ALL >> Business >> View Article
High Temperature Furnaces: Innovation And Applications
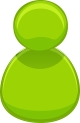
High temperature furnaces are a critical component in various industrial processes, enabling the achievement of extreme temperatures necessary for specific material treatments. These furnaces are instrumental in metallurgy, ceramics, and many other fields that require the manipulation and transformation of materials at high temperatures. This article explores the functionalities, types, innovations, and applications of high temperature furnaces, offering insights into their vital role in modern industry.
Understanding High Temperature Furnaces
A high temperature furnace is a device designed to reach and maintain exceptionally high temperatures, typically above 1,000°C (1,832°F). These furnaces are essential for processes such as annealing, sintering, and heat treatment, where materials undergo significant physical and chemical changes.
Key Components and Features
Heating Elements:
Metallic: Commonly made from materials like nichrome or kanthal, suitable for temperatures up to 1,400°C.
Non-Metallic: Includes silicon carbide or molybdenum disilicide, capable of withstanding temperatures ...
... up to 1,800°C and beyond.
Insulation: High temperature furnaces use advanced refractory materials to minimize heat loss and ensure energy efficiency. Materials such as alumina, zirconia, and various ceramic fibers are prevalent in these applications.
Temperature Control Systems: Modern furnaces are equipped with precise temperature control mechanisms, often incorporating thermocouples, infrared sensors, and advanced digital controllers to maintain stable temperatures and ensure process accuracy.
Types of High Temperature Furnaces
Muffle Furnaces:
Designed with an enclosed heating chamber, separating the material from direct flame contact.
Used extensively in laboratory settings for analytical applications and materials research.
Tube Furnaces:
Characterized by a cylindrical heating chamber, ideal for continuous processing of samples.
Common in processes like chemical vapor deposition (CVD) and thermal analysis.
Induction Furnaces:
Utilize electromagnetic induction to generate heat directly within the material, allowing for rapid heating and precise control.
Widely used in metal melting and alloy production.
Vacuum Furnaces:
Operate under reduced pressure to prevent oxidation and contamination of sensitive materials.
Essential for processes involving advanced ceramics, superalloys, and semiconductor fabrication.
Rotary Kilns:
Feature a rotating cylindrical chamber, providing uniform heat distribution and mixing of materials.
Used in large-scale applications such as cement production and waste treatment.
Innovations in High Temperature Furnace Technology
Energy Efficiency Enhancements:
Development of new insulation materials and heating element designs has led to significant reductions in energy consumption.
Advanced control systems allow for precise temperature regulation, minimizing energy waste.
Automation and Digitalization:
Integration of IoT (Internet of Things) technologies and AI (Artificial Intelligence) enables real-time monitoring and predictive maintenance.
Automation systems streamline operations, reducing labor costs and improving process consistency.
Environmentally Friendly Designs:
Modern furnaces are designed with a focus on reducing emissions and minimizing environmental impact.
Innovations in waste heat recovery and cleaner combustion technologies contribute to more sustainable operations.
Enhanced Material Handling:
Improvements in furnace loading and unloading systems increase throughput and reduce downtime.
Advanced robotics and conveyor systems facilitate the handling of materials in high-temperature environments.
Applications of High Temperature Furnaces
Metallurgical Processes:
Essential for refining and alloying metals, where precise temperature control is crucial for achieving desired material properties.
Used in processes such as annealing, hardening, and tempering to improve the mechanical characteristics of metals.
Ceramics and Glass Production:
High temperature furnaces are vital for the sintering of ceramics, ensuring the materials reach the required density and strength.
In glass production, these furnaces facilitate melting and shaping processes, allowing for the creation of various glass products.
Chemical Processing:
Employed in the production of chemicals such as ammonia, hydrogen, and various hydrocarbons.
High temperature environments enable chemical reactions that are otherwise not feasible at lower temperatures.
Semiconductor Manufacturing:
Critical for processes like diffusion and annealing in semiconductor fabrication, where controlled thermal environments are necessary for precise doping and defect management.
High temperature furnaces are used to grow silicon crystals and produce high-purity semiconductor materials.
Research and Development:
Used in scientific research to study material behaviors under extreme conditions.
High temperature furnaces are integral in developing new materials with advanced properties for aerospace, defense, and energy applications.
Conclusion
High temperature furnaces represent a cornerstone of industrial technology, enabling the transformation and enhancement of materials across a wide range of applications. With continuous advancements in furnace design and technology, these systems are becoming more efficient, environmentally friendly, and capable of meeting the demands of modern industry. As innovation continues, the role of high temperature furnaces will remain pivotal in driving progress in material science and industrial manufacturing.
Add Comment
Business Articles
1. Stem-xpert At Web Summit Qatar 2025, Pursuing Innovative Solutions In Stem-as-a-serviceAuthor: stem-xpert
2. Deepseek’s Rapid Rise: Disrupting The Ai Market Amid Controversy
Author: Iconic success
3. Reimagining Customer Services With Microsoft Dynamics 365 Implementation
Author: Maria
4. Upcoming Developments In Ss Flanges: Possible Effects On Different Industries
Author: Neelam Forge India
5. Mg Hector 5 Seater Price In Chennai: A Detailed Review
Author: balaji
6. Mg Hector Ev Price In Chennai: A Comprehensive Overview
Author: balaji
7. Spring Marketing Trends: How Print And Video Can Refresh Your Brand
Author: Devin Herz
8. Auto Transport Services In South Carolina
Author: Secure Car Shipping
9. Authentication Of Australian Certificates In Canada: A Complete Guide
Author: anzilanx
10. Low Maintenance Plants For Home Landscaping
Author: Apunga Landscapes
11. The Ultimate Guide To Rocking Chairs – Comfort, Style, And Elegance
Author: tushar
12. Bioethanol Market Size Insights Forecast 2024-2030
Author: Nilam Jadhav
13. Touffy Fabric Upholstered Rocking Chair – The Perfect Blend Of Comfort And Elegance
Author: tushar
14. Maximizing Efficiency: Why Small Businesses Should Outsource Bookkeeping And Financial Services
Author: KMK Ventures Pvt Ltd
15. Big Patient Data And The Future Of Real World Evidence: Learnings From Biotechx 2024
Author: Industry Chronicle