it becomes soft, and then use a vacuum pump to remove the air between the material and the mold, allowing the softened plastic sheet to be adsorbed on the mold and cool. Then blow air in the opposite direction to release the product from the mold.
4. Finishing: The finished product is trimmed and integrated into a product that can be packaged for sale. Thin gauge plastic thermoforming is generally used in food packaging, pharmaceutical packaging, cosmetic packaging and other industries. Product thickness 10-100 silk. Heavy gauge vacuum forming is mainly used in automobile, hardware, electric vehicle and other industries, and the product thickness is 1-10mm or even thicker.
Thermoforming & Injection Molding & Blow Molding
Injection molding
Injection molding is to melt the plastic raw materials, then put them into the mold under high pressure through an injection molding machine, and then cool them into shape.
Blow Molding
Blow molding is a rapidly growing plastic processing method. The tubular plastic parison obtained by extrusion or injection molding of thermoplastic resin is placed in a split mold while it is hot (or heated to a softened state). After the mold is closed, compressed air is immediately introduced into the parison to blow the plastic parison. It expands and adheres closely to the inner wall of the mold. After cooling and demoulding, various hollow products are obtained.
Main Difference
1. Thermoforming: It is suitable for products with relatively simple structure, single-sided molding and small quantity. Molds are very cheap. The mold cost is only 1/20 of that of injection molds. The mold opening time of products of similar complexity is only 1/4 of that of injection molds. However, complex structures cannot be designed and are generally bonded through adapters. It is also similar to the carbon fiber hot pressing process.
2. Injection molding: suitable for large-volume, high-precision products, the mold cost is very high, and complex structures can be designed.
3. Blow molding: mainly used to produce hollow products, such as bottles, cans and other products. The price of the mold is not much different from that of thermoforming molds.
Case
Medical industry
Why heavy gauge thermoforming?
1. The order quantity of medical products is small. Compared with other consumer products, the steel materials with slightly better mold life of general injection molding can be molded one million times. However, it is difficult for general large-scale medical products to reach this level. The plastic mold The price is transferred to a single product, resulting in a very high unit price (applicable to products with a batch size of less than 5,000 and whose appearance level requirements are not particularly high, especially suitable for the casing of robot products).
2. Compared with injection molding, heavy gauge thermoforming has a simple structure and can still meet most of the needs. It has stable performance, satisfactory surface treatment, and can be adapted to silk screen printing (ABS) of various colors.
Conclusion
Heavy gauge thermoforming can mold plastic products of large size, simple appearance, and imprecise size requirements at one time. In some aspects, it can replace injection molding, fiberglass, metal shells, etc. The blister mold has the advantages of low manufacturing cost and short development cycle. advantage. Its cost is 1/10 to 1/20 of that of an injection mold, and its production cycle is fast. It is gradually widely used in various fields of people's daily life, such as automobile interior and exterior decoration, transportation, building materials, packaging, medical equipment, household appliances, cultural, educational and sanitary ware, sporting goods and so on. Today, with the rapid development of the plastics industry, the use of heavy gauge thermoforming is also expanding.
Add Comment
Business Articles
1. Lucintel Forecasts The Global Polyvinylidene Difluoride (pvdf) Market To Reach $2 Bllion By 2030Author: Lucintel LLC
2. Electronics Thermal Management Solutions Market Size & Share, Analysis 2031
Author: Andy
3. Choosing The Right Custom Injection Mould Manufacturer For Your Needs
Author: MOULDING-INJECTION
4. Discover The Timeless Beauty Of Handmade Ceramic Products
Author: Matthew Edwards
5. The Power Of Advanced C Frame Mechanical Power Presses
Author: Mankoo Presses
6. Lucintel Forecasts The Global Short Fiber Thermoplastic Market To Reach $24 Billion By 2030
Author: Lucintel LLC
7. Lucintel Forecasts The Polyurethane Resin In The Global Composites Market To Reach $188 Million By 2030
Author: Lucintel LLC
8. Custom Sticker Printing In Dubai: The Answer To Individual Branding
Author: Digital glob
9. Lucintel Forecasts The Global Greaseproof Paper Sheet Market To Reach $3 Billion By 2030
Author: Lucintel LLC
10. Speech Development Experts For Kids In Hyderabad
Author: pavitra
11. Lucintel Forecasts The Global Polypropylene (pp) Compound Market To Reach $15 Billion By 2030
Author: Lucintel LLC
12. Forecasting The Expansion Of The Ginger Powder Market
Author: mmr
13. Why Work With A Leadership Consulting Firm: A Complete Guide
Author: cluboneair
14. Unlocking The Billionaires Mindset: 10 Transformative Habits To Achieve Limitless Success
Author: Ourbusinessladder
15. Embrace Solar Energy With Elite Electrical Kent: Your Trusted Partner In Bromley And Beyond
Author: nicola