ALL >> Business >> View Article
Optimizing Mixed-model Assembly Line Balancing And Sequencing
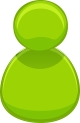
In today's dynamic manufacturing landscape, flexibility reigns supreme. Companies are increasingly turning to mixed-model production lines, where a variety of product models share the same assembly line. This approach offers agility in responding to diverse customer demands but comes with its own set of challenges. Mastering the intricate dance of balancing workloads and optimizing production sequences becomes crucial for maximizing efficiency and profitability.
The Balancing Act: Uneven Workloads and Setup Time Blues
Imagine a production line where assembling a complex smartphone takes twice as long as assembling a basic fitness tracker. This creates an uneven workload for different stations, leading to bottlenecks and idle time. Additionally, switching between models often necessitates setup time changes, further disrupting the flow. These factors contribute to inefficiencies and ultimately, lost production opportunities.
Optimizing the Dance Floor: Techniques for a Flawless Performance
Thankfully, a toolbox of techniques exists to help manufacturers optimize their mixed-model assembly lines. Here are ...
... some key strategies:
•Line Balancing: Techniques like Ranked Positional Weight (RPW) or the Kilbridge and Carrie (KC) algorithm help distribute tasks across workstations in a way that ensures an even flow of work. This minimizes idle time and prevents bottlenecks.
•Sequencing Magic: Finding the perfect order for assembling different models on the line can be a complex puzzle. Here, techniques like genetic algorithms or simulated annealing come into play. These methods help identify sequences that minimize setup time changes and optimize overall line utilization.
•Heuristics for Efficiency: Simple yet powerful rules like Largest Processing Time (LPT) or Smallest Processing Time (SPT) can also be used for sequencing. LPT prioritizes assembling the product with the longest processing time first, minimizing total completion time. SPT focuses on assembling the fastest-to-complete product first, potentially reducing idle time at the end of the line.
The Payoff: Efficiency, Cost Savings, and Quality Triumph
Optimizing your mixed-model assembly line isn't just about aesthetics; it's about real bottom-line benefits. Streamlined production leads to increased throughput, allowing you to produce more units in a given timeframe. Minimized setup times and efficient use of resources translate to reduced production costs. Additionally, a consistent workflow with less model switching can contribute to improved product quality by minimizing errors.
Real-World Examples: Success Stories on the Dance Floor
(Consider including a case study here, highlighting a specific example of a company that successfully optimized their mixed-model assembly line. You can find relevant examples through industry publications or search online for success stories from automation solution providers)
The Future of the Assembly Line Tango: Advanced Moves for Continued Success
The world of manufacturing is constantly evolving. As we move forward, expect to see even more sophisticated techniques emerge for optimizing mixed-model assembly lines. The integration of advanced analytics, machine learning, and digital twins promises to further enhance efficiency and flexibility. By embracing these advancements, manufacturers can ensure their assembly lines remain a well-rehearsed performance, delivering high-quality products while keeping costs under control.
Conclusion: Mastering the Mixed-Model Tango
Optimizing mixed-model assembly lines is no easy feat, but the rewards are undeniable. By employing the techniques discussed and staying attuned to future trends, manufacturers can create a well-balanced and efficient production environment, allowing them to thrive in this dynamic marketplace. Remember, a well-rehearsed assembly line tango is the key to keeping your customers happy and your bottom line singing.
Add Comment
Business Articles
1. Essential Photo Editing Tips To Enhance Your Website's AppealAuthor: ukclippingpath
2. 5 Ways To Revolutionize Telecom With Smart Inventory Management Software
Author: Kevin
3. Rubber Roller: Enhancing Industrial Efficiency And Performance
Author: Anar rub tech pvt.ltd.
4. Tips For Cleaning And Prepping Jars For Candle Making
Author: Namo Creations
5. Vip Desert Safari Dubai
Author: Safari kings deserts
6. Why Byst Offers The Best Mentorship Programs For Entrepreneurs
Author: Byst Youth
7. How A 5kw Solar System Can Power Your Home And Save You Money
Author: Keyur Patel
8. How Long To Get A Title Loan In Wyoming | Ez Car Title Loans
Author: Ez Car Title Loans
9. Lucintel Forecasts The Global Thermoplastic Composites Market To Reach $26 Billion By 2030
Author: Lucintel LLC
10. Essential Features To Look For In An Event Management App
Author: Event Management App
11. Technology Landscape, Trends And Opportunities In The Global Micro-led Market
Author: Lucintel LLC
12. Data Visualization Software Market Forecast: Growth In Cloud Solutions
Author: mmr
13. Lucintel Forecasts The Global Food Packaging Market To Reach $xx Billion By 2024
Author: Lucintel LLC
14. Beyond Wealth: Unlocking The Power Of Family Office Services In India
Author: Drishti Desai
15. Enteral Single Use Syringes Market Size & Share, Analysis 2031
Author: Andy