ALL >> Business >> View Article
From Concept To Creation: How Rigid-flex Pcbs Are Revolutionizing Product Design
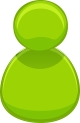
The evolution of electronics has brought about unprecedented advancements in product design, enabling devices to become more compact, versatile, and powerful. At the heart of this revolution is the innovative technology of Rigid-Flex Printed Circuit Boards (PCBs). Combining the robustness of rigid PCBs with the adaptability of flexible circuits, Rigid-Flex PCBs are transforming how engineers and designers approach product development. This article explores the journey from concept to creation and how Rigid-Flex PCBs are revolutionizing product design.
Understanding Rigid-Flex PCBs
Rigid-Flex PCBs are a hybrid technology that integrates flexible and rigid board materials within a single unit. This combination offers several distinct advantages:
Rigid Sections: Provide structural integrity and support for mounting components.
Flexible Sections: Allow the board to bend and conform to different ...
... shapes, ideal for dynamic or constrained spaces.
This unique construction enables Rigid-Flex PCBs to support complex designs that would be challenging or impossible with traditional rigid or flexible PCBs alone.
The Design Process: From Concept to Creation
Initial Concept and Requirements Gathering
The design process begins with a clear understanding of the product's requirements. This includes the intended application, environmental conditions, mechanical constraints, and electrical performance specifications. Designers and engineers collaborate to outline the key objectives and constraints that will guide the PCB design.
Schematic Design and Component Selection
Once the initial concept is defined, the schematic design phase begins. This involves creating a detailed electrical diagram that outlines how the components will be interconnected. Selecting the right components is crucial, as it impacts the overall performance, reliability, and manufacturability of the PCB. In Rigid-Flex designs, special consideration is given to components that may be subject to mechanical stress due to bending and flexing.
Mechanical Design and Layout
The mechanical design phase focuses on the physical arrangement of components and the layout of the PCB. Here, the flexibility of Rigid-Flex PCBs shines. Designers can create intricate shapes and fold the board to fit within tight spaces, making it ideal for compact and wearable devices. Advanced design software allows for precise modeling of the board's bending and stress points, ensuring reliability and performance.
Simulation and Prototyping
Before moving to production, simulations are conducted to validate the design. These simulations test the electrical performance, thermal behavior, and mechanical durability of the PCB under various conditions. Once the design passes the simulation phase, prototypes are manufactured. Prototyping is an iterative process that allows for testing and refining the design to address any issues and optimize performance.
Manufacturing and Assembly
The transition from prototyping to full-scale production involves selecting a suitable manufacturing process. Rigid-Flex PCBs require specialized manufacturing techniques, including precise layering, bonding, and drilling processes. The assembly phase involves placing and soldering components onto the board. Advanced automated systems ensure high precision and consistency in assembly.
Testing and Quality Assurance
Rigorous testing is conducted to ensure that the final product meets all design specifications and quality standards. This includes electrical testing, mechanical stress testing, and environmental testing. Quality assurance processes are critical to identifying and addressing any defects or inconsistencies before the product reaches the market.
Advantages of Rigid-Flex PCBs in Product Design
Enhanced Design Flexibility
Rigid-Flex PCBs provide unparalleled design flexibility, allowing engineers to create complex, multi-layered circuits that can be folded, twisted, and contoured to fit into unconventional shapes and spaces. This is particularly beneficial in applications such as medical devices, aerospace, and consumer electronics, where space and form factor are critical.
Improved Reliability and Durability
The integrated nature of Rigid-Flex PCBs reduces the need for connectors and cables, which are common points of failure in traditional designs. The ability to withstand mechanical stress and environmental factors enhances the overall reliability and durability of the product.
Space and Weight Savings
By eliminating the need for separate connectors and cables, Rigid-Flex PCBs contribute to significant space and weight savings. This is crucial for portable and wearable devices, where every millimeter and gram counts.
Cost-Effective Manufacturing
Although the initial design and manufacturing process for Rigid-Flex PCBs can be more complex, they often lead to cost savings in the long run. Reduced assembly time, fewer components, and improved reliability translate to lower production and maintenance costs.
Streamlined Assembly Process
The integration of rigid and flexible sections simplifies the assembly process, reducing the number of solder joints and interconnections. This streamlining not only enhances reliability but also accelerates the production timeline.
Applications of Rigid Flex PCBs
Consumer Electronics: Smartphones, tablets, and wearable devices benefit from the compact and versatile nature of Rigid-Flex PCBs.
Medical Devices: Implantable devices, diagnostic equipment, and portable medical tools rely on the reliability and flexibility of Rigid-Flex PCBs.
Aerospace and Defense: Aircraft, satellites, and military equipment require durable, lightweight, and reliable PCBs that can withstand harsh conditions.
Automotive: Advanced driver assistance systems (ADAS), infotainment systems, and electric vehicles utilize Rigid-Flex PCBs for their robustness and space-saving properties.
Conclusion
Rigid-Flex PCBs are at the forefront of a revolution in product design, offering unprecedented flexibility, reliability, and efficiency. From the initial concept to the final creation, these innovative PCBs enable engineers to push the boundaries of what is possible in electronics design. As technology continues to advance, Rigid-Flex PCBs will play an increasingly vital role in the development of next-generation devices, driving innovation and shaping the future of the electronics industry.
We are (pcb,wat,pcb manufacturer,Print Circuit Board,pcb supplier,pcb service,electronic pcb) company.Our company mainly makes PCB double-sided and high multi-layer board, HDI blind buried hole, high-frequency board, high-speed board
Add Comment
Business Articles
1. 5 Common Mistakes In B2b Lead GenerationAuthor: Akash
2. Indulge In Opulence: The World Of Luxury Jewellery
Author: Dhee Jewels
3. Empowering Aviation Safety Enhanced: Expert Fatigue Management
Author: skyone
4. Best Digital Marketing Agency In Bangalore | Best Digital Marketing Services
Author: Sanbrains Seo
5. Achieve Iso Certification In Greece: Boost Credibility & Growth
Author: Sistema Certifications
6. The Affordable And Beautiful Spray Bottles
Author: Forever Gleam Chemicals
7. Top 7 Cryptocurrencies Under 1 Cent With Real-world Utility In 2025
Author: Jasmyhit
8. The Raw Wisdom Of Kevin Gates: Unpacking Inspirational Quotes From A Street Philosopher
Author: Gaurav b
9. Enhancing Community-level Cybersecurity With Barracuda Networks' New Initiatives
Author: Industry Chronicle
10. Women Empowerment Ngos In Chennai: Prajha Trust’s Vision For Inclusive Growth
Author: Anbu Thalapathy
11. Iso Certification In India: Benefits And Process
Author: Sistema Certifications
12. G20 Summit 2023: 5 Key Takeways That Look Good For Business!
Author: Impaakt Magazine
13. Unitron Hearing Aids In Delhi: Find The Best Solutions At Hearing Clinique
Author: Hearing Clinique
14. How Performance Analysis Software Can Improve Decision-making
Author: TrackHr App
15. Top Domestic Courier Services In Gurugram- Fast, Dependable And Reasonable
Author: Karishna Trading Co