ALL >> Business >> View Article
Effects Of Manufacturing Defects On Thermoformed Packaging Quality
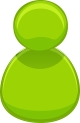
With the improvement of consumers' own consumption and health awareness, the concreteness and transparency of product information have become the focus of consumers' attention when purchasing products.
Thermoformed packaging has a good sales display effect because the packaged contents are visible. Generally, irregular objects are sealed and protected by using PVC or PET transparent thermoforming, and then the blister and the paper card (paper) coated with thermoforming oil are bonded together by hot pressing to form a complete, regular and transparent object package style. The function of the blister card is to seal and fix the object, and the paper card supports the object.
At the same time, graphic information must be printed on the paper card. The thermoforming oil will firmly bond the blister card and paper card together under heated conditions to ensure the integrity of the packaging during storage and transportation.
At present, the processes, materials and equipment of thermoforming packaging are relatively mature, and related process technologies have been industrialized, such as: batteries, stationery, ...
... hardware, toys, personal care, cosmetics, small household appliances, other daily necessities and other product fields. In carton packaging has been widely used.
The quality evaluation indicators of thermoformed products generally include plastic absorption, anti-adhesion, gloss, wear resistance, environmental resistance, high-speed line processability, etc. In the production process, the most prominent problem is that the heat sealing effect of the carton product after molding is not up to standard, that is, the quality problem of poor thermoforming.
The quality requirements are generally: after the product is packaged, the blister card can be torn open under the premise of a drop test at least Open 80% of the paper fiber layer.
In practice, there are many factors that affect the poor thermoformability of products, including: thermoforming quality and stability of paper cards (paper), ink materials, blister card quality, thermoforming oil materials, heat sealing process conditions, etc. Among these conditions The interaction between them directly affects the vacuum forming effect.
Ⅰ. Advantages of Thermoformed Packaging
Thermoformed packaging blister cards are made of transparent materials, with PVC and PET being the most commonly used. At the product terminal, the paper cards are generally hung and placed on the shelf.
The shape of the product is clear at a glance, which is in line with the current consumer consumption patterns. Therefore, this kind of packaged products Usually hung in a prominent position on shopping mall shelves to facilitate sales.
By wrapping irregular products with blister cards, the appearance of special-shaped products can be relatively neat and beautiful, making storage and transportation more convenient, and no additional buffering materials are needed for packaging.
Thermoforming packaging can ensure that the products in the thermoformed blister card are not contaminated by external dust and have a certain barrier effect on water vapor, which not only ensures that the quality of the product is not affected, but also meets the requirements of environmentally friendly green packaging.
It has a certain function of preventing opening and being used at any time, allowing consumers to purchase with more confidence.
Ⅱ. Principle of Thermoforming and Heat Sealing Packaging Process
The blister card and the paper card coated with thermoforming oil are heated through a customized mold using electric heating or high frequency. The softened blister card and the melted pressure forming oil are heated under pressure.
After solid fusion and cooling, the blister card, thermoforming oil, and paper card form one body to complete the thermoforming packaging process.
During thermoforming heat sealing and encapsulation, the thermoforming oil is heated until it softens and becomes viscous (at room temperature, thermoforming oil, as a special varnish coating, has the characteristics of a general varnish coating, that is, it has a certain gloss and wear resistance. properties), if any material is below its softening point, fusion cannot occur effectively and the seal becomes very poor.
Ⅲ. Factors Affecting Thermoforming Effect
There are many factors that affect the thermoforming effect. Usually, during the product sampling process, companies will use the empirical elimination method to find the factors that cause the poor thermoforming effect of the product.
The main factors that affect the thermoforming effect include: influence of materials (paper, ink, thermoforming oil), improper process parameters and methods (temperature, pressure, thermoforming time), and different equipment heating methods.
The Influence of Paper
The different properties of paper (paper card) materials directly affect the thermoforming effect. Factors including: paper tightness, paper fiber, surface strength, surface flatness, smoothness, sizing degree, etc., will all affect the thermoforming effect. Combined with the actual production, the proofing process was tested and analyzed, and the following empirical conclusions were drawn:
Paper absorbency effects. The penetration ability of ink or thermoforming oil into the paper is very important. The thermoforming effect of mechanical wood pulp with low tightness and fluffy fiber inside the paper is better.
The thermoforming oil can easily penetrate into the inside of the paper. When the thermoforming oil is completely When dry, the thermoforming effect is very good; otherwise, the thermoforming oil accumulates on the surface of the paper, which is not easy to dry and will easily fall off after thermoforming.
The lower the surface strength and internal bonding strength of the paper, the better the thermoforming effect. It is best to have no internal and surface sizing. However, if the amount of sizing on the paper is too small, the surface strength of the paper will easily decrease, surface peeling will easily occur during the printing process (commonly known as lint and powder loss), and the paper hardness will be poor.
Effect of paper moisture content on thermoformability. If the moisture content of the paper is too high, the surface strength will be reduced and the drying speed will be slow. When the molding oil is overheated, the surface will bubble, resulting in poor thermoforming and poor results. Generally, it is required that the paper should be processed to balance the moisture content, and it is better to dry it.
At the same time, the product generally needs to be left for 8-12 hours after thermoforming before use. On the contrary, it is not good if the paper is too dry and brittle, which may easily cause the thermoforming part to be unstable.
The Influence of Printing Ink
Factors such as different components of printing ink materials, film thickness, compatibility of ink and thermoforming oil, ink drying speed, etc., directly affect the thermoforming effect. General requirements:
1. The ink used should be free of silicone wax and oil as much as possible. It has good gloss and smoothness, but the thermoforming oil is not easy to penetrate, and the thermoforming effect will be lower.
2. If the printing ink layer is thin and the viscosity is low, the inside of the ink dries quickly, the thermoforming oil can easily penetrate, and the thermoforming effect is better; the toner particles in the ink component are small and the ink color concentration is high, which is beneficial to the thermoforming effect. .
3. It is difficult to thermoform metal ink, but it can be achieved when the ink layer is thin.
4. The properties of the ink and the thermoforming oil must match, have strong adhesion to each other, and will not produce other chemical reactions.
5. Some resin materials in the ink components will have high hardness after curing (such as UV ink), resulting in unstable thermoforming effects. Generally, printing inks with resin components that do not have high hardness after curing are selected.
The Influence of Thermoforming Oil
Thermoforming oil is a polymer material with many types, which can be classified according to applicable materials, such as PET thermoforming oil, PVC thermoforming oil, gold and silver card thermoforming oil, cardboard thermoforming oil, etc. Its main components are resins (such as polyurethane, acrylic), additives (such as anti-aging agents, diluents, etc.).
According to different properties, it is divided into water-based thermoforming oil, oil-based thermoforming oil, polishing thermoforming oil, wear-resistant thermoforming oil, powerful thermoforming oil, etc.
General requirements: During the coating process, the coating amount should be controlled to ensure the leveling, gloss, penetration, and dryness of the film surface. The thermoforming process mainly controls temperature, pressure, and time to ensure that the thermoforming is firm.
The Influence of Blister Card
Blister card is a transparent material used for thermoforming packaging (generally PET polyester, PVC polyvinyl chloride, PS polystyrene and other materials), which is heated by paper that has been coated with thermoforming oil. Press, shrink and bond together to form a complete, regular and transparent packaging product.
The most commonly used A-PET (Amorphous Polyethylene Terephthalate) thermoforming material is a kind of PET material. It is a thermoplastic environmentally friendly plastic product. It is stable at room temperature. It shrinks when heated (above the glass transition temperature of the material) and in one direction.
A thermal shrinkage of more than 50% is ideal. Compared with PVC materials, APET materials have obvious advantages: light specific gravity (low density), high strength, good folding resistance, high transparency, strong impact resistance, no crystal points, easy to decompose and environmentally friendly.
General requirements in actual production:
1. If APET is heated beyond the crystallization temperature and the heating time is too long, PET may be converted into a crystalline state and become white, which will lead to a significant reduction in sealing quality in the crystalline state and poor thermoformability.
2. The heat sealing temperature must be controlled enough to soften the thermoforming oil layer and PET vacuum forming, but not to convert PET into a crystalline state.
3. In actual production, if the material type of the thermoformed cover is changed, such as changing the PET model or changing PVC to PET, a comprehensive test and evaluation must be conducted first.
4. Combined with the actual production requirements, the design parameter requirements for the thermoformed cover:
The thickness must be greater than 0.15mm. The film thickness will be reduced during thermoforming. Pay attention to incoming material inspection. •Effective thermoforming area width >5mm.
The deformation of the thermoforming cover will affect the thermoforming effect.
If the release oil used in manufacturing the thermoformed cover remains on the surface of the thermoformed cover, it will affect the surface tension of the thermoformed cover, reduce the dyne value, and affect the thermoforming effect.
The Influence of Thermoforming Process Production
The thermoforming process includes: printing and coating thermoforming oil process and thermoforming heat sealing process. Currently, there are three ways to realize the coating process: offline oiling machine, full page oiling, silk screen partial oiling, and offset printing in-line oiling.
Offline coating and thermoforming processes generally require that the product be left for at least 72 hours after printing. After the large dark ink area is completely dry, hot molding oil can be applied to the surface and left for at least 24 hours before the thermoforming process can be carried out.
The current method of oiling the line (usually using water-based thermoforming oil) can shorten the time, but the thermoforming effect is not good. The main control objectives of the oiling process are: appropriate amount of oil (generally about 3-5g/m2, depending on the surface properties of the material and the concentration of the thermoforming oil), and full penetration of the thermoforming oil.
The coating amount must be controlled during the coating process to ensure the leveling, gloss, penetration, dryness, etc. of the film surface. The pressure forming process mainly controls temperature, pressure, time and other conditions to ensure the thermoforming effect.
The Influence of Thermoforming Equipment
There are three types of heating methods for thermoforming packaging equipment: traditional back heating, heating plate surface heating, and high-frequency internal heating. Different heating methods, different temperature control methods, and different heat transfer effects result in different thermoforming oil softening and thermoforming cooling forming effects.
The traditional thermoforming process uses back heating. The heated plate is heated, and heat is transferred to the surface of the thermoforming oil and the thermoforming cover through the back of the paper card to complete the thermoforming process.
The thermoforming temperature is relatively constant and cannot be adjusted quickly; the heat transfer is affected by the thickness of the paper has a great influence. The thicker the paper, the harder it is for the heat to be quickly transferred to the thermoforming cover.
Therefore, sufficient thermoforming pressing time must be given to allow the heat to be fully transferred to the thermoforming cover to ensure the thermoforming effect.
The heating plate thermoforming machine heats the surface of the thermoforming cover and transfers heat to the surface of the thermoforming oil to complete the vacuum forming process. The thermoforming temperature can be quickly adjusted; because the heating plate is in direct contact with the thermoforming cover, when the temperature is too high, the thermoforming cover is extremely susceptible to thermal deformation and it is difficult to transfer heat to the surface of the thermoforming oil (the thinner the thermoforming cover, the easier it is to transfer heat, but the easier it is to deform).
To ensure a good thermoforming effect, you must choose a thermoforming material with an appropriate thickness. Cover and adjust the thermoforming temperature and fusion time.
High-frequency internal heating uses a high-frequency electric field to oscillate the internal molecules of the thermoforming cover and thermoforming oil to generate heat energy to complete the thermoforming process. The temperature can be quickly adjusted.
This heating method has the most stable heat transfer and can adjust the corresponding temperature at will according to the properties of the material. However, because a large current is generated at the moment of fusion and sparks are easily generated, it is not suitable for transferring silver card products to thermoforming.
In practice, since the thermoforming temperature has a greater impact on the thermoforming effect, it is generally recommended to use thermoforming packaging equipment that can quickly adjust the temperature.
Conclusion
This article focuses on analyzing the quality problems of poor thermoformability during the thermoforming process of color box packaging products, and qualitatively analyzes the possible influencing factors from three aspects: materials, process methods, and equipment, which has obvious guiding significance for actual production. In actual work, we must first understand the customer's product requirements, master good problem analysis and solution methods, and be as familiar as possible with the thermoforming process principles, materials, equipment, and production processes in business.
When encountering quality problems, we must analyze them in principle, test and verify raw materials, process technology, and equipment control, find the causes and solutions in a timely manner, and ensure that each link is continuously carried out in strict accordance with the production operation process in daily work. monitor.
Add Comment
Business Articles
1. Essential Photo Editing Tips To Enhance Your Website's AppealAuthor: ukclippingpath
2. 5 Ways To Revolutionize Telecom With Smart Inventory Management Software
Author: Kevin
3. Rubber Roller: Enhancing Industrial Efficiency And Performance
Author: Anar rub tech pvt.ltd.
4. Tips For Cleaning And Prepping Jars For Candle Making
Author: Namo Creations
5. Vip Desert Safari Dubai
Author: Safari kings deserts
6. Why Byst Offers The Best Mentorship Programs For Entrepreneurs
Author: Byst Youth
7. How A 5kw Solar System Can Power Your Home And Save You Money
Author: Keyur Patel
8. How Long To Get A Title Loan In Wyoming | Ez Car Title Loans
Author: Ez Car Title Loans
9. Lucintel Forecasts The Global Thermoplastic Composites Market To Reach $26 Billion By 2030
Author: Lucintel LLC
10. Essential Features To Look For In An Event Management App
Author: Event Management App
11. Technology Landscape, Trends And Opportunities In The Global Micro-led Market
Author: Lucintel LLC
12. Data Visualization Software Market Forecast: Growth In Cloud Solutions
Author: mmr
13. Lucintel Forecasts The Global Food Packaging Market To Reach $xx Billion By 2024
Author: Lucintel LLC
14. Beyond Wealth: Unlocking The Power Of Family Office Services In India
Author: Drishti Desai
15. Enteral Single Use Syringes Market Size & Share, Analysis 2031
Author: Andy