ALL >> Business >> View Article
Why Thermoformed Packaging Is Better For The Environment?
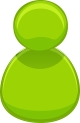
Thermoformed packaging products are the most widely used material for packaging various products. Due to its simple processing, flexible design, environmental protection and safety characteristics, it has become the preferred packaging material for specialized multi-industry packaging. According to statistics, in the field of packaging, thermoformed packaging and plastic packaging materials account for more than 40%-45% of the packaging market.
As for white pollution, we all think of excessive use of plastic products. Nowadays, thermoforming packaging accounts for an increasing proportion in the packaging industry because of its cheap price, easy use, and certain advantages in environmental protection. This blog will lead you to explore the environmental protection characteristics of vacuum forming packaging.
Ⅰ. Thermoforming Packaging
Thermoforming Packaging Principle
Thermoformed packaging uses a thermoforming machine to adsorb heated and softened plastic hard sheets to the surface of the mold. After cooling, the thermoformed packaging forms a concave-convex shaped plastic.
Thermoforming, ...
... also called vacuum forming, is one of the thermoforming methods for thermoformed plastic packaging. It refers to clamping the sheet or plate-like material on the frame of the vacuum forming machine. After heating and softening, it is vacuum-adsorbed to the mold through the air channel on the side of the mold. After a short period of cooling, the formed plastic absorbent is obtained. Plastic packaging products. The equipment used in this method is relatively simple. The mold does not need to withstand pressure and can be made of metal, wood or gypsum. The molding speed is fast and the operation is easy.
https://youtu.be/v0MiYwxRieI?si=eJW68tqiuYs-lTDm
Common Thermoformed Packaging
Thermoformed packaging products mainly include: blister card, packaging trays, lidding film packaging, thermoformed box, slide blister card packaging, carded blisters packaging, half blister card packaging, clamshell blister card packaging, double blister card packaging, etc.
Ⅱ. Environmental Performance of Thermoformed Packaging
The environmental protection of pressure forming packaging mainly depends on the selection of packaging materials and the production process. Generally speaking, benefits of thermoformed packaging in terms of environmental protection:
Material selection
Thermoforming packaging mainly uses plastic materials such as polyethylene (PE) and polypropylene (PP), which have good heat resistance, cold resistance and chemical stability. Among these materials, polyethylene and polypropylene are food-grade materials and are widely used in packaging in food, medicine and other fields.
In addition, there are some biodegradable materials, such as polylactic acid (PLA), which can be decomposed by microorganisms in the natural environment and have good environmental performance.
Vacuum forming packaging contains environmentally friendly packaging materials. Many customers will give priority to environmentally friendly materials when customizing packaging. As a manufacturer, environmentally friendly materials will also be placed in an important position. With the continuous improvement of technology levels, the types of environmentally friendly materials It is also increasing continuously.
Fewer raw materials are used to make thermoformed packaging, and many raw materials can be recycled for use. Many blister packaging produced can also be reused, reflecting the role of environmental protection.
Recyclability
Some thermoformed packaging materials, such as polyethylene and polypropylene, are eco friendly nature and sustainable plastic materials. These materials are recycled and then processed into new packaging products, which can reduce resource consumption and reduce environmental pollution.
Production Process
The production process of vacuum forming packaging mainly includes sheet production, mold making, thermoforming and other links. In these links, attention needs to be paid to controlling energy consumption and pollutant emissions during the production process. Adopting green and environmentally friendly production processes and technologies can reduce energy consumption and pollutant emissions during the production process and improve the environmental performance of thermoformed packaging.
Disposal
After use, thermoformed packaging needs to be disposed of. Generally speaking, plastic waste should be sorted and recycled to reduce the impact on the environment.
However, thermoformed packaging still has certain limitations in terms of disposal due to its large size and relatively high recycling labor costs. Therefore, improving the recycling rate of thermoforming packaging and developing new environmentally friendly materials are important ways to improve the environmental protection of pressure forming packaging.
Ⅲ. Commonly Used Materials for Thermoformed Packaging
The only raw materials for thermoforming packaging are plastic sheets. The thickness of the film generally does not exceed 1.5MM. Commonly used sheets include: PVC, PET, PP, PS, PET-G (GAG) and flocking sheets and gold plating based on this. sheets and anti-static sheets.
PVC
PVC sheet is a widely used and popular material. The hard sheet has high toughness and is not easy to burn. When burned, it will produce chlorine gas, which will cause certain obstacles to the environment. PVC is easy to heat seal, and can be sealed with sealing machines and high-frequency machines. , is an important raw material for the production of translucent thermoformed products.
PVC film can be divided into two types: environmentally friendly and non-environmentally friendly. It can be made into various pressure forming packaging products such as translucent, colorful, anti-static, gold-plated, flocking, etc. Its characteristics are high transparency, good surface gloss, few crystal points, and water content. It has small grain, wide application, strong impact resistance, and is easy to shape. The products comply with the US FDA and Japanese PL food hygiene standards. The products are widely used in toys, food and pharmaceutical products, electronic products, medicine, electrical appliances, gifts, cosmetics, stationery and other products. Outer packaging.
PET
PET sheet is a new material that has developed in recent years. It relies on its excellent toughness, high strength, high transparency, and excellent environmental performance of being recyclable and reusable. It does not produce harmful gases when burned. It is an environmentally friendly material and is gradually banned. PVC has been gradually banned. There is great confusion between consumers and producers, but the price is high. It is suitable for making high-end thermoformed products. Thermoformed bulbs in European and American countries also require the use of PET material, but its thermal melting point is high, which brings great difficulties to high-frequency packaging. In order to solve this problem, people laminate a layer on the surface of PET. A layer of PVC film is named PETG, but the price is higher. Mainly used in electronics, food, toys, color box windows, collar supports, footwear packaging, etc.
PP
PP sheet is made of PP resin through brewing, calendering, trimming and other processes. It has light weight, bright and quiet surface, good heat resistance, high mechanical strength, excellent chemical stability and electrical insulation. , non-toxic and other characteristics, it can be made into daily necessities such as beverage cups and food boxes through thermoforming.
PP can be used for a long time at 100°C and can withstand high-temperature bacterial treatment at 121°C. It has outstanding moisture-proof performance and reliable hygienic performance, and is widely used in food packaging. It has excellent folding performance and can be made into stationery clips, boxes, etc.
PETG
PETG, also known as GPET sheet, is a non-crystalline PET resin modified with cyclohexanediol. The biggest advantages of PETG sheets are good heat sealing performance, easy operation during sealing, good sealing effect and easy glue bonding. At the same time, its chemical resistance, optical properties, and scratch resistance are also very good. PETG has passed the US FDA's food contact standards and can be used in food and personal health product packaging, medical and health equipment and food, and can also be used in strong and durable packaging. Its advantages are as follows:
1. Good transparency, suitable for products requiring high transparency.
2. Excellent impact strength and rigidity
3. Excellent processability, it can be processed by sawing, die-cutting, drilling and laser cutting. It can also be cold-bent and hot-bent, adhered, welded and polished, printed and painted; and the cold-bending does not turn white and has a bright appearance.
4. It has good thermoformability, can be formed without preheating, has high precision, good deep formability, no cracking and uniform thickness.
5. Low flammability, good fire resistance, no combustion support, low smoke production, and no harmful substances after burning.
GAG
GAG is a three-layer composite sheet produced by co-extrusion of the middle layer of APET and the upper and lower layers of PETG raw materials in appropriate proportions. It is specially suitable for packaging boxes that require high-frequency heat sealing and glue bonding. Its advantages are as follows:
1. Good transparency, the transparency can reach more than 90%, and good texture. It is suitable for products requiring high transparency.
2. Excellent impact strength and rigidity, the material is hard and durable, and suitable for high impact strength applications.
3. Excellent processability, it can be processed by sawing, die-cutting, drilling and laser cutting. It can also be cold-bent and hot-bent, adhered, welded and polished, printed and painted; and the cold-bending does not turn white and has a bright appearance.
4. It has good thermoformability and can be formed without preheating, with high precision and shrinkage rate of about 0.5%; it has good deep formability, no cracking and uniform thickness.
5. Environmentally friendly, recyclable and does not pollute the environment.
6. Excellent food hygiene, the material is PETG, which can comply with all important food regulations, such as FDA or BGA, etc., and is suitable for food container packaging
7. It has good fire resistance, does not support combustion, produces low smoke, and has no harmful substances after burning.
Ⅳ. How to Make Thermoformed Packaging Meet Environmental Requirements
How to make thermoforming packaging meet the requirements of green environmental protection is an urgent problem now. How to solve it, of course, cannot be solved without relying on technological innovation. Achieve these six points to make vacuum forming packaging more green and environmentally friendly:
1. Innovate and develop new plastic materials and new processing technologies to make more plastics with excellent functions become packaging materials, and use the high functions of new materials, creating precise product packaging and completing the reduction of packaging materials.
2. Develop bio-based plastics, effectively regulate the degradation time and cycle of bioplastics, and while giving full play to the functions of bioplastic packaging materials, reduce and eliminate the pollution and impact of plastic packaging materials on the ecological environment.
3. Advance and improve plastic recycling and processing technology to significantly increase the recycling rate of plastic packaging materials, improve and eliminate the risk of white pollution caused by plastic packaging materials, and increase resource utilization.
4. Use advanced thermoformed packaging technology such as intelligence and the edible, water-soluble and other characteristics of some plastic packaging materials to reduce the amount of packaging waste and improve the safety and environmental protection performance of plastic packaging.
5. Through independent research and development and technological innovation, reduce the cost of new plastic packaging materials and new technologies, and avoid the problem that many plastic materials that are suitable for green packaging cannot be used in large areas due to excessive costs.
6. Promote the improvement and development of plastic blending technology, new plastic additives and application technologies. On the premise of ensuring that plastic packaging materials are non-toxic, hygienic and environmentally friendly, use low-cost technology to enhance the functions of plastic packaging materials and contribute to weight reduction. provides possibilities.
Conclusion
To measure the advantages and disadvantages of a kind of packaging, we mainly focus on the following points: whether the packaging cost is reasonable, whether it is convenient to transport, whether the transportation cost is high, whether it takes up less warehouse area, whether it is a waste of space, and how effective it is in preventing damage and loss of packaging materials. Whether it can better maintain or effectively increase the value of the packaged items, tamper resistant packaging option, whether to achieve brand recognition and product visibility, whether it is conducive to the application of high and new technologies such as automation and intelligence, etc. If these aspects can be achieved, it means that this kind of packaging is an ideal packaging and has good development prospects. Compared with plastic injection molding, vacuum forming packaging has advantages over other types of packaging in these aspects, making it the preferred method for packaging many electrical products and unique in the packaging field. Some industrially developed countries such as the United States, Japan, and Germany have implemented packaging automation controlled by electronic computers for mass-produced small electrical products. This creates good conditions for the promotion and application of thermoforming packaging.
Add Comment
Business Articles
1. Essential Photo Editing Tips To Enhance Your Website's AppealAuthor: ukclippingpath
2. 5 Ways To Revolutionize Telecom With Smart Inventory Management Software
Author: Kevin
3. Rubber Roller: Enhancing Industrial Efficiency And Performance
Author: Anar rub tech pvt.ltd.
4. Tips For Cleaning And Prepping Jars For Candle Making
Author: Namo Creations
5. Vip Desert Safari Dubai
Author: Safari kings deserts
6. Why Byst Offers The Best Mentorship Programs For Entrepreneurs
Author: Byst Youth
7. How A 5kw Solar System Can Power Your Home And Save You Money
Author: Keyur Patel
8. How Long To Get A Title Loan In Wyoming | Ez Car Title Loans
Author: Ez Car Title Loans
9. Lucintel Forecasts The Global Thermoplastic Composites Market To Reach $26 Billion By 2030
Author: Lucintel LLC
10. Essential Features To Look For In An Event Management App
Author: Event Management App
11. Technology Landscape, Trends And Opportunities In The Global Micro-led Market
Author: Lucintel LLC
12. Data Visualization Software Market Forecast: Growth In Cloud Solutions
Author: mmr
13. Lucintel Forecasts The Global Food Packaging Market To Reach $xx Billion By 2024
Author: Lucintel LLC
14. Beyond Wealth: Unlocking The Power Of Family Office Services In India
Author: Drishti Desai
15. Enteral Single Use Syringes Market Size & Share, Analysis 2031
Author: Andy