ALL >> Business >> View Article
Continuous Mesh Belt Furnace: Revolutionizing Heat Treatment Processes
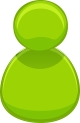
Introduction
Continuous mesh belt furnaces are pivotal in modern industrial heat treatment processes, offering an efficient, scalable solution for various applications. These furnaces are designed to handle large volumes of small parts, ensuring uniform heat treatment through continuous production lines. They are widely used in industries such as automotive, aerospace, electronics, and metalworking.
Key Features and Design
Mesh Belt Conveyor: The defining feature of these furnaces is the mesh belt conveyor, which continuously transports parts through different heating zones. The belt is typically made of heat-resistant metal alloys to withstand high temperatures.
Uniform Heating: Continuous mesh belt furnaces are designed to provide consistent and uniform heating across the entire belt width, ensuring that all parts receive the same heat treatment.
Multiple Zones: These furnaces often feature multiple heating zones, each with precise temperature control. This allows for different stages of heat treatment, such as preheating, heating, soaking, and cooling, all within one continuous process.
Atmosphere ...
... Control: Many continuous mesh belt furnaces offer controlled atmospheres, such as inert gas or vacuum, to prevent oxidation and contamination. This is particularly important for heat-treating sensitive materials.
Automation and Control Systems: Advanced control systems automate the process, regulating belt speed, temperature, and atmosphere. This ensures repeatability, reduces human error, and enhances efficiency.
Applications
Annealing: Continuous mesh belt furnaces are ideal for annealing processes, where materials are heated and then slowly cooled to soften them, improve ductility, and relieve internal stresses. This is commonly applied to metals and alloys.
Sintering: In powder metallurgy, these furnaces are used for sintering metal powders into solid parts. The continuous process is highly efficient for producing large quantities of parts with uniform properties.
Brazing: Brazing involves joining metals by melting a filler metal. Continuous mesh belt furnaces ensure uniform heating and controlled atmosphere, resulting in strong, clean joints. This is essential for manufacturing components in the automotive and aerospace industries.
Hardening and Tempering: These furnaces are also used for hardening and tempering processes, where metals are heated to high temperatures and then rapidly cooled to increase hardness. The continuous operation allows for efficient processing of high volumes of parts.
Coating and Curing: Continuous mesh belt furnaces are employed in the electronics industry for coating and curing processes. They ensure consistent and precise application of coatings, crucial for the performance and longevity of electronic components.
Advantages
High Throughput: The continuous nature of mesh belt furnaces allows for high-volume production, making them ideal for large-scale manufacturing operations.
Consistency and Uniformity: The design ensures uniform heat treatment, resulting in consistent quality across all parts.
Energy Efficiency: Modern continuous mesh belt furnaces are designed for energy efficiency, with advanced insulation and optimized heating elements reducing energy consumption.
Reduced Labor Costs: Automation and control systems minimize the need for manual intervention, reducing labor costs and increasing operational efficiency.
Versatility: These furnaces can be adapted for various heat treatment processes, making them versatile tools for different industrial applications.
Conclusion
Continuous mesh belt furnaces are essential in the industrial landscape, providing efficient, high-volume heat treatment solutions. Their ability to deliver uniform, high-quality results across large batches of parts makes them invaluable in industries where consistency and throughput are critical. As technology continues to advance, these furnaces will play an even more significant role in streamlining and enhancing heat treatment processes.
Add Comment
Business Articles
1. Stem-xpert At Web Summit Qatar 2025, Pursuing Innovative Solutions In Stem-as-a-serviceAuthor: stem-xpert
2. Deepseek’s Rapid Rise: Disrupting The Ai Market Amid Controversy
Author: Iconic success
3. Reimagining Customer Services With Microsoft Dynamics 365 Implementation
Author: Maria
4. Upcoming Developments In Ss Flanges: Possible Effects On Different Industries
Author: Neelam Forge India
5. Mg Hector 5 Seater Price In Chennai: A Detailed Review
Author: balaji
6. Mg Hector Ev Price In Chennai: A Comprehensive Overview
Author: balaji
7. Spring Marketing Trends: How Print And Video Can Refresh Your Brand
Author: Devin Herz
8. Auto Transport Services In South Carolina
Author: Secure Car Shipping
9. Authentication Of Australian Certificates In Canada: A Complete Guide
Author: anzilanx
10. Low Maintenance Plants For Home Landscaping
Author: Apunga Landscapes
11. The Ultimate Guide To Rocking Chairs – Comfort, Style, And Elegance
Author: tushar
12. Bioethanol Market Size Insights Forecast 2024-2030
Author: Nilam Jadhav
13. Touffy Fabric Upholstered Rocking Chair – The Perfect Blend Of Comfort And Elegance
Author: tushar
14. Maximizing Efficiency: Why Small Businesses Should Outsource Bookkeeping And Financial Services
Author: KMK Ventures Pvt Ltd
15. Big Patient Data And The Future Of Real World Evidence: Learnings From Biotechx 2024
Author: Industry Chronicle